Oil Condition Monitoring Market Size and Share
Oil Condition Monitoring Market Analysis by Mordor Intelligence
The oil condition monitoring market is valued at USD 1.88 billion in 2025 and is projected to reach USD 2.53 billion by 2030, expanding at a 6.12% CAGR. Growth is fueled by rapid adoption of predictive maintenance programs, especially in capital-intensive sectors where unplanned downtime invites significant operating losses. IoT-enabled sensors now transmit lubricant quality data to cloud platforms, allowing real-time diagnostics that replace calendar-based sampling. Energy security concerns have encouraged LNG carrier owners and offshore wind operators to install continuous wear-debris monitors, while tightening sustainability rules in Europe and North America boost demand for analytics that extend oil life. Competitive intensity has increased as bearing manufacturers, sensor specialists, and digital-twin software firms converge around integrated asset-health ecosystems, widening the addressable customer base within the oil condition monitoring market.
Key Report Takeaways
- By sampling type, off-site laboratory services led with 60% revenue share in 2024; on-site systems are advancing at a 9.4% CAGR through 2030.
- By equipment application, engines captured 32.3% of the oil condition monitoring market share in 2024, while hydraulic systems post the highest 9.0% CAGR to 2030.
- By sensor technology, viscosity sensors accounted for 24% share of the oil condition monitoring market size in 2024; ferrous debris counters are forecast to expand at an 11.5% CAGR.
- By service offering, laboratory testing commanded 55% of the oil condition monitoring market size in 2024; software and analytics platforms lead future growth at 12.8% CAGR.
- By end-user, oil & gas contributed 28% of the oil condition monitoring market in 2024; renewable energy is the fastest-growing vertical at 10.1% CAGR.
- Regionally, North America dominated with a 34.77% share in 2024, while Asia-Pacific is set to record the fastest 8.3% CAGR.
Global Oil Condition Monitoring Market Trends and Insights
Drivers Impact Analysis
DRIVER | (~) % IMPACT ON CAGR FORECAST | GEOGRAPHIC RELEVANCE | IMPACT TIMELINE |
---|---|---|---|
OEM warranty mandates on lubricant analytics | +0.8% | North America | Short term (≤ 2 years) |
Offshore wind gearbox failures spurring debris sensors | +0.7% | Europe | Medium term (2-4 years) |
LNG fleet expansion requiring real-time monitoring | +0.9% | Asia-Pacific & Middle East | Long term (≥ 4 years) |
Digital-twin programs in Canadian oil sands | +0.5% | North America | Medium term (2-4 years) |
Mining-insurance incentives for wear monitoring | +0.4% | South America | Short term (≤ 2 years) |
EU CSRD sustainability rules on oil-life extension | +0.6% | Europe | Long term (≥ 4 years) |
Source: Mordor Intelligence
OEM warranty mandates
North American heavy-duty OEMs have started tying extended engine warranties to routine submission of oil spectrography reports, driving accelerated uptake of the oil condition monitoring market within dealer networks. The program reduces OEM liability by catching early contamination and wear, while fleet operators gain longer engine life and optimized drain intervals. Major Class-8 truck builders now bundle sensor kits with power-train service contracts, nudging independent maintenance shops toward cloud-based dashboards that can ingest OEM telematics feeds. As warranty cost avoidance is quantified in predictive models, CFOs reallocate budgets from reactive repairs to predictive analytics subscriptions. Adoption remains highest in fleets with 300-plus vehicles that amortize sensor investments quickly.[1] U.S. Environmental Protection Agency, “Heavy-Duty Engine and Vehicle Standards,” epa.gov
Offshore wind gearbox failures
Europe’s offshore wind segment experiences gearbox replacement costs that exceed USD 200,000 per turbine, creating a robust business case for inline ferrous-debris monitors. Operators use real-time metal-particle counts to shift from calendar-based drains to data-dictated interventions, reducing crane-vessel deployments in harsh North Sea conditions. Sensor retrofits integrate with SCADA platforms and feed digital twins that model torque, vibration, and lubricant contamination concurrently. EU and UK subsidy structures penalize non-availability, so operators favor technologies that guarantee high service factors. Vendors offering pre-calibrated AI models gain traction because they reduce commissioning complexity, shrinking the payback period to under 18 months.
