Magnetic Materials Market Size and Share
Magnetic Materials Market Analysis by Mordor Intelligence
The Magnetic Materials Market size is estimated at 33.01 Million tons in 2025, and is expected to reach 44.32 Million tons by 2030, at a CAGR of 6.07% during the forecast period (2025-2030). Growth momentum flows from rapid electrification across automotive, renewable energy, and industrial automation, where high-performance magnets underpin motor efficiency, power density, and weight reduction. Asia-Pacific maintains an outsized influence due to China’s control of mined and refined rare earths, while policy incentives in Europe and North America are spurring domestic magnet production. Technology investments are accelerating in rare earth-free alternatives, additive manufacturing of complex magnet shapes, and grain-boundary diffusion processes that cut heavy rare earth usage without sacrificing coercivity. Competitive activity includes joint ventures between miners and motor makers to secure supplies, as well as vertical integration that links ore extraction with finished magnets.
Key Report Takeaways
- By type, soft magnetic materials led with 61.20% revenue share in 2024; hard/permanent magnets are projected to expand at a 6.91% CAGR through 2030.
- By material, NdFeB commanded 44.19% of magnetic materials market share in 2024, while ferrite magnets are forecast to grow at 6.20% CAGR to 2030.
- By end-user industry, electronics accounted for 38.10% of the magnetic materials market size in 2024; automotive applications exhibit the fastest growth at 7.85% CAGR between 2025-2030.
- By application, electric motors and generators captured 39.48% of magnetic materials market size in 2024 and are advancing at a 6.55% CAGR through 2030.
- By geography, Asia-Pacific held 67.12% of global demand in 2024 and is set to grow at 7.71% CAGR to 2030.
Global Magnetic Materials Market Trends and Insights
Drivers Impact Analysis
Driver | (~) % Impact on CAGR Forecast | Geographic Relevance | Impact Timeline |
---|---|---|---|
The Rising Adaption of Magnetic Materials in Power Generation Industry | +1.20% | Europe, Asia-Pacific | Medium term (2-4 years) |
Rising Electric Vehicle Adoption Fuels Demand for Magnetic Materials | +1.80% | China, Europe, North America | Short term (≤2 years) |
Growing Robotics and Automation Usage Accelerates Magnetic Materials Demand | +0.90% | East Asia, North America | Medium term (2-4 years) |
Increasing Advancements in Consumer Electronics Fuels Demand | +0.70% | Asia-Pacific | Short term (≤2 years) |
Increasing Usage in Medical Applications | +0.30% | North America and Europe | Long term (≥5 yrs) |
Source: Mordor Intelligence
The Rising Adoption of Magnetic Materials in Power Generation Industry
Permanent magnets—particularly neodymium-iron-boron (NdFeB)—enable direct-drive wind turbines that raise energy conversion efficiency by 20-25% compared with geared alternatives[1]International Energy Agency, “Rare-Earth Elements – Analysis,” iea.org . The International Energy Agency expects rare earth demand in clean-energy applications to reach 64 kilotons by 2040, a six-fold jump from 2021 that will sustain strong pull for high-grade magnets. Manufacturers are pursuing dysprosium-reduced compositions that preserve high coercivity while easing supply risk. In hydro generators, soft magnetic composites from Höganäs deliver 15-18% lower core losses, boosting power density and trimming system mass. Parallel R&D programs target low-temperature sintering and additive manufacturing to cut energy input and scrap.
Rising Electric Vehicle Adoption Fuels Demand for Magnetic Materials
Each battery electric car entails 2-5 kg of NdFeB magnets for traction motors, pumps, and thermal systems. Surging passenger EV sales, combined with electrification of buses and trucks, translates into steep volume gains for high-energy-product magnets. Grain-boundary diffusion techniques now lift coercivity by 20% while reducing heavy rare earth loading, enabling smaller motors with identical torque. Vehicle programs in China and Europe are driving near-term demand, while U.S. policy credits spur localized magnet facilities such as MP Materials’ plant in Texas scheduled for full magnet output by late 2025.
Growing Robotics and Automation Usage Accelerates Magnetic Materials Demand
Industrial robots rely on precise position feedback; Hall-effect and magnetoresistive sensors incorporating rare earth and ferrite elements now reach sub-micron accuracy for semiconductor and medical assembly lines. Soft magnetic composites allow three-dimensional flux paths that shrink motor footprints for collaborative robots, increasing payload-to-weight ratios without sacrificing speed. Magnetorheological elastomers enhance tactile sensing, improving safety in human-robot interaction. Factory automation investments across electronic assembly hubs in Japan, Korea, and Southeast Asia sustain incremental magnet demand.
