Rapid Liquid Printing Market Size and Share
Rapid Liquid Printing Market Analysis by Mordor Intelligence
The rapid liquid printing market size stood at USD 41.22 million in 2025 and is on track to reach USD 99.24 million by 2030, posting a 19.21% CAGR over the period. The technology prints objects inside a thermoreversible gel, bypassing the layer-by-layer constraint and enabling complex channels, overhangs, and meter-scale parts in a single uninterrupted pass. Early adoption in automotive and healthcare illustrates how ultra-fast cycle times and geometry freedom compress both product development and production lead times. Printers remain the primary revenue engine as OEMs retrofit lines for short-run interior panels and surgical devices, yet AI-driven software is emerging as the critical enabler for quality control, yield, and gel-flow efficiency. The expanding palette of industrial silicones, elastomers, and liquid metals moves the technology beyond prototyping toward durable, end-use components that rival injection-molded equivalents. Venture funding, led by major automakers and aerospace primes, underscores confidence that rapid liquid printing will unlock profitable mass-customization in high-value sectors.
Key Report Takeaways
- By offering, printers held 44.32% of rapid liquid printing market share in 2024, while software is forecast to climb at 22.49% CAGR to 2030.
- By application, prototyping led with 48.32% revenue share in 2024; functional part manufacturing is advancing at a 23.02% CAGR through 2030.
- By end-use industry, automotive captured 25.67% of rapid liquid printing market size in 2024; healthcare records the fastest 21.98% CAGR to 2030.
- By material type, photopolymer resins accounted for 58.54% share of the rapid liquid printing market in 2024, whereas metals and alloys expand at 22.98% CAGR through 2030.
- By geography, North America dominated with 34.56% share in 2024; Asia-Pacific is the fastest-growing region at 23.12% CAGR through 2030.
Global Rapid Liquid Printing Market Trends and Insights
Drivers Impact Analysis
Driver | (~) % Impact on CAGR Forecast | Geographic Relevance | Impact Timeline |
---|---|---|---|
Ultra-fast production cycles for large-format parts | +4.2% | Global, with concentration in North America & Europe | Medium term (2-4 years) |
Industrial-grade elastomers and silicones broaden use-cases | +3.8% | North America & APAC core, spill-over to Europe | Long term (≥ 4 years) |
Surge in custom automotive interiors and lightweight parts | +3.5% | Global, early gains in North America, Germany, Japan | Medium term (2-4 years) |
Expanding medical adoption for patient-specific devices | +3.1% | North America & Europe, emerging in APAC | Long term (≥ 4 years) |
AI-enabled real-time tool-path optimization | +2.4% | Global, with early adoption in North America | Short term (≤ 2 years) |
ESG-driven shift to solvent-free gel matrices | +2.1% | Europe & North America, expanding to APAC | Long term (≥ 4 years) |
Source: Mordor Intelligence
Ultra-fast production cycles for large-format parts
Printing inside a gel bath removes the sequential layer build, enabling prints that are 10–100 times faster than fused-filament or photopolymer methods for components exceeding 1 m in any axis. Washington State University showed that AI path-planning cuts another 35% from cycle time while holding ±0.1 mm accuracy. Multiple objects can share the same gel volume, pushing throughput high enough for limited-series dashboards, spoiler skins, or prosthetic sockets. BMW’s pilot line reduced interior trim lead time from weeks to hours by eliminating tooling and curing stages. Capacity gains translate directly into lower per-unit cost for low-to-mid volumes, a sweet spot traditional molding cannot reach.
Industrial-grade elastomers and silicones broaden use-cases
Silicone and high-durometer TPU keep their thermal stability and chemical resistance after gel-suspension printing, opening pathways for under-hood gaskets, flexible connectors, and acoustic dampers. Sika Automotive shortened acoustic baffle development from 4–8 weeks to 2–5 days by printing proprietary elastomers that self-support within the gel and cure without warping. Covestro’s conductive TPU films demonstrate integration of heating elements directly into sunroof shades, merging multiple parts into a single print.[1]Covestro, “Concept Car Sunroof Shade,” solutions.covestro.comThe ability to program material gradients inside a single elastomer piece widens adoption in footwear and wearable devices where comfort zones vary across the geometry.
