Industrial Rubber Market Size and Share
Industrial Rubber Market Analysis by Mordor Intelligence
The industrial rubber market size is valued at USD 16.33 billion in 2025 and is forecast to reach USD 19.69 billion by 2030, reflecting a 3.81% CAGR through the period. Demand remains firmly anchored in automotive, construction, mining and general-industrial supply chains, with synthetic grades supplying consistent quality and scale advantages. Conveyor systems, transmission equipment and high-pressure hose assemblies continue to pull large volumes, while bio-based and reclaimed alternatives steadily widen addressable demand. Supply-side resilience is shaped by volatile crude-derived feedstocks and natural-rubber shortages; producers that balance raw-material optionality with recycling capabilities reduce earnings volatility. Asia-Pacific, holding a decisive majority share, benefits from integrated upstream raw-material bases and downstream manufacturing density, whereas North America and Europe differentiate through specialty rubber grades and regulatory compliance leadership.
Key Report Takeaways
- By rubber type, synthetic rubber led with 71.09% of industrial rubber market share in 2024, while reclaimed rubber posted the highest projected CAGR at 5.02% to 2030.
- By process, extrusion commanded 45.16% share of the industrial rubber market size in 2024; 3D printing is set to expand the fastest at a 4.18% CAGR.
- By application, conveyor belts accounted for 38.65% of the industrial rubber market size in 2024 and are also advancing at 4.87% CAGR through 2030.
- By end-user industry, automotive and transportation held 53.76% share of the industrial rubber market size in 2024, while aerospace and defense is projected to grow at 4.96% CAGR.
- By geography, Asia-Pacific captured 59.07% of industrial rubber market share in 2024 and is forecast to rise at a 4.11% CAGR.
Global Industrial Rubber Market Trends and Insights
Driver Impact Analysis
Driver | (~) % Impact on CAGR Forecast | Geographic Relevance | Impact Timeline |
---|---|---|---|
Increasing application as conveyor & transmission belts | +1.2% | Global with Asia-Pacific concentration | Medium term (2-4 years) |
Growing demand for high-pressure hoses | +0.8% | North America & Europe industrial clusters | Short term (≤ 2 years) |
EV-led boom in lightweight automotive components | +0.9% | Global with spill-over to emerging markets | Medium term (2-4 years) |
Infrastructure build-out in emerging economies | +1.1% | Asia-Pacific core, MEA & Latin America spill-over | Long term (≥ 4 years) |
Shift to bio-based synthetic rubbers | +0.6% | Europe and North America lead adoption | Long term (≥ 4 years) |
Source: Mordor Intelligence
Increasing application as conveyor & transmission belts
Conveyor and transmission systems underpin automated material-handling strategies that lower operating costs, cut accident frequency and boost energy efficiency. Hard-rock mining, bulk-cargo ports and parcel-sorting hubs specify multi-ply, flame-retardant belts that handle temperatures exceeding 200 °C without accelerated abrasion. Upgraded rubber compounds, often nitrile-blended or aramid-reinforced, extend belt life by up to 25% compared with conventional compounds. Major producers increasingly integrate smart-sensor arrays into belt carcasses, enabling predictive-maintenance programs that reduce unscheduled downtime by nearly 35%. Asia-Pacific miners and construction material suppliers represent the largest customer pool, but value-added demand is rising in North America’s warehousing boom and Europe’s recycling facilities.
Growing demand for high-pressure hoses
Expanding chemical, oil-and-gas and advanced-manufacturing activity elevates the need for hoses that tolerate extreme pressure, rapid flexing and aggressive media. Leading suppliers formulate fluoroelastomer, EPDM and hydrogenated nitrile blends to withstand over 300 PSI and multi-chemical exposure while meeting FDA and EU food-contact regulations[1]Chemours Technical Team, “Chemical-Resistant Elastomers for Hose Applications,” Chemours, chemours.com. Producers complement compound development with crimp-coupling innovations that shorten assembly times and improve impulse-cycle life. Strategic acquisitions—such as Bridgestone’s 2024 purchase of Cline Hose & Hydraulics—illustrate the push to own both product and service footprints[2]Bridgestone Corporation, “Bridgestone Completes Acquisition of Cline Hose & Hydraulics,” Bridgestone, bridgestone.com. Custom-engineered assemblies, ship-to-stock delivery models and local certification centers round out competitive advantages in this high-mix application space.