Increasing Advancements in Consumer Electronics Fuels Demand
Wearable devices and true wireless earbuds require miniaturized magnets that preserve acoustic fidelity in ever-smaller cavities. High-flux NdFeB grades, alloyed with terbium-free recipes, maintain output while trimming critical material content. Wireless-charging pads exploit soft ferrite sheets and nanocrystalline alloys to direct flux and limit EMI, supporting multi-device fast-charging layouts. As device operating frequencies climb, demand rises for high-permeability shielding foils sourced from grain-oriented electrical steel manufacturers. Asia-Pacific contract manufacturers consume the bulk of these specialty grades, reinforcing the region’s leadership.
Restraints Impact Analysis
Restraint | (~) % Impact on CAGR Forecast | Geographic Relevance | Impact Timeline |
---|---|---|---|
High Cost in Extracting Rare Earth Materials | -1.10% | Non-Chinese manufacturers | Medium term (2-4 years) |
Environmental Scrutiny of Ferrite-Sintering Emissions | -0.60% | Europe, North America | Medium term (2-4 years) |
Limited Recycling Infrastructure for Magnetic Materials | -0.40% | Global, with variations by regional recycling capabilities | Long term (≥5 yrs) |
Source: Mordor Intelligence
High Cost in Extracting Rare Earth Materials
Rare earth ore processing demands complex separation chemistry, intensive water usage, and stringent waste remediation, all of which inflate operating costs. A 70% decline in rare earth prices through 2024 underscores volatility that discourages Western green-field projects. Regulatory initiatives such as the U.S. Inflation Reduction Act allocate grants for domestic refining, yet capital intensity and permitting hurdles prolong lead times. Technology developers like Materials Nexus claim iron-nitride magnets could slash costs by 20% and lower carbon emissions by 70%, though commercial volumes remain several years away .
Environmental Scrutiny of Ferrite-Sintering Emissions
Ferrite magnet sintering involves firing ceramic mixtures at 1,200-1,400 °C, emitting significant CO₂ and particulate matter. The European Union’s revised Industrial Emissions Directive compels producers to retrofit kilns with advanced filters and recuperative burners, elevating production costs by roughly 15-20%. Similar rules are taking shape in the United States under the Clean Air Act. Producers are piloting low-temperature sintering aids and microwave-assisted techniques that cut energy consumption. Recycling initiatives, including hydrometallurgical recovery of ferrite from end-of-life motors, claim material recovery rates of up to 90%, creating a circular feedstock stream that buffers raw-material volatility.
Segment Analysis
By Type: Soft Magnetics Maintain Scale as Permanent Magnets Accelerate
Soft magnetic materials accounted for 61.20% of demand in 2024, underpinned by extensive use in transformers, inductors, and rotating machinery. The segment’s dominance reflects the ubiquity of electrical steel laminations and amorphous ribbons in power distribution assets. Continuous casting of thin-gauge grain-oriented steel lowers core losses, raising grid efficiency across fast-industrializing economies. Meanwhile, permanent magnets draw faster incremental growth at a 6.91% CAGR because every additional EV, offshore turbine, or robotics servo relies on high-energy-product alloys. Innovations such as tomography-guided grain alignment shorten development cycles and boost remanence, ensuring sustained share gains for hard magnets within the magnetic materials market. Semi-hard magnets, though niche, serve magnetic recording heads and torque sensors where a balance of coercivity and remanence is required.
Market participants respond with differentiated portfolios: integrated steelmakers are commissioning continuous annealing lines for high-permeability NOES, whereas rare earth magnet producers invest in grain-boundary diffusion furnaces that lift coercivity without heavy rare earth surcharges. Research consortia in Japan and the EU explore exchange-spring nanocomposites that couple soft and hard phases at the nanoscale, targeting energy products above 70 MGOe. Collectively, these efforts reinforce the versatility of the magnetic materials market across voltage transformation, motion control, and data storage.
