Industrial Robotics Market Size and Share
Industrial Robotics Market Analysis by Mordor Intelligence
The industrial robotics market stands at USD 48.3 billion in 2025 and is projected to reach USD 90.6 billion by 2030, advancing at a 13.4% CAGR. Rapid integration of artificial intelligence, mounting labor shortages, and tariff-driven reshoring have moved robots from isolated automation tools to central, adaptive systems that keep production running amid volatile supply chains. Asia’s sustained appetite for factory automation, the United States’ accelerated expensing incentives, and European sustainability mandates together underpin a demand cycle that remains resilient even during macroeconomic slowdowns. Government incentives such as China’s 14th Five-Year Plan and Japan’s New Robot Strategy continue to lower investment risk while embedded AI and 5G networks lift overall equipment effectiveness. Competitive intensity is growing as collaborative robot pioneers challenge incumbents, yet scale advantages held by ABB, FANUC, Yaskawa, and KUKA still shape price discipline and service expectations in the industrial robotics market.
Key Report Takeaways
- By robot type, articulated robots led with 67% of industrial robotics market share in 2024, while collaborative robots are forecast to expand at a 14.0% CAGR through 2030.
- By payload capacity, the 16-225 kg band captured 42% share of the industrial robotics market size in 2024; the ≤15 kg segment is projected to grow at 15.2% CAGR to 2030.
- By application, material handling accounted for 33% share of the industrial robotics market size in 2024, whereas quality inspection is climbing at a 13.8% CAGR to 2030.
- By end-user industry, automotive held 25% of the industrial robotics market share in 2024 and food & beverage is advancing at 12.4% CAGR through 2030.
- By geography, Asia dominated with 70% revenue share in 2024; South America represents the fastest-growing region, poised for an 11.5% CAGR to 2030.
Global Industrial Robotics Market Trends and Insights
Drivers Impact Analysis
Driver | (~) % Impact on CAGR Forecast | Geographic Relevance | Impact Timeline |
---|---|---|---|
Rising labor costs & ageing workforce | 3.20% | Global, acute in Japan, Germany, South Korea | Long term (≥ 4 years) |
Rapid adoption of AI & IIoT-enabled smart factories | 2.80% | North America, Europe, core Asian markets | Medium term (2-4 years) |
Government cap-ex subsidies for automation | 2.10% | China, Korea, Germany | Short term (≤ 2 years) |
Tariff-driven reshoring fuels US automation spend | 1.90% | North America, secondary impact in Mexico | Medium term (2-4 years) |
Source: Mordor Intelligence |
Rising Labor Costs & Ageing Workforce
Escalating wages and shrinking labor pools push manufacturers to automate tasks that once relied on abundant human labor. Japan’s robot density reached 390 units per 10,000 workers in 2024, while Germany’s density climbed to 429, underscoring how advanced economies lean on robots to preserve productivity [1]ifr.org China’s climb in manufacturing wages has re-tilted total cost of ownership models, making payback periods for robotic cells shorter than in 2019. Companies also deploy collaborative robots in ergonomically demanding stations to retain experienced workers who can no longer perform repetitive lifting. The demographic squeeze simultaneously drives up turnover and erodes tacit knowledge; robots mitigate that risk by executing standardized workflows that preserve process memory for the next generation of employees.
Rapid Adoption of AI & IIoT-Enabled Smart Factories
Artificial intelligence turns robots into self-optimizing assets that learn from sensor feedback. NVIDIA’s Isaac platform allows manufacturers such as Siemens to develop digital twins, cut commissioning time, and reduce unplanned downtime by up to 30%[2]nvidianews.nvidia.com . Machine learning vision now classifies new SKUs without offline programming, enabling same-shift changeovers in e-commerce fulfillment. Edge computing processes high-frequency torque data, predicting bearing wear before catastrophic failure, while private 5G networks push control loops closer to actuators. These capabilities transform the industrial robotics market from simple repeatability toward data-driven adaptability, which is critical for just-in-time, high-mix factories.
Government Cap-ex Subsidies for Automation
Strategic public-sector spending remains a visible hand accelerating adoption. China earmarked USD 45 million for homegrown robotics during the 14th Five-Year Plan, while Korea invested USD 128 million to expand intelligent robot exports. The European Union’s Horizon Europe program directs significant funding toward energy-efficient robots that support circular-economy goals. These grants compress return-on-investment thresholds, placing automation within reach of tier-2 auto suppliers and mid-cap electronics assemblers. However, the paperwork favors large enterprises, widening capability gaps between global multinationals and small manufacturers.