Surge in custom automotive interiors and lightweight parts
General Motors installed more than 130 printed components in the Cadillac Celestiq, including its largest metal steering-wheel core, proving the feasibility of additive production in luxury series. 9T Labs achieved a 67% weight cut in brackets using continuous carbon-fiber infill while trimming lifetime CO₂ by 47%. Rapid liquid printing brings similar design latitude to elastomeric and metal parts that require deep undercuts or lattice reinforcement, allowing automakers to hit weight and personalization targets without delaying launch schedules.
Expanding medical adoption for patient-specific devices
The technology supports variable-density structures and porous scaffolds conducive to osseointegration. 3D-printed orthoses are projected to double from USD 289.49 million in 2023 to USD 587.19 million by 2030, pointing to strong demand for bespoke medical hardware. Abbott uses additive processes to accelerate diagnostic device iterations while retaining FDA design-history files. Surgical guides tailored to each patient reduce theater time and improve alignment outcomes, validating premium pricing for hospitals.
Restraints Impact Analysis
Restraint | (~) % Impact on CAGR Forecast | Geographic Relevance | Impact Timeline |
---|---|---|---|
High capital expenditure for printers | −2.8% | Global, acute in emerging economies | Medium term (2-4 years) |
Limited catalogue of standardized materials | −2.3% | Global, especially in regulated sectors | Long term (≥ 4 years) |
Health risks from aerosolized gel micro-drops | −1.9% | Europe, North America | Short term (≤ 2 years) |
IP leakage from unsecured file sharing | −1.4% | Defense, aerospace value chains | Short term (≤ 2 years) |
Source: Mordor Intelligence
High capital expenditure for proprietary printers
Industrial rapid liquid printing systems range from USD 20,000 to more than USD 1 million, a hurdle for small manufacturers whose ROI relies on sporadic custom jobs.[2]Unionfab, “How Much Does It Cost to 3D Print Something (2024)?,” unionfab.com Recent tariffs lifted prices of China-sourced hardware by up to 145% and lengthened delivery cycles, lowering the tech’s appeal for cost-sensitive buyers. Service bureaus are emerging as a bridge, offering print capacity on demand so users can evaluate the process without heavy capex.
Limited catalogue of standardized printable materials
Few chemistries are certified under aerospace, automotive, or medical standards, so engineers struggle to qualify parts that must last decades or withstand corrosive fluids. Specialized metal powders cost USD 300–1,000 per kg, and each new alloy demands fresh print-parameter discovery and fatigue testing. Purdue University’s 900 MPa aluminum variant shows progress, but data sets remain thin for long-term creep or crack growth. Standard bodies are drafting methods tailored to gel suspension, yet until they finalize protocols, adoption in safety-critical parts will proceed cautiously.
Segment Analysis
By Offering: Software ignites digital transformation
Printers anchored 44.32% of rapid liquid printing market share in 2024 as OEMs installed large-volume cells for automotive consoles and orthopedic shells. The segment benefits from recurring consumable sales and service contracts that lock users into proprietary gel formulas. Software, however, posts the quickest 22.49% CAGR through 2030. Multi-objective Bayesian solvers adapt tool paths in real time, shrinking scrap by 30% and elevating surface accuracy, thereby justifying premium licenses.
Service providers represent a rising slice as integrators help calibrate print parameters for elastomer blends and metallic suspensions. Materials growth remains tied to supplier capacity and geopolitics, with photopolymer resins widely available while custom TPU and liquid metal blends carry longer lead times. Integration of cloud MES platforms is also advancing, linking printer data to enterprise resource planning, and further embedding software into the production stack. These developments ensure the rapid liquid printing market continues shifting from hardware-centric to software-orchestrated ecosystems. The rapid liquid printing industry therefore pivots toward data-driven value capture rather than unit sales of machines.
Note: Segment shares of all individual segments available upon report purchase
By Application: Functional manufacturing gathers speed
Prototyping held 48.32% of revenue in 2024, yet functional manufacturing accelerates at 23.02% CAGR, signaling confidence in repeatable quality and isotropic properties. Automakers use rapid liquid printing to eliminate soft tools for runs under 5,000 units, slashing program launch costs. Medical OEMs rely on the process for porous implants that match patient CT scans, reducing revision surgeries and postoperative stays.
