Metal Coatings Market Size and Share
Metal Coatings Market Analysis by Mordor Intelligence
The Metal Coatings Market size is estimated at USD 13.96 billion in 2025, and is expected to reach USD 17.89 billion by 2030, at a CAGR of 5.09% during the forecast period (2025-2030). This trajectory highlights the sector’s resilience despite tighter air-quality rules, volatile feedstock prices, and shifting customer requirements. Regulatory bodies in North America, Europe, and Asia-Pacific are enforcing lower volatile-organic-compound (VOC) thresholds, prompting rapid reformulation but also opening opportunities for water-borne and energy-curable systems. Demand expands in tandem with infrastructure renewal in developed economies, electrification of transport fleets, and a surge in offshore wind power installations. Technology suppliers are meeting these needs with hybrid curing chemistries, self-healing binders, and digital process controls that promise both performance and sustainability gains.
Key Report Takeaways
- By resin type, epoxy dominated with 39.17% metal coatings market share in 2024 and specialty “other resins” are forecast to grow at 6.85% CAGR.
- By technology, solvent-borne systems retained 47.66% revenue share in 2024, while UV-cured coatings are set to advance at 6.45% CAGR to 2030.
- By application, protective coatings will outpace all others at 6.59% CAGR, whereas architectural coatings accounted for 40.24% of 2024 revenues.
- By geography, Asia-Pacific controlled 46.92% metal coatings market share in 2024; North America registers the fastest regional expansion at a projected 6.36% CAGR through 2030.
Global Metal Coatings Market Trends and Insights
Drivers Impact Analysis
Driver | (~) % Impact on CAGR Forecast | Geographic Relevance | Impact Timeline |
---|---|---|---|
Stringent Volatile Organic Compound (VOC) Regulations Boosting Water-Borne Technologies | +1.2% | North America, European Union, China | Medium term (2-4 years) |
Rising Infrastructure Renewal in Developed Economies | +0.8% | North America, EU, Japan | Long term (≥ 4 years) |
Expanding Automotive Production Volume | +0.9% | Asia-Pacific, North America | Medium term (2-4 years) |
Offshore Wind Installations Demanding High-Performance Anti-Corrosion Systems | +0.6% | North America, EU coastal areas, emerging APAC | Long term (≥ 4 years) |
Surge in Coil-Coated Aluminium for Electric Vehicle Battery Enclosures | +0.7% | Global, led by China, North America, and EU | Short term (≤ 2 years) |
Source: Mordor Intelligence
Stringent Volatile Organic Compound (VOC) Regulations Boosting Water-Borne Technologies
New air-quality standards are accelerating a structural shift from solvent-borne to water-borne formulations. The United States Environmental Protection Agency amended National Volatile Organic Compound (VOC) Emission Standards for aerosol coatings in January 2025 and retained stricter limits while extending compliance to January 2027, giving producers a finite window to transition [1]Environmental Protection Agency, “National Volatile Organic Compound Emission Standards for Aerosol Coatings: Final Rule,” epa.gov. California’s South Coast Air Quality Management District tightened Rule 1151 limits for automotive refinishes in May 2025, and industry observers expect similar caps to cascade into adjacent segments. Canada enforced Volatile Organic Compound (VOC) concentration limits across 130 product categories in January 2025, illustrating the breadth of the trend. These mandates reward suppliers that possess mature water-borne platforms and scalable production assets. Although water-borne systems now rival solvent-borne performance in many indoor and light-industrial uses, they still require meticulous surface preparation and more stringent humidity control during application.
Rising Infrastructure Renewal in Developed Economies
Large-scale refurbishment of bridges, ports, and energy infrastructure sustains demand for high-performance protective coatings across North America and Europe. The United States offshore-wind development pipeline surpassed 52 GW in early 2025, and state policies target 112 GW by 2030, driving uptake of 25-30 year anti-corrosion paint systems. Three-coat epoxy-polyurethane schemes with 660 µm dry-film thickness have delivered 15+ year field service, becoming de-facto specifications for steel monopiles and transition pieces. Infrastructure owners increasingly favor predictive-maintenance tools, and smart coatings able to signal degradation are entering pilot deployment.
Expanding Automotive Production Volume
Global automotive assembly rebounded in 2025, led by electric-vehicle (EV) platforms that use more aluminum and require bespoke thermal-management coatings. Honda committed CAD 15 billion to build an integrated EV complex in Ontario, underpinning orders for electrocoats, low-temperature topcoats, and battery-pack sealants. PPG invested USD 30 million in a dedicated battery-coating application center in Tianjin to capture similar EV demand in China. Research indicates that corrosion of aluminum current collectors can trigger capacity losses exceeding 20% in lithium-ion cells, spurring the development of advanced passivation layers.