Tariff-Driven Reshoring Fuels US Automation Spend
Trade-policy volatility and supply chain shocks have triggered a structural rethink of global footprints. IRS Section 179’s 100% expensing of robotics shortens payback cycles in North America,[3]Futura Automation, "USA IRS Section 179 – 100% Expensing for Robotic Automation", Futura Automation, futura-automation.comincentivizing production relocation closer to consumer markets. Automotive OEMs installing battery-module lines in Michigan combine heavy six-axis welders with mobile autonomous carts to offset high hourly wages. Collaborative robots that require no safety cages fit brown-field sites where floor space is limited. As a result, the industrial robotics market enjoys stickier demand even when consumer cycles soften because factories need resilience more than volume efficiency.
Restraints Impact Analysis
Restraint | (~) % Impact on CAGR Forecast | Geographic Relevance | Impact Timeline |
---|---|---|---|
High upfront cap-ex for SMEs | -2.70% | Global, acute in emerging markets | Medium term (2-4 years) |
Scarcity of robot-integration talent | -1.80% | Global, strongest in developing economies | Long term (≥ 4 years) |
Source: Mordor Intelligence |
High Upfront Cap-ex for SMEs
Turnkey robotic cells still cost between USD 50,000 and USD 500,000, and that range excludes opportunity costs from line downtime during installation. While Robot-as-a-Service converts capital outlays into monthly operating expenses, smaller plants remain wary of multi-year subscription liabilities. Financial constraints are tighter in emerging markets where commercial credit spreads exceed double digits, and public subsidy schemes focus on large exporters rather than local job shops. Without scale to amortize engineering effort across multiple sites, many SMEs delay automation, slowing overall penetration of the industrial robotics market despite compelling productivity gains.
Scarcity of Robot-Integration Talent
Demand for controls engineers and maintenance technicians routinely outstrips supply, adding hidden costs to every new deployment. Technical colleges refresh curricula slower than six-month release cycles of robot operating systems. Manufacturers therefore rely on a limited pool of system integrators whose day rates continue to climb, elongating payback periods. In fast-growing economies such as India, the talent gap is amplified by rapid capacity additions, creating longer lead times between purchasing robots and achieving steady-state output. Vendors have responded with drag-and-drop programming and remote support, yet multidomain expertise in welding processes, machine vision, and network security remains scarce, capping adoption velocity.
Segment Analysis
By Robot Type: Collaborative Surge Challenges Traditional Dominance
Articulated systems retained 67% share of the industrial robotics market in 2024 as six-axis flexibility supports welding, painting, and sealant application in automotive plants that run near-continuous shifts. Extensive installed bases guarantee spare-parts availability, protecting uptime commitments for OEMs. Meanwhile, collaborative robots held 10.5% share but are riding a 14.0% CAGR, driven by safety-rated force sensors that allow operators to work shoulder-to-shoulder without cages. Integrators now mount cobots on autonomous mobile platforms, creating re-deployable workcells that address labor gaps on multiple lines.
Growth momentum continues as lightweight arms automate tasks below 15 kg that previously relied on manual dexterity. Food processors use hygienic stainless-steel cobots to package ready-to-eat meals, while electronics assemblers teach robots new pick points via hand-guiding within minutes. SCARA and delta robots still dominate high-speed pick-and-place operations, yet their unit growth trails cobots because they lack built-in safety functions. Over the forecast period, AI-powered programming lowers barriers for non-experts, ensuring collaborative platforms remain the vanguard of volume expansion in the industrial robotics market.
Note: Segment shares of all individual segments available upon report purchase
By Payload Capacity: Precision Applications Drive Lightweight Growth
Robots rated 16-225 kg captured 42% of the industrial robotics market size in 2024, underpinning automotive under-body welding, engine block handling, and palletizing in beverage plants. Manufacturers appreciate the balance between reach, inertia control, and cost per kilogram of payload. Conversely, the ≤15 kg class will post a 15.2% CAGR through 2030 because shrinking component geometries in smartphones and medical devices necessitate micron-level precision at higher cycle rates. Vacuum grippers paired with advanced vision enable these smaller robots to handle flexible materials once thought impossible in automated systems.
Heavy-duty robots above 226 kg remain critical for aerospace fuselage riveting and large casting finishing where no alternative automation exists. However, their growth is modest because investment outlays are higher and demand cycles correlate with long-lead capital goods orders. As force-torque sensors and high-strength composites reduce manipulator weight, tasks once assigned to mid-payload units migrate downward, expanding addressable opportunities for the light segment without cannibalizing core volumes of established categories.