Tooling applications gain traction as conformal cooling channels decrease injection-mold cycle times by up to 30%, offsetting the higher metal powder price. Decorative consumer goods such as footwear midsoles and fashion accessories validate the process at scale through brands seeking individualized aesthetics. The rapid liquid printing market thus transitions from a design-verification instrument to a short-run production resource, expanding its revenue pool beyond engineering departments. The rapid liquid printing industry enjoys wider executive-level sponsorship as business cases shift from cost-avoidance to revenue generation.
By End-Use Industry: Healthcare accelerates adoption
Automotive captured 25.67% of rapid liquid printing market size in 2024, reflecting both prototyping and rising content in premium electric vehicles. Custom interiors, vent bezels, and lightweight support brackets illustrate where subtractive machining fails to meet cost targets. Healthcare, posting 21.98% CAGR, is expected to eclipse automotive spending before 2030 as regulations codify digital workflows for patient-matched devices.
Hospitals favor in-house print labs that produce surgical guides within 24 hours of scan, bypassing external suppliers and inventory costs. Consumer goods makers exploit multi-material capability for ergonomic wearables that morph with body movement, while aerospace primes explore gel-printed titanium for weight-critical ducts. Altogether, sector diversity cushions cyclicality and underpins steady revenue expansion for the rapid liquid printing market.
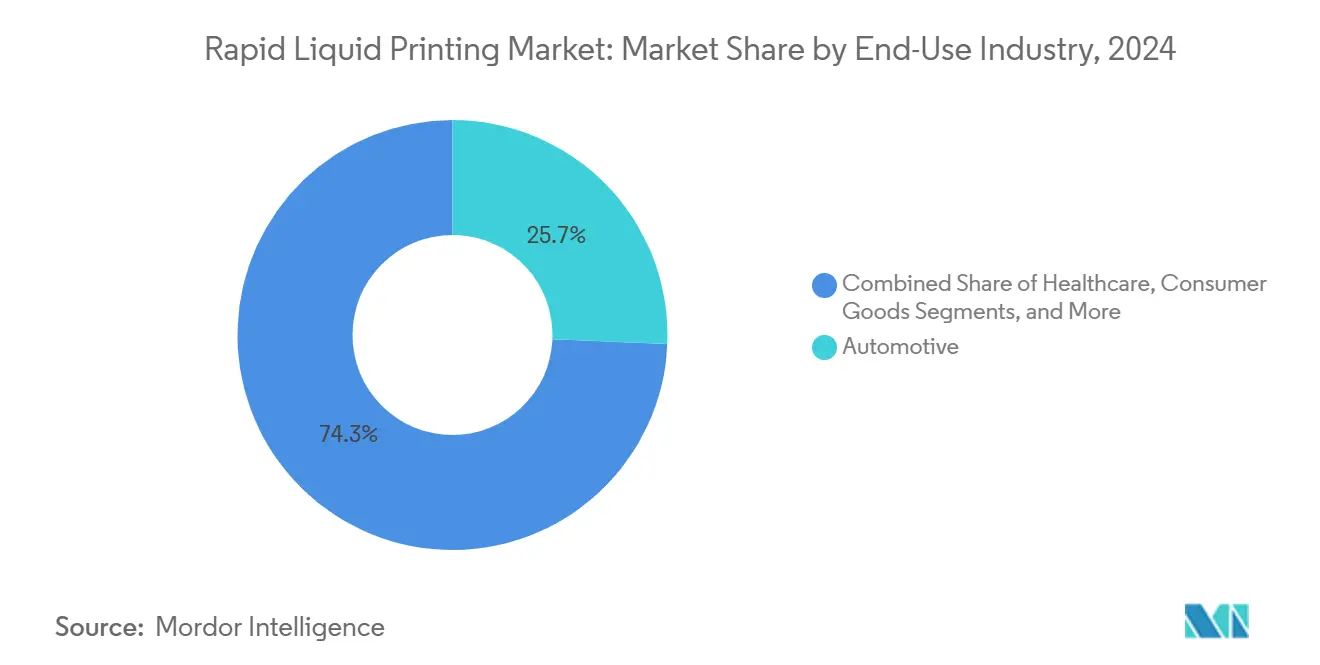
Note: Segment shares of all individual segments available upon report purchase
By Material Type: Metals drive innovation
Photopolymer resins dominate with 58.54% share due to low viscosity, minimal odor, and established cure profiles. They underpin most prototypes and visual models. Metals and alloys, growing at 22.98% CAGR, unlock value for lightweight structural parts where density and yield strength are critical. MIT’s liquid-metal advances enable continuous extrusion of aluminum and copper inside the gel, removing oxidation issues that plague powder-bed fusion.