Note: Segment shares of all individual segments available upon report purchase
By Material: NdFeB Holds the Lead while Ferrite Gains Momentum
NdFeB magnets captured 44.19% of demand in 2024 thanks to unrivaled energy density essential for compact traction motors and direct-drive turbines. The introduction of cerium-rich formulations lowers cost by leveraging more abundant light rare earths, supporting volume expansion without proportional price rises. Conversely, ferrite magnets, long valued for cost advantage and corrosion resistance, are projected to grow at 6.20% CAGR as performance improvements narrow the B-H gap with rare earth options. Multi-layer extrusion and liquid-phase sintering raise ferrite’s maximum energy product, allowing deployment in e-bike motors and HVAC compressors once reserved for NdFeB. SmCo retains share in aerospace and defense where 250 °C operating temperatures and radiation resistance are mandatory.
Electrical steel, amorphous, and nanocrystalline alloys remain cornerstones of transformer cores and common-mode chokes. Continuous improvements in thin-strip casting produce ribbons below 18 µm that trim eddy-current losses up to 80%, aligning with global energy-efficiency mandates. Collectively, diversification within materials ensures the magnetic materials market remains resilient to geopolitical supply swings and raw-material price cycles.
By End-user Industry: Electronics Lead while Automotive Accelerates
Electronics consumed 38.10% of magnetic materials in 2024, reflecting pervasive use in loudspeakers, disk drives, sensors, and wireless-charging modules. The segment benefits from ongoing miniaturization, where higher flux density compensates for shrinking form factors. Meanwhile, vehicle electrification drives the fastest CAGR of 7.85%; each electric powertrain integrates traction motors, on-board chargers, and numerous actuation systems rich in magnets. Automakers in China target 100% EV market share of new sales by 2035, ensuring sizable downstream pull.
Industrial machinery, including conveyors and pumps, continues to embed magnets in variable-speed drives that raise energy efficiency across manufacturing. Power generation remains pivotal as utilities roll out multi-megawatt offshore turbines and uprated hydro units. Healthcare adoption expands with higher-field MRI scanners employing superconducting wire reinforced by iron-based superconductor tape that boosts magnetic field strength beyond 20 T.
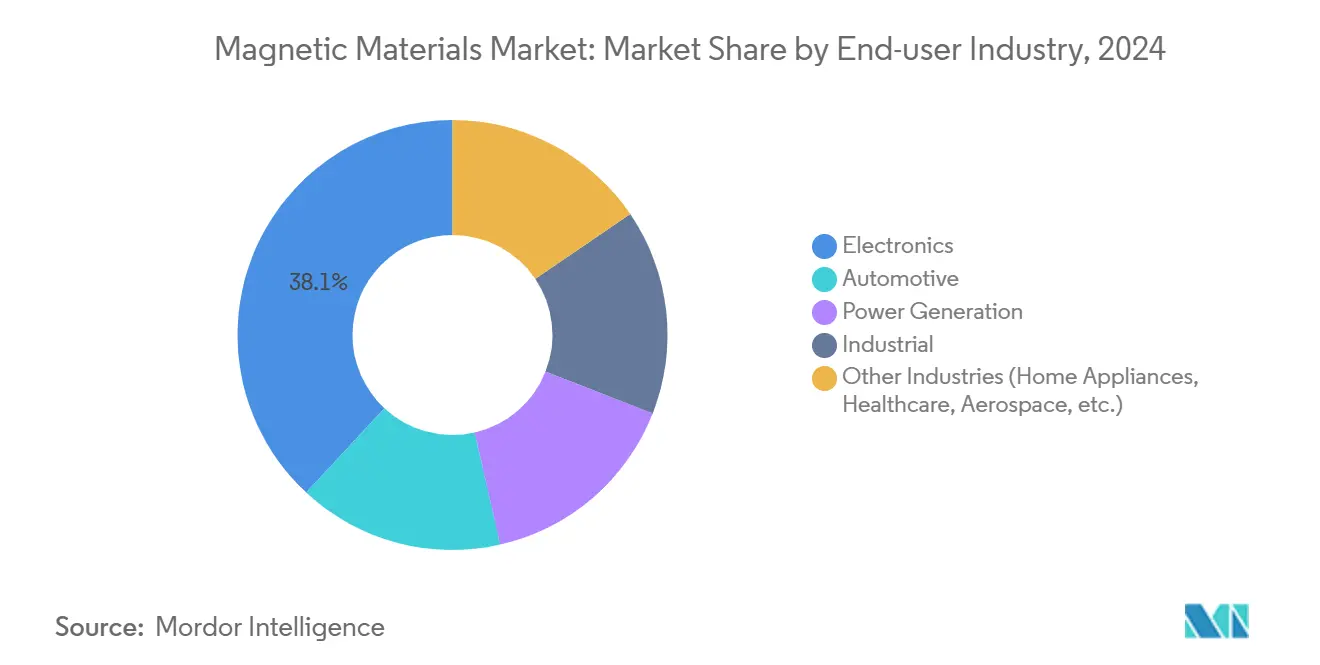
Note: Segment shares of all individual segments available upon report purchase
By Application: Electric Motors Anchor Demand across Sectors
Electric motors and generators accounted for 39.48% of magnetic materials market size in 2024, with growth of 6.55% CAGR through 2030 as axial-flux topologies enter passenger cars, drones, and industrial drives. High-power-density motors employ segmented NdFeB rings that reduce eddy currents, while liquid-cooled stators permit higher continuous torque. Transformer and inductor applications remain integral, driven by grid modernization and proliferation of data-center UPS systems. Sensor and actuator deployments climb in ADAS modules, robotic grippers, and pneumatically-coupled medical devices.
