Wind Turbine Composite Materials Market Size and Share
Wind Turbine Composite Materials Market Analysis by Mordor Intelligence
The Wind Turbine Composite Materials Market size is estimated at USD 13.45 billion in 2025, and is expected to reach USD 18.22 billion by 2030, at a CAGR of 6.26% during the forecast period (2025-2030). Widespread adoption of blades longer than 100 m, supported by lighter glass-, carbon- and hybrid-fiber architectures, is raising material content per turbine and pushing suppliers to expand capacity in Asia Pacific and Europe. Policy incentives such as the United Kingdom’s Contracts for Difference (CfD) budget and China’s 117 GW of new 2024 installations assure multi-year order visibility and accelerate automation and vertical integration strategies across the wind turbine composites market.
Key Report Takeaways
- By fiber type, glass fiber led with 71.66% wind turbine composites market share in 2024; carbon fiber is projected to post the highest 7.11% CAGR through 2030.
- By resin type, epoxy commanded 34.88% revenue share in 2024, while polyester/vinyl-ester systems are set to grow the fastest at 7.45% CAGR to 2030.
- By technology, vacuum infusion held 45.88% of the wind turbine composites market in 2024; prepreg processing is advancing at a 7.77% CAGR, the strongest among manufacturing routes.
- By application, wind blades accounted for 74.88% of the wind turbine composites market size in 2024 and are expanding at a 7.45% CAGR.
- By geography, Asia Pacific represented 46.44% of revenue in 2024 and shows the highest regional growth rate at 6.99% CAGR to 2030.
Global Wind Turbine Composite Materials Market Trends and Insights
Driver Impact Analysis
Drivers | (≈) % Impact on CAGR Forecast | Geographic Relevance | Impact Timeline |
---|---|---|---|
Increasing onshore and offshore turbine capacities | +1.8% | Global; strongest in Asia Pacific and Europe | Medium term (2-4 years) |
Government decarbonization goals and CfD auctions | +1.5% | North America and EU; expanding to Asia Pacific | Short term (≤ 2 years) |
Cost-saving polyurethane infusion resins | +0.9% | Global hubs, notably China and Europe | Medium term (2-4 years) |
Bio-based or recyclable thermoplastic systems | +0.7% | EU and North America first movers | Long term (≥ 4 years) |
Composites with smart-fabric integration | +0.4% | Advanced markets in North America, EU and select Asia Pacific economies | Long term (≥ 4 years) |
Source: Mordor Intelligence
Increasing Onshore and Offshore Turbine Capacities Drive Demand for Advanced Composites
Global turbine ratings now routinely exceed 15 MW offshore, pushing blade lengths past 115 m and multiplying structural loads that only advanced composites can withstand. Vestas’ 115.5 m-long blades on the V236-15 MW platform and Siemens Gamesa’s confidential 21.5 MW prototype exemplify the scale-up that magnifies composite volume per rotor while simultaneously mandating lighter carbon-reinforced spar caps for stiffness and fatigue resistance. The United Kingdom alone aims to raise offshore capacity to as much as 50 GW by 2030, a target that cements long-term pull for high-performance laminate systems able to deliver a 25-year design life in corrosive marine environments[1]Department for Energy Security and Net Zero, “Contracts for Difference Allocation Round,” gov.uk.
Government Decarbonization Policies Accelerate Composite Material Adoption
Supportive frameworks, such as the United Kingdom’s USD 1.2 billion CfD round dedicated to offshore wind and China’s record 117 GW of 2024 wind installations, lock in multi-gigawatt auction pipelines and de-risk investments in new composite plants. Clean-industry bonus mechanisms that reward low-carbon supply chains are encouraging local blade production and greener resin chemistries. The European Green Deal’s binding 2030 renewables targets, along with Germany’s 80% clean-power ambition, consolidate demand visibility across the wind turbine composites market and motivate capacity expansions from Vestas, LM Wind Power, and Chinese glass-fiber majors. Carbon pricing and renewable energy certificates further boost project economics, ensuring sustained pull for lightweight, durable, and recyclable composites.
