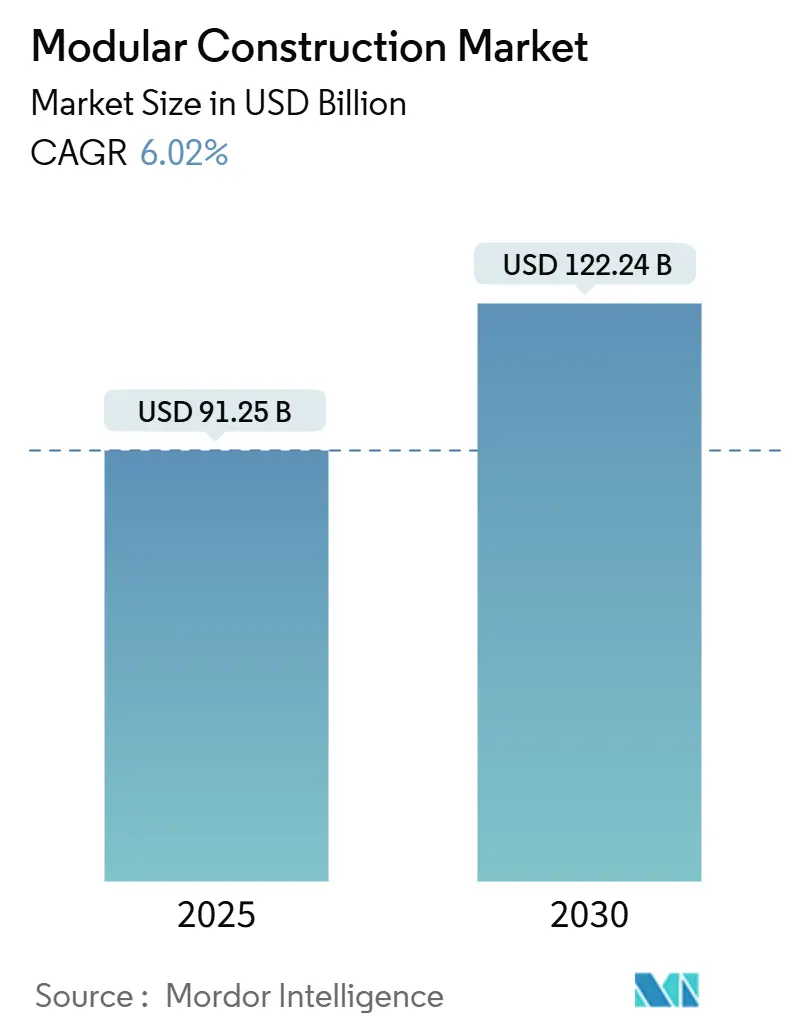
Modular Construction Market Analysis by Mordor Intelligence
The modular construction market stands at USD 91.25 billion in 2025 and is projected to reach USD 122.24 billion by 2030, expanding at a 6.02% CAGR. Rising labor shortages, supportive regulations, and the visible success of factory-built housing projects are repositioning modular methods from niche solutions to primary construction options across many regions. Asia-Pacific commands a 47% revenue share, powered by rapid urbanization, long-running affordable-housing mandates, and a deep manufacturing base that supplies modules to domestic and export projects. Permanent solutions account for 67% of the modular construction market, reflecting broad acceptance that factory-assembled buildings can meet durability and aesthetic expectations equal to site-built structures. Steel frameworks remain the backbone of production with an 84% share, favored for structural strength, dimensional stability, and well-established supply chains. Institutional owners—particularly education and healthcare operators—lead demand because off-site fabrication minimizes disruption, accelerates occupancy, and compresses overall project schedules.
Key Report Takeaways
- By construction type, permanent modular captured 67% of the modular construction market share in 2024, while relocatable units are the fastest-growing application at a 7.39% CAGR through 2030.
- By material, steel frameworks held 84% of the modular construction market share in 2024; and are projected to expand at a 6.12% CAGR to 2030.
- By end-user sector, industrial and institutional facilities accounted for 43% of the modular construction market size in 2024; residential is poised to grow at 7.82% CAGR through 2030.
- By service stage, new construction represented 72% of 2024 revenue, with after-sales maintenance & refurbishment (renovation) expected to register the fastest growth at 6.54% CAGR through 2030.
