Investment Casting Market Size
Investment Casting Market Analysis
The Investment Casting Market is expected to register a CAGR of 4.58% during the forecast period.
The global investment casting industry continues to evolve with significant technological advancements and shifting manufacturing dynamics. Currently, there are over 1,400 investment casting foundries worldwide, with Asia-Pacific housing approximately 70% of these facilities, highlighting the region's dominant role in global production capacity. Western manufacturers are increasingly focusing on high-value-added products like aerospace components and industrial machinery, while eastern regions maintain their stronghold in automotive applications. The integration of advanced technologies like augmented reality and 3D printing for wax pattern production is revolutionizing traditional metal casting processes, enabling more complex designs and improved precision.
Cost considerations and process efficiency remain central to the industry's development. The traditional water glass investment casting process, costing approximately 2.50 USD/kg, continues to be preferred for mass production compared to the more precise but expensive silica sol process at 6.5 USD/kg. Foundries are increasingly investing in automation and digital simulation technologies to optimize production efficiency and reduce operational costs. The investment casting industry is witnessing a gradual shift toward more sustainable and energy-efficient manufacturing processes, with companies implementing advanced melting technologies and recycling systems to minimize environmental impact.
The automotive sector represents a significant market for investment casting, with the casting industry supplying approximately 80% of components used in vehicle manufacturing, of which investment casting accounts for 10-15% of the parts in a typical vehicle. This substantial integration into automotive supply chains has driven foundries to develop specialized capabilities for producing complex, lightweight components that support vehicle efficiency and performance requirements. The industry is also experiencing growing demand from emerging applications in electric vehicles, particularly for battery housing components and high-voltage connectors.
Industry consolidation and capacity expansion continue to reshape the competitive landscape. Major manufacturers are pursuing strategic expansions to enhance their global presence and technological capabilities. Notable developments include Impro Group's significant investment in their San Luis Potosi Campus, which encompasses five different production facilities and technologies. Companies are increasingly focusing on vertical integration and expanding their value-added services, including machining, heat treatment, and surface finishing capabilities, to provide comprehensive solutions to their customers. This trend toward consolidated manufacturing capabilities is enabling producers to better serve diverse industry requirements while maintaining quality control throughout the production process.
Investment Casting Market Trends
Growing Aerospace & Defense Manufacturing
The aerospace and defense sector continues to be a primary driver for the investment casting market, with major manufacturers expanding their production capabilities. This is evidenced by significant infrastructure developments, such as Pratt & Whitney's new turbine airfoil facility established in 2022 with an investment of USD 650 million, which features an advanced casting foundry. The facility's establishment demonstrates the increasing demand for precision components in aircraft engine manufacturing, particularly for critical components like turbine blade casting and vanes that require exceptional dimensional accuracy and performance characteristics.
The military aerospace sector particularly drives demand through programs requiring high-precision components manufactured through aerospace casting. The presence of major defense manufacturers and their ongoing projects necessitates sophisticated casting capabilities for producing complex geometries with superior surface finish and tight tolerances. Investment casting's ability to produce components with intricate internal passages and complex external features makes it particularly valuable for aerospace applications, where component weight reduction and performance optimization are crucial considerations.
Technological Advancements in Casting Processes
The evolution of casting technologies, particularly in silica sol and sodium silicate processes, is driving market growth by enabling manufacturers to meet increasingly demanding specifications. The silica sol process has established itself as the premium choice for applications requiring superior dimensional accuracy and minimal defects, despite its higher cost of approximately 6.5 USD/kg for automotive and industrial components. This process's capability to produce both extra-large parts weighing 50-100kg and precise small components between 2-1000g demonstrates its versatility in meeting diverse manufacturing requirements.
Continuous improvements in the sodium silicate process are expanding its adoption, particularly in regions seeking cost-effective solutions without significantly compromising quality. The ongoing technological developments in this process have enhanced its capability to produce components with improved dimensional accuracy and surface finish, making it increasingly competitive with more expensive alternatives. These advancements are particularly significant for manufacturers looking to optimize their production costs while maintaining acceptable quality standards for various industrial applications.
