Rubber Conveyor Belt Market Size and Share
Rubber Conveyor Belt Market Analysis by Mordor Intelligence
The rubber conveyor belt market size is estimated at USD4.5 billion in 2025 and is forecast to reach USD5.55 billion by 2030, advancing at a 4.28% CAGR. Demand is expanding because operators in mining, logistics, recycling, and process industries are modernizing bulk-material‐handling systems and specifying heat-, fire-, and oil-resistant belts that last longer and run at higher speeds. Three structural forces are at work: stricter safety rules, accelerating automation, and rapid growth in energy-transition minerals. End-users now treat premium belts as productivity levers rather than consumables, a perception that is lengthening service contracts and smoothing revenue for suppliers. Concurrently, lingering raw-material volatility—especially in butadiene and carbon black—has pushed manufacturers to secure multi-year supply agreements and trial bio-based fillers, an early sign that cost risk is being actively managed.
Key Report Takeaways
- Heat-resistant belts held 29% of the rubber conveyor belt market share in 2024, and fire-resistant variants are on course for a 5.9% CAGR through 2030.
- Medium-weight belts contributed 45% of the rubber conveyor belt market size in 2024; heavy-weight belts are projected to expand at a 5.5% CAGR as mines lengthen overland routes.
- Textile carcass reinforcement commanded 52% market share in 2024, while steel-cord belts are forecast to post a 6.3% CAGR through 2030.
- Logistics and warehousing retained a 22% revenue share in 2024; mining and quarrying represent the fastest-growing end-user segment with a 6.1% CAGR to 2030.
- Asia led with 34% of 2024 revenue, yet Latin America is expected to be the quickest-growing region at a 6.3% CAGR, buoyed by large copper and iron ore investments.
Global Rubber Conveyor Belt Market Trends and Insights
Drivers Impact Analysis
Drivers | (~) % Impact on CAGR | Geographic Relevance | Peak Impact |
---|---|---|---|
Surge in High-Temperature Battery-Metals Processing in Asia Boosting Heat-Resistant Belts | +1.2% | Asia, with spillover to North America | Medium term (~ 3-4 yrs) |
Automated Micro-Fulfillment Warehouses in North America Driving Lightweight Belt Demand | +0.8% | North America, Europe | Short term (≤ 2 yrs) |
"Pit-to-Plant" Conveyor Retrofits in South American Copper Mines Elevating Replacement Cycle | +1.0% | Latin America, particularly Chile and Brazil | Medium term (~ 3-4 yrs) |
EU 2023/1115 Mandating Flame-Retardant Belts in Recycling Plants | +0.7% | European Union | Short term (≤ 2 yrs) |
Expansion of Solar-PV Manufacturing Clusters in India Requiring Oil-Resistant Belts | +0.6% | Asia, particularly India | Medium term (~ 3-4 yrs) |
IoT-Enabled Condition-Monitoring Unlocking Pay-Per-Ton Service Contracts | +0.9% | Global, with early adoption in North America and Europe | Long term (≥ 5 yrs) |
Source: Mordor Intelligence
Surge in High-Temperature Battery-Metals Processing in Asia Boosting Heat-Resistant Belts
Cathode and precursor plants across China, Korea, and Indonesia increasingly operate reactors above 200°C, driving rapid uptake of graphene-nanotube-enhanced belts that combine thermal stability with static dissipation. These belts allow processors to raise throughput without adding cooling capacity, and the resulting productivity gain is convincing vertically integrated miners to lock in multi-year supply agreements. A fresh inference is that early certification of high-heat compounds now serves as a proxy for project schedule reliability.
Automated Micro-Fulfilment Warehouses in North America Driving Lightweight Belt Demand
Urban micro-fulfilment centers occupy footprints under 10,000 sq ft and rely on compact lightweight belts that twist, climb, and stop within millimetres. Operators switching from multi-ply to single-ply constructions report energy savings exceeding 20%, highlighting how belt mass influences total operating cost. Because labour shortages persist, gains in picking accuracy linked to low-stretch fabrics directly elevate revenue per square foot, placing materials science at the heart of warehouse economics.
“Pit-to-Plant” Conveyor Retrofits in South American Copper Mines Elevating Replacement Cycle
Chile and Peru are converting haul-trucks to continuous pit-to-plant belts that move more than 10 000 t/h while trimming diesel use by two-thirds. Higher dynamic tensions accelerate belt wear, so replacement cycles shorten even as tonnage rises, ensuring steady aftermarket demand. Mines therefore prioritise vendors with fast splice-service teams, signalling that logistics support can be as decisive as tensile rating when tenders are evaluated.
