Europe Prefabricated Buildings Market Analysis
The Europe Prefabricated Buildings Market size is estimated at USD 61.00 billion in 2025, and is expected to reach USD 79.39 billion by 2030, at a CAGR of 5.41% during the forecast period (2025-2030).
The European prefabricated buildings industry is experiencing a significant transformation driven by sustainability initiatives and technological innovation. Leading construction companies are increasingly adopting green building practices, as evidenced by Hochtief's achievement of having 101 buildings with green building certification across the European Union by 2021. The industry is witnessing a surge in the adoption of additive manufacturing technologies and digital design tools, enabling more precise and efficient construction processes. Companies are investing heavily in research and development to create innovative building solutions that minimize environmental impact while maximizing construction efficiency and quality.
The market is witnessing a notable shift towards sustainable building materials, particularly in the Nordic regions. Sweden leads this transition with approximately 84% of detached houses utilizing prefabricated timber elements, setting a benchmark for sustainable construction practices across Europe. The DACH region (Germany, Austria, and Switzerland) has emerged as a significant hub for Cross-Laminated Timber (CLT) production, manufacturing over 750,000 m³ annually, demonstrating the growing preference for eco-friendly building materials. This trend is reinforced by stringent environmental regulations and increasing consumer demand for sustainable housing solutions.
Industry consolidation and strategic partnerships are reshaping the competitive landscape. Major players are forming alliances to enhance their technological capabilities and expand their market presence. The integration of Building Information Modeling (BIM) and other digital technologies is revolutionizing project planning and execution, leading to improved efficiency and reduced construction timelines. These technological advancements are particularly evident in markets like Germany and the United Kingdom, where an estimated 70,100 units are expected to be sold across six Northern European countries, with German demand particularly strong for turnkey solutions.
The sector is experiencing a paradigm shift in construction methodologies with the introduction of energy-absorbing materials and micro dwellings. Advanced manufacturing techniques are enabling the production of more sophisticated modular buildings components with enhanced thermal and acoustic properties. The industry is also witnessing increased investment in research and development of new materials and construction techniques that promise to further improve building performance and sustainability. This evolution is supported by growing collaboration between academic institutions, research centers, and industry players to develop innovative solutions for the next generation of prefabricated buildings.
Europe Prefabricated Buildings Market Trends
Growing Demand for Sustainable Construction
The increasing focus on environmental sustainability has become a major driver for the European prefabricated buildings market, particularly evident in the widespread adoption of timber-based construction methods. Cross-laminated timber (CLT) has emerged as a preferred sustainable building material, with production facilities across the DACH region (Germany, Austria, and Switzerland), the Czech Republic, and Italy demonstrating significant technological advancement in sustainable prefabrication methods. The environmental benefits of prefabricated buildings extend beyond the building phase, as these structures serve as long-term carbon storage solutions while offering superior thermal insulation properties.
The sustainability advantage of prefabricated construction is further enhanced by the controlled factory environment, which significantly reduces material waste compared to traditional on-site construction methods. Modern prefabrication facilities are increasingly incorporating renewable energy systems and optimized production processes, minimizing the carbon footprint of manufacturing operations. The ability to precisely calculate material requirements and optimize resource usage in prefabricated construction has made it particularly attractive for developers and contractors committed to meeting stringent environmental standards and achieving green building certifications.
Government Support and Regulatory Framework
Government initiatives and supportive regulatory frameworks across Europe have emerged as crucial drivers for the prefabricated building market. The implementation of specific quotas and requirements for sustainable building materials, particularly in public housing projects, has created a strong foundation for market growth. For instance, the city of Bordeaux's commitment to developing 270,000 square feet of wooden spaces annually for the next 15 years demonstrates how local government initiatives are actively shaping the market landscape and driving innovation in modular construction buildings market methods.