- By geography, Asia-Pacific led with 47% revenue share in 2024, and is projected to post the highest regional CAGR of 7.18% to 2030.
Global Modular Construction Market Trends and Insights
Drivers Impact Analysis
Driver | (~) % Impact on CAGR Forecast | Geographic Relevance | Impact Timeline |
---|---|---|---|
Increasing Demand for Modular Construction from Developed Economies | +1.80% | North America, Europe, developed Asia-Pacific markets (Japan, Australia) | Medium term (2-4 years) |
Supportive Government Initiatives for Modular Construction | +1.50% | Global, with early gains in Australia, Canada, United States, United Kingdom | Short term (≤ 2 years) |
Rising Demand for Temporary/Portable Structures | +0.80% | Global, with particular strength in disaster-prone regions and emerging markets | Short term (≤ 2 years) |
Significantly Reduced Project Timelines | +1.20% | Global, with highest impact in labor-constrained developed markets | Medium term (2-4 years) |
Solution to Skilled Labor Shortage | +1.00% | North America, Europe, developed Asia-Pacific markets with aging workforces | Long term (≥ 4 years) |
Source: Mordor Intelligence
Developed Economies Embrace Modular Solutions
High household demand collides with shrinking construction workforces across North America and Western Europe. In Sweden, 84% of detached homes now originate from factory lines, establishing a mature reference point that policymakers elsewhere study. Japanese builders also sustain high adoption levels, while the United States remains below 4% of its housing output but records strong momentum in healthcare, education, and multi-family projects. The visibility of successful Scandinavian and Japanese case studies reassures investors that modular construction market risk is manageable. Builders in Australia and Canada replicate similar models for social-housing pipelines, reinforcing a global learning loop that spreads expertise and reduces first-mover uncertainty.
Government Initiatives Catalyze Market Growth
Public authorities are increasingly writing modular requirements into housing and infrastructure programs. Queensland’s 2024-25 budget earmarked AUD 2.8 billion (USD 1.85 billion) to deliver 600 modular homes that can be placed on-site in 3 months, versus the lengthy schedules of conventional builds[1]Queensland Government, “Homes for Queenslanders Budget 2024-25,” qld.gov.au . The U.S. Department of Housing and Urban Development issued 90 new or revised manufactured-home standards in 2024, modernizing a code base that had been largely static for three decades[2]U.S. Department of Housing and Urban Development, “Manufactured Home Construction and Safety Standards 2024 Update,” hud.gov . These steps streamline approvals, reassure lenders, and nudge specifiers to evaluate a modular approach first, thereby expanding the modular construction market.
Temporary Structures Drive Market Flexibility
Relocatable units accounted for 33% of demand in 2024, underscoring the appeal of fast-to-deploy, reusable assets for disaster relief, health-care surges, and school expansions. During the COVID-19 response, modular triage centers and testing booths were stood up in days, proving that factory-built solutions can meet stringent clinical specifications under extreme time pressure. Similar techniques supplied temporary housing after the 2023 Hawaii wildfires, confirming value in crisis response. Increasing sophistication—such as integrated HVAC, renewables, and smart-building controls—allows these units to function as high-performance assets rather than stop-gap shelters, extending addressable demand for the modular construction market.
Accelerated Project Timelines Transform Industry Economics
Concurrent sitework and factory fabrication compress schedules by 30–50% for many building types. University of South Australia researchers calculated that weather-delay avoidance alone can save builders USD 26,400 on a USD 4.22 million project, emphasizing tangible financial upside. Earlier revenue generation and reduced carrying costs strengthen the owner’s business case, particularly for commercial developers. The ability to lock in predictable delivery timelines also de-risks public-sector infrastructure programs that face tight budget windows, thereby broadening the appeal of the modular construction market.
Restraints Impact Analysis
Restraint | (~) % Impact on CAGR Forecast | Geographic Relevance | Impact Timeline |
---|---|---|---|
High Initial Investment | -1.10% | Global, with higher impact in emerging markets with limited capital access | Long term (≥ 4 years) |
Design Limitations | -0.70% | Global, with particular constraints in markets requiring high architectural customization | Medium term (2-4 years) |
Regulatory and Code Variations Across region | -0.90% | Global, with highest impact on companies operating across multiple jurisdictions | Medium term (2-4 years) |
Source: Mordor Intelligence
High Initial Investment Creates Market Entry Barriers
Setting up a dedicated factory, automation lines, and a certified quality-control system requires sizable capital outlays before revenue flows. Several well-funded start-ups, including Katerra, failed despite clear product-market fit because operations ramped slower than capital was burned. Rising energy costs and inflation magnify those cash-flow stresses. Established contractors often respond through joint ventures that share risk, but the basic hurdle remains: entrants need scale almost immediately to amortize fixed assets, limiting the pool of viable new competitors and slowing overall growth of the modular construction market.
