Computer Numerical Controls (CNC) Market Size and Share
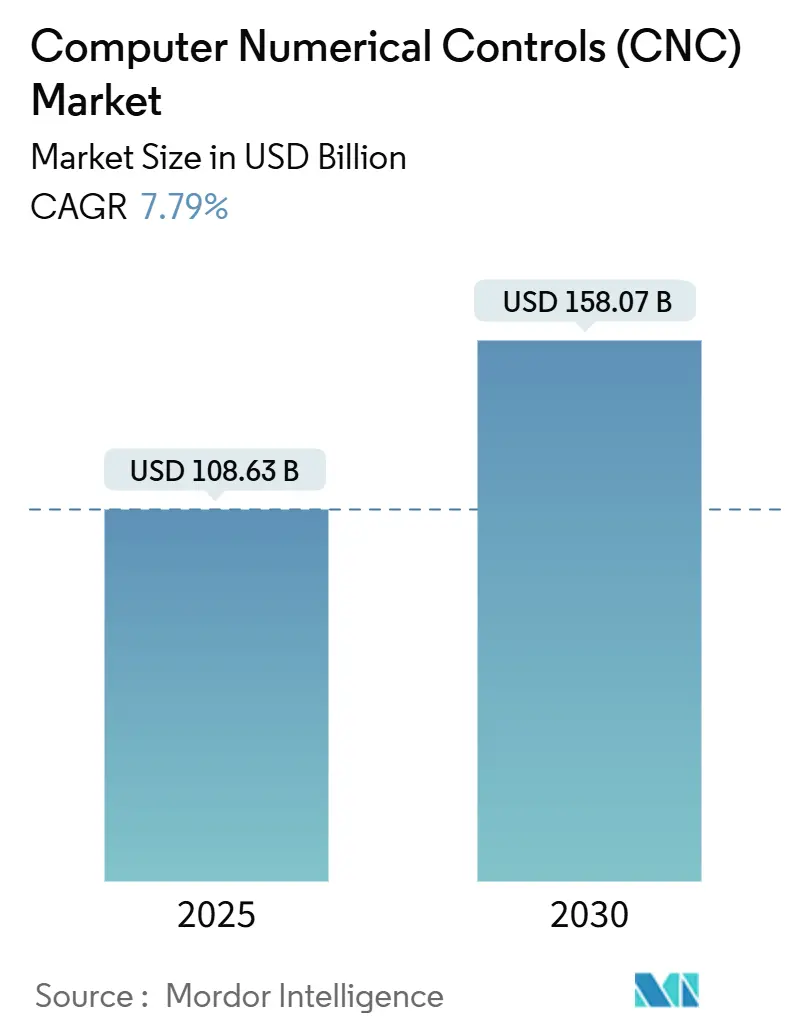
Computer Numerical Controls (CNC) Market Analysis by Mordor Intelligence
The global CNC machine market stands at USD 108.63 billion in 2025 and is forecast to reach USD 158.07 billion by 2030, reflecting a 7.79% CAGR. Persistently tight labor markets, near-shoring of production, and the push for Industry 4.0 automation are converging, so manufacturers are accelerating investments in multi-axis and digitally connected equipment. Reshoring legislation in the United States and Europe is shifting capital away from low-cost regions toward flexible machining assets that support short lead-time production. Cybersecurity risk is rising in parallel with connectivity, motivating vendors to embed security-by-design features in new controllers. [1]World Economic Forum, “Building a Culture of Cyber Resilience in Manufacturing,” weforum.org At the same time, sustained high steel and aluminum prices are driving demand for precision processes that minimize scrap. [2]Jeetendra Khadan & Kaltrina Temaj, “Metal Prices Set to Remain High in 2024-25,” blogs.worldbank.org Together these forces keep the CNC machine market on a solid growth trajectory even as component shortages create near-term supply friction.
Key Report Takeaways
- By machine type, CNC lathes held 23.4% of CNC machine market share in 2024, while 5-axis and above machines are projected to grow at 10.8% CAGR through 2030.