LNG fleet expansion
Asia-Pacific and Middle East shipyards have a combined orderbook exceeding 200 LNG carriers for delivery through 2030. The engines and cryogenic cargo pumps aboard these vessels demand pristine oil films under fluctuating load profiles, making real-time condition monitoring indispensable. Classification societies now recommend viscosity and PQ-index sensors for dual-fuel two-stroke engines, spurring orders for multiparameter probes rated to Zone 0 hazardous areas. Cloud connectivity enables shore-side engineers to trend wear rates across fleets and pre-position spares before dry-dock windows. As charterers insert uptime clauses in long-term contracts, shipowners view continuous monitoring as a compliance and revenue-assurance tool, accelerating growth of the oil condition monitoring market.
Digital-twin programs in Canadian oil sands
Surface mining assets in Alberta encounter abrasive contaminants that accelerate lubricant degradation. Producers deploy digital twins that fuse load, temperature, and oil chemistry, predicting component failure up to four weeks in advance. Pilot projects on 797F haul trucks recorded a 70% cut in downtime and a USD 2.5 million annual maintenance saving per fleet. Data platforms interface with pit-dispatch systems, balancing production scheduling against maintenance windows. Vendor collaborations focus on edge analytics that filter high-frequency data locally, reducing satellite bandwidth costs and mitigating cybersecurity risks associated with remote sites.
Restraints Impact Analysis
RESTRAINTS | (~) % IMPACT ON CAGR FORECAST | GEOGRAPHIC RELEVANCE | IMPACT TIMELINE |
---|---|---|---|
Capex Burden of Online Sensors for ASEAN SMEs | -0.9% | ASEAN core, spill-over to other emerging markets | Short term (≤ 2 years) |
Legacy SCADA Integration Issues in US Midstream Pipelines | -0.7% | North America, some EU applications | Medium term (2-4 years) |
Shortage of Tribologists in African Power Utilities | -0.5% | Sub-Saharan Africa, expanding to Middle East | Long term (≥ 4 years) |
Ferrography Consumable Supply Disruptions in Eastern Europe | -0.4% | Eastern Europe, spill-over to Central Asia | Short term (≤ 2 years) |
Source: Mordor Intelligence
Capex Burden of Online Sensors for ASEAN SMEs
Small and medium enterprises across ASEAN markets face significant capital expenditure constraints that limit adoption of online oil condition monitoring systems, despite clear operational benefits. The ASEAN SME Policy Index 2024 highlights that SMEs contribute 64.6% of regional employment and 38.3% to GDP, yet face persistent challenges in accessing capital for technology investments. Online sensor systems typically require USD 5,000-15,000 initial investment per monitoring point, representing a substantial financial barrier for manufacturing SMEs operating on thin margins. The region's heavy reliance on fossil fuels, with oil demand expected to increase 20% by 2035 and annual import bills exceeding USD 200 billion, creates additional cost pressures that limit discretionary technology spending.[2]Asian Development Bank, “SME Digitalization Financing in ASEAN,” adb.org
Legacy SCADA Integration Issues in US Midstream Pipelines
Aging SCADA infrastructure across U.S. midstream pipeline networks creates substantial technical and economic barriers to implementing modern oil condition monitoring systems. The Center for Midstream Management and Science identifies aging infrastructure as a critical industry concern, with many pipeline operators struggling to integrate new monitoring technologies with legacy control systems. SCADA systems installed 15-20 years ago often lack the communication protocols and processing capabilities required for real-time oil analytics integration, necessitating expensive infrastructure upgrades that can cost millions of dollars per facility.
Segment Analysis
By Sampling Type: Off-site Dominance, On-site Momentum
Off-site laboratory testing commanded 60% of the oil condition monitoring market in 2024 as heavy industry continued to rely on accredited labs for comprehensive elemental and contamination analyses. The model offers deep data sets but introduces lags between sampling and decision-making, sometimes leading to reactive maintenance. Large refineries and power plants maintain yearly contracts with regional labs covering ICP, FTIR, and ferrous density tests. However, courier delays and manual data entry remain pain points.