Regulatory Variations Complicate Cross-Border Expansion
Building codes still default to on-site methodologies, forcing modular producers to navigate overlapping state or national approvals. The Interstate Compact on Industrialized/Modular Buildings aims to standardize U.S. requirements, but adoption is uneven. Australia’s new Off-site Construction Handbook and the United Kingdom’s research into volumetric-module safety signal progress, yet true harmonization is years away. Each extra compliance step adds cost, extends lead times, and discourages small factories from exporting, tempering growth in the modular construction industry.
Segment Analysis
Construction Type: Permanent Solutions Dominate Market Share
Permanent modular formats delivered 67% of 2024 revenue. Within that share, residential high-rise projects such as 147 St. Felix in Brooklyn illustrate architectural flexibility that dismisses lingering perceptions of “boxy” units. The modular construction market size for permanent solutions is forecast to expand alongside digital design tools that knit mechanical, electrical, and plumbing systems into repeatable chassis, reducing re-work during assembly.
Institutional clients prize the diminished disruption that off-site fabrication delivers. Fifteen-story dormitory schemes erected in half the usual time frame help universities like California Polytechnic State University secure student revenue faster. Developers also value factory-controlled quality, which meets or exceeds code for structural integrity and fire resistance, supporting premium valuations in the modular construction market.
Material: Steel Frameworks Underpin Industry Growth
Steel claimed 84% of 2024 material volume due to its high strength-to-weight ratio and global availability. The modular construction market size for steel-based modules benefits from predictable torsional rigidity, allowing taller configurations without material changes. Insurance carriers often reduce premiums for non-combustible frames, tipping whole-life costs further in steel’s favor.
A 20-year lifecycle study comparing a typical 10,000 ft² project pegged total outlay at USD 350,000 for steel modules versus up to USD 1.1 million for traditional builds, underscoring economic resilience. Emerging engineered-wood technologies, such as cross-laminated timber, are penetrating niche mid-rise projects, but steel’s mature supply chain and recycling value maintain its dominance in the modular construction market.
End-user Sector: Industrial/Institutional Applications Lead Adoption
Industrial and institutional clients delivered 43% of 2024 sales. Hospitals turn to off-site fabrication to minimize operating-room downtime, while school districts rely on factory-built classrooms to add capacity with minimal campus disturbance. Collectively, these factors position the institutional segment as the anchor of the modular construction market.
The expansion of commercial offices, driven by flexible work policies, is encouraging landlords to implement adaptable floorplates that can be reconfigured off-site. Retailers deploy relocatable units for pop-up concepts that test new markets without lengthy capex commitments. Together, these shifts broaden the modular construction industry’s demand profile beyond its early health-care and education heartland.