EU 2023/1115 Mandating Flame-Retardant Belts in Recycling Plants
The regulation obliges European recycling facilities to use belts that self-extinguish within strict time limits, propelling orders for certified fire-resistant grades. Fenner Dunlop invested EUR 2.4 million (USD 2.81 million) in a new mixing line to produce low-halogen compounds, turning compliance expenditure into a marketing asset. Smaller fabricators lacking certification capacity are exiting, a shift that quietly consolidates market share among well-capitalised suppliers.
Restraints Impact Analysis
Restraints | (~) % Impact on CAGR | Geographic Relevance | Peak Impact |
---|---|---|---|
Volatility in Butadiene and Carbon Black Prices Compressing Margins | -0.9% | Global, with highest impact in Asia | Short term (≤ 2 yrs) |
PVC and Modular Belt Substitution in European Food Processing | -0.7% | Europe | Medium term (~ 3-4 yrs) |
Certification Lead-Times for UL/CSA Flame Tests in North America | -0.4% | North America | Short term (≤ 2 yrs) |
EU Scrutiny of Nitrosamine Exposure During Vulcanization | -0.5% | European Union | Medium term (~ 3-4 yrs) |
Source: Mordor Intelligence
Expansion of Solar-PV Manufacturing Clusters in India Requiring Oil-Resistant Belts
A planned 6 GW solar-module plant in Odisha will employ oil-resistant belts to handle plasticisers and encapsulants that degrade conventional covers. Pairing nitrile blends with abrasion-resistant carcasses prevents delamination, cutting unplanned downtime. This linkage between specialty chemistry and renewable-energy rollout underscores how national industrial policy can redirect rubber conveyor belt market size toward premium variants.
IoT-Enabled Condition-Monitoring Unlocking Pay-Per-Ton Service Contracts
Continental’s Conti+ 2.0 embeds wireless strain and vibration sensors that alert users to splice fatigue days in advance. Quarries adopting the platform have negotiated pay-per-ton service contracts that shift availability risk to the belt maker in return for higher unit pricing. Ownership of performance data thus transforms belts from one-off purchases into recurring-revenue assets, subtly changing valuation models for manufacturers.
Segment Analysis
Belt Type: Heat-Resistant Dominates While Fire-Resistant Accelerates
Heat-resistant belts held 29% of the rubber conveyor belt market share in 2024. Advances in silica-rich compounds let these belts run continuously above 200 °C, enabling kiln operators to raise furnace set-points and unlock throughput gains. Fewer thermal cracks mean shorter maintenance shutdowns, an outcome that expands effective plant availability.
Fire-resistant variants are forecast to grow at a 5.9% CAGR between 2025-2030, fuelled by underground-mine safety codes and EU recycling mandates. Belts achieving Type A or B certification under CAN/CSA-M422 command premiums, and many sites now specify only these grades, elevating barriers for non-certified competitors.
Note: Segment shares of all individual segments available upon report purchase
Belt Weight: Medium-Weight Versatility Meets Heavy-Weight Growth
Medium-weight belts provided 45% of the rubber conveyor belt market size in 2024. Polyester-nylon carcasses balance strength and flexibility, letting parcel hubs extend belt life without upgrading drives. The resulting energy savings and lower structural-steel requirements reinforce payback, especially where electricity tariffs are high.
Heavy-weight belts are projected to post a 5.5% CAGR as mines adopt longer overland conveyors. Goodyear’s extra-stiff polyester/nylon designs minimise stretch on multi-kilometre flights, keeping sag within design limits. Lower elongation allows single-flight layouts that reduce the number of transfer points, cutting dust emissions and maintenance hours.
End-User Industry: Logistics Leads While Mining Accelerates
Logistics and warehousing held 22% of the rubber conveyor belt market size in 2024. Noise-damped covers enable 24/7 operation in urban zones, and operators link quiet belts to higher worker retention.
Mining and quarrying are projected to grow at a 6.1% CAGR through 2030. Anglo American’s Quellaveco mine produced 319,000 tons of copper in its first year using high-capacity overland belts. Reduced truck kilometres lower Scope 1 emissions, and energy-efficient belts further improve decarbonisation disclosures, aligning procurement with investor climate expectations.