The regulatory environment has also evolved to accommodate and encourage prefabricated construction methods, with many European countries introducing streamlined approval processes and building codes specifically adapted for prefabricated structures. These regulatory adaptations, combined with government-backed research and development initiatives, have fostered innovation in prefabrication technologies and materials. The establishment of standardized quality control measures and certification systems for prefabricated components has further enhanced market confidence and adoption rates across both public and private sector projects.
Technological Advancements in Manufacturing
The integration of advanced manufacturing technologies has revolutionized the prefab industry, enabling higher precision, greater customization capabilities, and improved quality control. Modern manufacturing facilities are increasingly utilizing automation and digital design tools, allowing for the production of complex architectural elements with unprecedented accuracy. The adoption of Building Information Modeling (BIM) technology has particularly enhanced the ability to coordinate between design, manufacturing, and assembly phases, significantly reducing errors and improving project efficiency.
The development of new composite materials and innovative joining techniques has expanded the possibilities for modular buildings, enabling the creation of larger and more complex structures. Advanced production lines now incorporate quality control systems that ensure consistent product quality while maintaining high production rates. These technological improvements have not only enhanced the structural integrity and durability of modular buildings but have also expanded their architectural possibilities, making them increasingly attractive for both residential and commercial applications.
Segment Analysis: Material Type
Concrete Segment in Europe Prefabricated Buildings Market
The concrete segment continues to dominate the European prefabricated buildings market, commanding approximately 42% of the total market share in 2024. This significant market position is attributed to concrete's versatility and widespread application in both residential and commercial construction projects. The segment's strength lies in its ability to provide high-quality precast products, including hollow core slabs, panels of various sizes and shapes, prestressed beams, columns, stairs, landings, and foundations. The adoption of 3D printing construction techniques in Europe has further enhanced the segment's dominance, particularly in sustainable construction projects. Major precast companies maintain dedicated carpentry facilities where skilled workers create specialized forms for various precast products, while architectural concrete is often custom-cast for specific projects to meet unique design requirements.
Timber Segment in Europe Prefabricated Buildings Market
The timber segment is emerging as the most dynamic sector in the European prefabricated buildings market, with a projected growth rate of approximately 7% during the forecast period 2024-2029. This remarkable growth is driven by increasing environmental awareness and the push for sustainable construction materials. Timber's natural properties as a renewable resource and its excellent thermal insulation capabilities make it particularly attractive for eco-conscious developers and homeowners. The segment's growth is further supported by technological advancements in wood treatment and manufacturing processes, making timber structures more durable and versatile than ever before. European governments' initiatives promoting sustainable construction practices and reducing carbon footprints in the building sector have created a favorable environment for timber-based prefabricated solutions.
Remaining Segments in Material Type
The metal, glass, and other material segments each play crucial roles in the European prefabricated buildings market. The metal segment maintains its position as a reliable choice for industrial and commercial applications, offering superior strength and durability for large-scale projects. Glass components are increasingly integrated into modern architectural designs, providing enhanced aesthetic appeal and energy efficiency through advanced thermal and optical capabilities. Other materials, including innovative composites and hybrid solutions, continue to emerge as alternatives, offering unique combinations of properties that cater to specific construction requirements. These segments collectively contribute to the market's diversity, providing architects and developers with a comprehensive range of options to meet various project specifications and environmental considerations.
Segment Analysis: By Application
Residential Segment in European Prefabricated Buildings Market
The residential segment continues to dominate the European prefabricated building market, holding approximately 40% market share in 2024. This significant market position is driven by increasing demand for affordable housing solutions and rapid urbanization across European countries. The segment's growth is further supported by government initiatives promoting sustainable construction methods and energy-efficient housing developments. Prefabricated residential construction has gained particular traction in countries like Sweden, Germany, and the Netherlands, where modern manufacturing techniques and advanced design capabilities have elevated the quality and appeal of modular buildings. The segment benefits from shorter construction timelines, reduced labor costs, and improved quality control through factory-based manufacturing processes. Additionally, the rising focus on sustainable building practices and energy efficiency requirements has made prefabricated residential solutions increasingly attractive to both developers and homebuyers.
