Load Monitoring System Market Size and Share
Load Monitoring System Market Analysis by Mordor Intelligence
The Load Monitoring Systems Market is valued at USD 5.79 billion in 2025 and is forecast to reach USD 7.53 billion by 2030, expanding at a 5.40% CAGR. Demand is broadening from traditional crane safety into renewable-energy, battery-electric vehicle (BEV) assembly, and autonomous factories where predictive maintenance and regulatory compliance converge. Operators now specify platforms that combine certified load indication with edge analytics, creating new revenue pools for hybrid and intelligent systems. Analog and wired installations still dominate unit volumes, yet AI-driven, IoT-connected architectures capture the bulk of current capital expenditure. Competitive intensity is rising as global automation majors acquire software specialists to shorten time-to-market for integrated solutions. Asia-Pacific’s infrastructure boom, coupled with tightening OSHA and EU directives, anchors both current demand and future growth potential.
Key Report Takeaways
- By product category, load cells held 48.67% of the load monitoring systems market share in 2024, while software for data logging is projected to advance at a 7.2% CAGR through 2030.
- By load-cell capacity, systems rated above 20 tons captured 68.78% of the load monitoring systems market size in 2024; sub-20 ton units are set to grow at a 6.5% CAGR to 2030.
- By technology, analog platforms led with 55.65% revenue share in 2024, whereas hybrid and intelligent systems are poised for an 8.8% CAGR over the forecast horizon.
- By connectivity, wired architectures accounted for 67.54% of the load monitoring systems market in 2024; IoT-enabled solutions expand at a 10.3% CAGR.
- By industry, manufacturing and heavy equipment commanded 28.76% of the load monitoring systems market share in 2024, yet energy and utilities record the fastest 9.6% CAGR to 2030.
- By geography, Asia-Pacific held 38% of revenue in 2024 and is projected to compound at 7.3% annually through 2030.
Global Load Monitoring System Market Trends and Insights
Drivers Impact Analysis
Driver | % Impact on CAGR Forecast | Geographic Relevance | Impact Timeline |
---|---|---|---|
Tightening OSHA & EU lifting-safety mandates energizing certified load-monitoring adoption | +1.2% | North America & Europe, spillover to APAC | Medium term (2-4 years) |
Digital load cells enabling real-time monitoring of offshore wind turbine lifts | +0.9% | Global, concentrated in North Sea, East China Sea | Long term (≥ 4 years) |
Battery-electric vehicle pack assembly requiring high-precision force feedback | +0.8% | APAC core, expanding to North America & Europe | Medium term (2-4 years) |
Modular construction boom demanding synchronized multi-lift monitoring | +0.7% | Global, early adoption in North America & APAC | Short term (≤ 2 years) |
Integration of load sensors into predictive maintenance platforms | +0.6% | Global, led by industrial automation hubs | Short term (≤ 2 years) |
Hospital automation (patient-handling robotics) embedding smart load sensors | +0.5% | North America & Europe, emerging in APAC | Long term (≥ 4 years) |
Micro-grid deployment needing dynamic power-line tension monitoring | +0.4% | Global, accelerated in renewable-heavy regions | Medium term (2-4 years) |
Source: Mordor Intelligence
Tightening OSHA & EU Lifting-Safety Mandates Energizing Certified Load-Monitoring Adoption
Regulatory scrutiny is escalating as OSHA logged a surge in safety complaint forms from 68,896 to 94,529 in consecutive reporting periods, prompting construction and maritime operators to retrofit cranes with devices accurate within 95%–110% of actual load[1]Occupational Safety and Health Administration, “Commonly Used Statistics,” OSHA, osha.gov. EU directives mirror this stance, harmonizing standards and raising penalties for non-compliance. Insurers increasingly price premiums on documented sensor usage, pushing voluntary adoption toward compulsory rollout across high-risk sectors. Heightened enforcement thus redirects procurement toward systems that combine certified hardware with digital records, accelerating the replacement of obsolete analog indicators.