EV-led boom in lightweight automotive components
Electric vehicles accelerate rubber consumption despite broader vehicle lightweighting efforts. EV tires wear roughly 20% faster than internal-combustion equivalents due to higher torque and battery weight, prompting investment in silica-rich tread formulations that cut rolling resistance while controlling heat build-up. Battery pack integrity relies on fluoroelastomer gaskets and thermal-pad foams capable of surviving repeated temperature cycling and dielectric-fluid contact. Tier-1 suppliers apply microcellular rubber and hollow-core profiles to shave mass while maintaining noise-, vibration- and harshness-damping targets set by automakers. Bridgestone’s USD 85 million Indian plant upgrade emphasizes premium EV-specific tires, underscoring the shift toward silent, low-drag rubber solutions.
Infrastructure build-out in emerging economies
Megaproject pipelines across Southeast Asia, the Gulf and sub-Saharan Africa spur demand for industrial hoses, linings, seals and conveyor belts engineered for abrasive aggregates, hot asphalt, and corrosive chemicals. Thailand’s downstream rubber processors capture regional spending momentum, supported by development funds that expand capacity and promote value-added exports. Rubberized asphalt gains traction as road agencies measure 25% longer pavement lifetimes and reduced maintenance spending; ground-tire-rubber modifiers also help divert waste tires from landfills. Infrastructure stimulus improves long-cycle visibility for domestic mixing plants, enabling investment in continuous vulcanization lines and local compounding of specialty grades.
Restraint Impact Analysis
Restraint | (~) % Impact on CAGR Forecast | Geographic Relevance | Impact Timeline |
---|---|---|---|
Stringent environmental regulations | -0.7% | Global with EU & North America strictest | Short term (≤ 2 years) |
Volatile crude-oil-linked feedstock prices | -0.9% | Global with regional variations | Short term (≤ 2 years) |
Rapid uptake of reclaimed rubber cannibalising virgin demand | -0.4% | Developed markets primarily | Medium term (2-4 years) |
Source: Mordor Intelligence
Stringent environmental regulations
The U.S. EPA tightened National Emission Standards for Hazardous Air Pollutants in tire and mixed-rubber processing, capping volatile organics at 64 g per tonne and compelling plant retrofits by 2027[3]U.S. Environmental Protection Agency, “National Emission Standards for Hazardous Air Pollutants: Rubber Tire Manufacturing,” EPA, epa.gov. Europe’s Deforestation Regulation obliges full traceability for natural-rubber imports, raising procurement costs and documentation burdens. California’s investigation into 6PPD tire additives forces compound reformulation discussions amid durability concerns, while global proposals to phase out PFAS push fluoroelastomer R&D pipelines. Compliance outlays challenge smaller compounders but reward early adopters of cleaner solvents, closed-loop wash systems and bio-based feedstocks.
Volatile crude-oil-linked feedstock prices
Styrene, butadiene and isoprene price swings, often exceeding 30% within a quarter, compress synthetic-rubber margins and complicate long-term supply contracts. Natural-rubber spot rates rallied nearly 50% in 2024 on weather-related Southeast-Asian shortages, driving substitution discussions among tire majors. Geopolitical disruptions, such as Red Sea shipping detours, inflate voyage costs and stretch delivery times, prompting inventory build-ups in key consuming regions. Producers hedge with multi-feedstock portfolios, forward-buying programs and increased reliance on reclaimed or bio-derived monomers. Bio-route economics remain challenged by scale but offer improved cost predictability once established.
Segment Analysis
By Rubber Type: Synthetic scale leadership balanced by reclaimed growth prospects
Synthetic grades, dominated by styrene-butadiene, retained a commanding 71.09% share of the industrial rubber market in 2024 as automakers, machinery OEMs and infrastructure builders demanded consistent performance across broad temperature windows. Extensive catalyst and process innovations boost tensile strength, abrasion resistance and oil tolerance, aligning properties with stringent OEM specifications. Reclaimed rubber, harvested from devulcanized end-of-life tires and buffings, expands at a 5.02% CAGR on the back of 30–50% cost savings versus virgin feedstocks and mounting circular-economy mandates. Compounders re-engineer formulations to accommodate reclaimed content of up to 25% without compromising cure kinetics, thereby moderating overall scrap. Natural-rubber supply remains central to passenger-tire elasticity and heavy-haul off-road grip, yet producers wrestle with disease-related yield drops in Southeast Asia. Bio-based synthetic routes, particularly bio-butadiene and polyisoprene from plant sugars, advance pilot-scale trials that promise to ease resource pressures while shrinking carbon footprints.