Offshore Wind Installations Demanding High-Performance Anti-Corrosion Systems
Growth in offshore wind capacity creates a specialized need for coatings able to endure cyclic salt spray, abrasion, and ultraviolet radiation for three decades. Hempel introduced Hempaguard Ultima, a silicone-based fouling-release finish that extends maintenance intervals for foundation structures and support vessels. Academic studies have identified more than 200 chemical emissions from coating and anode systems on offshore turbines, compelling suppliers to formulate compliant yet robust products. Self-healing epoxy networks incorporating microencapsulated inhibitors are gaining traction to reduce lifetime maintenance expenditure.
Restraints Impact Analysis
Restraint | (~) % Impact on CAGR Forecast | Geographic Relevance | Impact Timeline |
---|---|---|---|
Volatile Feedstock Prices | -1.1% | Global, with strongest impact in emerging markets | Short term (≤ 2 years) |
Compliance Cost of Solvent-Borne Volatile Organic Compound (VOC) Limits in Emerging Nations | -0.7% | Emerging markets in APAC, Latin America, and MEA | Medium term (2-4 years) |
Challenges Associated with Harsh Operational Environment | -0.4% | Global, concentrated in marine and industrial applications | Long term (≥ 4 years) |
Source: Mordor Intelligence
Volatile Feedstock Prices
Metal-coating producers face margin compression as aluminum, copper, and zinc prices remain elevated due to green-energy demand and geopolitical tensions. The World Bank projects base-metal average prices to stay above the 2019-2021 levels through 2025 [2]World Bank, “Commodity Markets Outlook 2025,” worldbank.org . Titanium dioxide, the largest single cost item in many formulations, saw Chinese capacity climb toward 7 million tons in 2025, exerting downward pressure on pigment margins while introducing quality-consistency concerns for buyers. Energy-intensive smelters in Europe curtailed output during 2024, adding supply risk and forcing converters to adjust inventory policies.
Compliance Cost of Solvent-Borne Volatile Organic Compound (VOC) Limits in Emerging Nations
Regulatory convergence imposes financial burdens on manufacturers in price-sensitive regions. Indonesia’s coatings market is forecast to expand at 6.47% annually to USD 4.24 billion by 2030, yet smaller local firms must spend disproportionate capital on new spray booths, abatement systems, and worker training to meet tougher VOC limits. Chinese steel exports surged 36.2% in 2023 and have displaced some domestic output in Southeast Asia, adding competitive pressure for compliant coatings. Access to low-VOC binders and UV-curable lines often hinges on licensing agreements with multinationals, reinforcing consolidation trends.
Segment Analysis
By Resin Type: Epoxy’s Broad Base Meets Specialty Resin Upswing
Epoxy resins generated the largest share of 2024 revenue at 39.17% on the strength of unmatched adhesion and chemical resistance in marine and heavy-industrial service. The segment continues to benefit from innovations such as nanoscale fillers that improve barrier properties, while quantum-dot photoinitiators extend ultraviolet stability. At the same time, specialty “other resins” comprising acrylic, fluoropolymer, and siloxane hybrids are the fastest-growing category at 6.85% CAGR as builders, automakers, and renewable-energy operators demand tailored features such as self-cleaning, ice-phobic, and heat-dissipation attributes. Bio-based resin chemistries derived from plant oils and algal biomass are also gaining pilot-scale adoption in architectural topcoats and appliance finishes. Combined, these trends reinforce epoxy’s central role while widening the choice set for end users seeking targeted performance without sacrificing sustainability.
The competitive landscape for resins is diversifying as polyurethane chemistries carve out space in automotive plastics and polyester maintains cost leadership in building facades. Suppliers of advanced curing agents promote thiol-epoxy networks activated by near-infrared light, achieving over 90% conversion in films thicker than 2.5 cm and opening doors for heavy-equipment refinish. In parallel, polyaspartic systems allow accelerated return-to-service for bridges and parking structures. These developments position the resin category to capture incremental value through both traditional bulk volumes and premium niche solutions, underpinning a balanced growth outlook for the overall metal coatings market.