Polyurethane Infusion Resins Transform Manufacturing Economics
Polyurethane infusion blends from Covestro and Dow lower viscosity, shorten cure cycles by up to one-quarter and yield higher fiber volume fractions, enabling manufacturers to raise throughput without sacrificing fatigue performance. Vestas has already validated the chemistry in production, delivering millions of meters of polyurethane-based laminates for blades in China. Closed-injection pultrusion of carbon spar caps and temperature-controlled molding for thick laminates extend polyurethane’s reach to increasingly complex blade geometries. These capabilities cut per-unit costs and help the wind turbine composites market meet rising demand for ever-longer rotors.
Bio-based Thermoplastic Systems Enable Circular-Economy Transition
NREL’s sorbitol-derived PECAN resin lowers greenhouse-gas output by 40% compared with traditional epoxies and can be depolymerized to recover fibers for reuse, addressing Europe’s strict blade-waste rules. The ZEBRA project’s 62 m fully recyclable thermoplastic blade confirms industrial feasibility and attracts ESG-oriented investors that now scrutinize end-of-life strategies. Westlake’s EpoVIVE formulations and Arkema’s Elium resin widen the palette of circular solutions, while Airbus’ power-to-X composite concept hints at carbon-negative feedstocks. Such advances position recyclable systems as strategic differentiators in the wind turbine composites market.
Restraint Impact Analysis
Restraints | (≈) % Impact on CAGR Forecast | Geographic Relevance | Impact Timeline |
---|---|---|---|
Carbon-fiber price and supply volatility | -1.2% | Global; most acute in premium applications | Short term (≤ 2 years) |
Upcoming BPA and styrene emission limits | -0.8% | North America and EU | Medium term (2-4 years) |
Skilled-labor deficit in advanced infusion | -0.6% | Emerging Asia Pacific, Latin America and parts of EU | Long term (≥ 4 years) |
Source: Mordor Intelligence
Carbon Fiber Price Volatility Constrains Premium Applications
Surging demand for 100 m-plus blades is expected to triple carbon consumption by 2027, yet capacity expansions lag, creating price spikes that discourage wider uptake in cost-sensitive turbines. China’s market, which absorbed 69,000 t of carbon fiber in 2023, saw sharp swings as export restrictions and geopolitical frictions disrupted supply chains. OEMs, therefore, pursue hybrid glass-carbon architectures and localized sourcing to hedge volatility. Until additional lines lift global output toward the 450,000 tons predicted for 2030, the wind turbine composites market must navigate erratic input costs.
Regulatory Emission Limits Drive Manufacturing-Process Transformation
The United States EPA now caps hazardous air pollutants from reinforced-plastic facilities, forcing a pivot to closed molding and low-VOC resins that inflate capital budgets but ensure compliance[2]U.S. Department of Energy, “Wind Supply Chain Roadmap,” energy.gov. In Europe, circular-economy mandates intensify pressure to switch away from styrene-rich chemistries and to document recycling pathways, while OSHA continues workplace-safety crackdowns on styrene exposure in blade shops. Investments in automated infusion cells, emission-capture systems, and hybrid resin lines are therefore imperative across the wind turbine composites market.
Segment Analysis
By Fiber Type: Carbon Drives Premium-Performance Evolution
Glass fiber retained a dominant 71.66% share of the wind turbine composites market in 2024, underpinned by favorable cost and robust supply chains. Carbon, however, is growing at 7.11% CAGR as OEMs chase mass reductions that let longer rotors survive higher tip speeds without excess loads. LM Wind Power’s hybrid carbon/glass spar caps on its 88.4 m blade validated weight cuts without cost blowouts.