Note: Segment shares of all individual segments available upon report purchase
By Process: Extrusion versatility faces additive-manufacturing innovation
Extrusion held 45.16% share of the industrial rubber market size in 2024, favored for continuous production of hoses, profiles and sealing strips where dimensional accuracy and low scrap rates are critical. State-of-the-art screw designs increase throughput 15% and support real-time viscosity monitoring systems that cut change-over time. Injection and compression molding retain vital roles for high-volume automotive bushings and vibration isolators, benefitting from multi-cavity tooling and automated demolding robotics. Additive manufacturing, while only emerging, records the fastest 4.18% CAGR as aerospace, defense and medical users exploit 3D-printed thermoplastic polyurethane lattices for lightweight, complex geometries. Advances in photopolymerizable isoprene resins yield elastomeric parts with elongation at break surpassing 200%, bringing functional prototypes within days rather than weeks. Calendaring sustains specialty sheet markets—roofing membranes, tank linings and diaphragm sheets—thanks to microscopic gauge control afforded by precision-roll systems.
By Application: Conveyor belts dominate volume and growth metrics
Conveyor belts secured both the largest 38.65% share and the swiftest 4.87% CAGR of the industrial rubber market size in 2024. Bulk-material handlers favor multi-ply, steel-cord and textile-reinforced constructions that tolerate abrasion, heat and impact loads in mining, quarrying and cement plants. Integrated sensor loops feed wear data into cloud dashboards, driving preventive maintenance and adding service-contract revenue streams for belt OEMs. Transmission belts, notably V-belts and synchronous belts, maintain relevance in light-duty power-transmission applications where alignment flexibility and shock-load absorption are key. High-pressure hoses gain traction across chemical processing and hydraulic machinery, where compounders deploy peroxidic cure systems and nano-clay fillers to extend impulse life. Roofing membranes, rubber rolls and tubes round out diversified demand, supported by construction recovery and energy-efficient building codes.
By End-User Industry: Automotive holds scale while aerospace accelerates specialty demand
Automotive and transportation dominated 53.76% of industrial rubber market share in 2024, sustained by global vehicle output, replacement tire cycles and electrification trends that add gasket, seal and NVH component complexity. Tier-1 suppliers integrate recycled and bio-rubber into under-hood hoses and weatherstrips to satisfy OEM sustainability scorecards. Aerospace and defense, though smaller in absolute volume, records a 4.96% CAGR as airlines recover travel demand and defense agencies modernize fleets. High-temperature fluorosilicone seals, low-smoke cabin components and fuel-tank bladders exemplify niche, high-margin applications. Construction and infrastructure spending reinforces demand for vibration pads, expansion joints and rubberized asphalt modifiers, while mining remains reliant on belt, lining and hose solutions capable of withstanding corrosive slurries. Electrical and electronics segments absorb silicone rubber for insulation in renewable-energy grids and EV charging infrastructure.