Commercial Segment in European Prefabricated Buildings Market
The commercial segment is emerging as the fastest-growing segment in the European prefab industry, with a projected growth rate of approximately 7% during 2024-2029. This accelerated growth is primarily driven by the increasing adoption of modular building methods in office buildings, retail spaces, and hospitality sectors. The segment's expansion is supported by advantages such as faster project completion times, reduced site disruption, and consistent quality standards. Commercial developers are increasingly recognizing the benefits of prefabrication in meeting tight project deadlines and managing construction costs effectively. The trend towards sustainable commercial buildings and the need for flexible, adaptable spaces has further accelerated the adoption of prefabricated solutions in the commercial sector. Additionally, technological advancements in Building Information Modeling (BIM) and automated manufacturing processes have enhanced the precision and customization capabilities of commercial prefab structures.
Remaining Segments in Application Segmentation
Other applications in the prefabricated buildings market, including industrial, institutional, and infrastructure projects, play a vital role in shaping the overall market landscape. These segments cater to diverse needs such as manufacturing facilities, educational institutions, healthcare facilities, and transportation infrastructure. The industrial sector particularly benefits from the standardized and rapid deployment capabilities of prefabricated solutions, while institutional projects leverage the cost-effectiveness and quality consistency of modular construction. Infrastructure applications have seen increased adoption in projects requiring quick deployment and minimal site disruption. These segments collectively contribute to the market's diversification and demonstrate the versatility of prefabricated construction methods across different application areas.
Europe Prefabricated Buildings Market Geography Segment Analysis
Prefabricated Buildings Market in Germany
Germany dominates the European prefabricated buildings landscape, holding approximately 23% of the market share in 2024. The country's leadership in this sector is driven by its strong emphasis on sustainable building practices and technological innovation in construction methods. The German prefabricated building market has shown remarkable resilience, with every fifth building permit for single or two-family houses involving a prefabricated structure. Climate protection and environmental consciousness are key drivers, as many builders are increasingly confident in using wood as a renewable raw material that absorbs CO2 during growth. The country's success in prefabricated construction is particularly evident in the south and southwest regions, where the building technique has been especially successful for decades. German manufacturers of individually planned and mostly turnkey wooden prefabricated buildings have developed sophisticated offerings that meet the growing demand for high-quality, energy-efficient homes. The market's strength is further reinforced by comprehensive quality control systems, efficient production processes, and a well-established network of suppliers and manufacturers.
Prefabricated Buildings Market in Ukraine
Ukraine's prefabricated buildings market is projected to grow at approximately 7% CAGR from 2024 to 2029, emerging as the fastest-growing market in Europe. The country's construction sector is undergoing a significant transformation with the adoption of modern modular buildings technologies. Ukrainian architecture firms are pioneering innovative modular village designs that could house thousands of people, particularly focusing on rapid deployment and cost-effectiveness. The country's prefabricated construction industry is witnessing increased investment in manufacturing capabilities and technological advancement. Local manufacturers are developing expertise in various prefabrication techniques, from modular units to panelized systems. The market is particularly seeing growth in turnkey modular construction, which has become one of the most prominent trends in Ukrainian housing. The industry is also benefiting from an increased focus on sustainable building practices and energy-efficient designs, with manufacturers incorporating modern insulation techniques and eco-friendly materials in their prefabricated solutions. The sector's growth is further supported by government initiatives promoting modern construction methods and urban development projects.