Expanding Industrial Applications
The versatility of industrial casting in producing complex components for various industrial applications continues to drive market growth. The process's ability to manufacture critical components like water pumps, impellers, diversion shells, pump bodies, and valve plates demonstrates its essential role in industrial machinery manufacturing. The capability to produce both large-scale industrial components and precision small parts makes investment casting increasingly valuable across diverse industrial sectors.
The adoption of investment casting in specialized industrial applications is further driven by its ability to work with a wide range of materials and produce components with complex geometries that would be difficult or impossible to manufacture through other methods. This is particularly important in applications requiring high-performance materials and precise specifications, such as industrial gas turbines, power generation equipment, and high-pressure valve systems. The process's ability to maintain tight tolerances while producing complex shapes makes it indispensable for manufacturers seeking to optimize component performance and reliability.
Segment Analysis: By Type
Sodium Silicate Process Segment in Investment Casting Market
The Sodium Silicate Process, also known as water glass casting, dominates the investment casting market with approximately 73% market share in 2024. This process has maintained its leadership position due to its lower production costs compared to alternative methods, making it particularly attractive for mass production applications. The segment's prominence is especially notable in countries like China and Russia, where more than three-quarters of foundries focus on water glass casting operations. The process is particularly well-suited for manufacturing heavier or stronger complex shapes, with capabilities to produce castings ranging from 0.5 kg to 60 kg. Major applications include the production of trailers, agricultural machinery, and components for the offshore industry. The segment's cost-effectiveness, with water glass investment casting components averaging around 2.50 USD/kg, combined with its shortest production cycle and excellent shelling performance, continues to drive its widespread adoption across various industrial applications.
Tetraethyl Orthosilicate Process Segment in Investment Casting Market
The Tetraethyl Orthosilicate (TEOS) or Silica Sol Process segment represents a premium segment in the investment casting market, characterized by its superior dimensional accuracy and surface finish capabilities with minimal defects. Despite its higher costs, averaging around 6.5 USD/kg for automotive or industrial components, this process maintains significant importance in applications requiring the highest precision and quality standards. The process demonstrates particular strength in producing extra-large parts weighing 50-100 kg, such as water pumps, impellers, diversion shells, pump bodies, ball valve bodies, and valve plates. Simultaneously, it excels in manufacturing extra-small parts (2-1000 g) that demand high dimensional accuracy, particularly in electronics applications. The segment maintains a stronger presence in regions like North America and Europe, where quality and precision requirements often outweigh cost considerations.
Segment Analysis: By End User Type
Aerospace and Military Segment in Investment Casting Market
The aerospace and military segment maintains its dominant position in the global investment casting market, commanding approximately 26% market share in 2024. This leadership position is primarily driven by the extensive use of precision casting in manufacturing critical components for aircraft engines, structural parts, and military equipment. The segment's strength is reinforced by the increasing demand for fuel-efficient aircraft, the growing commercial aviation sector, and sustained military modernization programs worldwide. Investment casting's ability to produce complex geometries with high precision and superior surface finish makes it particularly valuable for aerospace applications, where components must meet stringent quality and performance requirements. The segment's robust performance is further supported by major aircraft manufacturers ramping up production to meet their substantial order backlogs and the increasing adoption of advanced materials in aerospace applications.
Medical Segment in Investment Casting Market
The medical segment is emerging as one of the most dynamic sectors in the investment casting market, projected to grow at approximately 5% during 2024-2029. This growth is primarily driven by the increasing demand for precision medical devices, surgical instruments, and orthopedic implants. The segment's expansion is fueled by aging populations worldwide, growing healthcare infrastructure in developing nations, and technological advancements in medical procedures. Investment casting's ability to produce complex, biocompatible components with excellent surface finish makes it particularly suitable for medical applications. The segment is witnessing increased adoption in manufacturing various medical equipment components, from surgical tools to diagnostic equipment parts, supported by stringent quality requirements and the need for precise, reliable medical devices.
Remaining Segments in Investment Casting Market by End User Type
The automotive and general industrial casting machinery segments continue to play vital roles in shaping the investment casting market landscape. The automotive sector leverages investment casting for producing complex engine components, turbocharger parts, and various structural elements, particularly as vehicles become more sophisticated and efficiency-focused. The general industrial machinery segment utilizes investment casting for manufacturing precision components used in pumps, valves, and various industrial equipment. These segments benefit from ongoing industrialization, technological advancements, and the increasing demand for high-performance components across various industrial applications. The versatility of investment casting in producing complex shapes with tight tolerances continues to make it an essential manufacturing process across these diverse end-user segments.