Digital Load Cells Enabling Real-Time Monitoring of Offshore Wind Turbine Lifts
Dual-axis shear pin sensors coupled with accelerometers now form the backbone of offshore lift supervision, preventing cable fatigue that can shut down multi-MW turbines[2]Caroline Evans, “Advanced Load-Cell Technology for Offshore Lifts,” Offshore Engineer, offshore-mag.com. Edge devices analyze vibration signatures locally, then forward anomalies through software-defined networks for fleet-wide visualization. Because a single cable failure risks multi-million-dollar revenue loss, operators prioritize predictive algorithms even at higher upfront cost. Uptake intensifies as installations move into deeper waters where manual inspections are unfeasible, cementing digital load cells as critical infrastructure for next-generation wind farms.
Battery-Electric Vehicle Pack Assembly Requiring High-Precision Force Feedback
Gigafactories rely on multi-axis sensors to verify weld force and alignment tolerances that affect cell longevity. Complementary instrumentation, mass-flow, pH, and conductivity feeds AI platforms such as Honeywell’s Battery Manufacturing Excellence software, which cuts material waste by 60% during start-up. At line speeds exceeding 120 ppm, failure-prediction analytics embedded in load monitoring systems reduce scrap and rework, anchoring their role in BEV cost competitiveness as more than 400 plants come online by 2030[3]Laura Martin, “Quality Control in Battery-Electric Vehicle Pack Welding,” Batteries, batteriesjournal.org.
Modular Construction Boom Demanding Synchronized Multi-Lift Monitoring
Prefabricated building techniques require several cranes to hoist modules simultaneously. Sensor suites measuring deflection, stress, wind force, and temperature transmit data every second, enabling supervisors to halt or resume lifts in real time. Vision systems, laser scanners, and encoders now merge with load cells to create 360-degree situational awareness. The convergence improves safety margins while trimming project schedules, prompting contractors to standardize multi-lift monitoring across high-rise and industrial builds.
Restraints Impact Analysis
Restraint | % Impact on CAGR Forecast | Geographic Relevance | Impact Timeline |
---|---|---|---|
High upfront cost of multi-axis retrofits for legacy cranes | -0.8% | Global, acute in cost-sensitive markets | Short term (≤ 2 years) |
Calibration drift & downtime in corrosive marine settings | -0.6% | Coastal regions, offshore operations | Medium term (2-4 years) |
Shortage of skilled personnel to interpret advanced load data | -0.5% | Global, acute in emerging markets | Long term (≥ 4 years) |
Fragmented certification schemes delaying cross-border approvals | -0.4% | Global, particularly EU-Asia trade corridors | Long term (≥ 4 years) |
Cyber-security risk in wireless load-monitoring for critical assets | -0.3% | Global, concentrated in critical infrastructure | Medium term (2-4 years) |
Source: Mordor Intelligence
High Upfront Cost of Multi-Axis Retrofits for Legacy Cranes
Multi-axis sensor packages, control-panel swaps, and operator training can push retrofit budgets beyond USD 100,000 per crane, forcing small and mid-size contractors to weigh capital outlay against regulatory penalties and insurance premiums. Downtime during installation compounds the hurdle because revenue-generating lifts pause while electrical rewiring and structural reinforcements take place. Financing options remain limited; most commercial lenders classify the upgrades as discretionary, so interest rates run higher than standard equipment loans. Vendors are responding with subscription models that bundle hardware, installation, and predictive-maintenance software under multi-year service agreements, but uptake is still concentrated among top-tier fleet owners. Until sensor prices fall or leasing spreads into smaller fleets, the high early-stage cash requirement will continue to damp adoption, shaving an estimated 0.8% from forecast CAGR.
Calibration Drift & Downtime in Corrosive Marine Settings
Salt spray, humidity, and temperature cycles foster sensor drift that compromises accuracy and forces unplanned recalibration stops. Research on offshore pressure transducers confirms that even pre-deployment pressurization cannot eliminate long-term drift in harsh seas[4]Daniel Young, “Long-Term Drift in Offshore Pressure Sensors,” Frontiers in Earth Science, frontiersin.org. Failures in mooring-line monitoring add repair costs and production delays. Newer systems apply corrosion-resistant alloys and hermetic seals, yet these features elevate purchase price. Operators thus calculate cost–benefit trade-offs closely, slowing adoption among smaller fleets.