Magnetic storage is transitioning toward spin-transfer torque MRAM, where perpendicular anisotropy stacks deliver endurance beyond 10¹⁵ write cycles, creating niche magnet needs in semiconductor fabs. Emerging uses in magnetic refrigeration exploit regenerative magnetocaloric cycles that promise 20% efficiency gains over vapor-compression chillers, presenting a new frontier for the magnetic materials market.
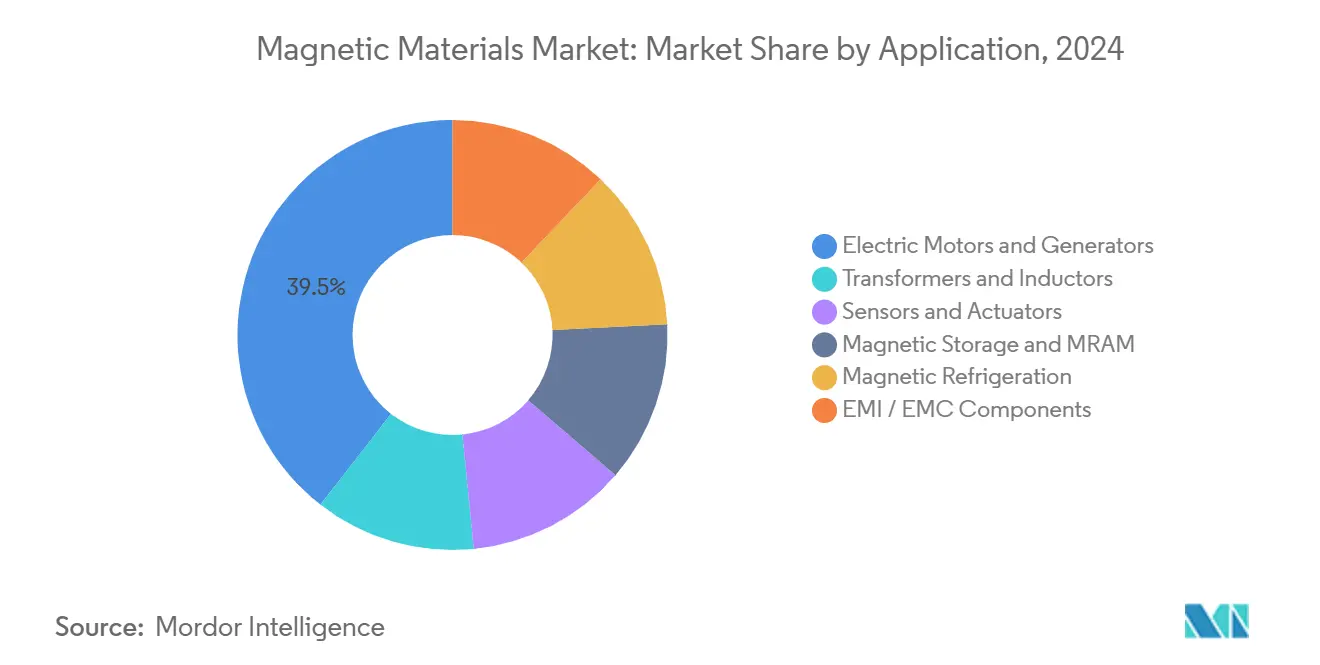
Note: Segment shares of all individual segments available upon report purchase
Geography Analysis
Asia-Pacific retained 67.12% of global demand in 2024 and is expected to grow at 7.71% CAGR through 2030. China extracts most of the world’s bastnaesite and monazite ores and refines nearly 90% of rare earth oxides, anchoring an end-to-end supply chain from mine to sintered magnet. Provincial incentives in Baotou and Ganzhou subsidize new strip-casting and powder-alignment lines, reinforcing regional dominance. Japan and South Korea focus on high-tolerance machining and coating processes that meet stringent electronics and automotive specifications, while India expands ferrite capacity to serve domestic white-goods plants.