On-site systems are the fastest-growing segment, expanding at a 9.4% CAGR as IoT mini-labs shrink footprint and cost. Portable viscometers and infrared spectrometers now fit into ruggedized cases, allowing technicians to cut turnaround time from days to minutes. Plants with continuous processes appreciate the closed-loop feedback that lets them adjust load profiles or filtration regimes immediately. Subscription models offer calibration services and cloud dashboards that archive historic trends across multiple sites. By 2030, on-site deployments could erode the oil condition monitoring market share of external labs among mid-tier manufacturers while labs pivot toward data science services.
By Equipment Application: Engine Reliability Tops, Hydraulics Accelerate
Engines remained the largest application, holding 32.3% of the oil condition monitoring market share in 2024. High-speed rotating parts create metal wear, soot, and acid that demand early detection. Commercial marine, mining haul trucks, and standby power gensets increasingly embed cylinder-liner wear models in enterprise maintenance planning. Extended drain intervals driven by low-sulfur and bio-blend fuels further underline the need for precise lubricant chemistry insights.
Hydraulic systems are projected to grow at 9.0% CAGR as factory automation and mobile equipment sophistication rise. Electrohydraulic actuators in injection-molding lines and precision presses rely on contaminant-free fluids to sustain micron-level tolerances. OEMs now pre-install 4-14 µm particle counters and moisture sensors that alert control-room PLCs in real time. With every unscheduled hydraulic failure reputed to cost USD 12,000 per hour in automotive stamping plants, operators justify sensor investments within a single incident avoidance. The oil condition monitoring market size for hydraulics will expand further as the global motion-control base broadens.
By Sensor Technology: Viscosity Platforms Lead, Debris Counters Surge
Viscosity sensors contributed 24% of revenue in 2024 thanks to their broad applicability across engines, turbines, and compressors. As next-generation 0W-20 oils enter heavy-duty fleets under 2027 EPA rules, viscosity monitoring remains central to warranty compliance. Continuous-reading MEMS viscometers, such as the SPL571 from Cambridge Applied Systems, now output kinematic values directly to cloud dashboards.
Ferrous-debris counters are forecast to log the fastest 11.5% CAGR, especially in offshore wind and mining. Hall-effect and inductive technologies detect sub-5 µm particles that predict bearing pitting well before vibration shifts signal damage. As gearbox manufacturers warrant availability under energy-as-a-service contracts, embedded debris counters become standard, adding recurring analytics revenue for vendors. This dynamic will enlarge the oil condition monitoring market size in high-torque applications through 2030.[3]Cambridge Applied Systems, “SPL571 Viscometer Datasheet,” cambridgeapplied.com
By Service Offering: Laboratory Testing Dominates, Software Takes Off
Laboratory testing represented 55% of the oil condition monitoring market size in 2024. Accredited labs remain indispensable for root-cause failure analysis, especially after warranty claims. They also benchmark additive depletion profiles for formulating drain-interval extensions. Yet their dominance is thinning as analytics platforms post a 12.8% CAGR, reflecting the pivot toward real-time decision support.
Software vendors bundle dashboards, machine-learning models, and ERP connectors that close the loop between detection and work-order generation. Predictive scoring algorithms correlate lubricant anomalies with process data, quantifying failure probability and financial risk. As plants adopt OEE-based performance incentives, maintenance teams rely on heat-map visualizations that prioritize interventions. The oil condition monitoring market will witness greater value migration from hardware to SaaS by decade-end.
