Aircraft Landing Gear Systems Market Size and Share
Aircraft Landing Gear Systems Market Analysis by Mordor Intelligence
The aircraft landing gear systems market size stands at USD 11.82 billion in 2025 and is forecasted to reach USD 17.46 billion by 2030, advancing at an 8.11% CAGR. Fleet renewal programs, the return of long-range travel, and the rise of electric-actuation technologies are fuelling demand. Commercial airframers are accelerating production to work through record backlogs, while defense ministries are modernizing tactical fleets. Airlines are shifting to managed maintenance agreements that guarantee gear availability and lower capital exposure, and urban-air-mobility prototypes are opening new low-weight, high-cycle niches. At the same time, supply-chain pressures around titanium, carbon fiber, and high-precision castings are forcing OEMs to dual-source critical forgings and invest in local capacity.
Key Report Takeaways
- By aircraft type, the commercial narrowbody segment held 43.55% of the aircraft landing gear systems market share in 2024, whereas the military aviation segment is projected to grow fastest at an 8.85% CAGR through 2030.
- By gear position, the main landing gear dominated with 63.45% of the aircraft landing gear systems market size in 2024; the nose landing gear is set to expand at a 9.55% CAGR to 2030.
- By material, steel alloys led with 46.75% revenue share in 2024, while composites are forecasted to post a 10.45% CAGR, the highest among all materials.
- By end user, OEM deliveries accounted for 68.35% of the aircraft landing gear systems market size in 2024; the aftermarket segment is advancing at an 8.78% CAGR on the back of exchange pools and power-by-the-hour contracts.
- By geography, North America retained the largest regional position with 37.89% market share in 2024; Asia-Pacific is expected to record the strongest regional CAGR of 8.32% between 2025 and 2030.
Global Aircraft Landing Gear Systems Market Trends and Insights
Drivers Impact Analysis
Driver | (≈) % Impact on CAGR Forecast | Geographic Relevance | Impact Timeline |
---|---|---|---|
Lightweight-materials demand surge | +1.8% | Global – strong momentum in Asia-Pacific | Medium term (2-4 years) |
OEM push for electric/hydraulic-free eBrake systems | +1.2% | North America and Europe | Long term (≥ 4 years) |
Commercial aircraft production ramp-ups post-2025 | +2.1% | Global – clustered around major OEM hubs | Short term (≤ 2 years) |
MRO outsourcing and exchange-service adoption | +0.9% | North America and Europe; spreading to Asia-Pacific | Medium term (2-4 years) |
Urban-air-mobility (eVTOL/air-taxi) landing-gear volumes | +0.7% | North America and Europe first movers | Long term (≥ 4 years) |
Digital twin-enabled predictive maintenance | +0.6% | Global – led by tier-one airlines | Medium term (2-4 years) |
Source: Mordor Intelligence
Lightweight-materials demand surge
Airframers are deploying titanium alloys and carbon-fiber composites to trim landing-gear weight by up to 30%, translating directly into lower fuel burn and longer range. A titanium–aluminum super-elastic alloy developed by Tohoku University maintains strength from -269°C to 127°C, widening its applicability across extreme operating environments.[1]Tohoku University, “Ti-Al Super-elastic Alloy Study,” tohoku.ac.jp Boeing and Airbus wide-bodies already feature airframes with more than 50% CFRP content, and regional supply chains across China and India are scaling carbon-fiber output to keep pace with demand. The 2024 investigation into counterfeit titanium underscored the importance of full material traceability. Military programs favour ultra-high-strength steels such as AerMet 310 for superior fracture toughness, further diversifying material choices.
OEM push for electric/hydraulic-free eBrake systems
Leading suppliers are replacing central hydraulic circuits with distributed electro-hydrostatic actuators to reduce pipeline complexity, slash maintenance hours, and lower system weight. Collins Aerospace invested USD 200 million to add 70,000 sq ft at its Spokane carbon-brake plant, boosting capacity by 50% to meet eBrake demand.[2]Collins Aerospace, “Spokane Plant Expansion Release,” compositesworld.com The Clean Aviation Electrical Nose Landing Gear System demonstrator validates full electric steering and retraction modules, moving towards zero-hydraulic architectures. Certification teams must now evaluate new fault modes, but electric solutions promise modular upgrades and smoother scalability for future aircraft.