By Application: Quality Inspection Emerges as AI-Powered Growth Driver
Material handling preserved 33% contribution to the industrial robotics market size in 2024 thanks to standardized interfaces with conveyors, AGVs, and warehouse management software. Automated tote transfer delivers immediate labor savings and ergonomic benefits, making it the default entry point for plants that are early in their automation journey. Quality inspection, however, is racing ahead at a 13.8% CAGR on the strength of machine vision systems that now detect sub-millimeter defects in painted surfaces and solder joints, outpacing human inspectors in both speed and repeatability.
Predictive analytics shifts quality control from post-process sampling to in-line verification, allowing root-cause corrections before scrap accumulates. Welding and soldering remain staple applications as they deliver quantifiable reductions in rework. Meanwhile, painting robots equipped with closed-loop flow meters cut overspray, directly supporting corporate sustainability goals. The breadth of tasks now addressable by camera-guided manipulators enlarges the industrial robotics market’s value proposition beyond throughput gains to include warranty cost avoidance and brand protection.
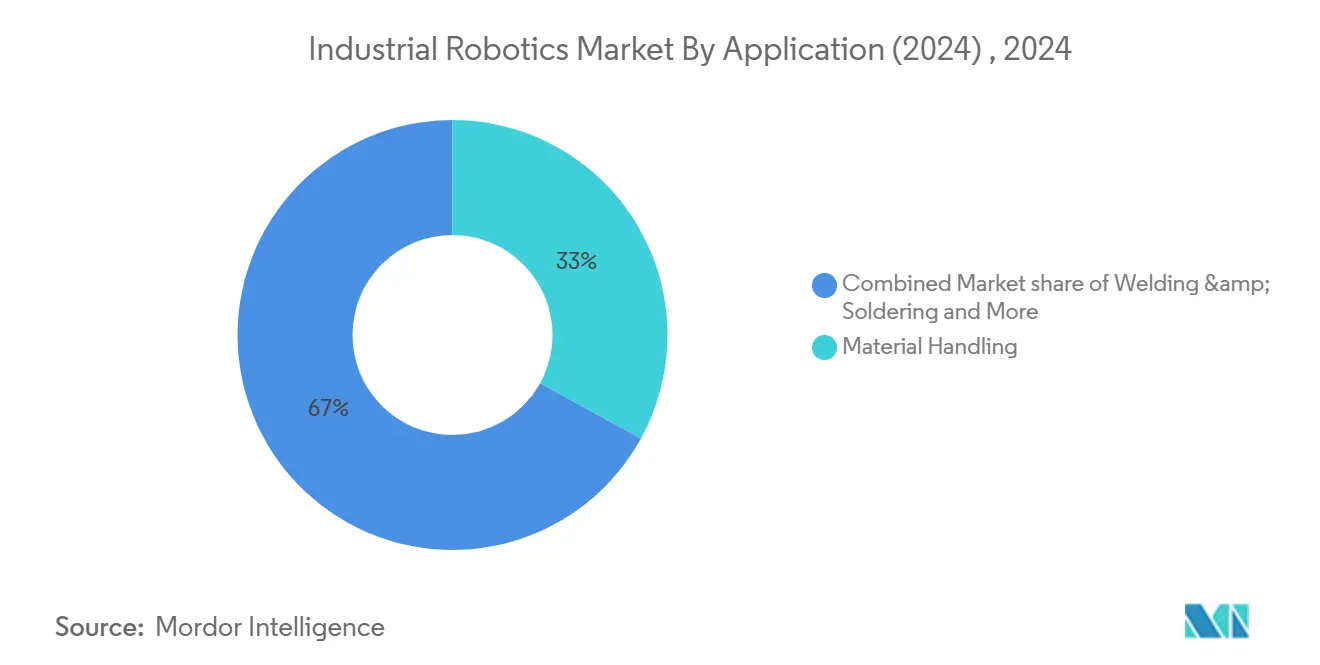
Note: Segment shares of all individual segments available upon report purchase
By End-User Industry: Food & Beverage Automation Accelerates
Automotive manufacturers accounted for 25% of industrial robotics market share in 2024, yet electrification introduces fresh complexity: battery modules require dry-room assembly and multiphase quality checks, altering cell specifications and tooling. OEMs respond by adding high-payload robots capable of simultaneous sealant dispensing and precision torque tightening. Food & beverage processors, in contrast, will log the fastest 12.4% CAGR through 2030. Labor shortages during pandemic‐era lockdowns revealed the vulnerability of manual deboning and packaging lines, prompting owners to install wash-down rated robots that meet stringent hygiene codes [3]roboticstomorrow.com .