North America holds a solid foothold as defense and aerospace demand secure long-term offtake contracts. The U.S. Department of Energy funds pilot programs in Utah and California to extract critical minerals from coal ash and electronic scrap, aiming to diversify inputs. MP Materials’ vertically integrated complex in Texas will deliver 1,000 tonnes of magnet precursor by late 2025, advancing ambitions for a continental supply chain. Canada leverages nickel and cobalt deposits to supply alloying elements for SmCo and AlNiCo magnets.
European policy centers on sustainability and resilience. The Critical Raw Materials Act, in force since May 2024, mandates that 40% of annual processing volume be sourced within the bloc by 2030, triggering brown-field expansions in Estonia and Germany[2]European Parliament, “Critical Raw Materials Act,” europarl.europa.eu . Consortia such as REFLUX focus on hydrometallurgical recycling routes that lower carbon intensity relative to primary mining. Outside the three core regions, Latin America scales magnet consumption in wind-energy corridors of Brazil and Chile, whereas Gulf Cooperation Council economies integrate high-capacity desalination motors rich in ferrite and soft magnetic composites.
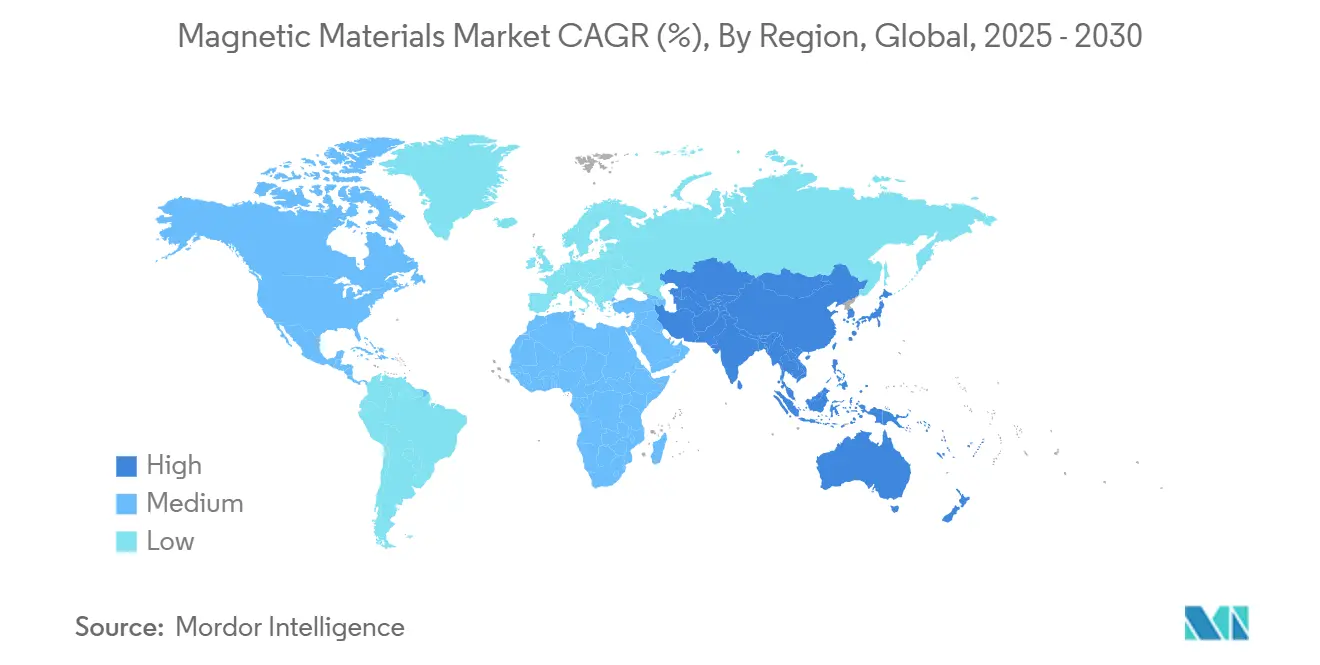
Competitive Landscape
The magnetic materials market is moderately fragmented, with at least 150 producers worldwide ranging from diversified metal majors to niche powder specialists. Chinese firms—Inner Mongolia Baotou Steel, JL MAG, and Yantai Zhenghai—leverage captive rare earth feedstock to hold cost leadership in sintered NdFeB. Non-Chinese players prioritize supply security: Neo Performance Materials inaugurated a 2,000 tonne sintered magnet plant in Estonia in April 2025, expandable to 5,000 tonnes, to service European automotive lines[3]Neo Performance Materials, “Sustainability Report 2023,” neomaterials.com .