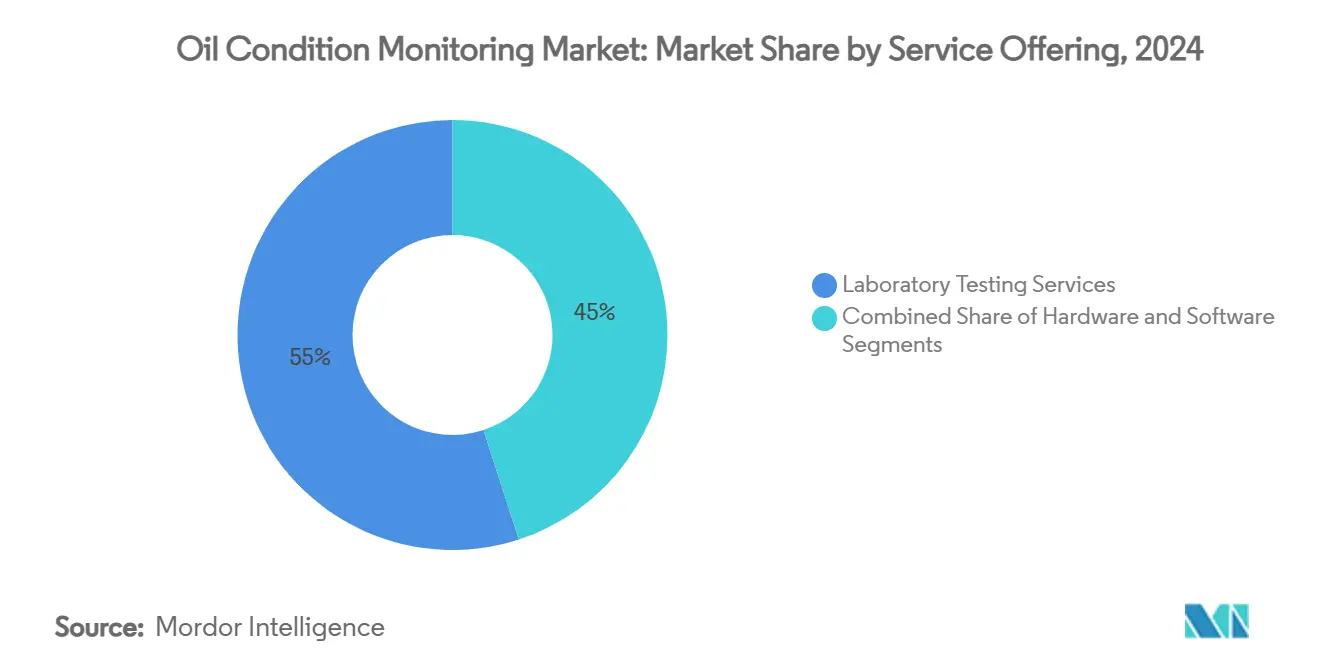
Note: Segment shares of all individual segments available upon report purchase
By End-User: Oil & Gas Largest, Renewables Fastest
Oil & gas operators accounted for 28% of global spending in 2024. Complex assets such as compressor trains, drilling rigs, and FPSOs operate in harsh conditions where lubricant degradation can trigger safety incidents. National oil companies therefore embed analytics into brownfield upgrades to maintain asset integrity during life-extension projects. The sector’s cyclic CAPEX can, however, temper year-to-year growth.
Renewable-energy owners are projected to record a 10.1% CAGR, reflecting the massive scale-up of offshore wind and utility-scale solar trackers. Stakeholders look to minimize lifecycle emissions not only through clean power generation but also through circular maintenance. Gearbox-oil life-extension goals align with EU CSRD reporting, helping developers secure green financing. As installed wind capacity crosses 190 GW offshore by 2030, the oil condition monitoring market will pivot from conventional fuels toward clean-energy infrastructure.
Geography Analysis
North America led the oil condition monitoring market with 34.77% revenue share in 2024. Stringent CAFE fuel-efficiency targets and forthcoming 2027 heavy-duty engine oil viscosity standards compel fleets to adopt real-time viscometers, bolstering supplier revenue. Legacy SCADA in midstream pipelines restrains sensor retrofits, yet federal funding for critical-infrastructure upgrades may unlock latent demand.
Europe remains the technology incubator, leveraging offshore wind deployment and circular-economy regulations to push oil-life-extension solutions. The EU CSRD forces manufacturers to disclose lubricant conservation metrics, turning compliance into a board-level priority. Scandinavian shipowners also prepare for the Arctic heavy-fuel-oil ban by Transport Canada, investing in condition monitoring to ensure alternative fuels maintain viscosity within safe ranges.
Asia-Pacific is the fastest-growing region at 8.3% CAGR as industrialization, LNG fleet growth, and mining automation converge. Governments raise safety standards in petrochemical complexes, creating opportunities for cloud-linked sensors. Yet small and mid-size enterprises face capital constraints, prompting vendors to roll out leasing schemes. In emerging ASEAN markets, off-site labs still dominate, although falling hardware costs will slowly tilt share toward in-plant online sensors, expanding the overall oil condition monitoring market.