Prefabricated Buildings Market in United Kingdom
The United Kingdom's prefabricated buildings market demonstrates strong potential, driven by the government's commitment to addressing the housing crisis through modern methods of construction. The country has established several partnerships to accelerate the adoption of prefabricated construction solutions, particularly in the affordable housing sector. The British market is witnessing increased third-party investment from major financial institutions and housing developers, supporting the growth of offsite manufacturing capabilities. The industry's focus has shifted towards volumetric and closed panel systems, with key players investing in advanced manufacturing facilities. The construction sector's adoption of Modern Methods of Construction (MMC) is transforming the traditional building landscape, with prefabrication emerging as a solution to challenges such as labor shortages and the need for faster construction timelines. The market is particularly seeing growth in the residential sector, where prefabricated buildings solutions are helping meet the government's ambitious housing targets while maintaining high quality and sustainability standards.
Prefabricated Buildings Market in France
France's prefabricated buildings market is characterized by its strong focus on concrete and wood-based prefabricated products, with the country being a pioneer in heavy prefabrication systems. The French market is experiencing a gradual shift towards industrialized construction methods, although adoption rates lag behind some European counterparts. The industry is seeing increased interest in multi-story prefabricated buildings, particularly in urban areas where construction speed and efficiency are crucial. French manufacturers are investing in research and development to improve prefabrication techniques and materials, with a particular focus on sustainable building solutions. The market is also witnessing growing demand for prefabricated wooden structures, especially in buildings ranging from 7 to 16 stories. Local authorities, such as the city of Bordeaux, are actively promoting timber construction, demonstrating the country's commitment to sustainable building practices. The industry is supported by a strong network of manufacturers, designers, and construction companies specializing in prefabricated solutions.
Prefabricated Buildings Market in Other Countries
The European modular construction market across other European countries showcases diverse development patterns and adoption rates. Countries like Sweden, Belgium, Finland, Poland, Italy, Spain, and the Netherlands each demonstrate unique approaches to prefabricated construction, influenced by their local building traditions, climate conditions, and regulatory frameworks. Nordic countries generally show higher adoption rates of timber-based prefabrication, while southern European nations tend to favor concrete-based systems. Eastern European countries are rapidly modernizing their prefabrication capabilities, investing in new technologies and manufacturing facilities. The market dynamics vary significantly across regions, with some countries focusing on residential applications while others emphasize commercial and industrial prefabrication. These markets are characterized by increasing collaboration between international players, knowledge sharing, and technological transfer, contributing to the overall advancement of the European prefab homes sector.
Europe Prefabricated Buildings Industry Overview
Top Companies in Europe Prefabricated Buildings Market
The European prefabricated buildings market features prominent players like ALHO Systembau, Kleusberg GmbH, Astron Buildings, Moelven Byggmodul AB, and Berkeley Group, among others, driving innovation and market growth. Companies are increasingly focusing on sustainable construction methods and energy-efficient building solutions, with many manufacturers investing in advanced manufacturing capabilities and digital technologies. The industry is witnessing a shift towards turnkey solutions and volumetric construction methods, particularly in residential and commercial segments. Strategic partnerships and collaborations are becoming more common, especially for developing innovative prefabrication technologies and expanding market reach. Companies are also emphasizing research and development to improve design capabilities, enhance manufacturing precision, and develop new materials that align with environmental sustainability goals.
Fragmented Market with Growing Consolidation Trends
The European prefab industry exhibits a highly fragmented structure with numerous regional and local players competing alongside established multinational corporations. The market is characterized by intense competition among existing players, particularly in regions like Sweden, Germany, and the United Kingdom, where companies vie for market share through product differentiation and technological advancement. The larger market participants are increasingly engaging in mergers, acquisitions, and joint ventures, both among themselves and with smaller companies, to acquire new technologies, expand product portfolios, and increase market presence.
The competitive dynamics are further shaped by the presence of both specialized prefabricated buildings manufacturers and diversified construction conglomerates. Local players often maintain strong positions in their respective regions due to their understanding of local building regulations and customer preferences. The industry is witnessing a gradual trend toward consolidation as larger companies seek to strengthen their market position through strategic acquisitions and partnerships, particularly in emerging segments like the modular construction buildings market and sustainable building solutions.