Segment Analysis
By Product: Software Drives Digital Transformation
Load cells retained the largest 48.67% revenue slice of the load monitoring systems market in 2024, underscoring hardware’s foundational role in safety compliance. Indicators, controllers, and accessories sustain steady replacement volumes tied to crane refurbishment cycles. However, software for data logging, visualization, and analytics is set to grow at a 7.2% CAGR, becoming the sector’s revenue accelerant. Vendors embed machine-learning models that flag anomalous force signatures hours before failure, turning historical sensor data into actionable intelligence. Subscription licensing further stabilizes cash flows and strengthens customer lock-in.
Industrial Internet of Things integration fuels this trajectory by enabling centralized command centers that supervise global crane fleets from a single dashboard. Telemetry modules leveraging LTE-M and 5G backhaul reduce the cost of remote sites. As predictive-maintenance contracts proliferate, software revenues magnify each hardware sale, shifting competitive focus from component margins to lifecycle services within the load monitoring systems market.
By Load-Cell Capacity: Heavy-Duty Applications Dominate
Systems rated above 20 tons accounted for 68.78% of the load monitoring systems market size in 2024, a testament to heavy construction, mining, and shipyard requirements. These high-capacity platforms emphasize overload alarms and redundant circuitry to satisfy insurance mandates. Mid-range 20-100 ton devices serve generalized building and manufacturing activities, offering a balance of price and robustness. Sub-20 ton units, though smaller, deliver precision essential for BEV battery assembly, medical robotics, and electronics fabrication.
The sub-20 ton category posts the fastest 6.5% CAGR as lightweight cobots and patient-lifting equipment proliferate. Miniaturized multi-axis load cells capture deflection down to single-newton increments, enabling quality control for spot welds and ensuring patient safety in hospital settings. Vendors differentiate through material science innovations—such as titanium housings—to fight fatigue, thereby broadening adoption across industries where micrometer accuracy outweighs brute strength.
By Technology: Intelligence Transforms Legacy Systems
Analog circuitry continues to power 55.65% of installed bases owing to proven reliability and low maintenance. Yet customers seeking higher OEE migrate toward hybrid and intelligent platforms, projected to clock an 8.8% CAGR. Intelligent systems couple micro-electromechanical sensors with microprocessors executing pattern-recognition models that predict equipment fatigue well in advance, reducing unplanned downtime. Explainable AI modules clarify anomaly causes in natural language, shortening diagnostic cycles and easing operator training burdens.
Digital platforms occupy a transitional niche: they improve accuracy and data storage compared with analog options but lack autonomous analytics. Suppliers offer firmware upgrades to protect installed investments and create upsell pathways to full intelligence. The technology spectrum within the load monitoring systems market, therefore, reflects a stair-step adoption curve that allows phased modernization without wholesale asset replacement.