Elastomers and silicones benefit from inherent compliance, supporting seals and vibration isolators in harsh settings. Composite gels that blend chopped carbon fibers or conductive fillers broaden electromagnetic shielding and thermal-management possibilities. Efficient recycling of the carrier gel further aligns the segment with ESG mandates, reinforcing uptake across regulated markets. Consequently, material innovation propels both volume and margin expansion in the rapid liquid printing market.
Geography Analysis
North America led with 34.56% share in 2024, fueled by Detroit’s integration of more than 130 printed parts into Cadillac Celestiq production and by GE Aerospace’s USD 1 billion commitment to additive engine components. Universities such as MIT and Purdue supply talent and material breakthroughs, while the FDA’s clarified guidance on patient-matched devices accelerates hospital adoption. Canada and Mexico supplement regional momentum through cross-border automotive supply chains and defense offsets that specify domestic additive content.
Asia-Pacific records the fastest 23.12% CAGR, propelled by China’s industrial policy and Japan’s magnesium-alloy milestone, set for commercialization by 2029.[3]Japan Aerospace Exploration Agency, “Industry's First Technology to Use Magnesium Alloys in Wire-Laser Metal 3D Printer,” global.jaxa.jp Chinese print-head makers such as Bambu Lab posted CNY 1.5 billion (USD 210 million) in 2024 sales, validating local demand for consumer and industrial printers. India’s EV supply chain begins to swap machined aluminum for printed brackets, shortening model cycles in a fiercely competitive domestic market. In Australia, mining firms test gel-printed elastomer seals that withstand abrasive slurries, targeting reduced downtime on remote sites.
Europe maintains steady expansion underpinned by stringent waste-reduction mandates and premium auto brands. BMW’s additive center in Germany proves out lattice-reinforced mounts that trim curb weight without sacrificing crash integrity. France and Italy focus on luxury goods and aerospace interiors, where customization commands pricing power. Regulatory alignment on REACH and MDR shapes supplier roadmaps and reinforces traceability features in print-monitoring software, bolstering the rapid liquid printing market’s credibility among risk-averse buyers.
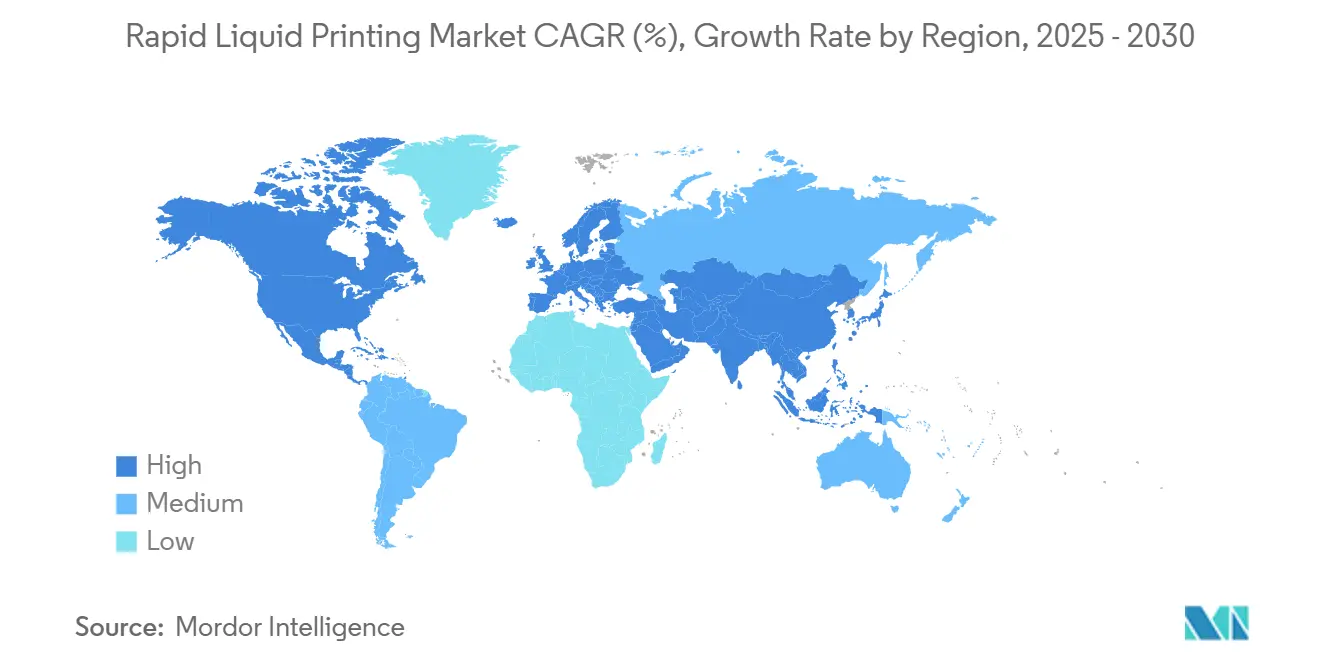
Competitive Landscape
The rapid liquid printing market remains consolidated. Heritage players such as Stratasys and 3D Systems leverage installed bases and service networks, yet pure-play innovators capitalize on gel-suspension know-how. Rapid Liquid Print, backed by USD 7 million Series A funds from BMW i Ventures, aims to scale to automotive takt times by pairing proprietary gels with open-architecture robots.
