India Prefabricated Buildings Market Analysis
The India Prefabricated Buildings Market size is estimated at USD 15.07 billion in 2025, and is expected to reach USD 23.13 billion by 2030, at a CAGR of 8.95% during the forecast period (2025-2030).
India's construction landscape is undergoing a dramatic transformation driven by rapid urbanization and evolving infrastructure needs. According to United Nations projections, India is expected to add 404 million urban residents by 2050, creating unprecedented pressure on housing and infrastructure development. This massive urbanization wave is compelling developers and construction companies to adopt innovative modular construction solutions that can deliver projects faster and more efficiently. The government's ambitious infrastructure development plans, including a USD 1.4 trillion investment under the National Infrastructure Pipeline (NIP), are further accelerating the adoption of prefabricated buildings technologies.
The commercial and industrial sectors are emerging as major growth drivers for prefabricated buildings, particularly in warehouse and logistics infrastructure. In November 2023, EPACK Prefab announced the successful construction of 10 million square feet of industrial and warehouse buildings, demonstrating the growing acceptance of prefabricated commercial buildings solutions in the commercial sector. The rapid expansion of e-commerce and retail sectors, especially in tier 2 and tier 3 cities, has created substantial demand for specialized industrial warehouses, with major development activities concentrated in southern states like Karnataka, Tamil Nadu, and Maharashtra.
Technological advancement and innovation in offsite construction methods are revolutionizing the construction industry. A prime example is the ongoing construction of Asia's largest precast development in Hyderabad - the My Home GRAVA project, spanning 3.7 million square meters, which showcases the capability of offsite construction technology in delivering large-scale commercial projects. The project, comprising eight high-rise commercial towers, represents a significant shift towards factory-made building components, with the first two towers scheduled for completion by 2024. This development is setting new benchmarks for prefabricated construction in terms of scale, efficiency, and quality.
The industry is witnessing a notable shift towards sustainable and green building practices through prefabrication. Major players like Nest-In from Tata Steel are introducing innovative prefabricated solutions that demonstrate significant environmental benefits. Recent studies conducted on their HabiNest building showed remarkable sustainability metrics, including 48% lower freshwater requirements, 26% reduced global warming potential, and 30% reduction in primary energy demand compared to conventional construction. These environmental advantages, coupled with the government's push for sustainable construction practices, are positioning prefabricated buildings as a key solution for India's future construction needs.
India Prefabricated Buildings Market Trends
Government Initiatives for Affordable Housing
The Indian government's ambitious housing initiatives have become a major catalyst for the prefabricated housing market. The Pradhan Mantri Awas Yojana (PMAY) scheme, which aims to provide housing for all by 2024, has created massive opportunities for prefabricated construction, as approximately 96% of the 18.78 million dwelling units belong to Economically Weaker Section (EWS) and Low Income Group (LIG) households. The implementation of affordable housing support policies has created significant market potential for prefabricated homes, as they offer cost savings of up to 50% compared to traditional construction methods, with prefab houses typically costing between INR 700-1500 per square foot versus INR 1500-2500 per square foot for conventional construction.
The government's commitment is further demonstrated through various other schemes like Rajiv Awas Yojana (RAY), Jawaharlal Nehru National Urban Renewal Mission (JNNURM), and Credit-Linked Subsidy Scheme (CLSS). These initiatives are supported by the Ministry of Housing and Urban Affairs' implementation of lighthouse projects across different states, showcasing various prefabrication technologies. For instance, the Light House Projects under the Global Housing Technology Challenge demonstrate successful implementation of different prefab technologies, such as Precast Concrete Construction in Chennai and Light Gauge Steel Structural Systems in Agartala, proving the viability and efficiency of prefabricated construction methods.
Rapid Urbanization and Infrastructure Development
India's accelerating urbanization is creating unprecedented demand for quick and efficient construction solutions, with projections indicating that the urban population will contribute 75% of GDP by 2025, up from 63% currently. The number of cities with populations exceeding one million is expected to increase from 42 in 2021 to 68 by 2025, creating massive pressure for rapid infrastructure development. This urban expansion is supported by the National Infrastructure Pipeline (NIP) with a substantial investment budget of USD 1.4 trillion, allocating significant portions to renewable energy (24%), roads and highways (19%), urban infrastructure (16%), and railways (13%).
The scale of infrastructure development is further amplified by technology-driven urban planning initiatives like the Smart City Mission, targeting 100 cities. Modular buildings, despite currently accounting for only 2% of India's USD 500 million construction market, are increasingly being recognized as a crucial solution for meeting these rapid development needs. The ability of prefabricated homes to reduce project timelines by up to 50% compared to traditional methods makes them particularly attractive for urban infrastructure projects, where speed of execution is critical. This is evidenced by successful implementations in various infrastructure projects, including metro stations, bridges, and commercial complexes across major urban centers.