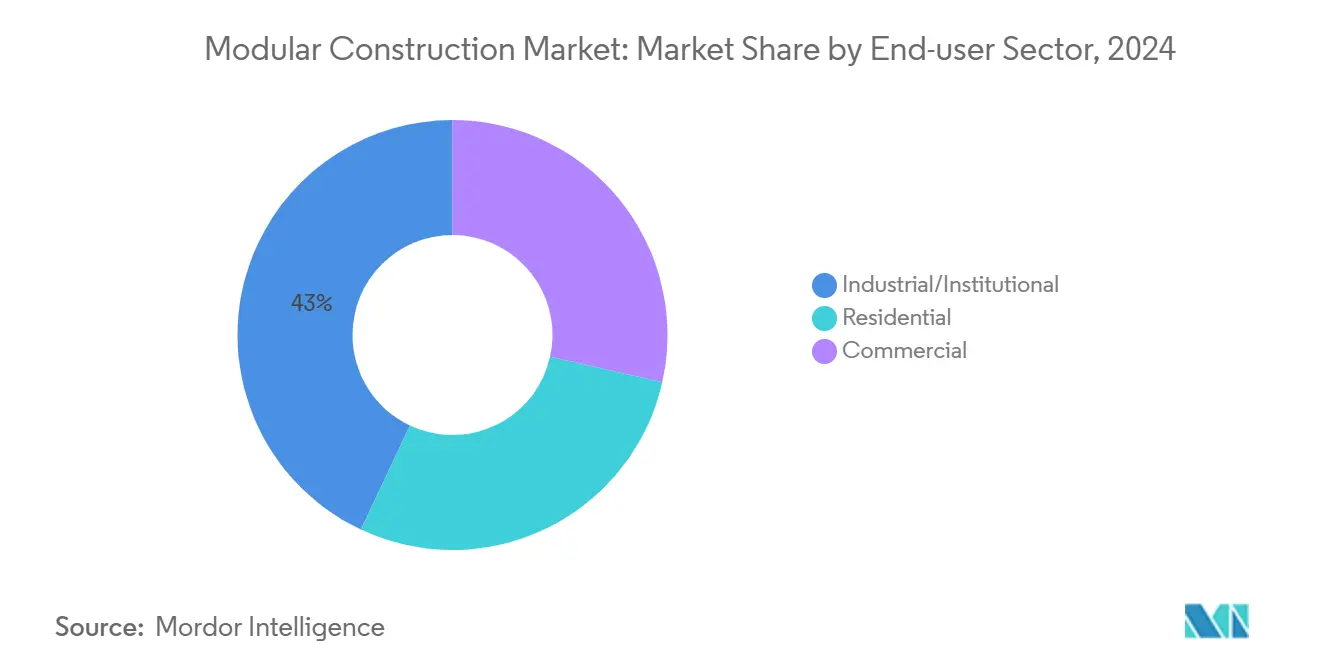
Note: Segment shares of all individual segments available upon report purchase
Service Stage: New Construction Dominates Current Applications
New-build projects generated 72% of revenue in 2024. Developers prefer sourcing entire modules from one factory to maximize coordination and minimize sequencing risk, cementing new construction as the core of the modular construction market.
As delivery volumes rise, a secondary market for module refurbishment is forming. Maintenance providers can swap façade panels or mechanical pods in controlled factory settings, shortening downtime compared with on-site refits. Circular-economy models that reclaim steel frames at end-of-life further extend the profit pool and enhance sustainability credentials, promising fresh revenue lines within the modular construction market.
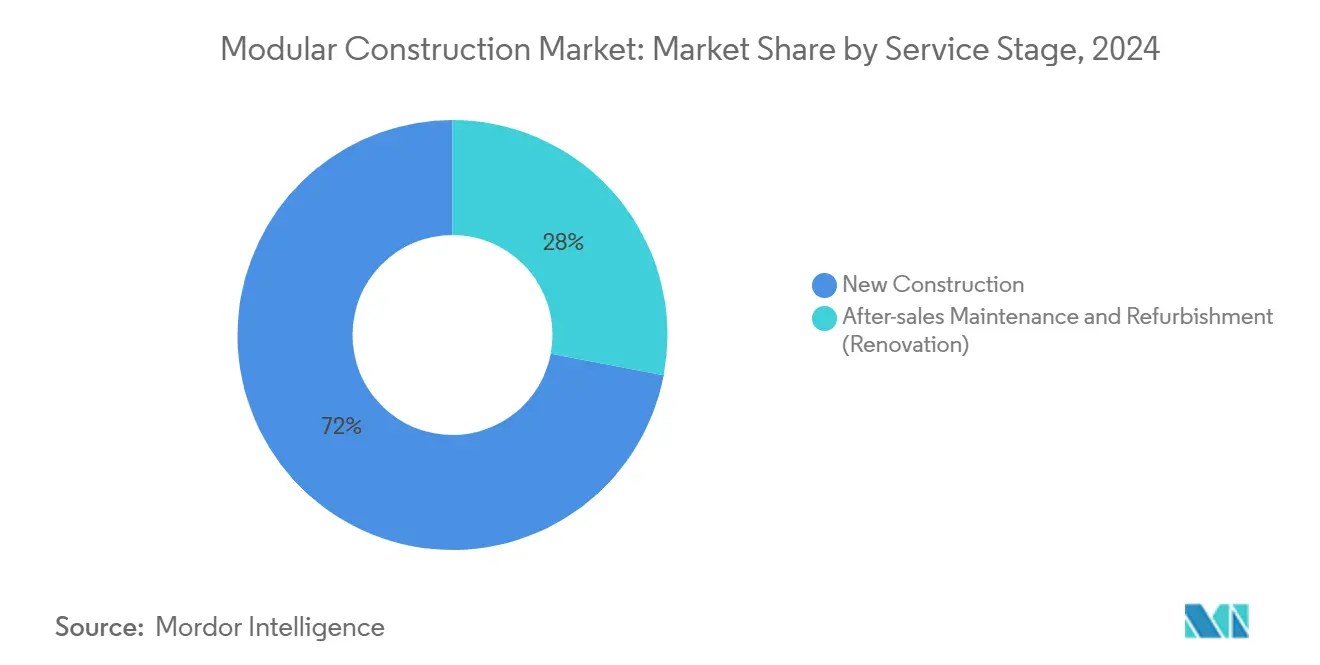
Geography Analysis
Asia-Pacific dominated with 47% modular construction market share in 2024. China’s vast manufacturing footprint enables low-cost module production, while Japan’s pioneers such as Sekisui House sustain a reputation for high-precision factory homes. Australia’s import of USD 330 million of prefab components over five years highlights robust cross-border trade, and state budgets earmark modular stock to ease social-housing backlogs. Urbanization pressures, supported by government grants, assure continued regional leadership.