Investment Casting Market Geography Segment Analysis
Investment Casting Market in North America
North America represents a crucial investment casting market, driven by its robust aerospace, automotive, and medical device manufacturing sectors. The United States dominates the regional landscape, followed by Canada, with both countries demonstrating strong technological capabilities in precision casting. The region's market is characterized by high-value applications, particularly in aerospace components and industrial gas turbines, where quality and precision requirements are stringent. Advanced manufacturing facilities and a strong focus on research and development have helped maintain North America's competitive edge in investment casting industry technology.
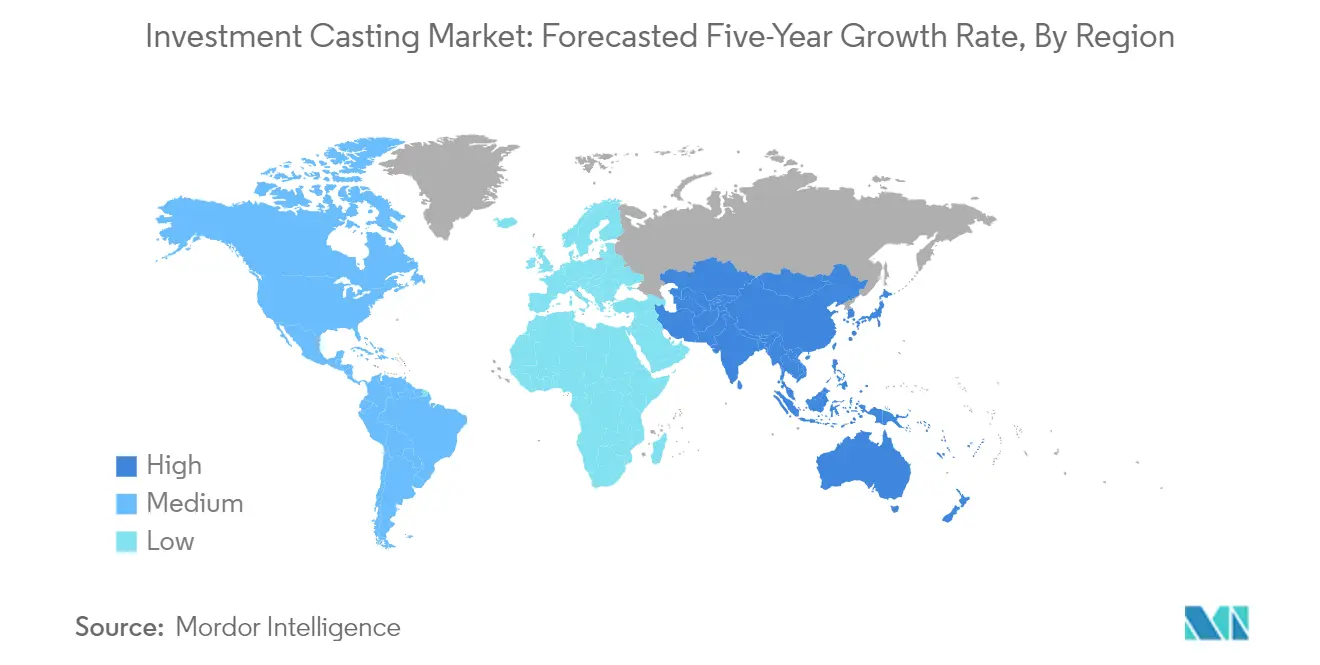
Investment Casting Market in United States
The United States leads the North American investment casting market with its extensive aerospace manufacturing base and advanced medical device industry. The country hosts production plants for major aircraft programs and has a thriving defense sector that generates consistent demand for investment cast components. The presence of key manufacturers like Precision Castparts Corp and MetalTek International has strengthened the country's position in the global metal casting market. The US market accounts for approximately 96% of North America's investment casting revenue in 2024, highlighting its dominant position in the region.