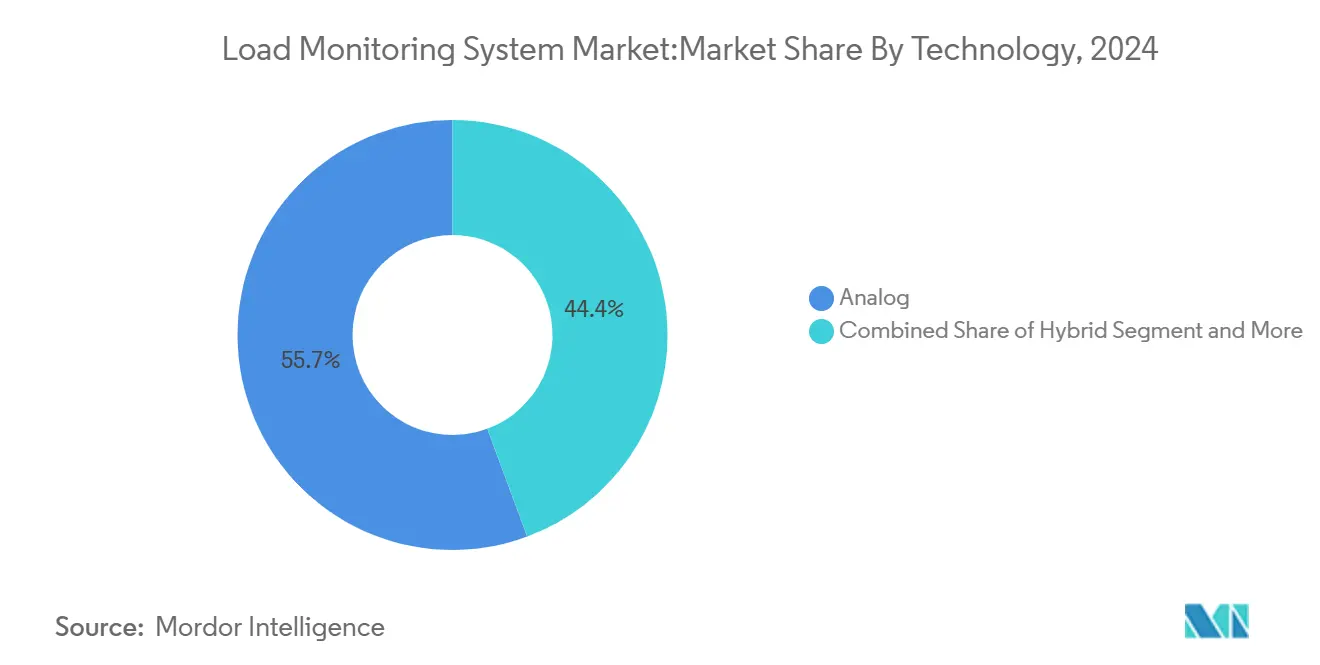
By Connectivity: IoT Revolution Accelerates
Wired configurations delivered 67.54% of 2024 shipments, prized for immunity to radio frequency interference and intrinsic cybersecurity. Nonetheless, IoT-enabled devices will grow 10.3% annually as cloud dashboards, edge computing, and 5G converge. Wireless solutions powered by energy harvesting, such as Sentient Energy’s MM3 line sensor, eliminate battery swaps and lower total cost of ownership. Utilities now integrate smart meters with cellular modules to perform remote firmware updates and demand forecasting, showcasing how connectivity extends beyond load measurement into broader grid intelligence.
Cyber-security remains a gating factor. Operators implement zero-trust architectures, multi-factor authentication, and encrypted MQTT protocols to mitigate hacking risks. Training programs align with NIST and IEC 62443 frameworks, reinforcing confidence in wide-area deployments. As barriers fall, connected architectures unlock new service models such as monitoring-as-a-service, converting one-time equipment sales into recurring revenue streams across the load monitoring systems market.
By Industry: Energy Sector Leads Growth
Manufacturing, heavy equipment, and industrial automation generated 28.76% of 2024 revenue, capitalizing on ongoing factory digitalization. Yet energy and utilities will outpace all verticals with a 9.6% CAGR, reflecting the urgency to integrate turbines, solar trackers, and hydro gates safely into power grids. Offshore wind farms embed load sensors into nacelle lifts and blade-handling rigs to avoid catastrophic failures that can sideline production for months. Construction and civil engineering absorb synchronized multi-lift solutions that streamline modular builds while meeting stringent safety audits.
Healthcare emerges as a niche yet lucrative space, where patient-handling robots require hospital-grade load certifications. Aerospace and defense demand high-g-capable sensors for aircraft assembly and missile test rigs, leveraging digital twins to model stress scenarios in advance. Oil and gas operators maintain investment to safeguard riser tensioning and flare-stack lifts, demonstrating the cross-industry relevance of real-time load intelligence.
Geography Analysis
Asia-Pacific dominated the load monitoring systems market in 2024, capturing 38% of worldwide revenue and growing at a projected 7.3% CAGR. China’s mega-projects, from high-speed rail to offshore wind, anchor demand, while India’s Smart Cities Mission funnels public spending into advanced construction technologies. Southeast Asian economies embrace modular high-rise techniques, importing synchronized multi-lift monitoring as part of turnkey packages. Government incentives for BEV supply chains accelerate adoption in battery and component plants, further expanding the regional customer base.
North America represents a mature yet innovation-driven arena. OSHA’s enforcement surge, combined with aggressive offshore wind targets along the Atlantic seaboard, sustains replacements and greenfield opportunities. The United States leads in BEV gigafactory construction, applying high-precision load measurement to welding lines. Canada’s mining sector adds steady demand for heavy-duty units that withstand extreme cold.