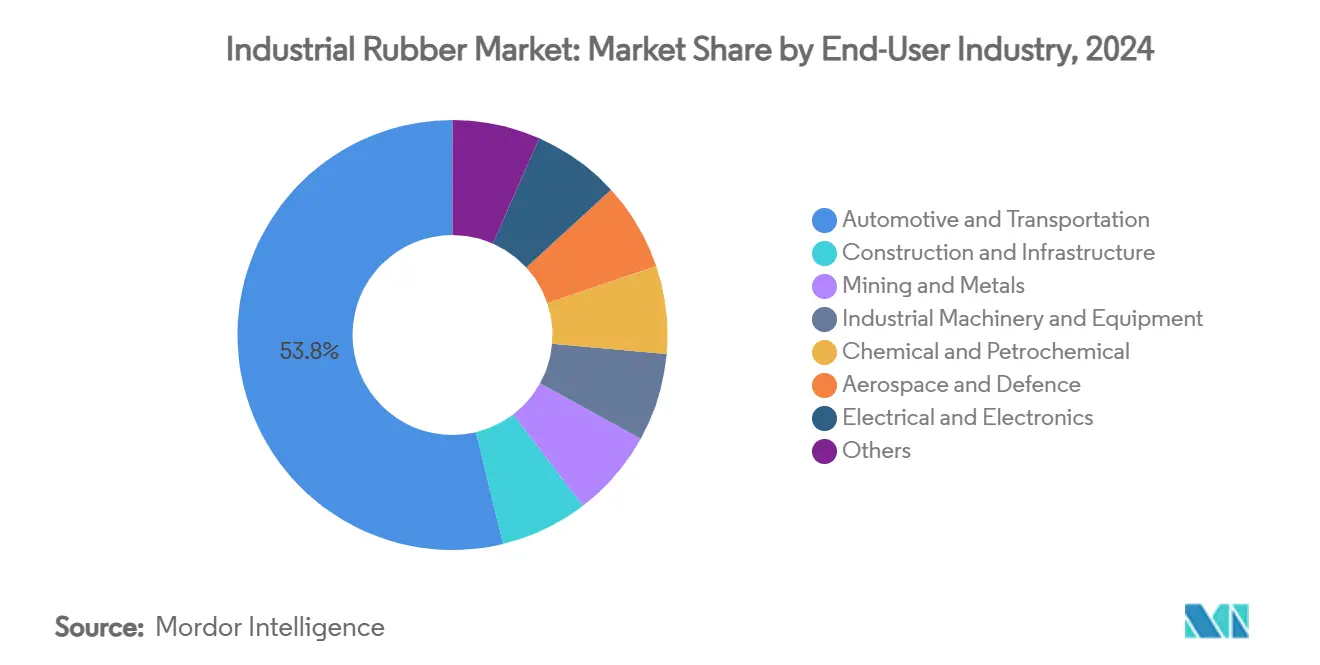
Note: Segment shares of all individual segments available upon report purchase
Geography Analysis
Asia-Pacific retained 59.07% share of the industrial rubber market in 2024 and is advancing at a 4.11% CAGR, underscored by its integrated plantation-to-compound supply chains, large-scale tire capacities, and vast infrastructure programs. China drives demand through EV adoption rates approaching one-third of new car sales, heightening traction for specialty tire and sealing compounds. Thailand and Indonesia together account for more than 60% of global natural-rubber output, but yields are strained by disease incidence and labor shortages, prompting government support for mechanized tapping and downstream processing upgrades. India tightens its import-export balance by expanding domestic mixing houses and encouraging reclaimed-rubber collection networks.
North America sustains mid-single-digit growth anchored in aerospace, shale-energy and logistics construction. The U.S. imports roughly 90% of its natural-rubber needs, sparking policy discourse around domestic guayule cultivation to improve supply resilience. Canada’s mining expansion in critical minerals feeds conveyor-belt and hose demand, while Mexico captures OEM investments relocating supply chains closer to U.S. consumer bases.
Europe’s demand profile is shaped by strict environmental regulations and rapid commercialization of bio-based materials. The EU Deforestation Regulation compels traceability for rubber imports, catalyzing digital ledger adoption among traders. Germany and France pioneer dandelion-based natural-rubber pilot farms that lower transport emissions compared with Southeast-Asian supply. Eastern European tire plants receive significant capital infusions to produce larger-rim EV tires domestically, reducing reliance on Asian imports amid shipping volatility.
Latin America and Middle East & Africa collectively contribute a modest but rising share as infrastructure projects launch new demand corridors. Brazil restarts public-works spending focused on bridge retrofits and port expansion, increasing calls for rubber bearings and hose assemblies. The Gulf Cooperation Council accelerates industrial diversification beyond hydrocarbons, with petrochemical complexes specifying EPDM seals and nitrile hoses resistant to sour gas exposure. Sub-Saharan African mining prospects in copper and lithium underpin conveyor-belt demand, yet project rollouts hinge on political stability and financing access.