E-commerce and Retail Sector Growth
The explosive growth of India's e-commerce sector is driving substantial demand for manufactured homes, particularly in warehouse and logistics infrastructure. The e-commerce revenue is projected to reach USD 188 billion by 2025, creating an urgent need for rapid warehouse expansion, especially in tier 2 and tier 3 cities. This growth has led to companies adopting prefabricated structures as their preferred choice for warehouse construction, as they offer up to 50% reduction in construction time compared to traditional methods, enabling faster operational readiness and quicker market entry.
The impact of this trend is evident in recent industry developments, such as EPACK Prefab's successful construction of 10 million square feet of industrial and warehouse buildings as of November 2023. Major companies like Coca-Cola, JK Tyre, GAIL, and Dalmia Cement have opted for prefabricated solutions for their warehouse requirements, particularly in southern India where cities like Bengaluru, Chennai, and Mumbai are experiencing significant warehouse construction activity. The streamlined construction process and modular nature of modular buildings align perfectly with the rapid expansion needs of e-commerce companies, making them an increasingly popular choice for modern retail and logistics infrastructure development.
Segment Analysis: By Material Type
Concrete Segment in India Prefabricated Buildings Market
The concrete segment continues to dominate the India prefabricated buildings market, holding approximately 53% market share in 2024. This significant market position is driven by the increasing adoption of prefabricated concrete buildings technology across various construction projects, particularly in affordable housing initiatives. The segment's strength is further reinforced by major developers like Janapriya Developers, Aurobindo Realty, and My Home Constructions setting up their own precast factories to meet delivery requirements with less dependency on labor. The government's emphasis on using precast construction technology for faster delivery of structures, particularly in projects by organizations like DRDO and the MES Department, has also contributed to concrete's market leadership. Additionally, state governments, including Telangana, have been actively promoting precast construction technology for affordable housing and institutional buildings, further cementing concrete's position as the preferred material in prefabricated construction.
Glass Segment in India Prefabricated Buildings Market
The glass segment is emerging as the fastest-growing segment in the prefabricated buildings market, with a projected growth rate of approximately 11% during 2024-2029. This remarkable growth is primarily driven by the increasing adoption of glass in modern architectural designs, particularly in metros and IT parks across India. The segment's growth is supported by the material's multiple advantages, including high insulating properties, strength, durability, fire resistance, weather resistance, and chemical resistance. The trend toward sustainable construction has further accelerated glass adoption, as it is fully recyclable and allows for natural light utilization, reducing energy consumption. The segment is also benefiting from technological advancements in safety glass manufacturing and increasing awareness about the flexibility and safety features of modern glass construction materials. The rising demand for glass facades, whether in curtain walling, bolted glazing, spider glazing, or point-fixed glass facades, is expected to continue driving this segment's growth trajectory.
Remaining Segments in Material Type
The metal, timber, and other material segments each play crucial roles in India's prefabricated buildings market. The metal segment, particularly prefabricated steel buildings, has established itself as a vital component in pre-engineered buildings, offering advantages in terms of strength, durability, and quick assembly. Timber has gained traction in eco-friendly construction projects, with materials like Glulam and Cross-laminated Timber becoming increasingly popular for their sustainability and aesthetic appeal, contributing to the rise of prefabricated wooden buildings. Other materials, including expanded polystyrene and PVC, are finding applications in specific niches where lightweight construction and superior insulation properties are required. These segments collectively contribute to the market's diversity, offering builders and developers a wide range of options to meet various construction requirements and environmental considerations.
Segment Analysis: By Application
Industrial, Institutional, and Infrastructure Segment in India Prefabricated Buildings Market
The industrial, institutional, and infrastructure applications segment dominates the India prefabricated buildings market, commanding approximately 45% of the total market share in 2024. This segment's prominence is driven by rapid industrialization and significant infrastructure development initiatives across India. The segment's growth is particularly notable in the construction of warehouses, factories, bridges, and educational institutions. Major companies like EPACK Prefab have successfully delivered numerous industrial prefab projects, including the construction of over 10 million square feet of industrial and warehouse buildings. The segment's dominance is further reinforced by government infrastructure initiatives and the increasing adoption of prefabricated solutions in public sector projects, including metro stations, airports, and educational facilities.
Residential Segment in India Prefabricated Buildings Market
The residential segment is emerging as the fastest-growing segment in the India prefabricated buildings market, projected to grow at approximately 10% during 2024-2029. This remarkable growth is primarily driven by the increasing demand for affordable housing solutions and government initiatives like the Pradhan Mantri Awas Yojana (PMAY). The segment's growth is further accelerated by the rising urbanization, with prefabricated solutions offering faster construction timelines and cost-effective housing alternatives. Modern prefabricated homes are gaining popularity among urban dwellers due to their customizable designs, energy efficiency, and reduced construction waste. The segment is also benefiting from technological advancements in prefabrication techniques, enabling the construction of high-quality residential units that meet diverse consumer preferences and requirements.