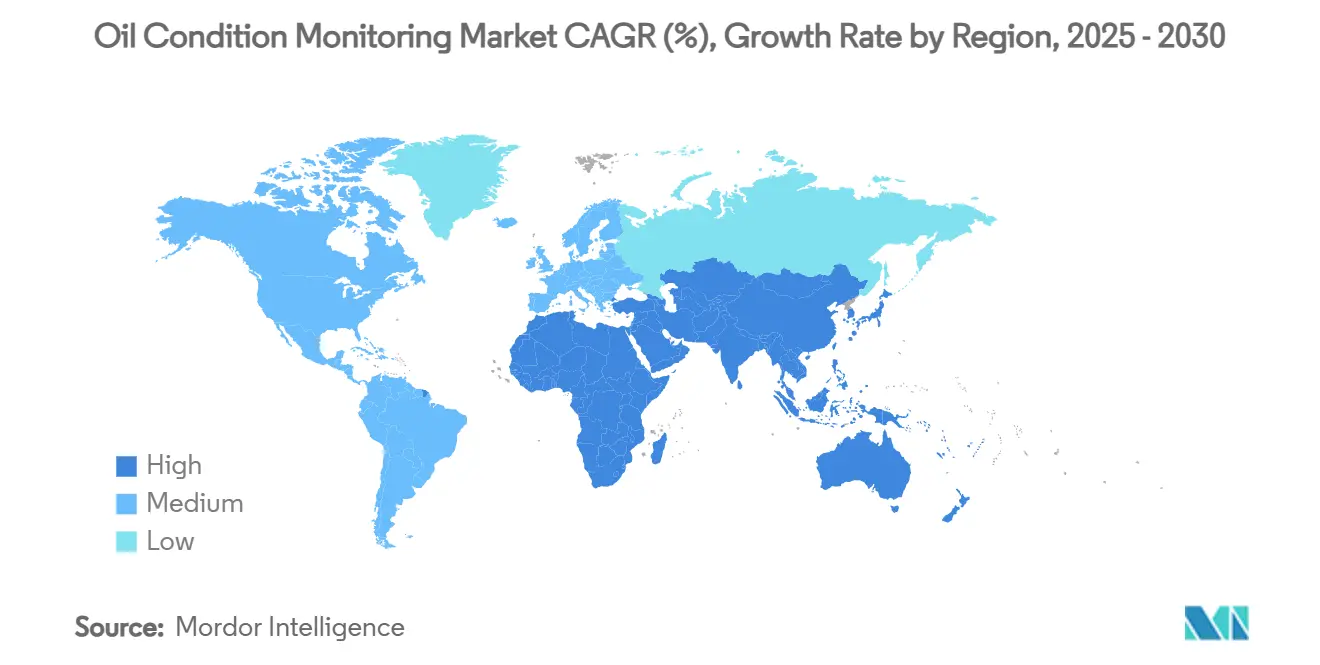
Competitive Landscape
The oil condition monitoring market exhibits moderate fragmentation. Major bearing suppliers, sensor boutiques, and software specialists overlap in value propositions, fueling partnerships and M&A. SKF’s SEK 550 million acquisition of John Sample Group in 2024 expanded its lubrication-management footprint and distribution presence in Southeast Asia. Similar vertical integrations aim to pair mechanical expertise with data sciences, allowing turnkey asset-health solutions.
Sensor innovators focus on multiparameter devices that measure viscosity, dielectric constant, and ferrous debris in one probe, cutting installation costs and simplifying analytics. Cambridge Applied Systems launched the SPL571 viscometer capable of delivering dashboard-ready readings, demonstrating the shift toward plug-and-play designs. AI start-ups add anomaly-detection layers that flag deviations earlier than threshold rules, differentiating offerings in a price-sensitive market.
Cloud-based software platforms battle for enterprise contracts by integrating with EAM and ERP suites. Vendors highlight cybersecurity certifications and low-latency edge architectures to win contracts in regulated utilities. As recurring SaaS revenue rises, equipment manufacturers embed software subscriptions in hardware pricing, blurring competitive lines. Market leaders offer joint warranties covering sensor hardware, data analytics, and on-site service, reinforcing switching costs and increasing market concentration.