North America holds significant expansion potential between 2025 and 2030. The United States faces a deficit of skilled construction labor amid a 7 million-home supply gap, so factory processes that decouple labor intensity from site location appeal strongly. HUD’s 2024 code overhaul and pending Federal legislation encourage wider adoption. Canada’s national housing strategy explicitly references prefabricated solutions, with senior ministers advocating modular supply to improve affordability[3]Government of Canada, “National Housing Strategy Progress Report 2024,” canada.ca .
Europe shows varied maturity by sub-region. Nordic countries display seasoned off-site ecosystems; Sweden builds 45% of homes in factories, offering proven technical and commercial templates for neighboring markets. The United Kingdom targets 25% modular penetration by 2030 and funds risk assessments to accelerate take-up. Southern Europe lags due to fragmented supply chains and complex permitting, yet rising carbon-reduction goals and labor scarcity are likely to converge in favor of the modular construction market.
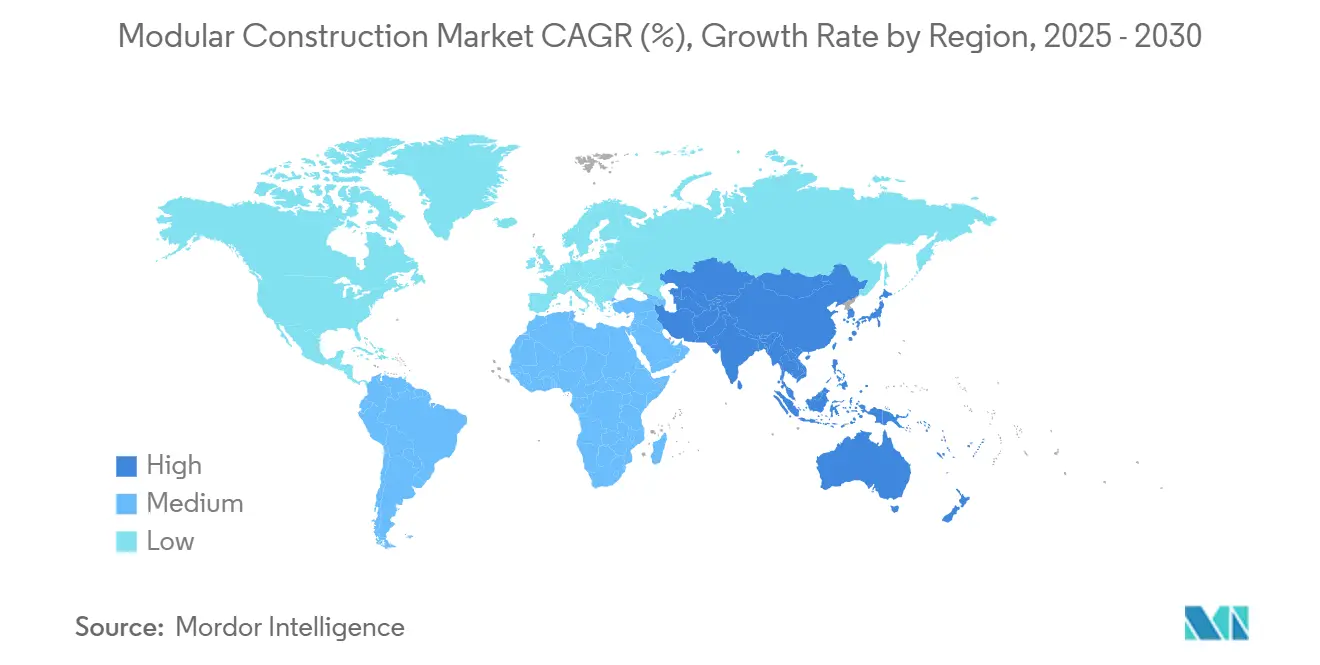
Competitive Landscape
Global competition is regionally clustered because haul-distance economics and local building codes restrict plant catchments. Skanska, Bouygues Construction, and Lendlease deploy vertically integrated models that include development, design, factory production, and on-site assembly, allowing tight control over quality and schedule. In Japan, Sekisui House operates dedicated lines capable of outputting customized homes in days, while Clayton Homes dominates the U.S. modular housing niche via a network of regional factories.