Innovation and Sustainability Drive Future Success
Success in the modular buildings market increasingly depends on companies' ability to innovate while maintaining cost competitiveness and meeting sustainability requirements. Market players need to invest in advanced manufacturing technologies, develop standardized yet customizable solutions, and build strong relationships with suppliers and contractors. Companies must also focus on developing efficient supply chain networks and logistics capabilities to ensure timely delivery and installation of prefabricated components. The adoption of digital technologies like Building Information Modeling (BIM) and automated manufacturing processes is becoming crucial for maintaining a competitive advantage.
Future market leadership will require companies to address growing environmental concerns and evolving regulatory requirements while meeting customer demands for faster construction times and cost-effective solutions. Players must develop strategies to mitigate the impact of raw material price fluctuations and labor shortages through increased automation and efficient resource management. Success will also depend on companies' ability to build strong brand recognition, establish effective distribution networks, and provide comprehensive after-sales support. The market presents significant opportunities for both incumbents and new entrants who can effectively combine technological innovation with sustainable practices and customer-centric approaches.
Europe Prefabricated Buildings Market Leaders
-
Laing O-Rourke
-
Bouygues Construction, VINCI
-
Skanska AB
-
Kleusberg GmbH & Co. (KG)
-
Deutsche Fertighaus Holding
- *Disclaimer: Major Players sorted in no particular order
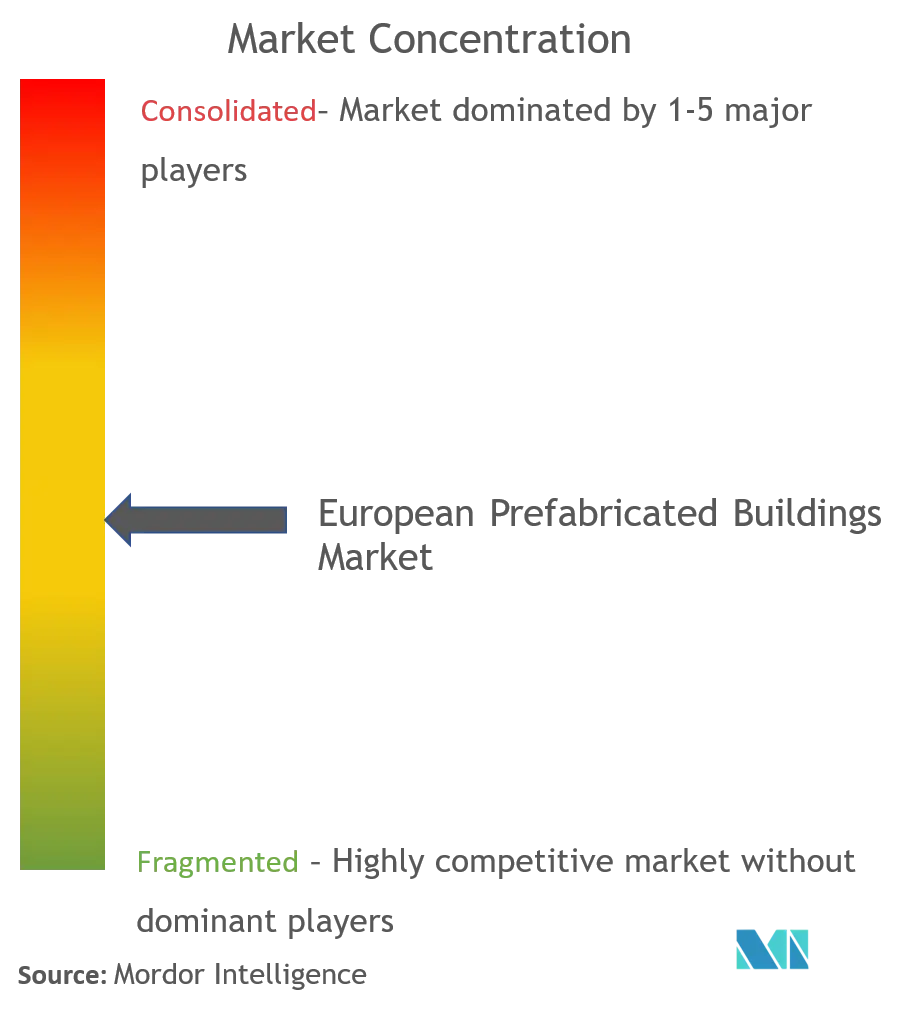
Europe Prefabricated Buildings Market News
In January 2022, the University of Oxford appointed its long-standing partner, Laing O'Rourke to deliver the Stephen A. Schwarzman Centre for the Humanities. The award could signify one of the university's largest single-building projects and would see Laing O'Rourke deliver its 12th project for a client it has worked with for two decades. The new building is estimated to bring nine faculties, institutes, and seven libraries and collections into one home, with sustainable, flexible, accessible spaces for graduate postgrad and post-doc learning, research, and experimentation. Performance and public engagement spaces form a key element of the project, with a 500-seat concert hall designed with global-leading acoustic capability, a 250-seat theater, and a film screening area. It is estimated to form the centerpiece of the Radcliffe Observatory Quarter (ROQ) and is estimated to be surrounded by an inviting landscaped space, connecting the wider community throughout.