Note: Segment shares of all individual segments available upon report purchase
Reinforcement Material: Textile Leads While Steel Cord Advances
Textile carcasses commanded 52% market share in 2024, favoured for flexibility in systems with sharp curves. Multi-weft breaker fabrics arrest tear propagation, reducing unscheduled stoppages in parcel sortation centres and saving overtime labour.
Steel-cord belts are expected to grow at a 6.3% CAGR. Continental’s ST10 000 line supports lift heights above 500 m without intermediate drives. Fewer splices lower failure probability, and the combination of high strength and low creep allows mines to phase out costly booster drives, freeing capital for other upgrades.
Geography Analysis
Asia dominated with 34% of 2024 revenue, propelled by China’s large manufacturing base and India’s infrastructure push. Access to natural rubber feedstock from Thailand and Malaysia buffers cost shocks, giving regional producers an input advantage. Policy incentives for battery-metal refining and solar-module manufacturing channel belt demand toward heat- and oil-resistant variants, effectively concentrating growth in specialised niches.
South America is forecast to record the highest 6.3% CAGR to 2030. Major copper projects in Chile, Peru, and Brazil are replacing haul trucks with overland conveyors, driving large orders for heavy-duty steel-cord belts. Antamina’s USD 2 billion life-extension dedicates substantial capital to new conveyors, and suppliers that offer sidewall or steep-angle designs are capturing premium contracts. The region’s commitment to renewable power for mines further raises interest in low-stretch belts that cut energy draw.
North America and Europe retain significant shares, but for different reasons. North American warehouses prioritise predictive uptime and thus purchase sensor-equipped belts, while European factories focus on low-nitrosamine formulations to meet health standards. The Middle East and Africa remain nascent yet promising: rail projects and iron-ore mines require belts that withstand high heat and abrasive dust, pushing buyers toward blended synthetic-natural rubbers with UV-stable covers.
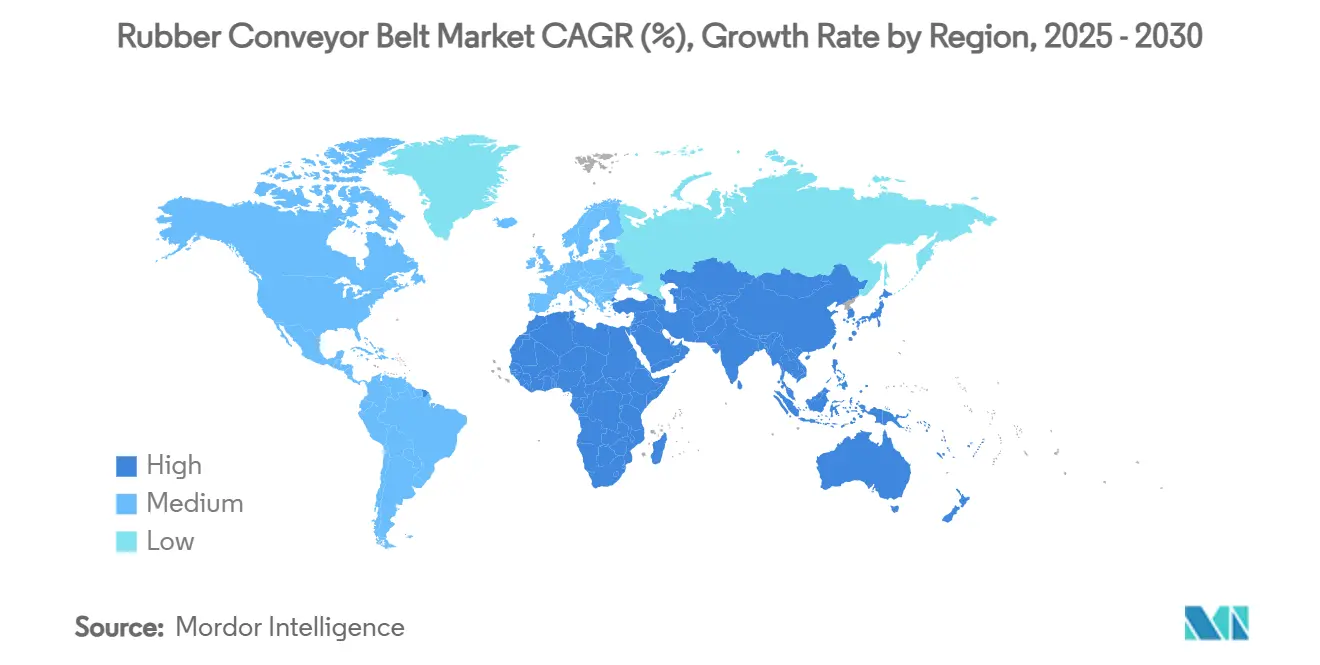
Competitive Landscape
The industry is moderately fragmented; the five largest suppliers account for under one-third of revenue. Bridgestone, Continental, and Yokohama leverage global R and D networks to commercialise high-performance belts quickly. Regional producers in China and India compete on price but are upgrading automation to narrow quality gaps, hinting that cost leadership alone may soon be insufficient.