Commercial aircraft production ramp-ups post-2025
Airbus lifted its 20-year delivery outlook to 43,420 jets, of which 34,250 are single-aisle, while Boeing sees total demand at nearly 44,000 aircraft through 2043. Safran shipped 304 A320 landing-gear shipsets in H1 2024, a 36% increase year on year. Casting shortages and workforce gaps constrain output, but OEMs are co-investing with tier-one suppliers to unlock bottlenecks.
MRO outsourcing and exchange-service adoption
Exchange pools allow airlines to avoid the USD 750,000 overhaul charge of a main-gear shipset, converting heavy capex into a predictable monthly fee. Boeing’s landing-gear exchange network now spans more than 2,000 assets worldwide, while Air India signed a multi-year managed-parts pact covering its B787 fleet. Independent overhaul shops are consolidating to stay relevant, with GA Telesis acquiring AAR’s gear-overhaul arm in 2025.
Restraints Impact Analysis
Restraint | (≈) % Impact on CAGR Forecast | Geographic Relevance | Impact Timeline |
---|---|---|---|
Titanium and composite supply-chain bottlenecks | −1.4% | Global – most acute in North America and Europe | Short term (≤ 2 years) |
Regulatory certification delays for novel architectures | −0.8% | Global – stringent in FAA/EASA jurisdictions | Medium term (2-4 years) |
High capex and eight-to-ten-year overhaul costs | −0.6% | Global – amplified in emerging markets | Long term (≥ 4 years) |
OEM–airline power-by-the-hour dominance squeezing independents | −0.4% | North America and Europe, expanding worldwide | Medium term (2-4 years) |
Source: Mordor Intelligence
Titanium and composite supply-chain bottlenecks
Accelerating aerospace demand has lengthened forging lead times past 12 months, especially for large 300M and Ti-6-4 billets. China produces only about 7,000 MT of aerospace-grade carbon fiber against global use of 22,000 MT, leaving a gap that drives prices higher and slows composite spar production.[3]Composites World, “Global Carbon-Fiber Market Review 2024,” compositesworld.com OEMs fund dual-sourcing and in-house forging lines to mitigate exposure, yet skilled-labor shortages and certification audits restrict rapid scale-up.
Regulatory certification delays for novel architectures
The FAA’s updated Part 25 rules require system-level safety analysis for electric actuation and composite bogies, adding test matrices that lengthen programs by quarters. Emerging eVTOL developers face special-condition frameworks covering crashworthiness, occupant safety, and novel nose-gear steering functions.[4]Composites World, “Global Carbon-Fiber Market Review 2024,” compositesworld.com Such scrutiny protects safety but slows commercialization, particularly for smaller entrants with limited compliance budgets.
Segment Analysis
By Aircraft Type: Commercial aircraft dominate, military accelerates
The aircraft landing gear systems market size for commercial platforms remained the largest in 2024, driven by narrowbody jets that captured 43.55% market share as carriers renewed ageing fleets and chased fuel-burn savings. Airbus’s backlog covers 40% of projected single-aisle deliveries, implying sustained volume through 2030. Widebody programs resumed steady output as intercontinental routes reopened, and freight conversions kept twin-aisle lines busy. Military demand is rising faster, posting an 8.85% CAGR as governments recapitalise fighter and tanker fleets and extend lifecycles on legacy aircraft. The US Department of Defense allocated USD 57.2 billion to tactical-aircraft operations between 2018 and 2023.[5]US GAO, “Tactical Aircraft O&M Spending FY2018-2023,” gao.gov Across Asia, Japan, India, and South Korea are inducting indigenous fighters that specify local content in landing-gear assemblies, diversifying the supplier map. Business-jet and rotorcraft segments remain niche yet important incubators for electro-mechanical actuation and additive manufacturing practices that migrate to higher-volume airliners.
Commercial operators will continue to dominate procurement volumes, but military programs will account for a larger share of R&D spending, particularly in corrosion-resistant alloys and automatic retraction diagnostics. As blended-wing-body demonstrators proceed, gear-position loads shift, encouraging spring-strut innovations that military prototypes often adopt first. The spillover accelerates technology maturity, shortening the time to commercial adoption and supporting the broader aircraft landing gear systems market.
Note: Segment shares of all individual segments available upon report purchase
By Gear Position: Main gear holds mass, nose gear innovates
Main undercarriage units sustained 63.45% of the aircraft landing gear systems market share in 2024, reflecting their structural heft, complex truck assemblies, and high-value brake packs. Twin-aisle designs can impose landing weights above 560 tons, demanding robust heat-treated steels, redundant shock absorbers, and multi-wheel bogies. Digital brake-by-wire upgrades and carbon/carbon discs keep repair shops busy, sustaining aftermarket revenues at every A-check cycle.