In August 2021, Uliving, a brand of Linkcity UK (the property development subsidiary of Bouygues UK) specializing in student accommodation, won a 50-year concession contract to construct and provide facilities management services for a 1,262-bedroom project at the University of Essex in consortium with Equitix, its equity partner. The contract is worth GBP 168 million (EUR 194 million).
Europe Prefabricated Buildings Industry Segmentation
The European prefabricated buildings market covers growing trends and projects like commercial, residential, and industrial construction. The report also covers the industry and materials used, like concrete, timber, glass, metal, and other types. The market scope has been extended to provide insights at the regional level by segmenting across geography. Along with the report's scope, it also analyzes the key players and the competitive landscape in the market. The impact of COVID-19 has also been incorporated and considered during the study.
By Application | Residential |
Commercial | |
Other Applications (Industrial, Institutional, and Infrastructure) | |
By Geography | Belgium |
Finland | |
France | |
Germany | |
Italy | |
Rest of Europe |
Residential |
Commercial |
Other Applications (Industrial, Institutional, and Infrastructure) |
Belgium |
Finland |
France |
Germany |
Italy |
Rest of Europe |
Europe Prefabricated Buildings Market Research FAQs
How big is the Europe Prefabricated Buildings Market?
The Europe Prefabricated Buildings Market size is expected to reach USD 61.00 billion in 2025 and grow at a CAGR of 5.41% to reach USD 79.39 billion by 2030.
What is the current Europe Prefabricated Buildings Market size?
In 2025, the Europe Prefabricated Buildings Market size is expected to reach USD 61.00 billion.
Who are the key players in Europe Prefabricated Buildings Market?
Laing O-Rourke, Bouygues Construction, VINCI, Skanska AB, Kleusberg GmbH & Co. (KG) and Deutsche Fertighaus Holding are the major companies operating in the Europe Prefabricated Buildings Market.
Which is the fastest growing region in Europe Prefabricated Buildings Market?
North America is estimated to grow at the highest CAGR over the forecast period (2025-2030).
Which region has the biggest share in Europe Prefabricated Buildings Market?
In 2025, the North America accounts for the largest market share in Europe Prefabricated Buildings Market.
What years does this Europe Prefabricated Buildings Market cover, and what was the market size in 2024?
In 2024, the Europe Prefabricated Buildings Market size was estimated at USD 57.70 billion. The report covers the Europe Prefabricated Buildings Market historical market size for years: 2020, 2021, 2022, 2023 and 2024. The report also forecasts the Europe Prefabricated Buildings Market size for years: 2025, 2026, 2027, 2028, 2029 and 2030.