Investment Casting Market in Canada
Canada demonstrates promising growth potential in the investment casting market with an expected growth rate of approximately 4% during 2024-2029. The country's automotive sector, which serves as an assembly hub for major OEMs like Fiat Chrysler, Ford, GM, Honda, and Toyota, drives significant demand for investment cast components. Canada's aerospace industry, supported by companies like Airbus, Boeing, and Bombardier, further contributes to market growth. The country's focus on expanding its manufacturing capabilities and increasing parts production has positioned it as an emerging player in the North American foundry market.
Investment Casting Market in Europe
Europe maintains a strong position in the global investment casting industry, supported by its advanced manufacturing capabilities and diverse industrial base. The region's market is led by the United Kingdom, followed by Germany, France, and Spain, each contributing significantly to the overall market value. European manufacturers are particularly known for their expertise in producing high-precision components for the aerospace, automotive, and medical sectors. The region's focus on technological innovation and quality standards has helped maintain its competitive position in the global market.
Investment Casting Market in United Kingdom
The United Kingdom leads the European investment casting market with its strong aerospace and automotive manufacturing sectors. The country's premium and sports car manufacturers, including Aston Martin, Bentley, Jaguar, and Rolls-Royce, generate substantial demand for precision cast components. The presence of major aerospace companies and defense manufacturers further strengthens the market position. The UK accounts for approximately 18% of Europe's investment casting revenue in 2024, making it the largest market in the region.
Investment Casting Market in United Kingdom
The United Kingdom also demonstrates the highest growth potential in the European region, with a projected growth rate of approximately 4.5% during 2024-2029. The country's ongoing investments in aerospace manufacturing facilities and the expansion of its defense manufacturing capabilities drive this growth. The development of new manufacturing technologies and the increasing adoption of investment casting in emerging applications contribute to the market's positive outlook.
Investment Casting Market in Asia-Pacific
The Asia-Pacific region represents a dynamic investment casting market, characterized by rapid industrialization and expanding manufacturing capabilities. China leads the regional market, followed by India, Japan, and South Korea. The region's growth is driven by increasing automotive production, expanding aerospace industry, and growing industrial machinery sector. The presence of numerous investment casting companies and ongoing technological advancements has established Asia-Pacific as a major hub for investment casting production.
Investment Casting Market in China
China dominates the Asia-Pacific investment casting market with its extensive manufacturing infrastructure and diverse industrial base. The country's robust automotive sector, developing aerospace industry, and expanding industrial machinery sector drive substantial demand for investment cast components. China's strategic focus on improving product quality and technological capabilities, supported by initiatives like 'Made in China 2025', has strengthened its position as the regional market leader.
Investment Casting Market in India
India emerges as the fastest-growing market in the Asia-Pacific region, driven by its expanding automotive sector, growing aerospace industry, and increasing industrial manufacturing activities. The country's focus on developing end-to-end aerospace solutions and the government's support through initiatives like 'Make in India' create favorable conditions for market growth. The ongoing expansion of manufacturing capabilities and increasing adoption of advanced technologies position India as a key growth market in the region.
Investment Casting Market in Rest of the World
The Rest of the World region, encompassing countries in Latin America and the Middle East, presents diverse opportunities in the foundry industry. This region includes key markets such as Brazil, Argentina, Mexico, and the United Arab Emirates. Mexico emerges as both the largest and fastest-growing market in this region, driven by its strong automotive manufacturing base and expanding aerospace sector. The region's growth is supported by increasing industrialization, rising automotive production, and growing investments in manufacturing capabilities across various sectors.
Investment Casting Industry Overview
Top Companies in Investment Casting Market
The investment casting market features prominent players like Georg Fischer Ltd, Zollern GmbH, Precision Castparts Corp, and Impro Precision Industries Limited leading the industry through continuous innovation and strategic expansion. Companies are increasingly focusing on technological integration, incorporating advanced automation, 3D printing, and digital solutions to enhance precision and reduce lead times. The industry witnesses ongoing investments in research and development, particularly in areas of material science and process optimization, with companies developing proprietary technologies for competitive advantage. Strategic moves include geographical expansion through new facility establishments and acquisitions, particularly in emerging markets, while operational agility is being achieved through the implementation of smart manufacturing processes and Industry 4.0 initiatives. Market leaders are also emphasizing sustainability and energy efficiency in their operations while expanding their product portfolios to serve diverse end-user industries from aerospace to medical devices.