Nose gear volumes are lower, yet growth is stronger, tracking a 9.55% CAGR to 2030. Electric steering actuators spearhead weight cuts, and modular electro-mechanical jackscrew assemblies slash line-replaceable-unit counts. Clean Aviation’s nose-gear demonstrator validates electro-hydrostatic retraction methods that can shave several kilograms per shipset. Business-jet makers are early adopters; Liebherr’s high-reliability nose-gear prototype, unveiled at NBAA-BACE 2024, positions the company to capture both eVTOL and regional-jet awards.
By Material: Steels still rule, composites surge
High-strength steels such as 300M and AerMet held 46.75% market share in 2024 because they withstand high landing loads and simplify qualification. The segment continues to benefit from established hot-forging lines and known fatigue curves. Yet, composites are on the fastest trajectory with a 10.45% CAGR. Carbon-fiber shafts and yokes cut weight without sacrificing stiffness, and automated-fiber-placement machines now produce repeatable thick-section laminates suitable for primary gear beams. Tohoku University’s super-elastic Ti-Al alloy shows promise for temperature-extreme landings, while hybrid lay-ups pair CFRP with metallic inserts to ease bolting interfaces.
Steel suppliers are responding by offering vacuum-melt variants with better corrosion resistance. Still, certification of composite main-gear beams on large transports remains the milestone that would spur mass adoption and tilt share beyond 2030.
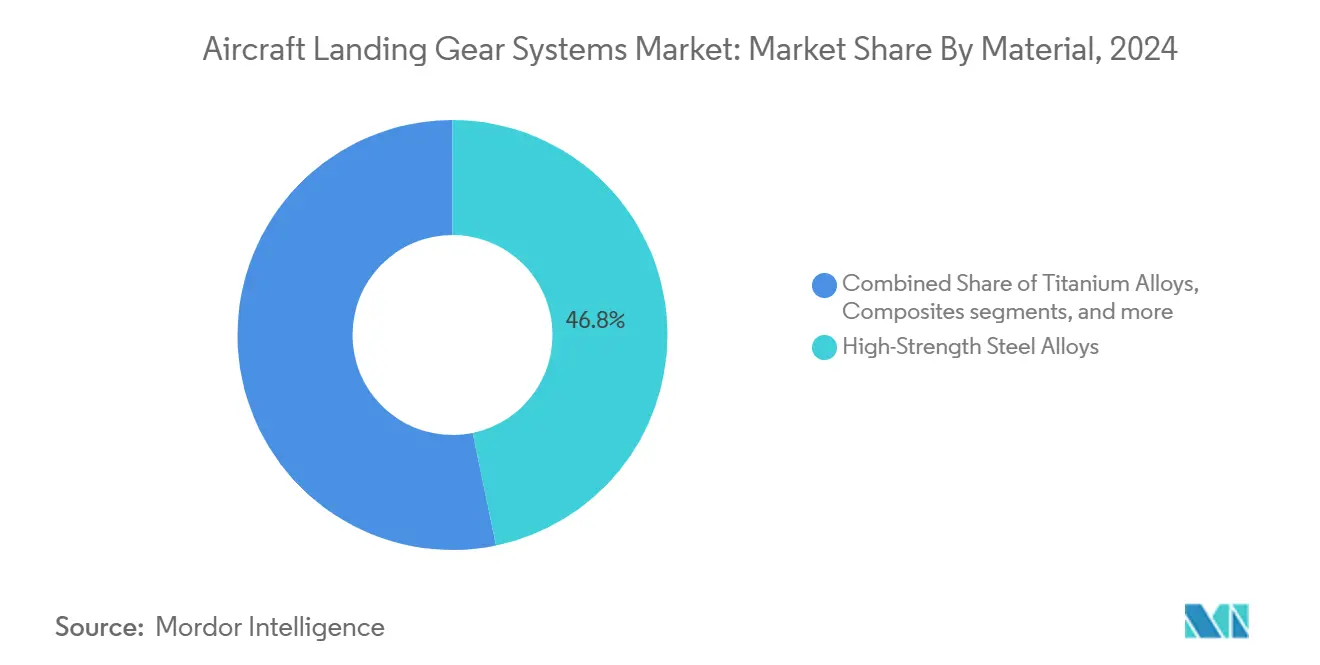
Note: Segment shares of all individual segments available upon report purchase
By End User: OEM share solid, aftermarket momentum builds
Airframe factories captured 68.35% of 2024 revenue as Boeing and Airbus worked through unprecedented order books. Each narrowbody requires two or three shipsets during development and flight-test phases, multiplying near-term demand. Nevertheless, services bring the stickier margin: airlines increasingly choose pay-as-you-fly models that bundle rotable pools, logistics, and engineering support. The aftermarket is forecast to deliver an 8.78% CAGR as fleets expand and gear overhaul cycles peak every 8-10 years. GA Telesis’s purchase of AAR’s gear-overhaul operation and Héroux-Devtek’s private-equity buy-out show capital rotating into long-term service plays.