- By axis type, 3-axis platforms led with 46% share in 2024, whereas 5-axis and above configurations are advancing at 10.8% CAGR.
- By component, controllers accounted for 41% share of the CNC machine market size in 2024, and servo motors are expanding at 9.5% CAGR.
- By control system, closed-loop technology commanded 67% share in 2024, with feedback sensors registering an 11.2% CAGR outlook.
- By deployment, stand-alone units retained 78% revenue share in 2024; integrated production cells post the fastest 12.3% CAGR to 2030.
- By end user, automotive applications led with 29% share, while medical devices are on track for a 9.9% CAGR through 2030.
- By region, Asia-Pacific captured 52% of 2024 revenue, supported by China’s scale and Japan’s precision engineering strengths.
Global Computer Numerical Controls (CNC) Market Trends and Insights
Drivers Impact Analysis
Driver | (~) % Impact on CAGR Forecast | Geographic Relevance | Impact Timeline |
---|---|---|---|
Reshoring-led demand for flexible CNC equipment | +1.20% | North America and Europe | Medium term (2-4 years) |
Industry 4.0 adoption of digital-twin-enabled controllers | +1.80% | Global, APAC leading | Long term (≥ 4 years) |
EV power-train complexity boosting multi-axis orders | +1.50% | APAC core, spill-over to North America | Medium term (2-4 years) |
Government aerospace incentives for precision machining | +0.70% | Japan and France | Long term (≥ 4 years) |
Automated CNC cells easing skilled-labor gaps | +1.30% | Global, acute in North America and Europe | Short term (≤ 2 years) |
Micro-CNC demand from medical devices | +0.90% | Global, regulated regions | Medium term (2-4 years) |
Source: Mordor Intelligence
Reshoring-led Demand for Flexible CNC Equipment in North America and Europe
U.S. imports of finished goods from China fell 13% in 2023 while domestic factory investment rose sharply after infrastructure and semiconductor incentives. [3]Source: Harry Moser, “U.S. Reshoring Surges as China’s Exports to the U.S. Plunge,” amtonline.org Incoming work is highly variable, so buyers prefer adaptable 5-axis machines and modular robot cells that handle diverse part families. Near-market production justifies higher capital outlays because freight risks fall and delivery speed improves. Vendors that offer rapid re-tooling and digital setup features gain a competitive edge. This reshoring vector directly enlarges the CNC machine market by converting decades of outsourced volumes into local capacity growth.
Industry 4.0-Driven Adoption of Digital-Twin-Enabled CNC Controllers
Digital twins let programmers validate tool paths virtually, cutting physical setup time by 20% with Siemens Sinumerik 828D hardware. Studies show 14.53% productivity gains and 13.9% lower energy use when machines run in closed-loop coordination with their virtual counterparts. Adoption is strongest in aerospace and automotive sectors that need real-time compensation for thermal drift and tool wear. Controller suppliers embed cloud connectivity and AI analytics, turning the CNC machine market into a software-centric arena. As license revenues grow, machine builders look to recurring income rather than one-time hardware margin.
EV Power-train Complexity Boosting Multi-Axis CNC Orders in Asia
Battery enclosures and motor housings require intricate cavities and mixed-material machining that legacy 3-axis setups cannot deliver. Tier-1 suppliers across China, Japan, and South Korea are standardizing on simultaneous 5-axis and mill-turn centers to cut features in one clamp. Regional EV output could reach 50% of car sales by 2030, locking in long-term demand for advanced equipment. Knowledge transfer from early adopters accelerates the upgrade cycle across the supply base. The CNC machine market therefore expands not just in volume but also in average selling price as axis counts and controller sophistication rise.