Electronics assemblers remain heavy adopters as board densities rise and component tolerances tighten. Pharmaceutical cleanrooms embrace delta robots for vial handling, guaranteeing sterility while reducing operator exposure to potent compounds. Cross-industry technology diffusion accelerates because successful deployments in food provide blueprints for cosmetics, nutraceuticals, and specialty chemicals, widening the total addressable base of the industrial robotics market.
Geography Analysis
Asia held 70% revenue share of the industrial robotics market in 2024, underpinned by China’s 276,288 installations that equaled 51% of the global total hai-production. Subsidies, domestic component ecosystems, and rising wage levels combine to maintain the momentum. Japan leverages deep supplier networks and Industry 4.0 roadmaps, sustaining a robot density of 390 units per 10,000 workers. South Korea tops density charts above 1,000 units, reflecting aggressive smart-factory roll-outs championed by chaebol conglomerates.
South America represents the fastest-growing bloc with an 11.5% CAGR forecast as Brazilian meat processors and vehicle assemblers introduce robots to rein in labor cost volatility and improve export compliance. Mexico’s proximity to US consumer markets attracts EV component makers that capitalize on reshoring incentives. Argentina adopts agricultural packing robots to elevate throughput and reduce post-harvest losses, establishing proof points for other segments within the industrial robotics market.
North America and Europe are mature yet far from saturated. The United States deploys 295 robots per 10,000 workers, placing it tenth globally, but reshoring legislation and Section 179 incentives stimulate sustained double-digit unit growth. Germany’s 429-unit density rides on automotive clusters and Mittelstand exporters, while EU carbon-neutrality targets open niches for energy-efficient robot models. Middle East and African manufacturers remain early adopters, focusing on petrochemical packaging lines and increasingly on solar-panel fabrication, indicating long-term upside for the industrial robotics market once logistics infrastructure matures.
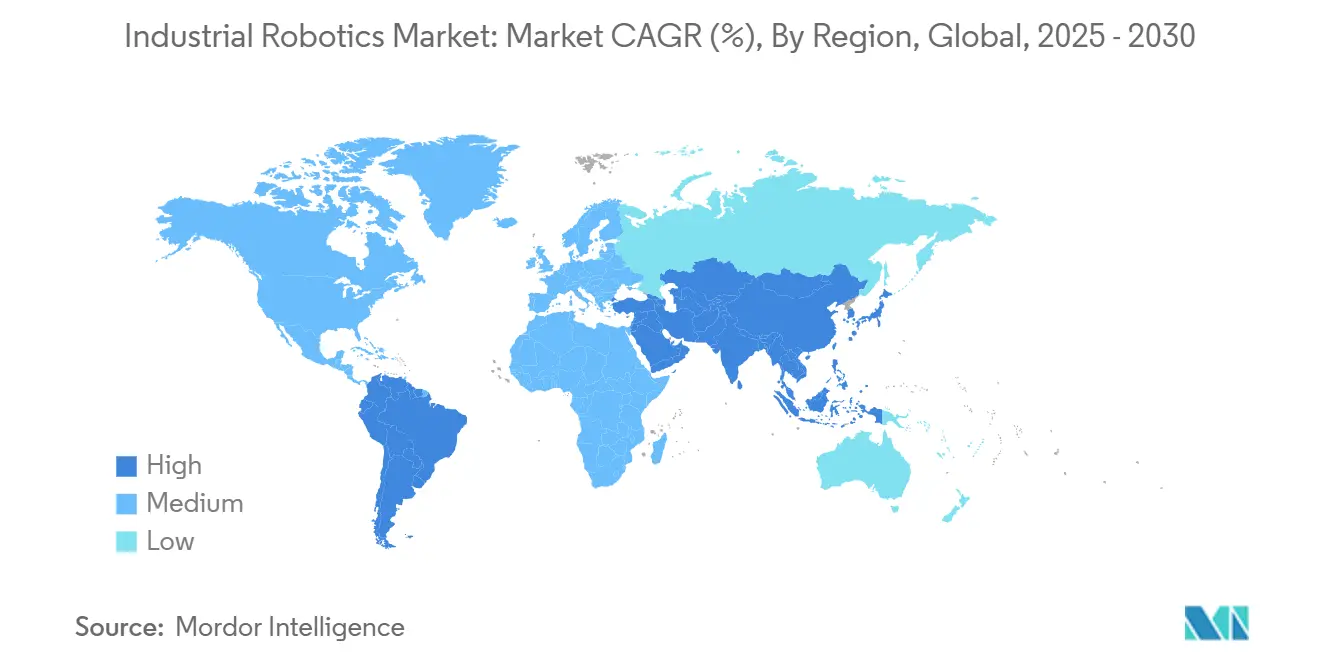
Competitive Landscape
Market concentration is moderate: ABB, FANUC, Yaskawa, and KUKA together control roughly 75% of shipments, leveraging scale to secure semiconductor allocations and sustain global service footprints. Their strategies emphasize vertical integration—FANUC, for example, designs its own servo motors—ensuring supply reliability and performance consistency. ABB’s decision to spin off its robotics division seeks to unlock shareholder value and sharpen focus on electrification while endowing the unit with currency for targeted acquisitions.