Europe balances stringent safety statutes with environmental imperatives. The North Sea offshore-wind corridor spearheads the deployment of digital load cells capable of autonomous diagnostics. Germany’s Industrie 4.0 programs finance IoT retrofits in brownfield factories. Meanwhile, the Middle East and Africa leverage oil and gas projects to pilot wireless monitoring on offshore platforms, and South America’s commodity extraction sites adopt heavy-capacity systems as part of modernization drives.
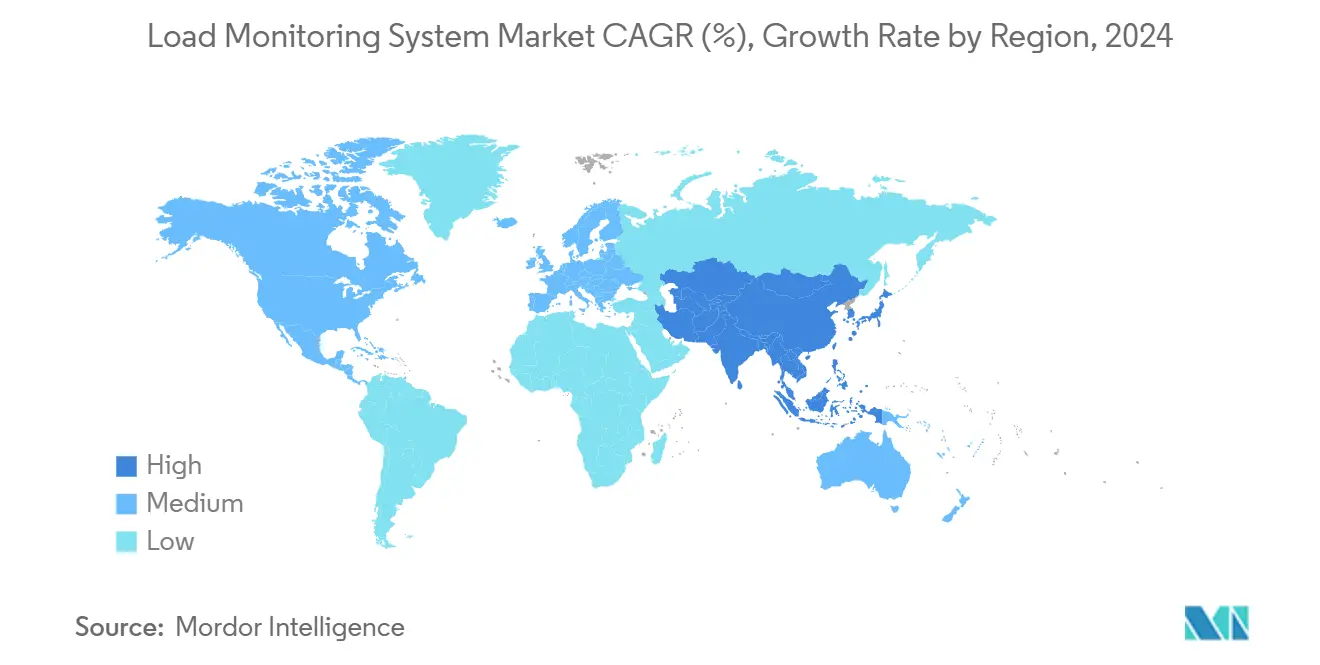
Competitive Landscape
The competitive field remains moderately concentrated. Spectris, Mettler Toledo, and Honeywell collectively command significant influence through broad portfolios and global service networks. Honeywell’s partnership with Google to embed Gemini generative AI into Experion platforms demonstrates how incumbents fuse edge hardware with cloud intelligence to defend market share. IMI plc’s EUR 25 million acquisition of TWTG Group adds wireless sensors and Industrial IoT software, illustrating inorganic strategies to fill capability gaps.
Specialist firms such as Straightpoint, Dynamic Load Monitoring, and LCM Systems differentiate via application depth, offering bespoke shackles, subsea pins, and high-frequency telemetry for niche sectors like super-yacht rigging. Service-based start-ups market cloud dashboards that visualize multi-brand fleets, lowering integration friction and courting price-sensitive operators.
Convergence between hardware and software recasts competitive boundaries. Suppliers invest in explainable AI, 5G modules, and cybersecurity accreditations to comply with IEC 62443. The holistic value proposition of certified hardware, predictive analytics, and lifecycle services now dictates vendor selection criteria within the load monitoring systems market.