Government Incentives for Aerospace Precision Machining (Japan, France)
Japan’s multi-sector consortium introduced magnesium-alloy wire-laser technology that reduces rocket component weight by 20%. France is channeling grants into additive-subtractive hybrid machines to enhance space launch competitiveness. These programs de-risk investment for machine buyers who need extreme accuracy and exotic-material capability. Success stories diffuse into medical implants and semiconductor fixtures, widening the CNC machine market footprint. Because public funding underwrites R&D, vendors can fast-track toolpath algorithms and in-process metrology features that later migrate to mainstream models.
Restraints Impact Analysis
Restraint | (~) % Impact on CAGR Forecast | Geographic Relevance | Impact Timeline |
---|---|---|---|
Semiconductor motion-control chip shortages | -0.80% | Global, acute in APAC | Short term (≤ 2 years) |
High CAPEX of 5-axis and hybrid machines | -0.60% | Global, affects SMEs | Medium term (2-4 years) |
Cyber-security concerns with networked CNC systems | -0.40% | Global, critical infrastructure | Long term (≥ 4 years) |
Volatile steel and aluminum prices impacting ROI | -0.50% | Global, price-sensitive markets | Short term (≤ 2 years) |
Source: Mordor Intelligence
Semiconductor Motion-Control Chip Shortages Constraining Supply
Precision servo drives rely on specialty ASICs that remain in short supply, stretching lead times for premium machines beyond nine months. Some builders redesign around available chips, but that demands costly re-qualification. OEMs with secured allocations win share while latecomers lose backlog. The bottleneck suppresses the near-term CNC machine market volume despite solid order books.
High CAPEX of 5-Axis and Hybrid Additive–Subtractive Machines
Top-tier 5-axis centers can cost twice the price of conventional 3-axis mills, while hybrid additive-subtractive platforms command even larger premiums). Small job shops struggle to finance these systems, especially when inflation lifts borrowing costs. Leasing programs gain traction, yet payback periods often exceed three years. The price hurdle slows penetration, limiting the CNC machine market expansion in the SME segment.
Segment Analysis
By Machine Type: Lathes Maintain Core Demand While 5-Axis Surges
CNC lathes held 23.4% of CNC machine market share in 2024 and remain indispensable for round parts such as shafts and hubs. Continuing EV power-train development raises tolerance demands, so many shops retrofit live tooling and Y-axis capability to conventional turning centers. Milling machines form the next largest slice of the CNC machine market, serving complex mold cavities for aerospace and medical implants. Laser and plasma cutters grow as sheet-metal designs multiply in battery enclosures, and EDM stays relevant for hardened tool steels. The CNC machine market size for 5-axis platforms is poised to grow 10.8% CAGR because single-setup capability slashes fixture time and eliminates reposting errors. Grinding and welding machines add niche depth: friction-stir welding joins battery shells without filler metal, while grinding delivers mirror finishes on turbine discs.
The 5-axis and above category illustrates why value is shifting toward flexibility rather than raw spindle horsepower. Integrated tool changers allow several hundred cutters that handle aluminum, titanium, and composites in one cycle. Probing routines verify geometry in situ, reducing scrap despite high material costs. Early adopters report 18% throughput gains once operators master simultaneous axis commands. Component suppliers therefore treat multi-axis as a strategic hedge against labor risk, pushing the CNC machine market toward higher complexity tiers regardless of plant size.
Note: Segment shares of all individual segments available upon report purchase
By Axis Type: Multi-Axis Configurations Outpace Legacy Platforms
Three-axis units still anchor the installed base with a 46% share and attractive price-performance ratios for simple work. Yet part programs with undercuts and helical flutes drive shops to add rotary tables or invest in full five-axis machines. The 5-axis and above segment posts a 10.8% CAGR because it merges milling and turning, enabling machining from all directions without reclamping. Improved CAM software plus training subsidies make the technology accessible to mid-market buyers, widening the CNC machine market size for advanced axis counts.