Fragmented Market with Regional Player Dominance
The investment casting market exhibits a highly fragmented structure, with regional players commanding over eighty percent of the market share, particularly in Asia-Pacific where more than seventy percent of global foundries are located. Western manufacturers, particularly in North America and Europe, dominate the high-value segments such as aerospace and industrial machinery, while Eastern players lead in automotive and general industrial applications. The market demonstrates a clear geographical specialization, with Chinese foundries focusing on automotive and aerospace sectors, Japanese manufacturers specializing in turbochargers and biomedical applications, and Korean facilities concentrating on industrial and automotive components.
The industry's consolidation pattern shows interesting dynamics, with larger conglomerates pursuing strategic acquisitions to expand their global footprint and technological capabilities, while specialized regional players maintain their stronghold through deep local market knowledge and customer relationships. Merger and acquisition activities are primarily driven by the need to access new markets, acquire technological capabilities, and achieve operational synergies. Companies are increasingly forming strategic partnerships and joint ventures to combine their strengths in serving specific industry segments or geographical markets, while maintaining their individual expertise and market positions.
Innovation and Adaptability Drive Future Success
Success in the metal casting industry increasingly depends on companies' ability to adapt to evolving industry demands while maintaining technological leadership and operational efficiency. Market players must focus on developing advanced materials and processes to meet the stringent requirements of high-growth sectors like aerospace and medical devices. Companies need to invest in digital transformation initiatives, including automation and smart manufacturing capabilities, while building robust quality management systems to maintain competitive advantage. The ability to offer customized solutions, reduce lead times, and provide value-added services will become crucial differentiators in the market.
Future market dynamics will be shaped by the increasing focus on sustainable manufacturing practices and the ability to serve emerging application areas. Companies must develop strategies to address the growing demand for lightweight components in automotive and aerospace sectors while managing the substitution risks from alternative manufacturing technologies like additive manufacturing. Success will also depend on building strong relationships with key end-users, particularly in industries with high entry barriers and specific certification requirements. Regulatory compliance, particularly in environmental and quality standards, will continue to influence market participation and success, making it essential for companies to maintain robust compliance frameworks and certification programs.
Investment Casting Market Leaders
-
Signicast
-
MetalTek International
-
Precision Castparts Corp.
-
Georg Fischer Ltd
-
Milwaukee Precision Casting Inc.
- *Disclaimer: Major Players sorted in no particular order
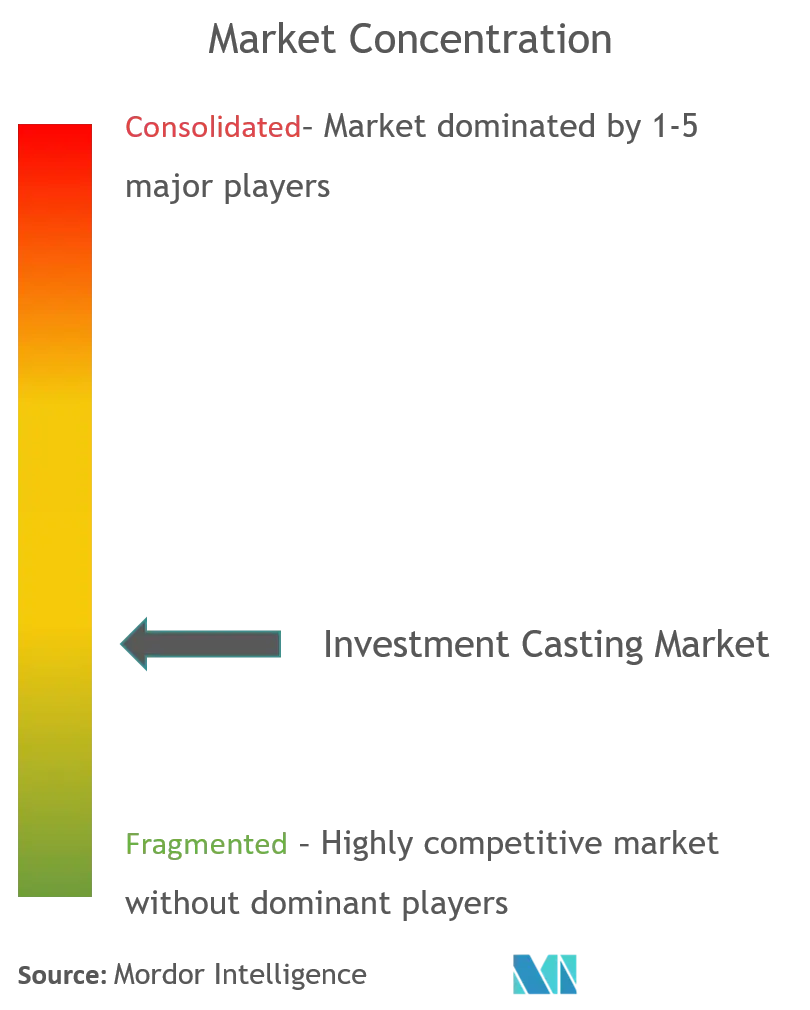
Investment Casting Market News
In October 2022, Winsert which is the advanced manufacturer of the critical metal parts announced the acquisition of Alloy Cast Products Inc. which is the investment casting mand machining company. The acquisition will allow the mutual growth of both companies and would tap inexplored product segments in their coming tenure.