Strategic M&A is redefining scale economics. ATCO Structures’ 2024 acquisition of NRB Modular Solutions expanded its relocatable and permanent offerings, while Builders FirstSource’s purchase of Alpine Lumber brought engineered structural products into its national network. Technology investment is equally pivotal: AECOM integrates BIM, data analytics, and program-management platforms to win megaproject mandates, citing a record design backlog in 2025. Artificial-intelligence pilots focus on automated design-for-manufacture scripts that raise throughput and reduce change-order risk, reinforcing digital capabilities as a competitive moat within the modular construction market.
Bankruptcies of capital-intensive start-ups highlight execution challenges. Firms such as Katerra raised significant venture funds yet failed to attain the throughput required to offset fixed-plant costs. Consequently, established contractors with balance-sheet strength or joint-venture consortiums currently command buyer confidence, while smaller entrants often specialize in niche medical or educational pods to avoid head-to-head competition.
Modular Construction Industry Leaders
-
Bechtel Corporation
-
Laing O'Rourke
-
Red Sea International
-
Sekisui House Ltd
-
Skanska
- *Disclaimer: Major Players sorted in no particular order
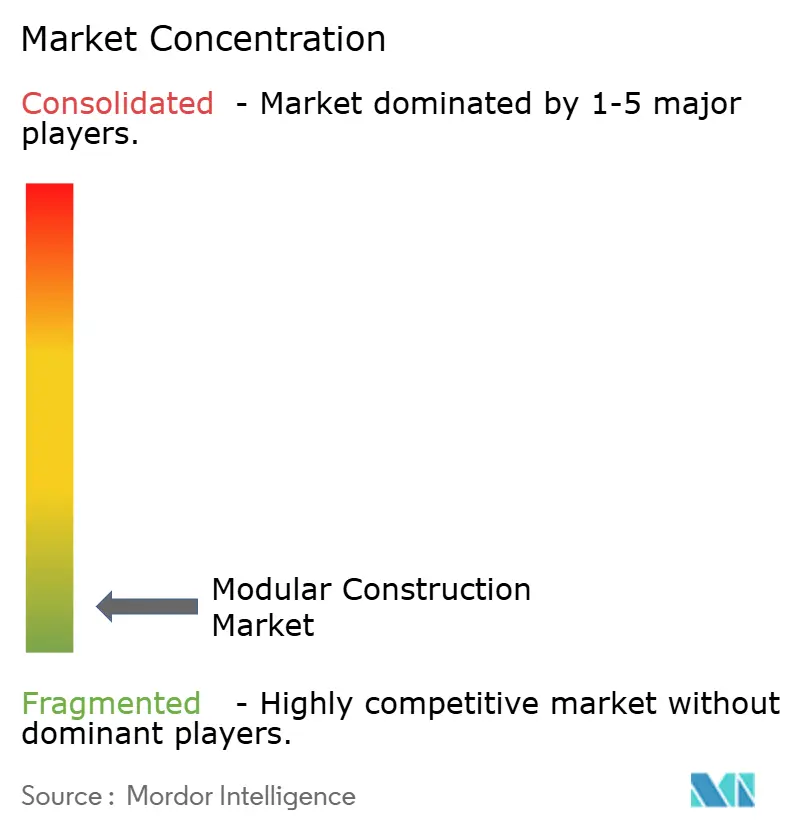
Recent Industry Developments
- February 2025: Skanska has finalized an agreement to sell its modular factory, BoKlok Byggsystem AB, located in Gullringen, Sweden, for approximately SEK 110 million (~USD 10.11 million), to Surewood Housing AB, which is part of Gelba and Active Invest.