Oil Condition Monitoring Industry Leaders
-
General Electric Company
-
Exxon Mobil Corporation
-
Chevron Corporation
-
Shell plc
-
TotalEnergies SE
- *Disclaimer: Major Players sorted in no particular order
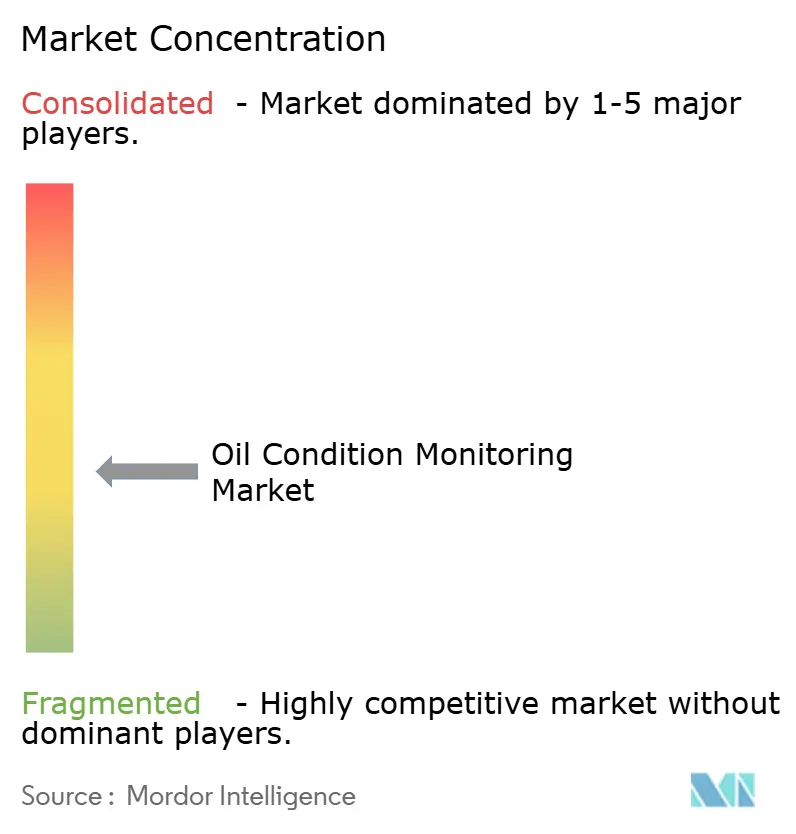
Recent Industry Developments
- March 2025: Cambridge Applied Systems launched the SPL571 viscometer for real-time oil viscosity monitoring, enabling dashboard-based condition assessment that captures transient chemistry changes impossible to detect through traditional sampling methods. The technology is being tested by major engine manufacturers and offers significant advantages in reducing new model development times while improving oil change recommendation accuracy.
- January 2025: Kongsberg Digital expanded its digital twin platform capabilities for midstream oil and gas operations, introducing enhanced real-time monitoring and predictive analytics features that create integrated data management solutions for pipeline operators. The platform integrates 12,000 data points per facility to enable single-operator management of complex industrial installations.
- December 2024: U.S. Departments of Energy, Transportation, and Housing published an action plan for medium and heavy-duty vehicle emissions innovation, targeting 30% zero-emission vehicle sales by 2030 and 100% by 2040. The plan emphasizes enhanced monitoring requirements for remaining internal combustion engines and sustainable liquid fuel applications.
- August 2024: SKF completed acquisition of John Sample Group's Lubrication and Flow Management businesses for approximately SEK 550 million, strengthening its position in India and Southeast Asia markets. The deal increases SKF's Lubrication Management business net sales to around SEK 7 billion and provides access to mining and food processing industry customers.
Global Oil Condition Monitoring Market Report Scope
- The Oil Condition Monitoring refers to a predictive maintenance program that measures, monitors, and analyses the changes that occur in lubricant and fuel oils for chemicals and containments. It provides a vital warning regarding the degradation in the quality of oil from new to end-of-life thereby supports the reliability of the machine
- The reports cover the emerging trends in the oil condition monitoring market segmented by sampling type, measurement type, product type, and Industry across different regions studied.