Strategic intent centers on vertical integration. Hardware firms bundle AI path-planning suites and proprietary resin cartridges to lock in recurring revenue. Service bureaus differentiate via certifications such as AS9100 and ISO 13485, giving regulated industries a turnkey route when capital budgets tighten. Patent activity clusters around gel chemistry, anti-settling agents, and sensorized nozzles that auto-correct deposition drift, creating defensive moats.
Mergers are expected as legacy CNC and laser-cladding vendors seek entry points into high-growth additive niches. Partnerships between printer OEMs and material suppliers accelerate validation cycles, with Purdue-developed alloys licensed to powder vendors for niche aerospace contracts. Competitive intensity therefore shifts from pure hardware throughput to holistic platform performance, encompassing software, materials, and after-sales ecosystems.
Rapid Liquid Printing Industry Leaders
-
Stratasys Ltd.
-
3D Systems Corporation
-
Dassault Systemes
-
ExOne Operating LLC
-
Materialise NV
- *Disclaimer: Major Players sorted in no particular order
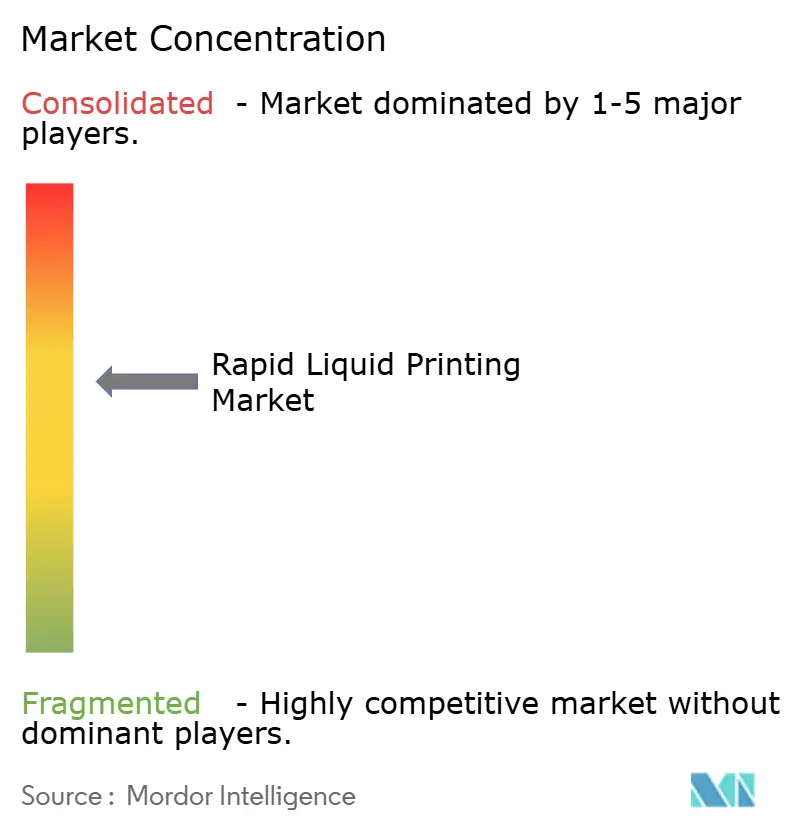
Recent Industry Developments
- March 2025: GE Aerospace committed USD 1 billion to expand US additive manufacturing facilities focused on rapid liquid printing for engine components.