Note: Segment shares of all individual segments available upon report purchase
By Technology: Solvent-Borne Holds Ground While Ultraviolet (UV)-Cured Gains Speed
Solvent-borne coatings commanded 47.66% of 2024 revenue, proving that many industrial users still rely on robust wetting, long pot life, and adhesion to weathered substrates. The technology’s entrenched application infrastructure and tolerant processing windows sustain demand in sectors from oil-and-gas to heavy machinery. Nevertheless, UV-cured lines are projected to expand at 6.45% CAGR, the fastest among technologies, propelled by zero-VOC credentials, rapid-line speeds, and falling capital cost of LED lamps. Producers such as PPG introduced energy-curable metal topcoats that achieve full properties without bake ovens, reducing utility loads by up to 40% [3]PPG Industries, “PPG Introduces Energy-Curable Metal Coatings,” ppg.com.
Water-borne systems continue to gain regulatory favor in Europe and North America yet face adoption barriers in humid tropical regions where drying windows narrow. Powder coatings deliver near-100% material utilization and are penetrating agricultural equipment, metal furniture, and appliance housings. Hybrid innovations blur boundaries: UV-curable powder delivers the solvent-free advantage of powder with the speed of photo-activation, while laser curing slashes bake times for conventional formulations. Taken together, these technology choices allow customers to align performance, sustainability, and cost constraints, reinforcing the diverse yet competitive fabric of the metal coatings market.
By Application: Architectural Scale Meets Protective Premium
Architectural coatings accounted for 40.24% of total 2024 value, buoyed by renovation cycles in North America and Europe and green-roof metal adoption across Asia. Yet protective coatings are the star performer, forecast to grow at 6.59% CAGR as offshore wind, wastewater treatment, and petrochemical assets specify long-life, high-film-build paint systems. Operators accept higher upfront spend in exchange for reduced lifetime maintenance, a trend that lifts unit pricing and margins. Automotive applications, influenced by EV architecture, rely on coil-coated aluminum battery enclosures and low-temperature electrocoats that lower energy use in paint shops.