Rotary-tilt tables on 4-axis systems bridge the gap and allow affordable entry into positional machining. However, aerospace primes increasingly require simultaneous motion capability that only true 5-axis delivers. FANUC’s 500i-A controller, with 2.7 times CPU power, optimizes axis interpolation for complex tool paths. [4]Roger Sanders, “Robotic CNC Machine Tending Automation Increases Production and ROI,” fanucamerica.com As OEMs validate shorter cycle times and better surface finishes, even conservative job shops reconsider equipment roadmaps. This dynamic ensures a steady migration that enlarges the CNC machine market beyond conventional formats.
By Component: Controllers Capture the Digital Value
Controllers represented 41% of revenue in the 2024 component split and act as the brains of every installation. They host digital-twin models, cybersecurity layers, and AI algorithms that predict tool wear. The CNC machine market size tied to controller upgrades grows as manufacturers retrofit legacy iron with new electronics rather than buy full machines. Servo motors follow at 9.5% CAGR because higher torque density and energy-saving drives meet both precision and sustainability mandates.
Sensor arrays now integrate vibration, temperature, and acoustic emission data to feed condition-based maintenance dashboards. Edge processing modules crunch data locally to avoid latency, then forward summaries to cloud platforms for fleet analytics. This shift moves value creation out of hardware housing into firmware updates, reinforcing a service-oriented revenue model that transforms the CNC machine industry during the forecast horizon.
By Control System: Closed-Loop Dominates Precision Workflows
Closed-loop feedback claimed 67% share in 2024 because alloy variations and thermal drift demand real-time correction. Probing cycles inside the work envelope measure features mid-process, then update tool offsets on the fly. Open-loop drives survive in wood routing and plastics, where tolerances are forgiving, but their share keeps contracting. The CNC machine market share for closed-loop solutions will widen further as sensor prices fall and quality audits tighten.
Digital-twin commissioning elevates closed-loop systems to new relevance. Siemens SINUMERIK ONE allows programmers to debug virtual G-code weeks before the physical machine lands on the floor, cutting launch time sharply. Over-the-air updates add new kinematics without hardware swaps, future-proofing assets. As inspection standards stiffen across aerospace and medical segments, buyers gravitate to platforms that assure sub-10 micron repeatability, reinforcing closed-loop dominance in the CNC machine market.
By Deployment: Integrated Cells Redefine Productivity
Stand-alone machines still make up 78% of installed capacity because they offer flexible scheduling across mixed orders. Yet integrated robot cells are expanding at 12.3% CAGR as plants chase lights-out production. A single robot can tend multiple spindles, vacuum parts into coordinate-measuring fixtures, and palletize finished goods, lifting utilization well above the 60% typical of manual shifts. The CNC machine market benefits because every cell includes not only a new mill or lathe but also peripherals such as grippers, vision cameras, and safety scanners.
Return-on-investment cases are becoming clearer. Custom Tool Inc. raised throughput 20% after installing a FANUC M-10 tending cell and redeployed operators to quality engineering tasks. Software orchestrators now balance priority jobs across multiple cells, smoothing flow without human dispatchers. This systemic approach will push plant managers to specify integrated cells in future capex plans, expanding the CNC machine market beyond single point solutions.