By Sampling Type | On-Site (On-board, Fixed Continuous Monitoring) | ||
Off-Site (Laboratory-based) | |||
By Product / Equipment Type | Turbines | ||
Engines | |||
Gear Systems | |||
Hydraulic Systems | |||
Compressors | |||
By Sensor / Measurement Type | Viscosity Sensors | ||
Temperature Sensors | |||
Pressure Sensors | |||
Dielectric Constant Sensors | |||
Ferrous Debris Counters | |||
TAN/TBN Analyzers | |||
Soot and Oxidation Meters | |||
Water and Fuel Dilution Detectors | |||
By Service Offering | Hardware and Inline Instrumentation | ||
Software and Analytics Platforms | |||
Laboratory Testing Services | |||
By End-user Industry | Transportation (Road, Rail, Aviation) | ||
Oil and Gas | |||
Industrial Manufacturing | |||
Mining | |||
Power Generation | |||
Marine | |||
Aerospace and Defense | |||
Renewable Energy (Wind, Solar Thermal) | |||
By Geography | North America | United States | |
Canada | |||
Mexico | |||
Europe | United Kingdom | ||
Germany | |||
France | |||
Italy | |||
Rest of Europe | |||
Asia-Pacific | China | ||
Japan | |||
India | |||
South Korea | |||
Rest of Asia-Pacific | |||
Middle East | Israel | ||
Saudi Arabia | |||
United Arab Emirates | |||
Turkey | |||
Rest of Middle East | |||
Africa | South Africa | ||
Egypt | |||
Rest of Africa | |||
South America | Brazil | ||
Argentina | |||
Rest of South America |
On-Site (On-board, Fixed Continuous Monitoring) |
Off-Site (Laboratory-based) |
Turbines |
Engines |
Gear Systems |
Hydraulic Systems |
Compressors |
Viscosity Sensors |
Temperature Sensors |
Pressure Sensors |
Dielectric Constant Sensors |
Ferrous Debris Counters |
TAN/TBN Analyzers |
Soot and Oxidation Meters |
Water and Fuel Dilution Detectors |
Hardware and Inline Instrumentation |
Software and Analytics Platforms |
Laboratory Testing Services |
Transportation (Road, Rail, Aviation) |
Oil and Gas |
Industrial Manufacturing |
Mining |
Power Generation |
Marine |
Aerospace and Defense |
Renewable Energy (Wind, Solar Thermal) |
North America | United States |
Canada | |
Mexico | |
Europe | United Kingdom |
Germany | |
France | |
Italy | |
Rest of Europe | |
Asia-Pacific | China |
Japan | |
India | |
South Korea | |
Rest of Asia-Pacific | |
Middle East | Israel |
Saudi Arabia | |
United Arab Emirates | |
Turkey | |
Rest of Middle East | |
Africa | South Africa |
Egypt | |
Rest of Africa | |
South America | Brazil |
Argentina | |
Rest of South America |
Key Questions Answered in the Report
What is the current size of the oil condition monitoring market?
The oil condition monitoring market is valued at USD 1.88 billion in 2025 and is forecast to reach USD 2.53 billion by 2030 at a 6.12% CAGR.
Which region leads the oil condition monitoring market?
North America leads with a 34.77% share, driven by stringent emission and warranty regulations.
What segment within equipment applications is growing the fastest?
Hydraulic systems are advancing at a 9.0% CAGR, outpacing engines in growth momentum.
How are regulations influencing market demand?
EPA low-viscosity oil standards, EU CSRD sustainability reporting, and Arctic heavy-fuel-oil bans compel industries to adopt real-time oil monitoring solutions.
Why are on-site systems gaining traction over laboratory services?
On-site systems cut sample-to-decision time from days to minutes, enabling immediate corrective action and reducing unplanned downtime.
Which technology trend offers the largest efficiency gains?
Digital-twin platforms that integrate oil analytics with operational data have demonstrated up to 70% reductions in unplanned downtime for heavy equipment fleets.
Page last updated on: July 6, 2025