Strategic alliances are reshaping the value chain. Technology differentiation intensifies: Niron Magnetics pilots iron-nitride powders achieving 150 MGOe maximum energy product without rare earths, while Magna develops bonded magnets optimized for axial-flux motors. Artificial-intelligence platforms screen millions of compositions, shaving years off discovery cycles and opening avenues for altermagnetic and quasicrystalline phases.
Capital investments center on powder-production upgrades, grain-boundary diffusion ovens, and strip-casting lines that lift throughput by 30%. Downstream integrators in robotics and medical imaging increasingly co-locate with magnet suppliers to shorten lead times and collaborate on application-specific grades. This convergence of resources, IP, and processing independence defines the next phase of competition within the magnetic materials market.
Magnetic Materials Industry Leaders
-
Arnold Magnetic Technologies
-
Daido Steel Co., Ltd.
-
Proterial, Ltd.
-
Shin-Etsu Chemical Co., Ltd.
-
TDK Corporation
- *Disclaimer: Major Players sorted in no particular order
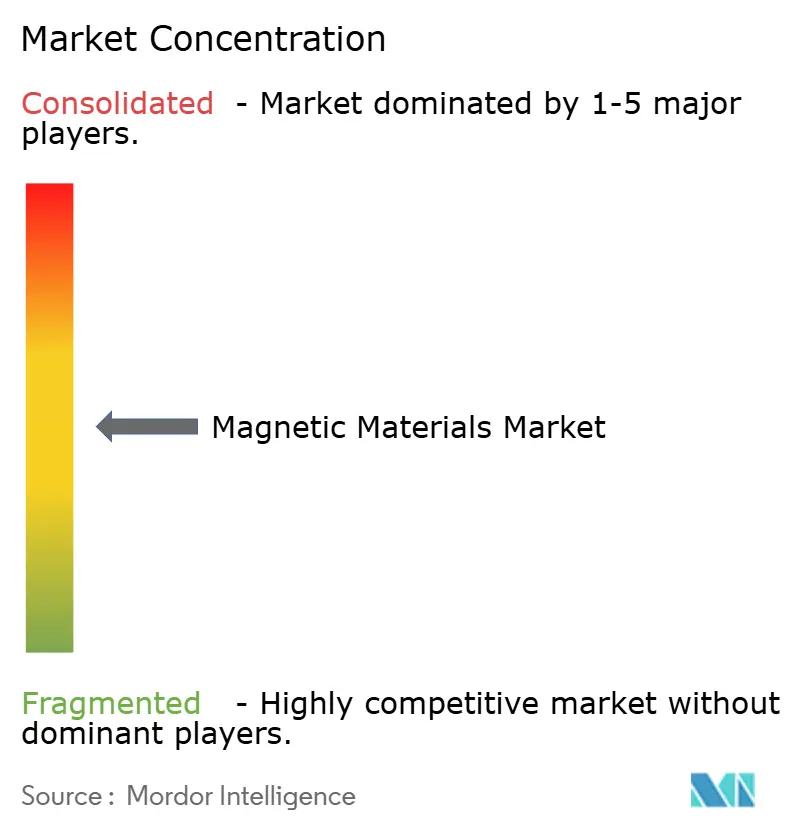
Recent Industry Developments
- April 2025: Neo Performance Materials (NEO), has initiated production at its sintered rare earth magnet facility in Estonia, with an annual capacity of 2,000 tonnes. This development is expected to strengthen the supply chain and drive growth in the magnetic materials market.