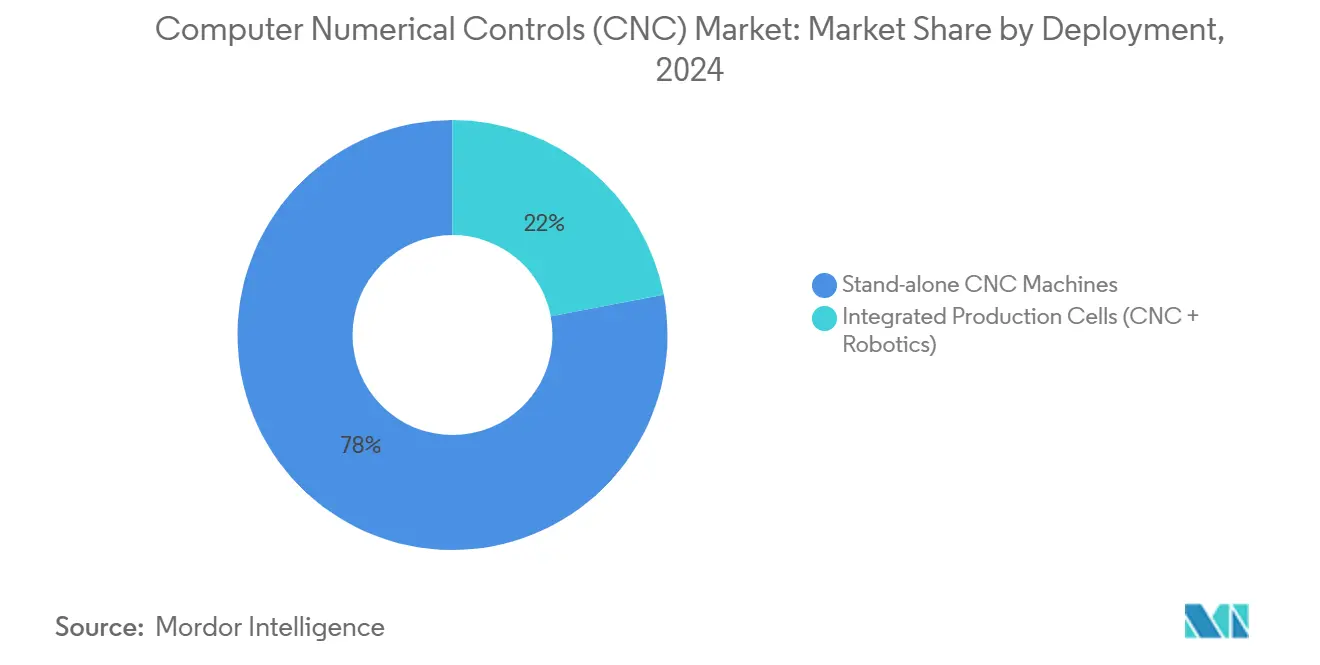
By End User: Automotive Anchors Demand, Medical Devices Accelerate
Automotive producers consumed 29% of 2024 revenue, machining engine blocks, motor housings, and battery trays with cycle-time targets under one minute. Lightweighting pushes them toward high-speed aluminum milling and friction-stir joining, sustaining steady spend. Aerospace primes require tighter tolerances in nickel alloys, purchasing 5-axis centers with vacuum work-holding to avoid distortion. Power-generation firms invest in large-format vertical lathes for wind-turbine hubs, while electronics manufacturers adopt micro-mills for connector housings.
Medical devices show the fastest 9.9% CAGR because aging populations seek minimally invasive tools, each with micro-threads and bio-compatible coatings. Sub-micron accuracy and validation reports are non-negotiable, so suppliers favor premium platforms with integrated measurement. This niche attracts startups that design purpose-built micro-turning centers, broadening competition inside the CNC machine market. As health-care regulation tightens traceability, machine vendors supplying turnkey compliance software will capture share at the expense of hardware-only rivals.
Geography Analysis
Asia-Pacific leads the CNC machine market with a 52% revenue share, anchored by China’s vast supplier ecosystem and Japan’s trail-blazing multi-axis technology. Beijing’s dual-circulation policy encourages local content, spurring demand for domestic spindle makers and feedback encoders. Tokyo’s investment in magnesium alloy machining for space launch widens its leadership in lightweight materials. South Korea’s state-funded drive system advances cut reliance on imported servos, underlining a regional strategy toward self-sufficiency. ASEAN countries benefit from supply-chain diversification, attracting greenfield plants that require entry-level yet upgradeable equipment.
North America gains momentum as reshoring projects proliferate under the Infrastructure Investment and Jobs Act and the CHIPS Act. Siemens earmarked over USD 10 billion to expand U.S. production lines for electrification hardware, adding 900 skilled roles. FANUC’s USD 110 million campus in Michigan trains thousands of technicians annually, alleviating talent shortages. Canadian aerospace clusters in Quebec adopt high rpm titanium cutters, while Mexican automotive hubs invest in flexible machining to service near-term EV assembly demand. The CNC machine market thus benefits from synchronized policy and private investment.