- September 2024: ATCO Structures has successfully acquired NRB Modular Solutions, enhancing its portfolio of modular products. This acquisition is expected to strengthen ATCO's position in the modular construction market by offering a more diverse range of solutions to meet evolving customer demands.
Global Modular Construction Market Report Scope
Modular construction involves delivering and assembling pre-fabricated engineered building units on the construction site. The construction process of modular buildings is faster than the conventional process, as it requires less time and offers greater flexibility and improved air quality.
The modular construction market is segmented by construction, material, end-user industry, and geography. By construction, the market is segmented into permanent modular and relocatable modular. The market is segmented by materials: steel, concrete, wood, and plastic. By end-user industry, the market is segmented into commercial, industrial/institutional, and residential. The report also covers the market sizes and forecasts for the modular construction market in 15 countries across major regions. For each segment, the market sizing and forecasts are done based on value (USD).
Segmentation by Construction Type | Permanent Modular | ||
Relocatable Modular | |||
Segmentation by Material | Steel | ||
Concrete | |||
Wood | |||
Plastic | |||
Segmentation by End-user Sector | Residential | ||
Commercial | |||
Industrial/Institutional | |||
Segmentation by Service Stage | New Construction | ||
After-sales Maintenance and Refurbishment (Renovation) | |||
Segmentation by Geography | Asia-Pacific | China | |
India | |||
Japan | |||
South Korea | |||
Australia | |||
Rest of Asia-Pacific | |||
North America | United States | ||
Canada | |||
Mexico | |||
Europe | Germany | ||
United Kingdom | |||
France | |||
Italy | |||
Nordics | |||
Rest of Europe | |||
South America | Brazil | ||
Argentina | |||
Chile | |||
Rest of South America | |||
Middle East and Africa | Saudi Arabia | ||
United Arab Emirates | |||
Turkey | |||
South Africa | |||
Nigeria | |||
Rest of Middle East and Africa |
Permanent Modular |
Relocatable Modular |
Steel |
Concrete |
Wood |
Plastic |
Residential |
Commercial |
Industrial/Institutional |
New Construction |
After-sales Maintenance and Refurbishment (Renovation) |
Asia-Pacific | China |
India | |
Japan | |
South Korea | |
Australia | |
Rest of Asia-Pacific | |
North America | United States |
Canada | |
Mexico | |
Europe | Germany |
United Kingdom | |
France | |
Italy | |
Nordics | |
Rest of Europe | |
South America | Brazil |
Argentina | |
Chile | |
Rest of South America | |
Middle East and Africa | Saudi Arabia |
United Arab Emirates | |
Turkey | |
South Africa | |
Nigeria | |
Rest of Middle East and Africa |
Key Questions Answered in the Report
What is the current value of the modular construction market?
The modular construction market is valued at USD 91.25 billion in 2025 and is forecast to reach USD 122.24 billion by 2030.
Which region holds the largest modular construction market share?
Asia-Pacific leads with 47% of 2024 revenue, supported by rapid urbanization and strong government backing for factory-built housing.
Why is steel the preferred material for modular buildings?
Steel commands 84% share because of its strength-to-weight ratio, fire resistance, and mature recycling and supply chains, which together reduce lifecycle costs.
How quickly can a modular project be delivered compared with traditional construction?
Parallel site and factory workflows cut schedules by 30–50%, enabling faster revenue generation and lower financing risk.
What are the main barriers to wider modular adoption?
High upfront factory investment and inconsistent building codes across jurisdictions raise entry costs and complicate expansion for modular producers.