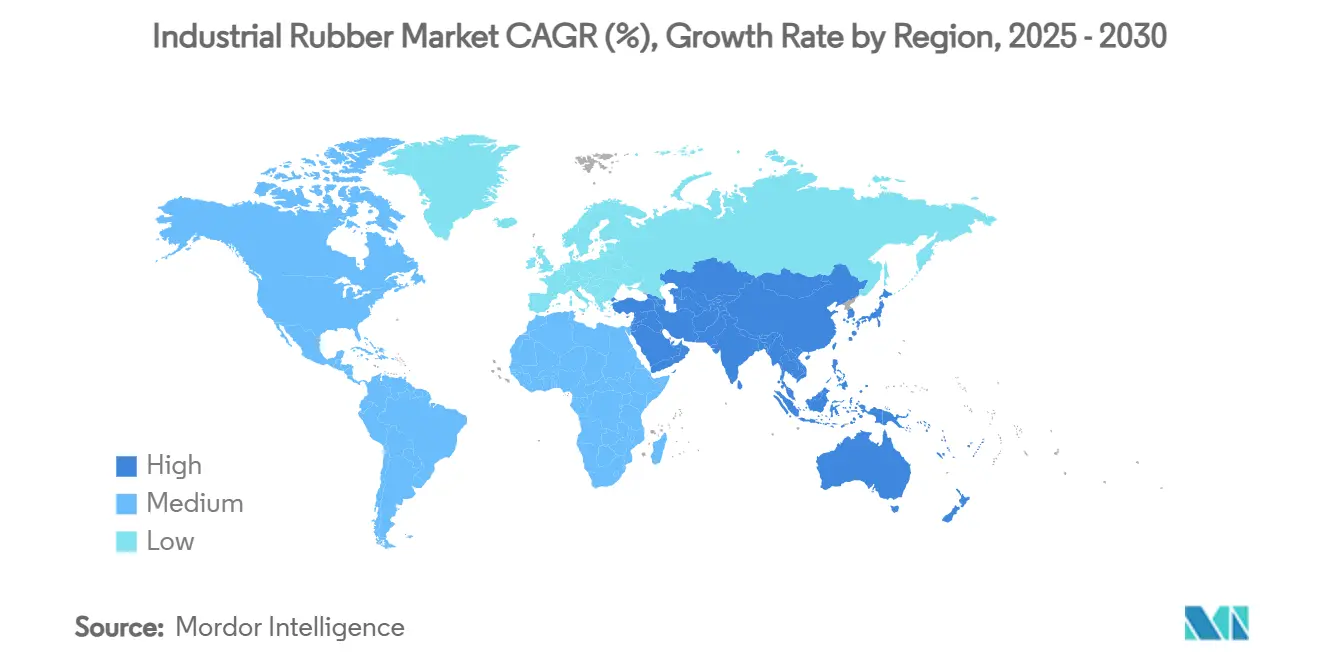
Competitive Landscape
The industrial rubber industry is moderately fragmented. Digitalization and automation drive competitiveness. Sumitomo Rubber adopted Rockwell Automation’s FactoryTalk, achieving real-time quality tracking and 7% scrap reduction. Yokohama Rubber’s Romanian facility acquisition reduced lead times and import duties. PPG’s 3D-printed sealants cut aircraft window installation cycles by 90%.
Sustainability is pivotal. Michelin targets 40% sustainable inputs by 2030 through waste-to-butadiene collaborations. Goodyear’s USD 320 million Oklahoma expansion focuses on low-rolling-resistance tires for electric vehicles, ensuring supply reliability for OEMs. Early entry into low-carbon rubber secures premium pricing and long-term contracts with automakers and aerospace firms.
Industrial Rubber Industry Leaders
-
Bridgestone Industrial
-
ContiTech Deutschland GmbH
-
Sumitomo Rubber Industries, Ltd.
-
The Goodyear Tire & Rubber Company
-
THE YOKOHAMA RUBBER CO., LTD.