Europe shows steady growth amid sustainability mandates and push for electric mobility. French aerospace subsidies accelerate hybrid additive-subtractive machine trials, boosting local OEM competitiveness. Germany’s Mittelstand firms retrofit legacy mills with closed-loop drives to cut energy use, aligning with EU Green Deal goals. FANUC’s Iberia office expansion signals rising demand in Spain and Portugal for robotized machining cells. Eastern European countries capture overflow work from Western plants, driving orders for mid-range 3-axis centers. Despite macro headwinds, Europe remains a technology testbed that shapes future CNC machine market specifications.
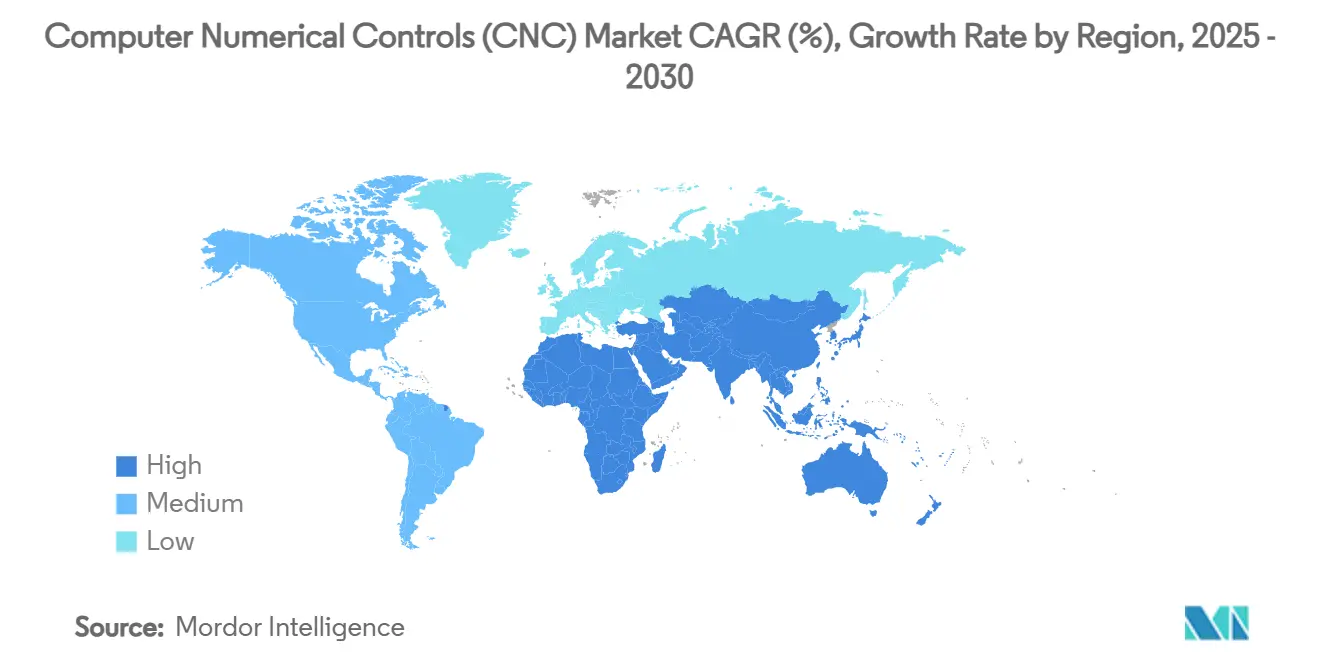
Competitive Landscape
The CNC machine market shows moderate consolidation. FANUC, Siemens, and DMG MORI leverage global service footprints and broad portfolios to secure key accounts. Their combined strength spans controllers, robots, and analytics software, creating bundled solutions difficult for single-product rivals to match. Mid-tier players differentiate through industry focus—Mazak targets aerospace titanium, while Okuma tailors thermal compensation for heavy automotive cuts.