Marine coatings grapple with evolving biocide restrictions; silicone-fouling-release matrices and self-polishing polymers fill the regulatory vacuum. General industrial uses—from compressors to lawn equipment—favor powder and water-borne technologies for their finish quality and environmental profile. Emerging niches include solar-tracker structures and hydrogen pipeline internals, both demanding tailored corrosion protection. In aggregate, these patterns confirm a pivot from volume-driven sectors toward mission-critical, value-added applications, further enlarging the addressable metal coatings market size for innovators.
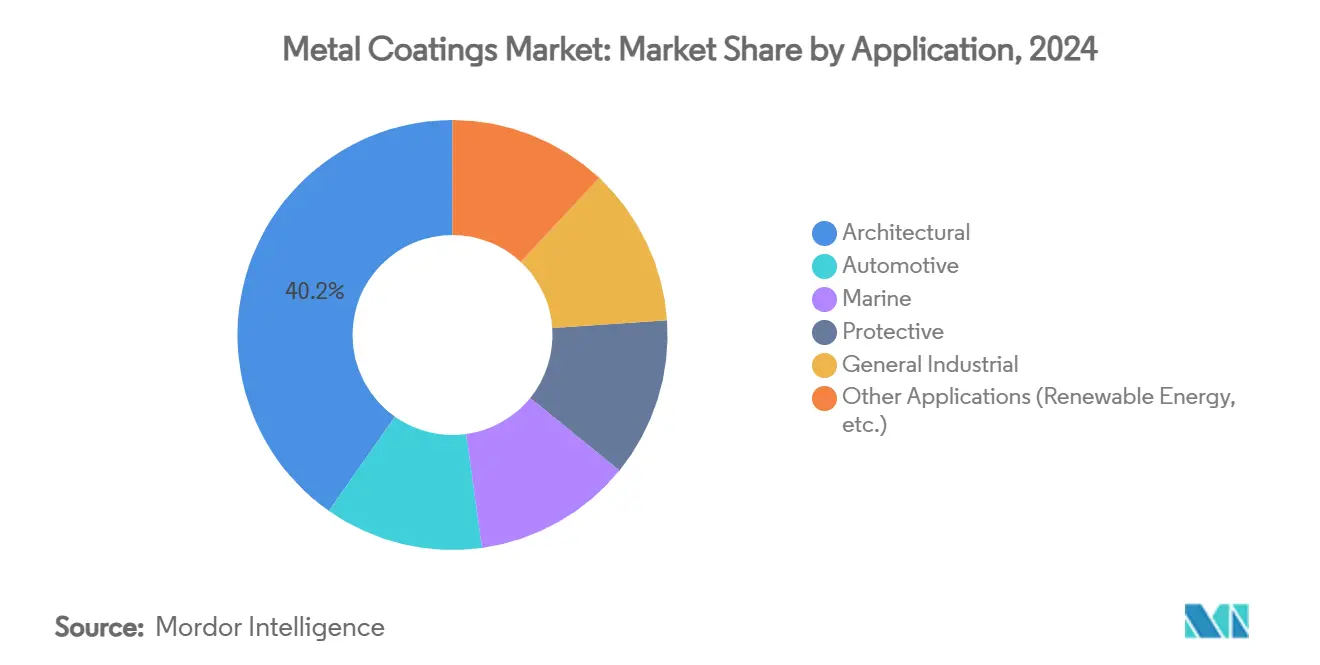
Note: Segment shares of all individual segments available upon report purchase
Geography Analysis
Asia-Pacific retained leadership with 46.92% revenue in 2024 and is projected to advance at 6.36% CAGR through 2030. China’s decision to raise steel exports by 36.2% during 2023 sustains local consumption of conversion and coil coatings even as domestic demand levels fluctuate. India’s roadmap to triple steel-making capacity to 500 million tons by 2047 underpins vast downstream opportunities; the country already targets a reduction of carbon-intensity to 2.25 tons CO₂ per ton of crude steel, incentivizing adoption of high-solid and water-borne formulations. Regional titanium-dioxide capacity nears 7 million tons, supporting vertical integration for Chinese and Japanese producers but also sharpening quality competition. Indonesia illustrates the broader arc: its coatings value is set to reach USD 4.24 billion by 2030 as legislation phases out lead and institutes VOC fees.
North America maintains a solid demand base across infrastructure and transportation. The United States aims for 112 GW of installed offshore wind by 2030, driving procurement of glass-flake epoxies and advanced primers that guarantee 25-year lifetimes in splash-zone environments. Federal and state incentives for domestic EV production have unlocked multi-billion-dollar capital programs, translating to orders for low-bake cathodic electrocoats and insulating battery-pack coatings. Mexico’s emergence as a near-shoring hub spurred AkzoNobel to expand coil lines in Nuevo León by 35% capacity in 2024, signaling expectations of sustained automotive output growth.