Incremental uptake also stems from textile-based carbon fibers that are 40% cheaper than aerospace grades, unlocking mid-tier turbine segments. Natural-fiber blends offer sustainable niches, with palm or flax hybrids matching key mechanical metrics while lowering embodied energy. Over the forecast horizon, hybridization strategies will remain pivotal as the wind turbine composites market balances stiffness, fatigue life and affordability.
Note: Segment shares of all individual segments available upon report purchase
By Resin Type: Polyurethane Challenges Epoxy Dominance
Epoxy systems held 34.88% revenue share in 2024, thanks to well-characterized performance, yet polyester/vinyl-ester and polyurethane blends are tracking the fastest 7.45% CAGR. Proven 10-25% cycle-time savings and improved wet-out make polyurethane infusion the prime candidate for stretching annual output without large capex.
Demand for bio-based chemistries that curb life-cycle emissions by 30-40% will steer formulation research and development, broadening the wind turbine composites market size for greener resins, particularly in Europe, where carbon-footprint disclosures already feature in tenders. Baxxodur curing agents and additive packages that cut exotherm peaks further enhance epoxy competitiveness, ensuring multiple resin classes co-exist through 2030.
By Technology: Prepreg Advances Challenge Vacuum-Infusion Leadership
Vacuum infusion captured 45.88% of the wind turbine composites market share in 2024 due to its scalability for 100 m-class blades. Prepreg throughput, however, will climb 7.77% per year as tighter tolerances on thick spar caps and complex aerodynamic surfaces demand quasi-void-free laminates. Hexcel’s fast-cure HexPly M19 shrinks oven cycles by up to 20%, helping large-scale prepreg plants in Europe and China contend with cost pressures.
By Application: Blade Innovation Anchors Revenue Concentration
Blades represented 74.88% of the wind turbine composites market in 2024 and will continue at a 7.45% CAGR as swept-area expansion is the most powerful lever for higher energy yield. Vestas’ 43,000 m² swept area confirms the volume opportunity, with each 115 m blade containing more than 70 t of composite laminate.
Specialized parts such as spinners, tower fairings, and internal platforms account for modest volumes but remain value-added due to complex tooling and tight dimensional tolerances. Continued research and development into stitched 3-D preforms that slash root assembly time to 10 minutes illuminates how the wind turbine composites market keeps refining cost and structural margins simultaneously.
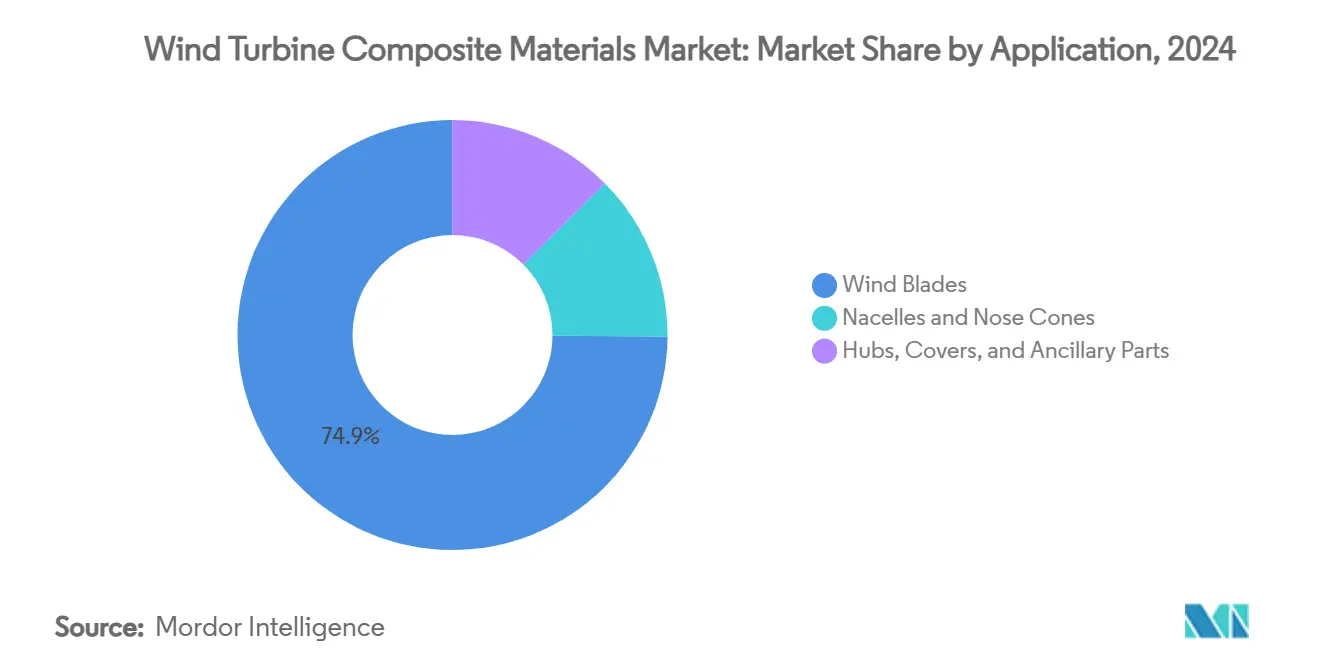
Note: Segment shares of all individual segments available upon report purchase
Geography Analysis
Asia Pacific, at 46.44% of 2024 revenue, remains the anchor region for the wind turbine composites market and posts a leading 6.99% CAGR. China’s record 117 GW of 2024 additions, supported by local-content rules favoring China Jushi and CPIC, underpin an unrivaled supply-chain footprint that exports both raw fabrics and finished blades worldwide.