Independent MROs still carve out space by offering quicker turn-times and tailoring contracts for regional carriers that cannot afford OEM rates. Digital twins cut downtime further, enabling maintenance deferral decisions while staying within airworthiness limits and preserving residual asset values.
Geography Analysis
North America remained the largest regional contributor with 37.89% of 2024 revenue. Boeing’s Renton and Everett lines, Collins’s Spokane brake factory, and Pratt & Whitney landing-gear machining centers anchor a dense supplier footprint that feeds civil and defense orders. US defense budgets guarantee high-tempo overhauls, and the emerging air-mobility ecosystem centred in California and Texas will soon require thousands of lightweight shipsets. Regulatory scrutiny, including a 2024 FAA probe into counterfeit titanium, has tightened oversight, nudging primes to in-source more metallurgical testing.
Asia-Pacific is the fastest-expanding arena, rising at an 8.32% CAGR on the back of burgeoning traffic in China, India, and Southeast Asia. Airbus forecasts that the region will absorb 45% of global jet deliveries over two decades, and COMAC’s C919 certification accelerates indigenous supply chains. China’s carbon-fiber output remains skewed to industrial grades, encouraging joint ventures with international prepreg specialists. Japan and South Korea, with long aerospace pedigrees, are scaling super-plastic-forming operations that support regional jet and fighter programs.
Europe retains a strong technology edge, housing Safran Landing Systems, Liebherr-Aerospace, and major Airbus plants. EU sustainability mandates incentivise electrification roadmaps and life-cycle impact disclosures for landing-gear hardware. Eastern European clusters in Poland and the Czech Republic attract investment for precision-machined sub-assemblies. Middle-East, Latin American, and African operators form smaller but strategic nodes, leveraging geographic positioning to serve long-haul hub-and-spoke networks and charter segments that require flexible MRO availability.