Load Monitoring System Industry Leaders
-
Flintec Inc.
-
Mettler Toledo
-
Precia Molen
-
Spectris Plc
-
JCM Load Monitoring Ltd
- *Disclaimer: Major Players sorted in no particular order
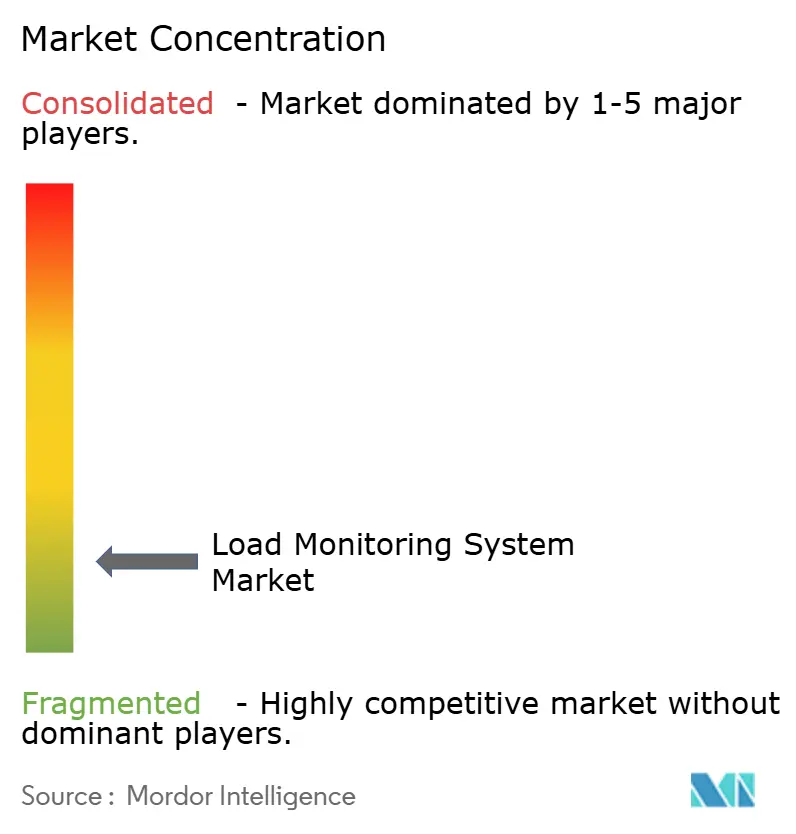
Recent Industry Developments
- July 2025: SICK AG and Endress+Hauser finalized a joint venture that transfers 800 employees to Endress+Hauser SICK GmbH+Co. KG, boosting gas-analyzer and flowmeter capacity for integrated process-automation and load-monitoring solutions.
- March 2025: Honeywell and Verizon Business embedded 5G modules into Honeywell smart meters, enabling real-time grid analytics that enhance utility load monitoring capabilities.
- January 2025: Honeywell rolled out Experion Operations Assistant with explainable AI features and partnered with Chevron to apply the tool in refinery operations.
- January 2025: Honeywell introduced Batch Historian software to contextualize production data for compliance reporting in life sciences and food & beverage load-monitoring use cases.
Global Load Monitoring System Market Report Scope
The load monitoring system measures and displays the weights of various objects to provide an early warning to the workers if the load is too heavy. The load monitoring system combines load cells, load indicators and controllers, and data logging software. It is based on analog or digital technology and used in various industries such as automotive, marine, food & beverages, agriculture, healthcare, aerospace, construction, and oil & gas. Load monitoring systems are equipped in aircraft, for structural and fatigue testing, along with the operational load monitoring of the plane, during flight tests and services.
The Load Monitoring System Market is segmented by By Product (Load Cell, Indicator, Controller, and Data Logging Software), By Technology (Analog and Digital), Application (Automotive, Healthcare, Construction, Marine, and Others), and By Geography (North America, Europe, Asia-Pacific, Middle East & Africa, and South America). The report offers the market size and forecasts in value (USD billion) for all the above segments.