- January 2025: SpaceX debuted Raptor 3 featuring gel-printed cooling channels for mission-critical performance.
- November 2024: Makino and Fraunhofer ILT integrated EHLA3D into a five-axis CNC platform, reaching 30 m/min deposition speeds.
- November 2024: Nike launched the Air Max 1000 with Zellerfeld, showcasing consumer-grade customization via rapid liquid printing.
Global Rapid Liquid Printing Market Report Scope
The rapid liquid printing market is segmented by offering (Printers, Services, Materials and Software), by application (Prototyping, Functional Part/End-Use Manufacturing and Tooling), and by end-use industry (Healthcare, Consumer Goods, Automotive, Fashion & Accessories, Electronics and Other End-Use Industries) and by geography (North America, Europe, Asia Pacific, South America and Middle East and Africa). The market sizing and forecasts are provided in terms of value (USD) for all the above segments.
By Offering | Printers | |||
Services | ||||
Materials | ||||
Software | ||||
By Application | Prototyping | |||
Functional Part / End-Use Manufacturing | ||||
Tooling | ||||
By End-Use Industry | Healthcare | |||
Consumer Goods | ||||
Automotive | ||||
Fashion and Accessories | ||||
Electronics | ||||
Other End-Use Industries | ||||
By Material Type | Elastomers and Silicones | |||
Photopolymer Resins | ||||
Composite Gels | ||||
Metals and Alloys (liquid metal variants) | ||||
Bio-inks / Hydrogels | ||||
By Geography | North America | United States | ||
Canada | ||||
Mexico | ||||
Europe | Germany | |||
United Kingdom | ||||
France | ||||
Italy | ||||
Spain | ||||
Russia | ||||
Rest of Europe | ||||
Asia-Pacific | China | |||
India | ||||
Japan | ||||
South Korea | ||||
Australia and New Zealand | ||||
Rest of Asia-Pacific | ||||
Middle East and Africa | Middle East | United Arab Emirates | ||
Saudi Arabia | ||||
Turkey | ||||
Rest of Middle East | ||||
Africa | South Africa | |||
Nigeria | ||||
Egypt | ||||
Rest of Africa | ||||
South America | Brazil | |||
Argentina | ||||
Rest of South America |
Printers |
Services |
Materials |
Software |
Prototyping |
Functional Part / End-Use Manufacturing |
Tooling |
Healthcare |
Consumer Goods |
Automotive |
Fashion and Accessories |
Electronics |
Other End-Use Industries |
Elastomers and Silicones |
Photopolymer Resins |
Composite Gels |
Metals and Alloys (liquid metal variants) |
Bio-inks / Hydrogels |
North America | United States | ||
Canada | |||
Mexico | |||
Europe | Germany | ||
United Kingdom | |||
France | |||
Italy | |||
Spain | |||
Russia | |||
Rest of Europe | |||
Asia-Pacific | China | ||
India | |||
Japan | |||
South Korea | |||
Australia and New Zealand | |||
Rest of Asia-Pacific | |||
Middle East and Africa | Middle East | United Arab Emirates | |
Saudi Arabia | |||
Turkey | |||
Rest of Middle East | |||
Africa | South Africa | ||
Nigeria | |||
Egypt | |||
Rest of Africa | |||
South America | Brazil | ||
Argentina | |||
Rest of South America |
Key Questions Answered in the Report
What is the current size of the rapid liquid printing market?
The rapid liquid printing market size reached USD 41.22 million in 2025 and is forecast to climb to USD 99.24 million by 2030.
Which segment grows fastest within the rapid liquid printing market?
Software rises at a 22.49% CAGR through 2030 as AI path-planning becomes pivotal for print efficiency and quality.
Why is healthcare adopting rapid liquid printing so rapidly?
Hospitals value the ability to create patient-specific guides and implants within 24 hours, cutting surgery time and inventory costs.
Which material category shows the highest growth?
Metals and alloys expand at 22.98% CAGR due to aerospace and automotive demand for lightweight, high-strength parts.
How fragmented is the competitive landscape?
The market is moderately fragmented; no single vendor controls more than a few percentage points, giving innovative startups room to scale.
Page last updated on: July 8, 2025