Digital capability is the new battleground. Siemens bought Altair’s simulation assets to embed AI-assisted design into machining workflows, blurring the line between CAD and toolpath execution. DMG MORI collaborates with Renishaw to integrate in-machine probing and cloud dashboards, delivering turnkey process verification. Startups focus on niches such as hybrid additive or micro-machining, using open software stacks to shorten development cycles. United Grinding’s planned acquisition of GF Machining Solutions exemplifies horizontal consolidation aimed at ultra-precision markets.
Partnership ecosystems multiply. Machine builders align with cloud providers to offer subscription-based optimization tools. Tooling companies integrate sensorized cutters that feed back to the controller, closing the loop on tool life predictions. This convergence rewards firms that combine mechanical reliability with data science talent, raising competitive intensity. The result is a CNC machine market that continues to reward scale on one axis and hyper-specialization on the other, leaving mid-sized firms to choose strategic alliances or risk marginalization.
Computer Numerical Controls (CNC) Industry Leaders
-
Siemens AG
-
JTEKT Corporation
-
Hurco Companies Inc
-
Haas Automation, Inc.
-
Fanuc Corporation
- *Disclaimer: Major Players sorted in no particular order
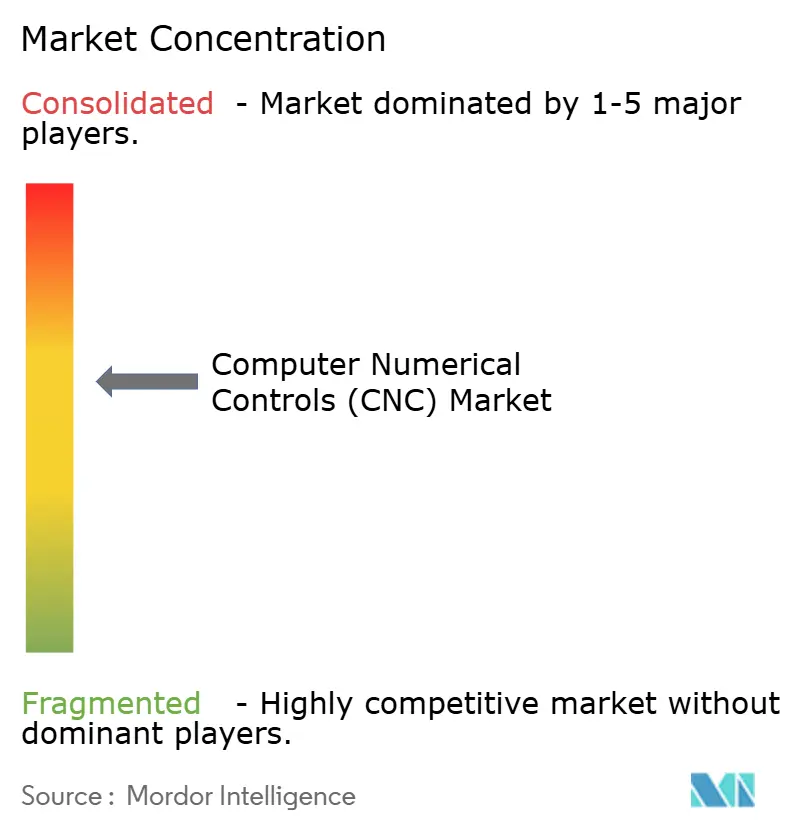
Recent Industry Developments
- March 2025: Siemens committed over USD 10 billion to new U.S. factories, creating 900 jobs and expanding electrification equipment output.
- March 2025: Mastercam (Sandvik) added four CAM firms, lifting 2025 acquisitions to eight as it deepens its software ecosystem.
- January 2025: Walter AG and Heller formed a machining partnership to co-develop sustainable processes for automotive and aerospace sectors.