By Product | Load Cell | ||
Indicators & Controllers | |||
Load Monitoring Software (Data logging) | |||
Others (Accessories (Mounting Plates, Shackles, Cables), Telemetry, etc.) | |||
By Load-Cell Capacity | Less than 20 t | ||
20 – 100 t | |||
More than 100 t | |||
By Technology | Analog Load Monitoring Systems | ||
Digital Load Monitoring Systems | |||
Hybrid / Intelligent | |||
By Connectivity | Wired | ||
Wireless | |||
IoT-Enabled (Cloud Connected) | |||
By Industry | Automotive | ||
Construction, Infrastructure & Civil Engineering | |||
Oil & Gas / Offshore | |||
Aerospace & Defense | |||
Marine & Shipbuilding | |||
Healthcare & Biomedical | |||
Manufacturing, Heavy Equipment & Industrial Automation | |||
Energy & Utilities (Wind, Solar, Hydro) | |||
Other Industries (Mining, Entertainment Rigging, Trasport & Logistics, Testing, etc.) | |||
By Geography | North America | United States | |
Canada | |||
Mexico | |||
South America | Brazil | ||
Argentina | |||
Peru | |||
Rest of South America | |||
Europe | United Kingdom | ||
Germany | |||
France | |||
Italy | |||
Spain | |||
BENELUX (Belgium, Netherlands, and Luxembourg) | |||
NORDICS (Denmark, Finland, Iceland, Norway, and Sweden) | |||
Rest of Europe | |||
Asia-Pacific | China | ||
India | |||
Japan | |||
Australia | |||
South Korea | |||
ASEAN (Indonesia, Thailand, Philippines, Malaysia, Vietnam) | |||
Rest of Asia-Pacific | |||
Middle East and Africa | Saudi Arabia | ||
United Arab Emirates | |||
Qatar | |||
Kuwait | |||
Turkey | |||
Egypt | |||
South Africa | |||
Nigeria | |||
Rest of Middle East and Africa |
Load Cell |
Indicators & Controllers |
Load Monitoring Software (Data logging) |
Others (Accessories (Mounting Plates, Shackles, Cables), Telemetry, etc.) |
Less than 20 t |
20 – 100 t |
More than 100 t |
Analog Load Monitoring Systems |
Digital Load Monitoring Systems |
Hybrid / Intelligent |
Wired |
Wireless |
IoT-Enabled (Cloud Connected) |
Automotive |
Construction, Infrastructure & Civil Engineering |
Oil & Gas / Offshore |
Aerospace & Defense |
Marine & Shipbuilding |
Healthcare & Biomedical |
Manufacturing, Heavy Equipment & Industrial Automation |
Energy & Utilities (Wind, Solar, Hydro) |
Other Industries (Mining, Entertainment Rigging, Trasport & Logistics, Testing, etc.) |
North America | United States |
Canada | |
Mexico | |
South America | Brazil |
Argentina | |
Peru | |
Rest of South America | |
Europe | United Kingdom |
Germany | |
France | |
Italy | |
Spain | |
BENELUX (Belgium, Netherlands, and Luxembourg) | |
NORDICS (Denmark, Finland, Iceland, Norway, and Sweden) | |
Rest of Europe | |
Asia-Pacific | China |
India | |
Japan | |
Australia | |
South Korea | |
ASEAN (Indonesia, Thailand, Philippines, Malaysia, Vietnam) | |
Rest of Asia-Pacific | |
Middle East and Africa | Saudi Arabia |
United Arab Emirates | |
Qatar | |
Kuwait | |
Turkey | |
Egypt | |
South Africa | |
Nigeria | |
Rest of Middle East and Africa |
Key Questions Answered in the Report
What is the current size of the load monitoring systems market?
The market is valued at USD 5.79 billion in 2025 and is projected to reach USD 7.53 billion by 2030.
Which segment is growing fastest within the load monitoring systems market?
Energy and utilities applications, especially offshore wind and grid modernization, register the highest 9.6% CAGR through 2030.
How quickly are IoT-enabled load monitoring solutions expanding?
IoT-connected systems are forecast to grow at a 10.3% CAGR as cloud dashboards and 5G backhaul gain traction.
How concentrated is vendor competition?
The market posts a moderate concentration score of 6, with top multinationals exceeding 60% combined share but facing agile specialist competitors in niche applications.