Challengers anchor differentiation in software. Universal Robots extends its ecosystem with plug-and-play peripherals, while cloud-native startups deliver robot-agnostic fleet managers that shift value from hardware to recurring analytics revenue. NVIDIA positions itself as an enabler, supplying AI toolchains that robot OEMs integrate to accelerate perception-driven autonomy, effectively commoditizing basic motion control while raising the bar on computational capability. Patent races in grasping and 3D vision intensify; OSARO’s depth-estimation breakthrough exemplifies how intellectual property shields niche profitability in the industrial robotics.
Partnership models are evolving. Symbotic’s acquisition of Walmart’s robotics arm embeds an end-user into its supply-chain automation platform, ensuring volume commitments and real-world test environments. 1X’s purchase of Kind Humanoid signals bets on next-generation form factors that extend robots from fixed cells to agile, human-scale roles. Established players answer with portfolio expansions into mobile manipulation, ensuring they stay relevant as factory layouts migrate to modular, flow-based production.
Industrial Robotics Industry Leaders
-
FANUC
-
ABB
-
Yaskawa
-
KUKA
-
Mitsubishi Electric
- *Disclaimer: Major Players sorted in no particular order
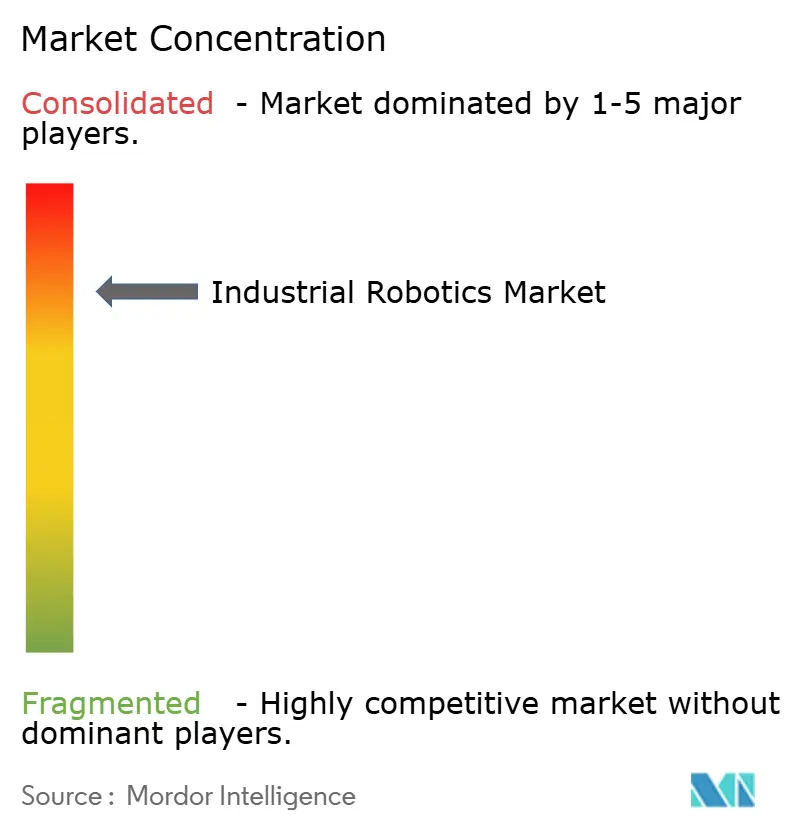
Recent Industry Developments
- April 2025: ABB announced plans to spin off its robotics division following strong Q1 earnings, aiming to sharpen strategic focus and access dedicated capital for growth
- February 2025: OSARO secured a patent for AI-powered robotic depth estimation, lowering hardware costs while boosting SKU flexibility in fulfillment centers
- January 2025: Symbotic acquired Walmart’s advanced systems and robotics business and signed long-term commercial agreements, locking in demand for its warehouse automation portfolio
- January 2025: 1X purchased Kind Humanoid to speed up humanoid robot development for industrial use, positioning itself for tasks requiring human-level reach and navigation
Global Industrial Robotics Market Report Scope
An industrial robot is a robot system used for manufacturing. Industrial robots are automated, programmable, and capable of movement on three or more axis. Industrial robots are used in multiple industries and applications. The elimination of labor-intensive activities is driving the Industrial robotics market.