Commercial Segment in India Prefabricated Buildings Market
The commercial segment plays a vital role in shaping the India prefabricated buildings market, offering solutions for offices, retail spaces, and hospitality structures. This segment is particularly driven by the rapid expansion of e-commerce and retail sectors in tier 2 and tier 3 cities, necessitating quick deployment of commercial spaces. The segment benefits from the advantages of prefabrication, such as faster construction times, consistent quality, and flexible design options. Commercial prefabricated buildings are increasingly preferred for their ability to incorporate modern amenities, energy-efficient features, and sustainable construction practices, making them attractive for businesses seeking quick establishment or expansion of their operations. Innovations such as containerized building and panelized building systems are enhancing the versatility and appeal of prefabricated commercial structures.
India Prefabricated Buildings Industry Overview
Top Companies in India Prefabricated Buildings Market
The market is led by established players like Everest Industries Limited, Satec Envir Engineering, Epack Prefab, Speed 4 Prefab Solutions, and Balarka Fabricon Private Limited. Companies are increasingly focusing on innovative prefabricated building solutions through investments in research and development to create designs that excel in aesthetics, functionality, and sustainability. The adoption of advanced technologies like Building Information Modeling (BIM), automation, and robotics has become a key trend, enabling improved efficiency and production quality. Strategic collaborations with architects, contractors, and industry stakeholders are common, helping companies expand their reach and offer comprehensive solutions. Many players are expanding their manufacturing capabilities and geographical presence, particularly in southern India, to cater to growing demand from sectors like warehousing, commercial spaces, and affordable housing.
Fragmented Market with Strong Local Players
The Indian prefabricated buildings market exhibits a moderately fragmented structure, characterized by the presence of both established national players and regional manufacturers. The market features a mix of large conglomerates with diversified building material portfolios and specialized precast construction companies, each bringing unique strengths to the competitive landscape. While some global players operate through partnerships and subsidiaries, local companies maintain a strong presence due to their understanding of regional requirements, established distribution networks, and ability to offer customized solutions at competitive prices. The competition is primarily based on factors such as price, design innovation, production efficiency, and favorable material pricing.
The market has witnessed limited merger and acquisition activity, with companies preferring organic growth through capacity expansion and technology upgrades. The industry structure allows for the coexistence of different business models, from full-service providers offering end-to-end solutions to specialized manufacturers focusing on specific prefab components. Regional players have carved out strong niches in their respective territories, while larger national players leverage their brand reputation and extensive distribution networks to maintain market position.
Innovation and Sustainability Drive Future Success
For established players to maintain and increase their market share, focus needs to be placed on developing sustainable and energy-efficient prefabricated solutions that align with growing environmental consciousness. Companies must invest in digital technologies and automation to improve production efficiency and reduce costs while maintaining quality standards. Building strong relationships with key stakeholders in the construction ecosystem, including developers, architects, and government bodies, will be crucial for long-term success. Additionally, established players need to diversify their product portfolios to cater to various market segments, from affordable housing to premium commercial spaces.
New entrants and smaller players can gain ground by focusing on specialized market segments or geographical regions where they can build strong competencies. Success factors include developing innovative designs that address specific regional requirements, establishing efficient supply chain networks, and maintaining cost competitiveness through lean operations. The regulatory environment, particularly government initiatives promoting prefabricated construction and sustainable building practices, presents opportunities for both incumbents and new entrants. Companies must also consider the concentration of end-users in specific sectors like warehousing, commercial spaces, and affordable housing while developing their market strategies.