In August 2022, TriTech Titanium Parts which is the spin-off company formed after AmeriTi Manufacturing launched its Detroit-based titanium parts for various markets. The company uses metal injection, 3-D binder jet printing, and investment casting technology for producing the products. The company offers these titanium products for industrial, aerospace, automotive, and medical applications.
Investment Casting Industry Segmentation
Investment casting which is also considered as the precising and low wax casting. It ias the manufacturing process under which the wax is utilized to take the shape of disposable ceramic molds.
The Investment Casting Market is Segmented By Type (Sodium Silicate Process, Tetraethyl Orthosilicate/ Silica Sol Process), End-user Type (Automotive, Aerospace and Military, General Industrial Machinery, Medical, and Other End User Types), and Geography(North America, Europe, Asia-Pacific, and Rest of the World).
By Type | Sodium Silicate Process | ||
Tetraethyl Orthosilicate/Silica Sol Process | |||
By End-user Type | Automotive | ||
Aerospace and Military | |||
General Industrial Machinery | |||
Medical | |||
Other End-user Types | |||
By Geography | North America | United States | |
Canada | |||
Rest of North America | |||
Europe | Germany | ||
United Kingdom | |||
France | |||
Spain | |||
Rest of Europe | |||
Asia-Pacific | India | ||
China | |||
Japan | |||
South Korea | |||
Rest of Asia-Pacific | |||
Rest of the World | Brazil | ||
Argentina | |||
Mexico | |||
United Arab Emirates | |||
Other Countries |
Sodium Silicate Process |
Tetraethyl Orthosilicate/Silica Sol Process |
Automotive |
Aerospace and Military |
General Industrial Machinery |
Medical |
Other End-user Types |
North America | United States |
Canada | |
Rest of North America | |
Europe | Germany |
United Kingdom | |
France | |
Spain | |
Rest of Europe | |
Asia-Pacific | India |
China | |
Japan | |
South Korea | |
Rest of Asia-Pacific | |
Rest of the World | Brazil |
Argentina | |
Mexico | |
United Arab Emirates | |
Other Countries |
Investment Casting Market Research FAQs
What is the current Investment Casting Market size?
The Investment Casting Market is projected to register a CAGR of 4.58% during the forecast period (2025-2030)
Who are the key players in Investment Casting Market?
Signicast, MetalTek International, Precision Castparts Corp., Georg Fischer Ltd and Milwaukee Precision Casting Inc. are the major companies operating in the Investment Casting Market.
Which is the fastest growing region in Investment Casting Market?
Asia Pacific is estimated to grow at the highest CAGR over the forecast period (2025-2030).
Which region has the biggest share in Investment Casting Market?
In 2025, the North America accounts for the largest market share in Investment Casting Market.
What years does this Investment Casting Market cover?
The report covers the Investment Casting Market historical market size for years: 2020, 2021, 2022, 2023 and 2024. The report also forecasts the Investment Casting Market size for years: 2025, 2026, 2027, 2028, 2029 and 2030.