Europe balances high energy costs with stringent sustainability mandates. BASF’s ongoing strategic review of its USD 6.8 billion coatings division shows how energy volatility influences portfolio decisions. Meanwhile, Hempel’s EUR 2,185 million revenues in 2024 underscore the resilience afforded by premium marine and protective technologies. Offshore wind in the North Sea remains a powerhouse for ultra-durable systems, with three-coat epoxy-polyurethane specifications serving as the gold standard. Aerospace primes and topcoats migrate to chrome-free alternatives to satisfy European Aviation Safety Agency requirements. Circular-economy policies drive R&D on bio-derived resins and recyclable packaging, reinforcing Europe’s role as a crucible for future coating science.
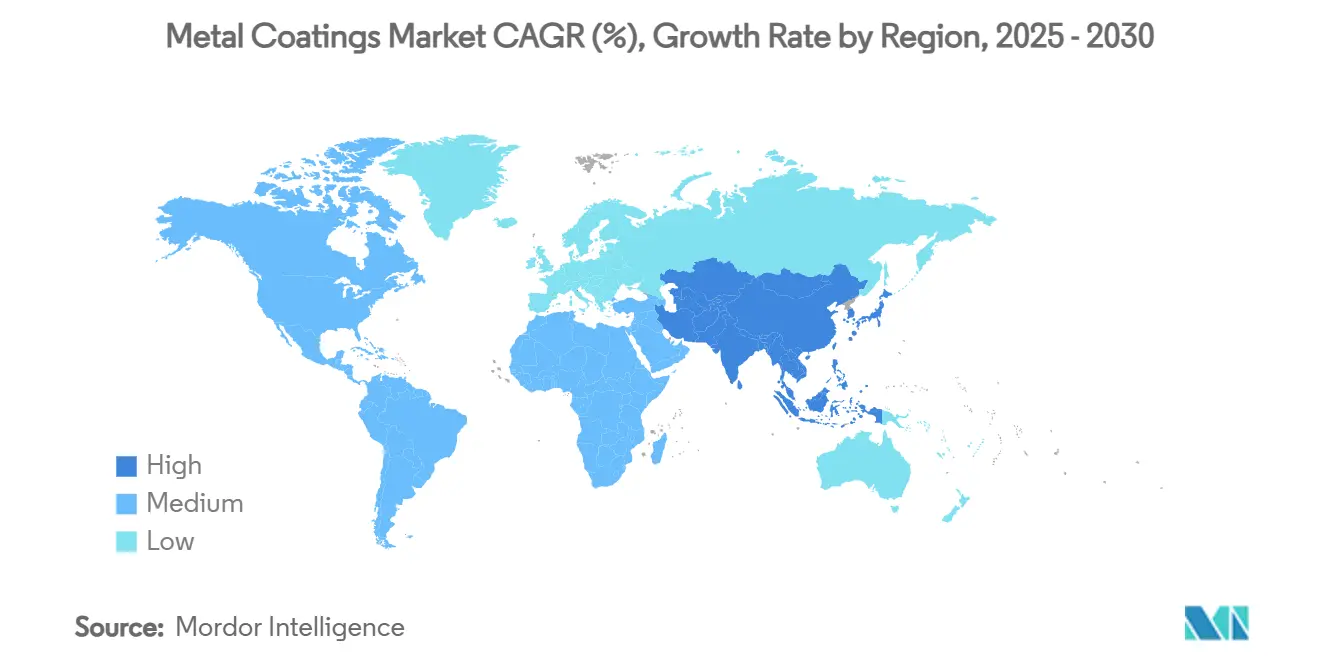
Competitive Landscape
The metal coatings market exhibits moderate concentration with established players, such as PPG Industries, Inc., AkzoNobel N.V., The Sherwin-Williams Company, Axalta Coating Systems LLC, and Nippon Paint Holdings Co., Ltd., pursuing aggressive expansion strategies while facing pressure from emerging technologies and regulatory compliance costs. Strategic mergers underscore the pivot toward scale and specialization. AkzoNobel plowed USD 70 million into North American facilities and another USD 3.6 million into Mexican coil-coating lines to secure supply against demand spikes.
Metal Coatings Industry Leaders
-
Axalta Coating Systems, LLC
-
The Sherwin-Williams Company
-
Akzo Nobel N.V.
-
PPG Industries, Inc.
-
Nippon Paint Holdings Co., Ltd.
- *Disclaimer: Major Players sorted in no particular order
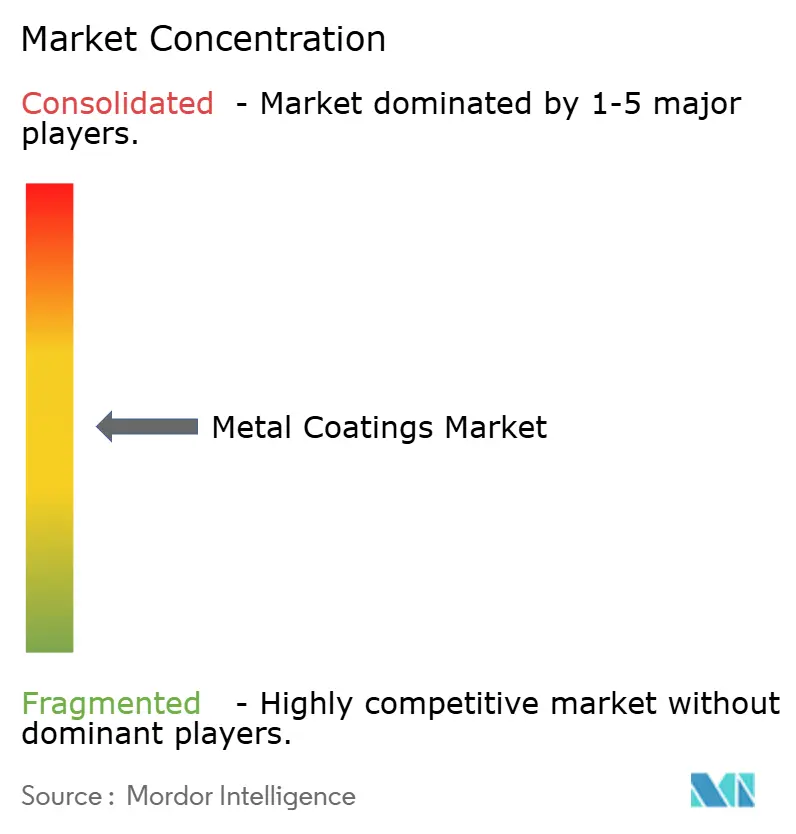
Recent Industry Developments
- July 2024: Axalta Coating Systems, LLC completed its acquisition of the CoverFlexx Group for USD 285 million, specializing in coatings for automotive refinish and aftermarket applications.