India Prefabricated Buildings Market Leaders
-
Everest Industries Limited
-
Satec Envir Engineering (India) Private Limited
-
Epack Prefab
-
Speed 4 Prefab Solutions Pvt. Ltd
-
Balarka Fabricon Private Limited
- *Disclaimer: Major Players sorted in no particular order
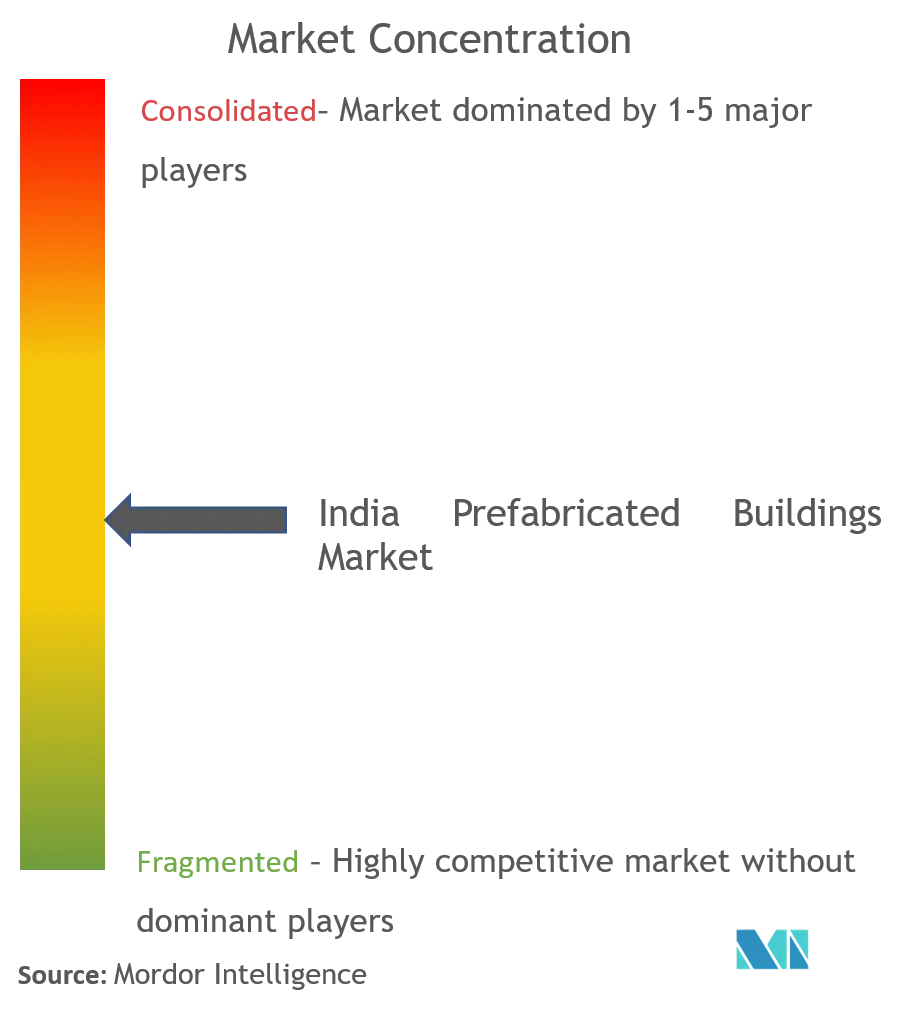
India Prefabricated Buildings Market News
- 2024: and shall be funded through a mix of debt and internal accruals.
- February 2023: EPACK PREFAB, a manufacturer of pre-engineered building solutions, is expanding its manufacturing footprint with an investment of INR 198 crore to set up a new facility spread over 25 acres in Andhra Pradesh. At present, it has two manufacturing plants in Rajasthan and Greater Noida, with a total capacity to produce 1,00,000 metric tonnes of prefabricated material annually, which will increase to 200,000 metric tonnes with the third plant.
India Prefabricated Buildings Industry Segmentation
A prefabricated building, informally a prefab, is a building that is manufactured and constructed using prefabrication. It consists of factory-made components or units transported and assembled on-site to form the complete building.
The Indian prefabricated buildings market is segmented by material type (concrete, glass, metal, timber, and other material types) and by application (residential, commercial, and other applications [industrial, institutional, and infrastructure]). The report offers market size and forecasts for India's prefabricated buildings industry in value (USD) for all the above segments.
By Material Type | Concrete |
Glass | |
Metal | |
Timber | |
Other Material Types | |
By Application | Residential |
Commercial | |
Other Applications (Industrial, Institutional, and Infrastructure) |
Concrete |
Glass |
Metal |
Timber |
Other Material Types |
Residential |
Commercial |
Other Applications (Industrial, Institutional, and Infrastructure) |
India Prefabricated Buildings Market Research FAQs
How big is the India Prefabricated Buildings Market?
The India Prefabricated Buildings Market size is expected to reach USD 15.07 billion in 2025 and grow at a CAGR of 8.95% to reach USD 23.13 billion by 2030.
What is the current India Prefabricated Buildings Market size?
In 2025, the India Prefabricated Buildings Market size is expected to reach USD 15.07 billion.
Who are the key players in India Prefabricated Buildings Market?
Everest Industries Limited, Satec Envir Engineering (India) Private Limited, Epack Prefab, Speed 4 Prefab Solutions Pvt. Ltd and Balarka Fabricon Private Limited are the major companies operating in the India Prefabricated Buildings Market.
What years does this India Prefabricated Buildings Market cover, and what was the market size in 2024?
In 2024, the India Prefabricated Buildings Market size was estimated at USD 13.72 billion. The report covers the India Prefabricated Buildings Market historical market size for years: 2020, 2021, 2022, 2023 and 2024. The report also forecasts the India Prefabricated Buildings Market size for years: 2025, 2026, 2027, 2028, 2029 and 2030.