Europe follows with mature technology adoption and rigorous sustainability regulations. The United Kingdom’s ambition to reach up to 50 GW of offshore wind by 2030, Germany’s 80% clean-power target, and France’s circular-economy mandates push European makers toward recyclable thermoplastics and closed molding.
North America couples federal tax credits with state procurement to expand onshore fleets in the Great Plains and repower coastal wind zones. The U.S. Department of Energy forecasts composite demand tripling by 2027, propelling investments from TPI Composites and GE Vernova that localize spar-cap and root-insert production.
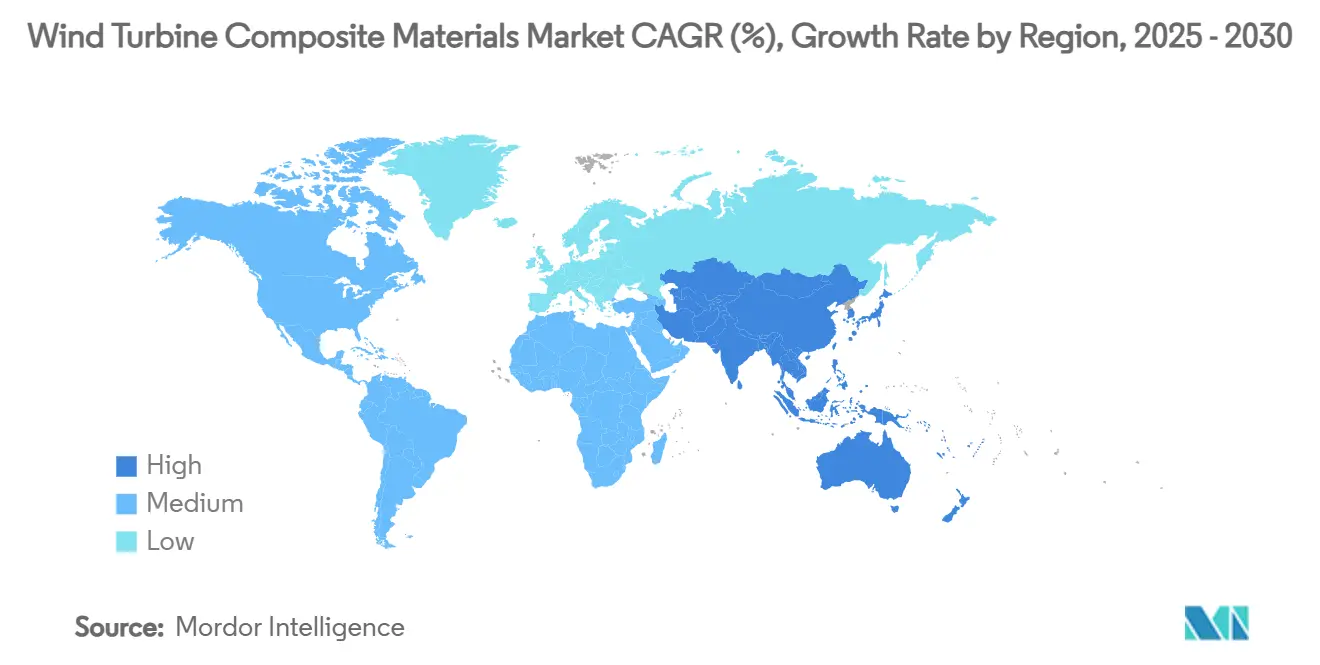
Competitive Landscape
The wind turbine composites market shows moderate fragmentation around global blade specialists, fiber producers, and integrated turbine OEMs. Material suppliers such as Hexcel, Toray, and Owens Corning pursue long contracts with OEMs, co-developing low-void prepregs and high-modulus glass fabrics. Digital-twin platforms, embedded fiber-optic sensors and automated kitting solutions round out competitive toolkits, permitting life-cycle monitoring that reduces maintenance costs.
Wind Turbine Composite Materials Industry Leaders
-
LM WIND POWER
-
Siemens AG
-
TPI Composites
-
Vestas
-
Zhongfu Lianzhong Group
- *Disclaimer: Major Players sorted in no particular order
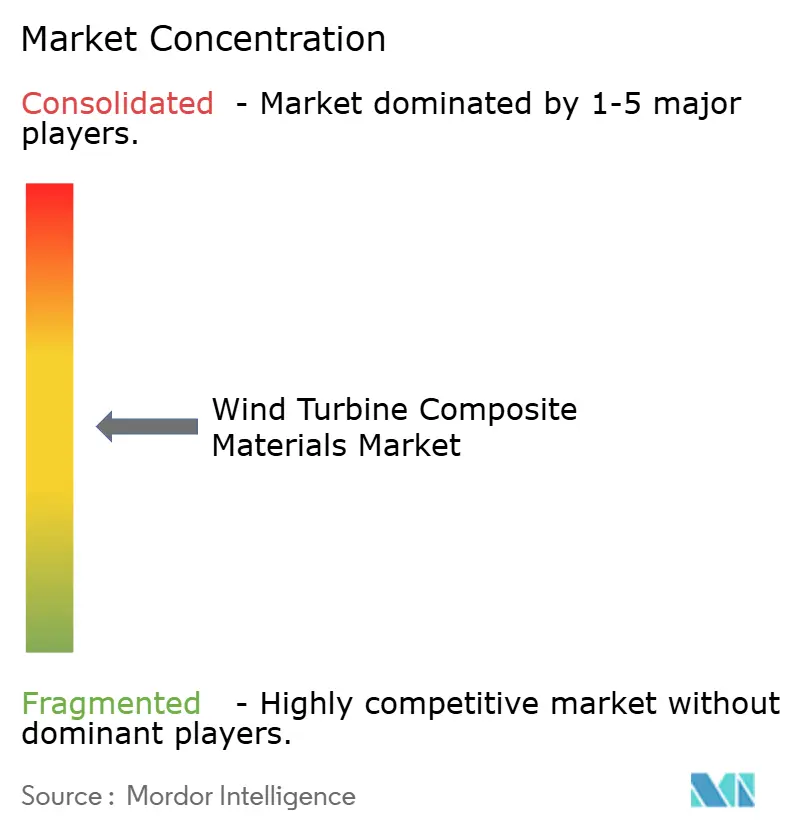
Recent Industry Developments
- April 2023: INCA Renewtech received a USD 40 million commitment to commercialize hemp-based biocomposites, becoming the first vertically integrated natural-fiber supplier for blades.