Strategic consolidation is underway. Yokohama Rubber is negotiating to acquire Goodyear’s Off-the-Road tire business for up to USD1.5 billion, aiming to bundle tires and belts for mining clients and secure raw-material scale advantages. Such mergers promise cross-selling opportunities and could raise entry barriers for smaller rivals.
Digital capability is the emerging differentiator. Continental’s Conti+ 2.0 streams belt-health data to cloud dashboards, enabling service-level agreements that guarantee uptime. Vendors lacking comparable analytics risk commoditisation as buyers increasingly include predictive maintenance in tender criteria. Data ownership also guides replacement timing, shifting bargaining power toward digitally adept manufacturers.
Rubber Conveyor Belt Industry Leaders
-
Bridgestone Corporation
-
Continental AG (ContiTech & Phoenix)
-
Fenner Dunlop Holdings Ltd.
-
The Yokohama Rubber Co. Ltd.
-
Bando Chemical Industries Ltd.
- *Disclaimer: Major Players sorted in no particular order
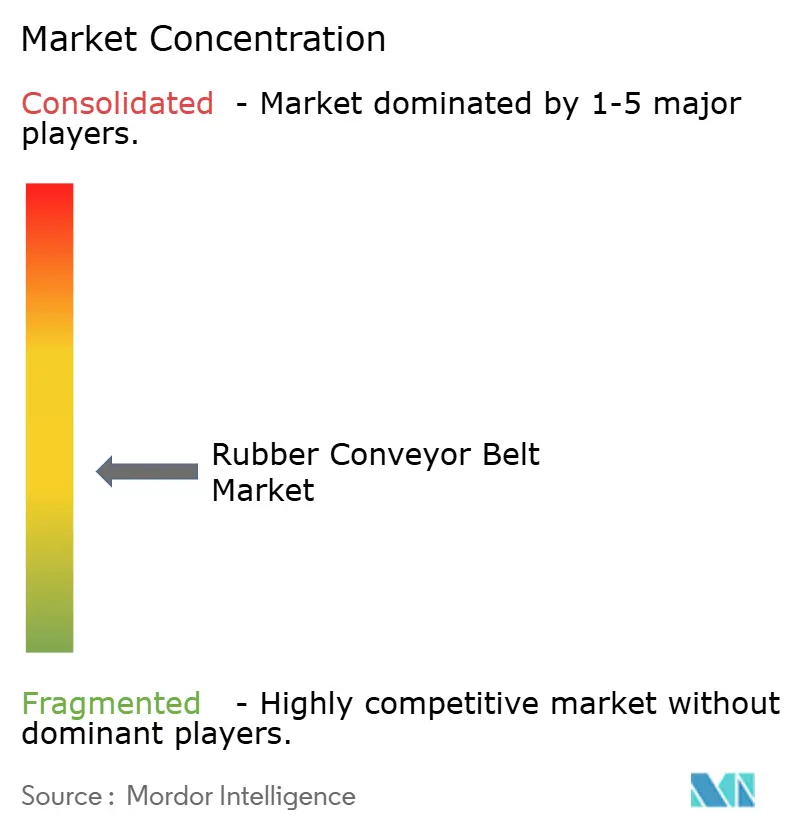
Recent Industry Developments
- May 2025: Yokohama Rubber entered advanced talks to acquire Goodyear’s Off-the-Road tire business for USD1-1.5 billion, a move that would deepen its mining portfolio and expand global service reach.
- April 2025: Continental launched Conti+ 2.0 Monitoring at MINExpo 2024, adding wireless edge devices that transmit splice-strain and idler-vibration data for predictive analytics.
- March 2025: Compañía Minera Antamina secured approval for a USD2 billion life-extension through 2036, allocating significant capital to overland conveyor upgrades.
- February 2025: Fenner Dunlop completed a €2.4 million mixing-line upgrade to meet EU 2023/1115 flame-retardant rules and ensure uninterrupted supply to European recyclers.
Global Rubber Conveyor Belt Market Report Scope
A conveyor belt is used to transport goods from one location to another. They're typically utilised for short-distance movement within a facility, as well as connecting assembly lines to final inspection and packing lines. The material to be conveyed is placed on the belt and transported horizontally or along an inclined slope to its destination. Two or more pulleys are used to rotate the belt in continuous circles in this method. Conveyor belts are widely used in a variety of sectors because to their high adaptability, light weight, and cost-effectiveness. One of the major factors driving the worldwide conveyor belt market is rising demand from the power, mining, and industrial industries.
Rubber conveyor belts can be classified as heat-resistant, oil-resistant, fire-resistant and chemical resistant. They are increasingly being utilized by various end-user industries such as Logistics, Mining, Manufacturing and Metal Processing at various stages.
By Belt Type | Heat-Resistant | ||
Oil-Resistant | |||
Fire-Resistant | |||
Chemical-Resistant | |||
General-Purpose | |||
By Belt Weight | Lightweight | ||
Medium-Weight | |||
Heavy-Weight | |||
By Reinforcement Material | Textile / Fabric Carcass | ||
Steel Cord | |||
Solid-Woven | |||
By End-user Industry | Logistics and Warehousing | ||
Mining and Quarrying | |||
Manufacturing (Discrete and Process) | |||
Metal Processing and Steel Mills | |||
Power Generation (Thermal and Biomass) | |||
Food and Beverage | |||
Construction and Aggregates | |||
By Geography | North America | United States | |
Canada | |||
Mexico | |||
South America | Brazil | ||
Argentina | |||
Rest of South America | |||
Europe | Germany | ||
United Kingdom | |||
France | |||
Italy | |||
Spain | |||
Rest of Europe | |||
Asia-Pacific | China | ||
Japan | |||
South Korea | |||
India | |||
Australia | |||
New Zealand | |||
Rest of Asia-Pacific | |||
Middle East and Africa | United Arab Emirates | ||
Saudi Arabia | |||
South Africa | |||
Rest of Middle East and Africa |
Heat-Resistant |
Oil-Resistant |
Fire-Resistant |
Chemical-Resistant |
General-Purpose |
Lightweight |
Medium-Weight |
Heavy-Weight |
Textile / Fabric Carcass |
Steel Cord |
Solid-Woven |
Logistics and Warehousing |
Mining and Quarrying |
Manufacturing (Discrete and Process) |
Metal Processing and Steel Mills |
Power Generation (Thermal and Biomass) |
Food and Beverage |
Construction and Aggregates |
North America | United States |
Canada | |
Mexico | |
South America | Brazil |
Argentina | |
Rest of South America | |
Europe | Germany |
United Kingdom | |
France | |
Italy | |
Spain | |
Rest of Europe | |
Asia-Pacific | China |
Japan | |
South Korea | |
India | |
Australia | |
New Zealand | |
Rest of Asia-Pacific | |
Middle East and Africa | United Arab Emirates |
Saudi Arabia | |
South Africa | |
Rest of Middle East and Africa |
Key Questions Answered in the Report
What is the projected growth rate for the rubber conveyor belt market during 2025-2030?
The market is expected to grow at a 4.28%CAGR, rising from USD4.5 billion in 2025 to USD5.55 billion by 2030.
Which belt type currently holds the largest rubber conveyor belt market share?
Heat-resistant belts lead the market because high-temperature industries depend on their ability to withstand continuous operation above 200 °C.
Why are steel-cord belts gaining traction in mining applications?
Steel-cord reinforcement provides high tensile strength and low elongation, enabling longer single-flight conveyors that lower energy consumption and maintenance.
How is IoT technology changing conveyor-belt maintenance strategies?
Sensor-equipped belts deliver real-time condition data that support predictive maintenance and enable suppliers to offer pay-per-ton service models.
What regulation is driving demand for flame-retardant belts in Europe?
EU 2023/1115 mandates self-extinguishing conveyor belts in recycling facilities, accelerating replacement cycles with certified fire-resistant variants.
Which region is expected to record the highest growth rate through 2030?
Latin America is projected to grow fastest at a 6.3%CAGR, spurred by large-scale mining and infrastructure investments that rely on heavy-duty conveyor systems.
Page last updated on: June 28, 2025