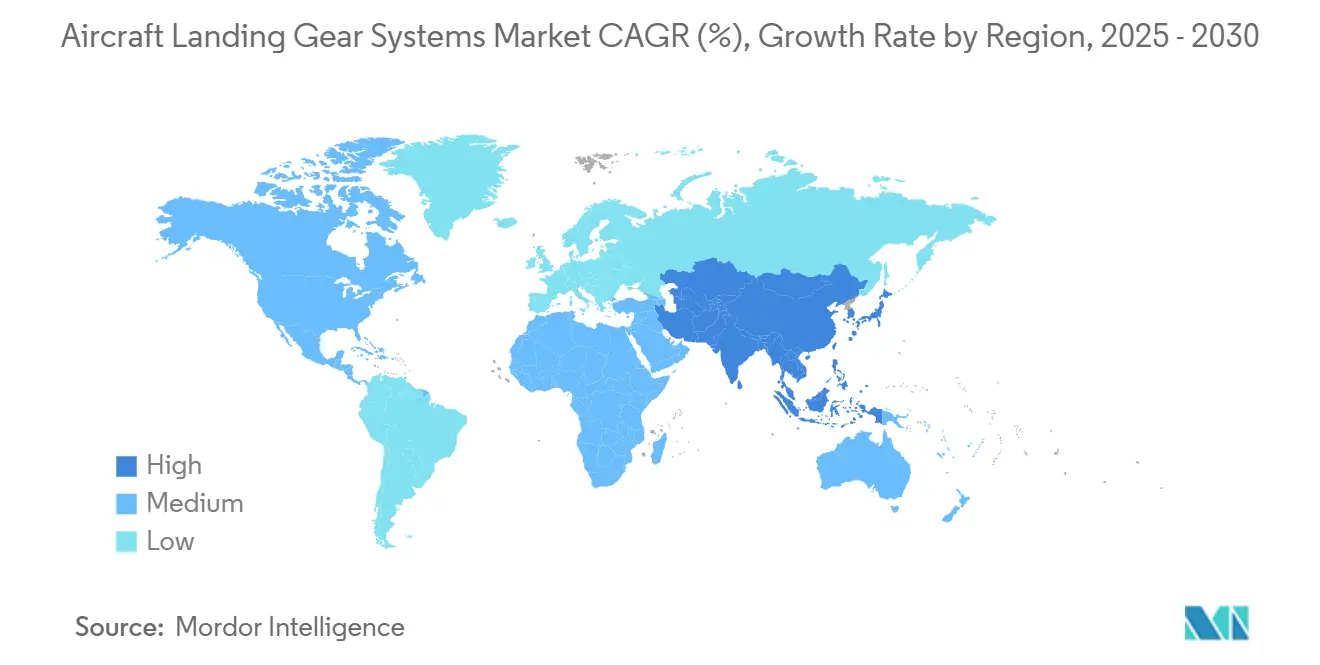
Competitive Landscape
Safran Landing Systems (Safran SA) leads the aircraft landing gear systems market, equipping more than 33,000 aircraft worldwide and ramping A320 outputs by 36% in 2024. Collins Aerospace follows closely, channelling USD 200 million into Spokane to widen carbon-brake lines. Liebherr-Aerospace reinvests over 17% of annual turnover into R&D, cementing positions on the Airbus A320neo family and Boeing B777X. Héroux-Devtek’s private-equity sale underscores market confidence in specialist machining and aftermarket contracts, while Triumph and GKN Aerospace supply critical actuators and composite fittings.
Competition is shifting from metal-cutting capacity to digital-service propositions: predictive analytics, remote-support AR, and rotable pools. OEMs are bundling these into long-term service agreements that extract revenue across the 30-year airframe life. At the same time, start-ups focused on eVTOL applications partner with traditional houses for certification know-how, extending incumbents’ relevance into new mobility ecosystems.
Aircraft Landing Gear Systems Industry Leaders
-
Safran SA
-
Honeywell International Inc.
-
Collins Aerospace (RTX Corporation)
-
Héroux-Devtek
-
Liebherr Group
- *Disclaimer: Major Players sorted in no particular order
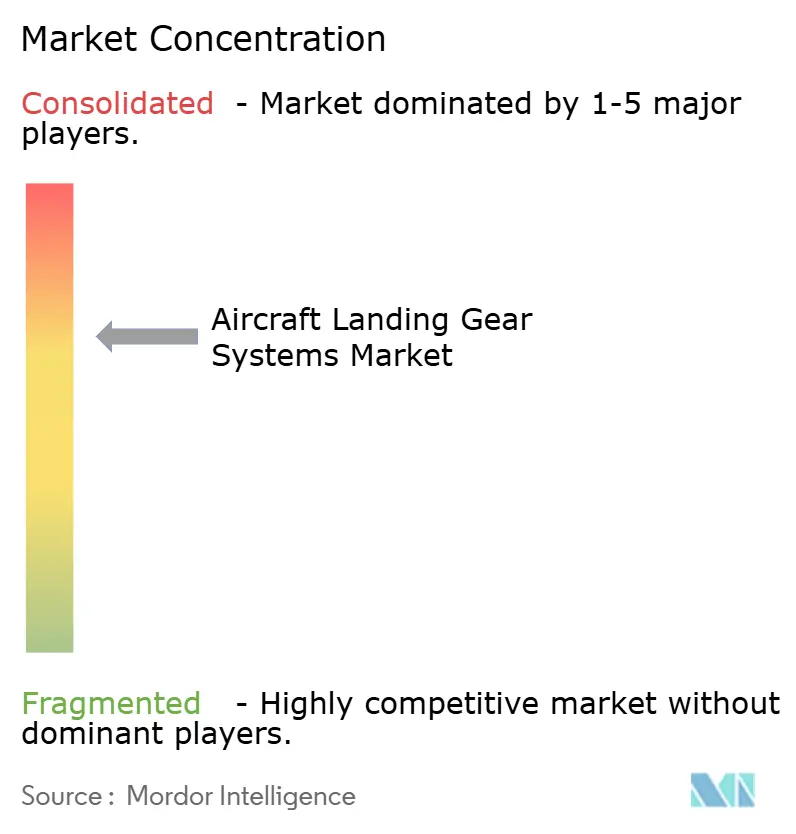
Recent Industry Developments
- June 2025: Revima broadened its maintenance capabilities to encompass newer Airbus aircraft models, thanks to an extended partnership with Safran Landing Systems, focusing on landing gear aftermarket services.