- December 2024: Ventec earmarked USD 17 million for a PCB materials plant in Thailand, targeting Q1 2026 full output.
Global Computer Numerical Controls (CNC) Market Report Scope
Computer numerical control (CNC) machining is the process through which computers control machine-based processes in manufacturing. The kinds of machines controlled include lathes, mills, routers, and grinders all of which are used for the manufacturing of metal and plastic products. Applications are in automotive. oil and gas, aerospace and defense, and others.
By Machine Type | CNC Lathe Machines | ||
CNC Milling Machines | |||
CNC Laser Cutting Machines | |||
CNC Plasma Cutting Machines | |||
CNC Electric Discharge Machines (EDM) | |||
CNC Grinding Machines | |||
CNC Winding Machines | |||
CNC Welding Machines | |||
Other Machine Types | |||
By Axis Type | 3-Axis | ||
4-Axis | |||
5-Axis and Above | |||
By Component | CNC Controller | ||
Servo Motor Drive | |||
Sensors and Feedback | |||
Others | |||
By Control System | Open-loop | ||
Closed-loop | |||
By Deployment | Stand-alone CNC Machines | ||
Integrated Production Cells (CNC + Robotics) | |||
By End User | Automotive (incl. EV) | ||
Aerospace and Defense | |||
Power and Energy | |||
Industrial Machinery | |||
Medical Devices | |||
Electronics and Semiconductor | |||
Other End Users | |||
By Geography | North America | United States | |
Canada | |||
Latin America | Mexico | ||
Brazil | |||
Argentina | |||
Rest of Latin America | |||
Europe | Germany | ||
United Kingdom | |||
France | |||
Italy | |||
Spain | |||
Rest of Europe | |||
Middle East and Africa | |||
Asia-Pacific | China | ||
Japan | |||
South Korea | |||
India | |||
Australia | |||
Rest of Asia-Pacific |
CNC Lathe Machines |
CNC Milling Machines |
CNC Laser Cutting Machines |
CNC Plasma Cutting Machines |
CNC Electric Discharge Machines (EDM) |
CNC Grinding Machines |
CNC Winding Machines |
CNC Welding Machines |
Other Machine Types |
3-Axis |
4-Axis |
5-Axis and Above |
CNC Controller |
Servo Motor Drive |
Sensors and Feedback |
Others |
Open-loop |
Closed-loop |
Stand-alone CNC Machines |
Integrated Production Cells (CNC + Robotics) |
Automotive (incl. EV) |
Aerospace and Defense |
Power and Energy |
Industrial Machinery |
Medical Devices |
Electronics and Semiconductor |
Other End Users |
North America | United States |
Canada | |
Latin America | Mexico |
Brazil | |
Argentina | |
Rest of Latin America | |
Europe | Germany |
United Kingdom | |
France | |
Italy | |
Spain | |
Rest of Europe | |
Middle East and Africa | |
Asia-Pacific | China |
Japan | |
South Korea | |
India | |
Australia | |
Rest of Asia-Pacific |
Key Questions Answered in the Report
What is the current size of the CNC machine market?
The CNC machine market stands at USD 108.63 billion in 2025.
How fast is the CNC machine market expected to grow?
Global revenue is projected to rise at a 7.79% CAGR, reaching USD 158.07 billion by 2030.
Which region holds the largest share of the CNC machine market?
Asia-Pacific leads with a 52% revenue share, driven by China’s scale and Japan’s precision engineering leadership.
What machine type is growing the fastest?
Five-axis and above configurations are expanding at a 10.8% CAGR as firms consolidate operations into single-setup machining.
Why are integrated CNC cells gaining popularity?
Robot-tended cells boost spindle utilization, offset labor shortages, and enable lights-out production, delivering 20% or higher throughput gains.
Which end-user industry will see the fastest CNC spending growth?
Medical device manufacturing is poised for a 9.9% CAGR because of rising demand for sub-micron implants and stringent regulatory requirements.