- January 2025: Arnold Magnetic Technologies has established a new manufacturing facility in Thailand to enhance the production capacity of high-reliability magnetic components. This expansion is expected to strengthen the company's position and drive growth in the magnetic materials market.
Global Magnetic Materials Market Report Scope
Magnetic materials are capable of attracting and repelling other materials, such as steel or iron. Magnetic materials are widely used in transformers, generators, and motors.
The magnetic materials market is segmented by type, end-user industry, and geography. Based on type, the market is segmented into hard magnetic materials, soft magnetic materials, and semi-hard magnetic materials. Based on the end-user industry, the market is segmented into automotive, electronics, power generation, industrial, and other end-user industries (consumer goods, communication and technology, etc.).
The report also covers the market size and forecasts for magnetic materials in 15 countries across major regions. Each segment's market sizing and forecasts are based on volume (tons).
By Type | Hard / Permanent Magnetic Materials | ||
Soft Magnetic Materials | |||
Semi-Hard Magnetic Materials | |||
By Material | Ferrite | ||
Neodymium-Iron-Boron (NdFeB) | |||
Samarium-Cobalt (SmCo) | |||
Aluminum-Nickel-Cobalt (AlNiCo) | |||
Other Materials (Electrical Steel (GO and NGO), Nanocrystalline and Amorphous Alloys) | |||
By End-user Industry | Automotive | ||
Electronics | |||
Power Generation | |||
Industrial | |||
Other Industries (Home Appliances, Healthcare, Aerospace, etc.) | |||
By Application | Electric Motors and Generators | ||
Transformers and Inductors | |||
Sensors and Actuators | |||
Magnetic Storage and MRAM | |||
Magnetic Refrigeration | |||
EMI / EMC Components | |||
By Geography | Asia-Pacific | China | |
Japan | |||
India | |||
South Korea | |||
Rest of Asia-Pacific | |||
North America | United States | ||
Canada | |||
Mexico | |||
Europe | Germany | ||
United Kingdom | |||
France | |||
Italy | |||
Rest of Europe | |||
South America | Brazil | ||
Argentina | |||
Rest of South America | |||
Middle East and Africa | Saudi Arabia | ||
South Africa | |||
Rest of Middle East and Africa |
Hard / Permanent Magnetic Materials |
Soft Magnetic Materials |
Semi-Hard Magnetic Materials |
Ferrite |
Neodymium-Iron-Boron (NdFeB) |
Samarium-Cobalt (SmCo) |
Aluminum-Nickel-Cobalt (AlNiCo) |
Other Materials (Electrical Steel (GO and NGO), Nanocrystalline and Amorphous Alloys) |
Automotive |
Electronics |
Power Generation |
Industrial |
Other Industries (Home Appliances, Healthcare, Aerospace, etc.) |
Electric Motors and Generators |
Transformers and Inductors |
Sensors and Actuators |
Magnetic Storage and MRAM |
Magnetic Refrigeration |
EMI / EMC Components |
Asia-Pacific | China |
Japan | |
India | |
South Korea | |
Rest of Asia-Pacific | |
North America | United States |
Canada | |
Mexico | |
Europe | Germany |
United Kingdom | |
France | |
Italy | |
Rest of Europe | |
South America | Brazil |
Argentina | |
Rest of South America | |
Middle East and Africa | Saudi Arabia |
South Africa | |
Rest of Middle East and Africa |
Key Questions Answered in the Report
What is the current size of the magnetic materials market?
The magnetic materials market stands at 33.01 million tons in 2025 and is forecast to reach 44.32 million tons by 2030.
Which region dominates demand?
Asia-Pacific leads with 67.12% share in 2024 and is also the fastest-growing region at 7.71% CAGR through 2030.
Which material type is growing the fastest?
Ferrite magnets show the highest projected growth at 6.20% CAGR between 2025-2030 due to cost advantages and improved performance.
How do electric vehicles influence magnet demand?
Each EV uses 2-5 kg of NdFeB magnets; rising EV adoption contributes a +1.8 percentage-point uplift to overall market CAGR.
Are rare earth-free magnets commercially viable?
Pilot projects by firms like Niron Magnetics demonstrate iron-nitride magnets approaching 150 MGOe, though large-scale production is expected beyond 2027.
What is the environmental challenge in magnet production?
High-temperature ferrite sintering emits significant CO₂; stricter EU regulations are adding up to 20% to production costs, spurring investment in low-temperature processes and recycling.
Page last updated on: July 1, 2025