- June 2025: Dublin Aerospace secured a three-year contract with Las Vegas-based Allegiant Air. The agreement tasks Dublin Aerospace with overhauling and repairing landing gear systems for Allegiant Air's more than 100-aircraft Airbus A320 family fleet.
- March 2025: Liebherr-Aerospace Saline in Michigan agreed with SkyWest Airlines to provide landing gear overhaul and systems maintenance for a portion of SkyWest's Embraer 175-E1 fleet.
- January 2025: Air Industries Group received a USD 2.6 million contract to manufacture main landing gear assemblies for the US Navy E-2D Advanced Hawkeye aircraft.
Global Aircraft Landing Gear Systems Market Report Scope
The aircraft landing gear systems market has been segmented by aircraft type into commercial aviation, military aviation, general aviation, and by gear position into nose, and undercarriage. The report also covers the market sizes and forecasts for the aircraft landing gear systems market in major countries across different regions. For each segment, the market sizing and forecasts have been provided in value (USD billion).
By Aircraft Type | Commercial Aviation | Narrowbody Aircraft | ||
Widebody Aircraft | ||||
Regional Aircraft | ||||
Military Aviation | Combat Aircraft | |||
Non-Combat Aircraft | ||||
Helicopters | ||||
General Aviation | Business Jets | |||
Turboprop Aircraft | ||||
Piston Aircraft | ||||
Helicopters | ||||
By Gear Position | Nose Landing Gear | |||
Main/Undercarriage Landing Gear | ||||
By Material | High-Strength Steel Alloys | |||
Titanium Alloys | ||||
Composites (CFRP/GFRP) | ||||
Aluminum Alloys | ||||
By End-User | OEM | |||
Aftermarket (MRO) | ||||
By Geography | North America | United States | ||
Canada | ||||
Mexico | ||||
Europe | United Kingdom | |||
France | ||||
Germany | ||||
Russia | ||||
Rest of Europe | ||||
Asia-Pacific | China | |||
Japan | ||||
India | ||||
Rest of Asia-Pacific | ||||
South America | Brazil | |||
Rest of South America | ||||
Middle East and Africa | Middle East | United Arab Emirates | ||
Saudi Arabia | ||||
Egypt | ||||
Rest of Middle East | ||||
Africa | South Africa | |||
Rest of Africa |
Commercial Aviation | Narrowbody Aircraft |
Widebody Aircraft | |
Regional Aircraft | |
Military Aviation | Combat Aircraft |
Non-Combat Aircraft | |
Helicopters | |
General Aviation | Business Jets |
Turboprop Aircraft | |
Piston Aircraft | |
Helicopters |
Nose Landing Gear |
Main/Undercarriage Landing Gear |
High-Strength Steel Alloys |
Titanium Alloys |
Composites (CFRP/GFRP) |
Aluminum Alloys |
OEM |
Aftermarket (MRO) |
North America | United States | ||
Canada | |||
Mexico | |||
Europe | United Kingdom | ||
France | |||
Germany | |||
Russia | |||
Rest of Europe | |||
Asia-Pacific | China | ||
Japan | |||
India | |||
Rest of Asia-Pacific | |||
South America | Brazil | ||
Rest of South America | |||
Middle East and Africa | Middle East | United Arab Emirates | |
Saudi Arabia | |||
Egypt | |||
Rest of Middle East | |||
Africa | South Africa | ||
Rest of Africa |
Key Questions Answered in the Report
What is the current value of the aircraft landing gear systems market?
The market is valued at USD 11.82 billion in 2025 and is projected to reach USD 17.46 billion by 2030, advancing at an 8.11% CAGR.
Which aircraft segment leads demand for landing-gear systems?
Commercial narrowbody jets account for 43.55% of 2024 revenue, reflecting their large installed base and high production rates.
Which region is growing fastest?
Asia-Pacific is forecasted to expand at an 8.32% CAGR through 2030, powered by fleet growth in China and India.
How are airlines reducing landing-gear maintenance costs?
Carriers increasingly rely on exchange pools and power-by-the-hour contracts that turn heavy capex into predictable service fees.
What materials are seeing the strongest growth in landing-gear applications?
Composite components are expected to post a 10.45% CAGR due to weight-saving and fatigue-resistance advantages.
How will eVTOL aircraft affect the landing-gear market?
Urban-air-mobility (UAM) programs create a new sub-segment for lightweight, high-cycle gear sets, spurring partnerships between legacy suppliers and start-ups.
Page last updated on: June 26, 2025