The industrial robotics market is segmented by type of robot (articulated robots, linear robots, cylindrical robots, parallel robots, SCARA Robots), end-user industry (automotive, chemical, and manufacturing, construction, electrical and electronics, food and beverage, machinery and metal, pharmaceutical), and Geography Europe (United Kingdom, Germany, France, rest of Europe), Asia Pacific (Japan, China, India, South Korea, and Rest of Asia Pacific), Latin America, Middle East and Africa. The market sizes and forecasts are provided in terms of value (USD) for all the above segments.
By Robot Type | Articulated Robots | |
SCARA Robots | ||
Cartesian/Gantry Robots | ||
Parallel/Delta Robots | ||
Cylindrical Robots | ||
Collaborative Robots (Cobots) | ||
By Payload Capacity | ≤15 kg | |
16–225 kg | ||
226–500 kg | ||
>500 kg | ||
By Application | Material Handling & Packaging | |
Welding & Soldering | ||
Assembly & Dispensing | ||
Machine Tending & CNC | ||
Painting & Coating | ||
Quality Inspection | ||
By End-user Industry | Automotive | |
Electrical & Electronics | ||
Food & Beverage | ||
Machinery & Metal | ||
Pharmaceuticals & Healthcare | ||
Construction Materials | ||
Others (Rubber, Optics) | ||
By Geography | North America | United States |
Canada | ||
South America | Brazil | |
Argentina | ||
Europe | Germany | |
United Kingdom | ||
France | ||
Italy | ||
Russia | ||
Asia | China | |
Japan | ||
South Korea | ||
India | ||
Middle East and Africa | GCC | |
South Africa |
Articulated Robots |
SCARA Robots |
Cartesian/Gantry Robots |
Parallel/Delta Robots |
Cylindrical Robots |
Collaborative Robots (Cobots) |
≤15 kg |
16–225 kg |
226–500 kg |
>500 kg |
Material Handling & Packaging |
Welding & Soldering |
Assembly & Dispensing |
Machine Tending & CNC |
Painting & Coating |
Quality Inspection |
Automotive |
Electrical & Electronics |
Food & Beverage |
Machinery & Metal |
Pharmaceuticals & Healthcare |
Construction Materials |
Others (Rubber, Optics) |
North America | United States |
Canada | |
South America | Brazil |
Argentina | |
Europe | Germany |
United Kingdom | |
France | |
Italy | |
Russia | |
Asia | China |
Japan | |
South Korea | |
India | |
Middle East and Africa | GCC |
South Africa |
Key Questions Answered in the Report
How big is the Industrial Robotics Market?
The Industrial Robotics Market size is expected to reach USD 48.30 billion in 2025 and grow at a CAGR of 13.40% to reach USD 90.57 billion by 2030.
What is the current Industrial Robotics Market size?
In 2025, the Industrial Robotics Market size is expected to reach USD 48.30 billion.
What is the current size of the industrial robotics market?
The industrial robotics market is valued at USD 48.3 billion in 2025 and is on course to reach USD 90.6 billion by 2030.
Which region leads global robot installations?
Asia commands 70% of revenue, with China alone accounting for 51% of global robot deployments in 2024 hai-production.
Why are collaborative robots growing faster than traditional robots?
Built-in safety features eliminate cages, enabling flexible deployment in space-constrained lines and helping SMEs navigate labor shortages, which drives a 14.0% CAGR through 2030
How do government incentives influence robot adoption?
Subsidies and tax credits such as China’s 14th Five-Year Plan and US Section 179 accelerate payback periods, making automation financially viable even during economic uncertainty
Page last updated on: