Physical Vapor Deposition (PVD) Coatings Market Size
Physical Vapor Deposition (PVD) Coatings Market Analysis
The Physical Vapor Deposition Coatings Market size is estimated at USD 11.13 billion in 2025, and is expected to reach USD 15.20 billion by 2030, at a CAGR of 6.43% during the forecast period (2025-2030).
The Physical Vapor Deposition Coatings industry is experiencing significant transformation driven by technological advancements and evolving manufacturing processes. The integration of Industry 4.0 technologies has revolutionized coating processes, enabling precise control and monitoring of deposition parameters. The adoption of smart manufacturing solutions has enhanced coating quality consistency while reducing material waste and operational costs. According to the German Machine Tool Builders Association, the global production value of machine tools reached USD 83.9 billion in 2021, indicating robust growth in manufacturing capabilities that utilize PVD Coating technologies.
The renewable energy sector has emerged as a significant growth avenue for PVD Coatings, particularly in wind turbine components and solar panel manufacturing. These coatings provide crucial protection against environmental factors while improving operational efficiency. In Canada alone, wind energy accounts for 3.5% of electricity generation, representing a substantial market for protective coatings in turbine components. The increasing focus on renewable energy infrastructure globally has created new opportunities for specialized Thin Film Coating applications in this sector.
The electronics manufacturing sector continues to evolve with increasing demands for miniaturization and improved performance. According to ZVEI, the German electro and digital industry turnover reached EUR 200.4 billion in 2021, demonstrating the sector's robust growth. This has led to the development of more sophisticated Thin Film Coating solutions capable of meeting the stringent requirements of modern electronic components, particularly in terms of thermal management and electrical conductivity.
The industry is witnessing a significant shift towards environmentally sustainable coating solutions and processes. Manufacturers are investing in research and development to create eco-friendly alternatives to traditional coating materials and methods. This transformation is driven by stringent environmental regulations and increasing consumer awareness about sustainable manufacturing practices. The focus has shifted to developing Functional Coating processes that minimize energy consumption and reduce environmental impact while maintaining high performance standards. The advancement of Vacuum Coating technologies also plays a crucial role in achieving these sustainability goals.
Physical Vapor Deposition (PVD) Coatings Market Trends
Demand from the Electronics Sector
Physical vapor deposition (PVD) coatings have become increasingly critical in the electronics sector, particularly for applications in microelectronics, optics, storage devices, and semiconductors. The application of electronics coating significantly improves substrate materials by reducing wear and friction while providing essential mechanical properties such as hardness, adhesion, and mechanical and fracture strength. These coatings are especially valuable for coating heat-sensitive materials like zinc and plastic, offering superior wear resistance, corrosion protection, chemical resistance, excellent adhesion, and uniform coating properties.
The deployment of PVD coating technology has expanded significantly in optical applications, including anti-reflection coatings in cameras, high-reflection coatings in solar receivers, and optical storage in discs. According to the World Semiconductor Trade Statistics, the global semiconductor market reached USD 555.89 billion in 2023, with optoelectronics accounting for 7.4% of the total market share. The application of sputtering targets for physical vapor deposition has become an essential component in the electronics industry, particularly in manufacturing conductive materials and dielectric thin films for semiconductor devices, integrated circuits, superconducting thin films, and ITO films. The use of semiconductor thin film technology is pivotal in advancing these applications.
Increasing Usage in Medical Industry
Physical vapor deposition (PVD) has emerged as a crucial technology in the medical industry, being widely utilized as a deposit wear-resistant thin-film coating on various medical devices due to its underlying material properties and biomechanical functionality. The application of medical device coating on medical devices provides multiple benefits, including increased adhesion, bonding, lubricity, wear resistance, reduced friction, corrosion protection, electromagnetic and radio frequency shielding, biocompatibility, decorative colors and aesthetics, chemical barriers, and nickel sensitivity compatibility with sterilization processes.
The technology has found extensive applications across various medical devices, including catheters, dental instruments, digital thermometers, endoscopes, heart valves, laboratory equipment, orthodontic appliances, orthopedic implants, pacemakers, prostheses, surgical instruments, and tubing. Titanium nitride (TiN) and chromium nitride (CrN)-based PVD coatings are predominantly used in medical devices owing to their biocompatibility and atoxic properties. Titanium nitride, with its chemical stability, acts as a barrier layer against the material layer below, reducing the interaction of biological liquids with the base metals of the prosthetics and decreasing the risk of rejection. The integration of medical device coating technology ensures enhanced performance and longevity of these devices.
Recovering Automotive Industry
PVD coatings have become integral to numerous processes and equipment in the automotive industry, including gear manufacturing knives, cutting tools, sheet metal cutting and forming molds, and metal and plastic injection molds. These automotive coating solutions are specifically designed to minimize the wear rate and provide extended tool and mold life, while also decreasing friction between moving elements of the motor, enhancing total vehicle performance efficiency. The technology enables automakers to use lighter alloys for moving parts, such as aluminum, titanium, and magnesium, resulting in significantly lighter weight vehicles without compromising performance.
The coating temperature of the PVD process, being low (around 700 degrees) compared to other coatings, reduces damage to the tooling substrate while providing superior surface properties. PVD treatments also enhance the vehicle's appearance while broadening customization options. Trims play a major marketing role in the automotive industry, differentiating models and manufacturers in a market that has been standardized by aerodynamic functions and fashion-influenced aesthetic trends. Decorative coating materials offer manufacturers a significant advantage in this area, providing decorative parts for both interior and exterior applications with a unique, exclusive appearance that weighs even less than plastic while maintaining a premium metal finish that customers prefer.
Segment Analysis: By Substrate
Metals Segment in Physical Vapor Deposition (PVD) Coatings Market
The metals substrate segment continues to dominate the global PVD coatings market, accounting for approximately 72% of the total market share in 2024. This substantial market presence is attributed to metals' superior properties as substrate materials, including excellent electrical and thermal conductivity, durability, and versatility across various applications. The segment encompasses a wide range of metals such as iron, steel, aluminum, copper, brass, titanium, bronze, zinc, tin, chromium, and nickel, which are extensively used in commercial applications. PVD coatings on metal substrates provide enhanced durability and attractive metal finishing, making them particularly valuable in industries like construction, electronics, arms and ammunition, machines and equipment, refractories, automobiles, jewelry sets, decorative products, medical devices, furniture, safes, and locks. The segment's growth is further bolstered by the increasing adoption of PVD-coated metal components in emerging applications and the continuous advancement in coating technologies that improve adhesion and performance characteristics. The use of metal coating technologies in these applications enhances the durability and aesthetic appeal of the products.
Remaining Segments in PVD Coatings Market by Substrate
The plastics and glass substrates segments represent significant opportunities in the PVD coatings market, each serving unique application areas. The plastics substrate segment has gained considerable traction due to its ability to be molded into various shapes and its lightweight properties, making it an attractive choice for automotive, consumer goods, and electronics applications. PVD coatings on plastic substrates are applied using the low-temperature arc vapor deposition process, which has opened new possibilities in decorative and functional applications. The glass substrate segment, while smaller, plays a crucial role in optical and electronic applications, particularly in industries requiring high transparency and specific electromagnetic properties. Glass substrates coated with PVD are extensively used in architectural applications, modern information and communication technologies, TV screens, and data displays, demonstrating the versatility and importance of these substrate materials in the overall market landscape. The integration of optical coating technologies in glass substrates enhances their performance in these applications.
Segment Analysis: By Material Type
Metals Segment in Physical Vapor Deposition (PVD) Coatings Market
The metals segment, including alloys, dominates the global PVD coatings market, accounting for approximately 60% of the total market share in 2024. This significant market position is attributed to the extensive use of metal and alloy PVD coating materials across various end-user industries, particularly in automotive and aerospace applications. The segment encompasses a wide range of metals including aluminum, chromium, titanium, nickel, and various precious metals, along with their alloys. These materials are preferred for their superior wear resistance, corrosion protection, and ability to enhance substrate durability. The versatility of metal coating in applications ranging from microelectronics and solar cells to medical devices and computer memory has further strengthened their market dominance.
Ceramics Segment in Physical Vapor Deposition (PVD) Coatings Market
The ceramics segment is experiencing the highest growth rate in the PVD coatings market, projected to expand at approximately 6.4% during 2024-2029. This growth is driven by the increasing adoption of ceramic PVD coatings, particularly nitrides, borides, carbides, hydrides, and oxides, in cutting tool applications. The segment's growth is further fueled by the rising demand for titanium nitride (TiN), which is extensively used as a hard, inert thin film coating on precision metal parts. The superior properties of ceramic coating, including increased hardness, enhanced lubricity, low coefficient of friction, and exceptional wear resistance, are driving their adoption across various industrial applications, particularly in high-performance cutting tools and precision components.
Remaining Segments in Material Type Segmentation
The other materials segment in the PVD coatings market includes specialized materials such as glass-based PVD coatings, fluoride compositions/compounds, and other innovative formulations. These materials play a crucial role in specific applications, particularly in modifying optical properties of glass, improving solar transmission characteristics, and enhancing aesthetic appearances. Glass-based PVD coatings are particularly important in solar and energetic control applications, while fluoride compounds are essential in antireflection coating for delicate laboratory glass equipment. These specialized materials, though representing a smaller market share, continue to be vital for specific high-value applications where conventional metal and ceramic coatings may not be suitable.
Segment Analysis: By End User
Components Segment in Physical Vapor Deposition (PVD) Coatings Market
The Components segment dominates the global Physical Vapor Deposition (PVD) Coatings market, accounting for approximately 75% of the total market share in 2024. This segment encompasses various critical applications including aerospace and defense, automotive, electronics and semiconductors, power generation, and other industrial components. The segment's leadership position is driven by increasing demand from the electronics sector, particularly in microelectronics, optics, storage devices, and semiconductors, where PVD coatings improve substrate materials by reducing wear and friction. The segment is also experiencing robust growth, projected to expand at the highest rate during 2024-2029, fueled by the recovering automotive industry and growing adoption in medical applications. The expansion is further supported by the increasing usage of PVD coatings in aerospace components, where they provide crucial properties such as wear resistance, corrosion protection, and thermal barrier capabilities. Additionally, the rising demand for electronic devices and semiconductors, coupled with the growing focus on renewable energy infrastructure, continues to drive the segment's growth.
Tools Segment in Physical Vapor Deposition (PVD) Coatings Market
The Tools segment represents a significant portion of the PVD coatings market, serving crucial applications in various cutting tools, end mills, drills, reamers, boring tools, countersinks, form tools, punches, grooving tools, and bits. This segment benefits from the lower coating temperature of the PVD process (around 700 degrees) compared to other coating methods, which reduces damage to the tooling substrate. The segment's growth is driven by the increasing demand for tools with enhanced properties such as improved hardness, wear and oxidation resistance, and prevention of premature cutting-edge chipping. PVD coatings in the tools segment also contribute to reducing edge build-up and increasing the time between tool re-sharpening/re-grindings and replacements. The segment's value proposition is particularly strong in applications requiring sharp edges, where tool coating has become the standard technology, especially for solid carbide cutting tools. TiAlN PVD coating remains the most widely deposited coating for cutting tools, while other coatings such as TiCN and CrN continue to gain traction in specialized tooling applications. The integration of hard coating technologies further enhances the performance and lifespan of these tools.
Physical Vapor Deposition (PVD) Coatings Market Geography Segment Analysis
Physical Vapor Deposition (PVD) Coatings Market in Asia-Pacific
The Asia-Pacific region represents the dominant force in the global Physical Vapor Deposition (PVD) coatings market, encompassing major economies like China, India, Japan, and South Korea. The region's leadership is driven by its robust manufacturing sector, particularly in electronics, automotive, and medical devices. The presence of major manufacturing facilities, coupled with increasing investments in research and development, has established Asia-Pacific as a hub for PVD coating technologies. Countries in this region have shown significant advancement in adopting these technologies across various applications, from semiconductors to decorative finishes, aligning with the growing ceramic coating market.
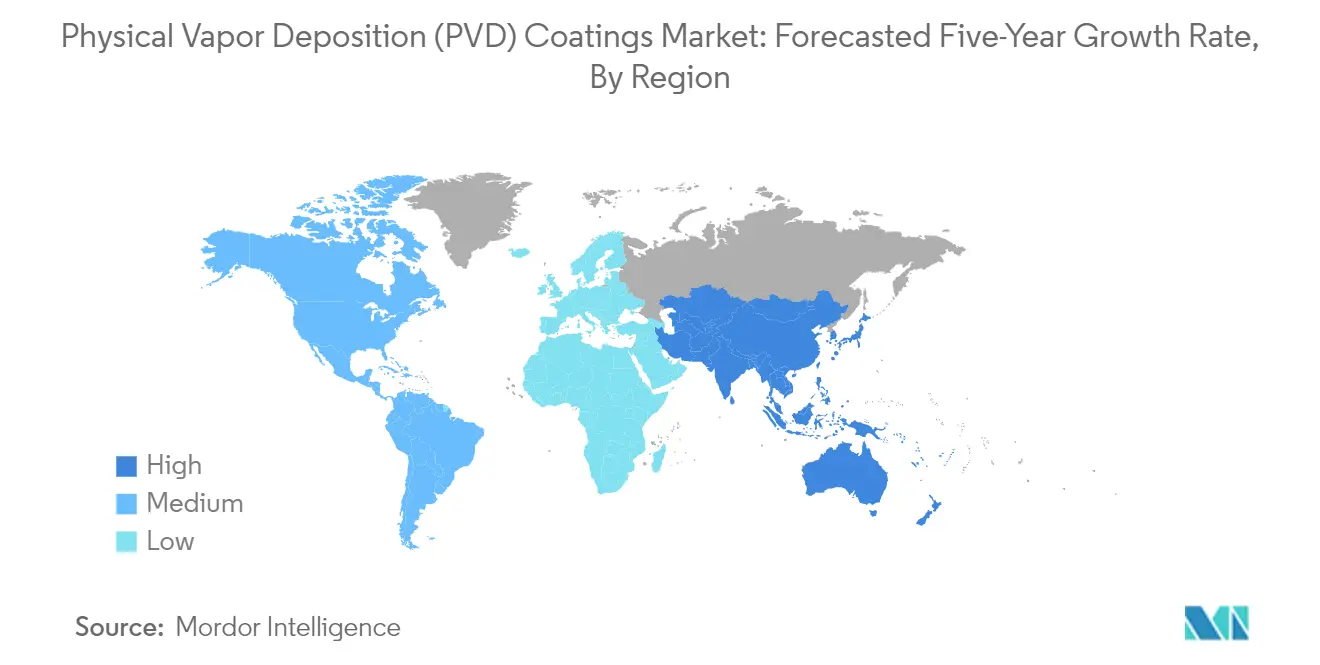
Physical Vapor Deposition (PVD) Coatings Market in China
China stands as the powerhouse of the Asia-Pacific PVD coatings market, commanding approximately 61% of the regional market share. The country's dominance is supported by its extensive manufacturing infrastructure and strong presence in electronics production. China's leadership in sectors such as automotive, electronics, and renewable energy has created substantial demand for PVD coatings. The country's commitment to technological advancement, particularly in semiconductor manufacturing and electric vehicle production, continues to drive market growth. The presence of numerous electronics manufacturing facilities and ongoing investments in research and development further solidifies China's position as the regional leader, contributing significantly to the optical coating market.
Growth Dynamics in Chinese PVD Coatings Market
China is also leading the growth trajectory in the Asia-Pacific region, with a projected growth rate of approximately 6% from 2024-2029. The country's aggressive expansion in renewable energy sectors, particularly in solar and wind energy applications, is creating new opportunities for PVD coatings. China's push towards electric vehicle manufacturing and the development of advanced electronics manufacturing capabilities are key drivers of this growth. The government's focus on technological self-reliance and the expansion of domestic manufacturing capabilities in critical sectors are expected to further accelerate market development, impacting the automotive coating market and the metal coating market.
Physical Vapor Deposition (PVD) Coatings Industry Overview
Top Companies in Physical Vapor Deposition (PVD) Coatings Market
The physical vapor deposition (PVD) coatings market is led by established players like OC Oerlikon Management AG, voestalpine eifeler group, and IHI Corporation, who have maintained their positions through continuous innovation and a global presence. Companies are focusing on developing advanced coating technologies and expanding their product portfolios through R&D investments, particularly in areas like electronics, automotive, and aerospace applications. Strategic partnerships and collaborations with end-user industries have become increasingly common to develop customized coating solutions. Market leaders are emphasizing operational excellence through modernization of coating facilities and the adoption of automated processes. Geographic expansion, particularly in the emerging markets of Asia-Pacific, has been a key growth strategy, with companies establishing new coating centers and technical support facilities to better serve regional customers.
Fragmented Market with Strong Regional Players
The global PVD coatings market exhibits a mixed competitive structure with both multinational conglomerates and specialized coating service providers playing significant roles. While major corporations like OC Oerlikon and IHI Corporation leverage their diverse technological capabilities and extensive distribution networks, specialized players have carved out strong positions in specific applications or regional markets. The market remains relatively fragmented, with numerous regional players maintaining substantial market share in their respective territories through deep customer relationships and localized service offerings. The industry has witnessed increasing consolidation through strategic acquisitions, particularly in mature markets, as companies seek to expand their technological capabilities and geographic reach.
The competitive dynamics are characterized by a combination of global reach and local expertise, with successful players maintaining both elements in their business models. Market participants are increasingly focusing on vertical integration to control quality and costs while expanding their service offerings. The barriers to entry remain high due to the capital-intensive nature of the business and the technical expertise required, which has led to the emergence of strong regional players who specialize in specific industry verticals or coating technologies like ion plating and sputtering coating. The industry has seen a trend toward consolidation, particularly in mature markets, though new entrants continue to emerge in developing regions with growing industrial bases.
Innovation and Service Excellence Drive Success
Success in the PVD coatings market increasingly depends on the ability to offer comprehensive coating solutions rather than just products. Market leaders are investing heavily in research and development to develop proprietary coating technologies and processes that offer superior performance characteristics. Customer service excellence, including quick turnaround times and technical support, has become a critical differentiator in the market. Companies are also focusing on developing sustainable coating solutions and environmentally friendly processes to address growing regulatory pressures and customer preferences. The ability to offer customized solutions for specific applications while maintaining cost competitiveness has become crucial for market success.
For new entrants and smaller players, success lies in identifying and serving niche markets or specific geographic regions where they can build strong customer relationships and specialized expertise. The development of innovative coating solutions for emerging applications, particularly in the electronics and renewable energy sectors, presents opportunities for market expansion. Companies must also focus on building robust supply chains and maintaining strong relationships with raw material suppliers to ensure consistent quality and competitive pricing. The increasing focus on quality certifications and compliance with industry standards has become crucial for maintaining market position and accessing new opportunities in regulated industries like aerospace and medical devices. Technologies such as cathodic arc deposition and thermal evaporation coating are being explored to enhance performance and meet specific industry needs.
Physical Vapor Deposition (PVD) Coatings Market Leaders
-
voestalpine eifeler group
-
OC OerlikonManagement AG
-
IHI Ionbond AG (IHI Corporation)
-
HEF
-
Impact Coatings
- *Disclaimer: Major Players sorted in no particular order
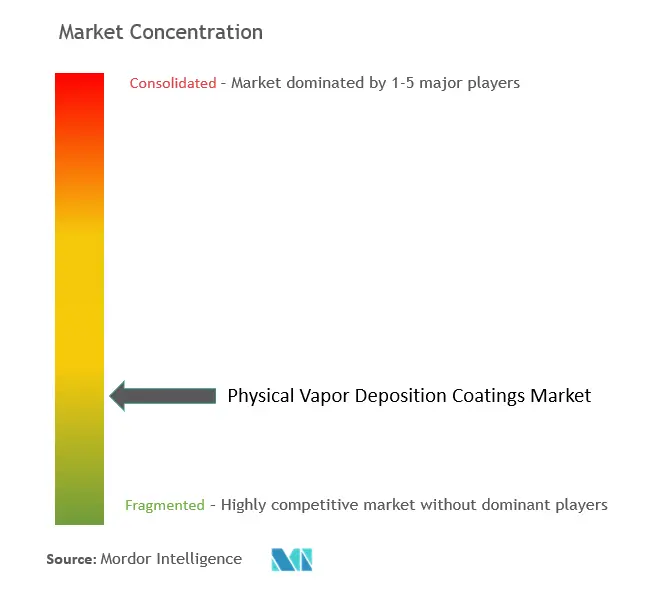
Physical Vapor Deposition (PVD) Coatings Market News
- April 2022: Impact Coatings announced the establishment of a Chinese subsidiary with headquarters in Shanghai. The opening is expected to disseminate Impact Coatings' market-leading expertise in PVD coatings for hydrogen solutions and increase the availability of coating services solutions to Chinese customers in the hydrogen value chain.
- January 2022: IHI Ionbond announced its significant investment in decorative coating capacity by purchasing a Hauzer Flexicoat 1500 PVD system. This large-scale coating system has an impressive coating zone of 0.9 m diameter by 1.5 m height. It is a welcome addition to the growing capabilities of the Ionbond component coating facility at Consett County Durham.
Physical Vapor Deposition (PVD) Coatings Industry Segmentation
Physical vapor deposition (PVD) coating is a dry coating process. Mostly, the coating is transferred to the substrate with the help of a medium, such as a solvent. In the case of PVD coatings, the vapor is generated, transferred in the gas phase, and then deposited as a coating directly to the substrate without using any medium.
The physical vapor deposition (PVD) coating market is segmented by substrate, material type, end user, and geography. By substrate, the market is segmented into metals, plastics, and glass. By material type, the market is segmented into metals (including alloys), ceramics, and other material types. By end user, the market is segmented into tools and components (aerospace and defense, automotive, electronics and semiconductors (including optics), power generation, and other components. The report also covers the market sizes and forecasts for the PVD coatings market in 27 major countries across various regions. For each segment, the market sizes and forecasts are provided in terms of revenue (USD).
Substrate | Metals | ||
Plastics | |||
Glass | |||
Material Type | Metals (Includes Alloys) | ||
Ceramics | |||
Other Material Types | |||
End User | Tools | ||
Components | Aerospace and Defense | ||
Automotive | |||
Electronics and Semiconductors (Including Optics) | |||
Power Generation | |||
Other Components (Solar Products, Medical Equipment, and Others) | |||
Geography | Asia-Pacific | China | |
India | |||
Japan | |||
South Korea | |||
Malaysia | |||
Thailand | |||
Indonesia | |||
Vietnam | |||
Rest of Asia-Pacific | |||
North America | United States | ||
Canada | |||
Mexico | |||
Europe | Germany | ||
United Kingdom | |||
France | |||
Italy | |||
Spain | |||
Turkey | |||
Russia | |||
NORDIC Countries | |||
Rest of Europe | |||
South America | Brazil | ||
Argentina | |||
Colombia | |||
Rest of South America | |||
Middle East and Africa | Saudi Arabia | ||
Nigeria | |||
Qatar | |||
Egypt | |||
United Arab Emirates | |||
South Africa | |||
Rest of Middle East and Africa |
Metals |
Plastics |
Glass |
Metals (Includes Alloys) |
Ceramics |
Other Material Types |
Tools | |
Components | Aerospace and Defense |
Automotive | |
Electronics and Semiconductors (Including Optics) | |
Power Generation | |
Other Components (Solar Products, Medical Equipment, and Others) |
Asia-Pacific | China |
India | |
Japan | |
South Korea | |
Malaysia | |
Thailand | |
Indonesia | |
Vietnam | |
Rest of Asia-Pacific | |
North America | United States |
Canada | |
Mexico | |
Europe | Germany |
United Kingdom | |
France | |
Italy | |
Spain | |
Turkey | |
Russia | |
NORDIC Countries | |
Rest of Europe | |
South America | Brazil |
Argentina | |
Colombia | |
Rest of South America | |
Middle East and Africa | Saudi Arabia |
Nigeria | |
Qatar | |
Egypt | |
United Arab Emirates | |
South Africa | |
Rest of Middle East and Africa |
Physical Vapor Deposition (PVD) Coatings Market Research FAQs
How big is the Physical Vapor Deposition Coatings Market?
The Physical Vapor Deposition Coatings Market size is expected to reach USD 11.13 billion in 2025 and grow at a CAGR of 6.43% to reach USD 15.20 billion by 2030.
What is the current Physical Vapor Deposition Coatings Market size?
In 2025, the Physical Vapor Deposition Coatings Market size is expected to reach USD 11.13 billion.
Who are the key players in Physical Vapor Deposition Coatings Market?
voestalpine eifeler group, OC OerlikonManagement AG, IHI Ionbond AG (IHI Corporation), HEF and Impact Coatings are the major companies operating in the Physical Vapor Deposition Coatings Market.
Which is the fastest growing region in Physical Vapor Deposition Coatings Market?
Asia-Pacific is estimated to grow at the highest CAGR over the forecast period (2025-2030).
Which region has the biggest share in Physical Vapor Deposition Coatings Market?
In 2025, the Asia-Pacific accounts for the largest market share in Physical Vapor Deposition Coatings Market.
What years does this Physical Vapor Deposition Coatings Market cover, and what was the market size in 2024?
In 2024, the Physical Vapor Deposition Coatings Market size was estimated at USD 10.41 billion. The report covers the Physical Vapor Deposition Coatings Market historical market size for years: 2019, 2020, 2021, 2022, 2023 and 2024. The report also forecasts the Physical Vapor Deposition Coatings Market size for years: 2025, 2026, 2027, 2028, 2029 and 2030.