- April 2023: INCA Renewtech has secured an additional $10 million in funding to accelerate the development of its hemp-processing and composite manufacturing facility. The investment aims to fast-track the company’s sustainable materials production.
Global Wind Turbine Composite Materials Market Report Scope
The Wood Turbine Composites Materials market report include:
By Fiber Type | Glass Fiber | ||
Carbon Fiber | |||
Natural/Hybrid Fibers | |||
By Resin Type | Epoxy | ||
Polyester/Vinyl-Ester | |||
Polyurethane | |||
Thermoplastic Resins | |||
By Technology | Vacuum Infusion | ||
Prepreg | |||
Hand Lay-up | |||
Filament Winding / Pultrusion | |||
By Application | Wind Blades | ||
Nacelles and Nose Cones | |||
Hubs, Covers and Ancillary Parts | |||
By Geography | Asia-Pacific | China | |
India | |||
Japan | |||
South Korea | |||
ASEAN | |||
Rest of Asia-Pacific | |||
North America | United States | ||
Canada | |||
Mexico | |||
Europe | Germany | ||
United Kingdom | |||
France | |||
Italy | |||
Spain | |||
Rest of Europe | |||
South America | Brazil | ||
Argentina | |||
Rest of South America | |||
Middle-East and Africa | Saudi Arabia | ||
United Arab Emirates | |||
South Africa | |||
Egypt | |||
Rest of Middle-East and Africa |
Glass Fiber |
Carbon Fiber |
Natural/Hybrid Fibers |
Epoxy |
Polyester/Vinyl-Ester |
Polyurethane |
Thermoplastic Resins |
Vacuum Infusion |
Prepreg |
Hand Lay-up |
Filament Winding / Pultrusion |
Wind Blades |
Nacelles and Nose Cones |
Hubs, Covers and Ancillary Parts |
Asia-Pacific | China |
India | |
Japan | |
South Korea | |
ASEAN | |
Rest of Asia-Pacific | |
North America | United States |
Canada | |
Mexico | |
Europe | Germany |
United Kingdom | |
France | |
Italy | |
Spain | |
Rest of Europe | |
South America | Brazil |
Argentina | |
Rest of South America | |
Middle-East and Africa | Saudi Arabia |
United Arab Emirates | |
South Africa | |
Egypt | |
Rest of Middle-East and Africa |
Key Questions Answered in the Report
What is the current value of the wind turbine composites market?
The wind turbine composites market was valued at USD 13.45 billion in 2025 and is projected to reach USD 18.22 billion by 2030, reflecting a 6.26% CAGR.
Which region leads the wind turbine composites market?
Asia Pacific led with 46.44% revenue share in 2024 and is also the fastest-growing region at 6.99% CAGR through 2030, driven primarily by China’s large-scale wind installations.
Which fiber type is growing fastest in wind turbine blades?
Carbon fiber is expanding at 7.11% CAGR as OEMs adopt hybrid carbon/glass spar caps to cut weight in blades longer than 100 m.
How are new resins improving blade manufacturing?
Polyurethane infusion resins reduce mold cycle times by up to 25% and improve fiber wet-out, increasing factory throughput while meeting fatigue-life requirements.
Why are recyclable thermoplastic composites gaining attention?
European circular-economy rules and ESG finance mandates are steering OEMs toward thermoplastic systems like Elium or bio-based PECAN that enable full material recovery at end of life.
Page last updated on: July 9, 2025