- June 2024: Akzo Nobel N.V.invested USD 3.6 million to boost its coil and extrusion coatings production in Garcia, Mexico. The expansion follows a USD 70 million investment in other North American facilities.
Global Metal Coatings Market Report Scope
Metal coatings are chemicals used for metallic surfaces for functional properties such as anti-corrosion, anti-slip surface, anti-bacterial, etc. The metal coatings market is segmented by resin type, technology, application, and geography. The market is segmented by resin type into epoxy, polyester, polyurethane, and other resin types. The market is segmented by technology into water-borne, LED curing, solvent-borne, powder, and UV cured. The market is segmented by application into architectural, automotive, marine, protective, general industrial, and other applications. The report also covers the market size and forecasts for the UV curable adhesives market in 17 countries across major regions. The report offers market size and forecasts for the calcium oxide market in revenue (USD million) for all the above segments.
By Resin Type | Epoxy | ||
Polyester | |||
Polyurethane | |||
Other Resin Types (Acrylic, Fluoropolymer, etc.) | |||
By Technology | Water-borne | ||
Solvent-borne | |||
Powder | |||
Ultraviolet (UV)-Cured | |||
Light Emitting Diode (LED) Curing | |||
By Application | Architectural | ||
Automotive | |||
Marine | |||
Protective | |||
General Industrial | |||
Other Applications (Renewable Energy, etc.) | |||
By Geography | Asia-Pacific | China | |
Japan | |||
India | |||
South Korea | |||
Thailand | |||
Malaysia | |||
Phillipines | |||
Vietnam | |||
Singapore | |||
Rest of Asia-Pacific | |||
North America | United States | ||
Canada | |||
Mexico | |||
Europe | Germany | ||
United Kingdom | |||
France | |||
Italy | |||
Spain | |||
Russia | |||
NORDIC Countries | |||
Turkey | |||
Rest of Europe | |||
South America | Brazil | ||
Argentina | |||
Colombia | |||
Rest of South America | |||
Middle East and Africa | Saudi Arabia | ||
South Africa | |||
United Arab Emirates | |||
Egypt | |||
Qatar | |||
Nigeria | |||
Rest of Middle East and Africa |
Epoxy |
Polyester |
Polyurethane |
Other Resin Types (Acrylic, Fluoropolymer, etc.) |
Water-borne |
Solvent-borne |
Powder |
Ultraviolet (UV)-Cured |
Light Emitting Diode (LED) Curing |
Architectural |
Automotive |
Marine |
Protective |
General Industrial |
Other Applications (Renewable Energy, etc.) |
Asia-Pacific | China |
Japan | |
India | |
South Korea | |
Thailand | |
Malaysia | |
Phillipines | |
Vietnam | |
Singapore | |
Rest of Asia-Pacific | |
North America | United States |
Canada | |
Mexico | |
Europe | Germany |
United Kingdom | |
France | |
Italy | |
Spain | |
Russia | |
NORDIC Countries | |
Turkey | |
Rest of Europe | |
South America | Brazil |
Argentina | |
Colombia | |
Rest of South America | |
Middle East and Africa | Saudi Arabia |
South Africa | |
United Arab Emirates | |
Egypt | |
Qatar | |
Nigeria | |
Rest of Middle East and Africa |
Key Questions Answered in the Report
What is the current size of the metal coatings market?
The metal coatings market size is estimated to be USD 13.96 billion in 2025, with a projected value of USD 17.89 billion by 2030 at a 5.09% CAGR.
Which region leads global demand?
Asia-Pacific holds 46.92% of 2024 revenue and is forecast to grow at 6.36% CAGR through 2030, driven by infrastructure expansion and automotive production growth.
What technology segment is growing the fastest?
Ultraviolet (UV)-cured coatings are the fastest-growing technology, expanding at 6.45% CAGR as manufacturers seek rapid processing, low energy use, and zero-Volatile Organic Compound (VOC) outcomes.
Why are protective coatings gaining importance?
Protective coatings benefit from infrastructure renewal and offshore wind installations that require 25-30 year durability, leading to the highest application-level CAGR of 6.59%.
How are regulations influencing product development?
Tighter VOC limits in North America, Europe, and parts of Asia are accelerating the shift toward water-borne, powder, and energy-curable systems, while also raising compliance costs for solvent-borne producers.
Page last updated on: May 21, 2025