- *Disclaimer: Major Players sorted in no particular order
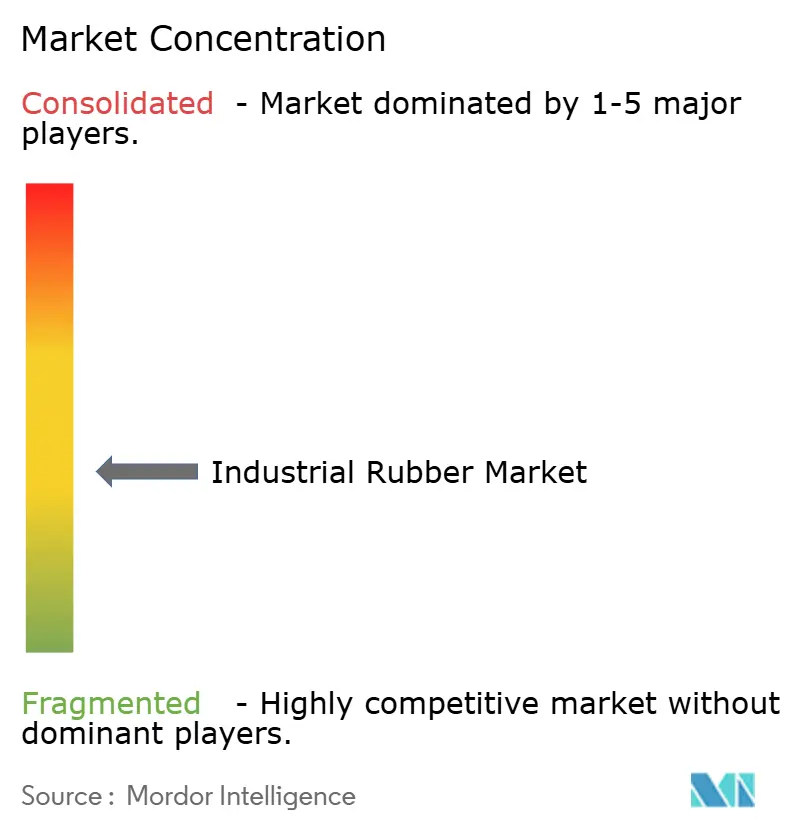
Recent Industry Developments
- May 2025: In a move to bolster its off-highway tire capacity in Europe, Yokohama Rubber purchased a former tire facility in Drobeta-Turnu Severin, Romania, for USD 35 million. This acquisition aligns with the company's strategy to expand its footprint in the European market and meet growing demand in the region.
- February 2025: Goodyear unveiled a USD 320 million expansion at its Lawton, Oklahoma plant, aiming to boost production by 10 million annual units, with a focus on premium tires for EVs and autonomous vehicles. This investment underscores Goodyear's commitment to innovation and addressing the evolving needs of the mobility sector.
Global Industrial Rubber Market Report Scope
Industrial rubber is made of polymers and has a major application in end-user industries, including mining, automotive, and others. In the automotive industry, industrial rubber is mainly used as flexible shaft couplings, drive belts, high-pressure hoses, process control rubber sheets, etc. In the mining industry, it is used to make conveyors and transmission belts to carry minerals.
The industrial rubber market is segmented by application and geography. The market is segmented by application into conveyor belts, transmission belts, pressure hoses, and other applications (insulations, gaskets, etc.). The report also covers the market size and forecasts in 27 countries across major regions. Market sizing and forecasts were made for each segment based on USD revenue.
By Rubber Type | Natural Rubber | ||
Synthetic Rubber | |||
Reclaimed Rubber | |||
By Process | Extrusion | ||
Molding and Casting | |||
Calendaring | |||
3-D Printing / Additive Manufacturing | |||
By Application | Conveyor Belts | ||
Transmission Belts | |||
Pressure Hoses | |||
Other Application (Roofing, Tubes, Rolls, etc.) | |||
By End-User Industry | Automotive and Transportation | ||
Construction and Infrastructure | |||
Mining and Metals | |||
Industrial Machinery and Equipment | |||
Chemical and Petrochemical | |||
Aerospace and Defence | |||
Electrical and Electronics | |||
Others | |||
By Geography | Asia-Pacific | China | |
India | |||
Japan | |||
South Korea | |||
Thailand | |||
Indonesia | |||
Vietnam | |||
Malaysia | |||
Philippines | |||
Rest of Asia-Pacific | |||
North America | United States | ||
Canada | |||
Mexico | |||
Europe | Germany | ||
United Kingdom | |||
France | |||
Italy | |||
Spain | |||
Russia | |||
NORDIC Countries | |||
Turkey | |||
Rest of Europe | |||
South America | Brazil | ||
Argentina | |||
Colombia | |||
Rest of South America | |||
Middle East and Africa | Saudi Arabia | ||
United Arab Emirates | |||
Qatar | |||
South Africa | |||
Nigeria | |||
Egypt | |||
Rest of Middle East and Africa |
Natural Rubber |
Synthetic Rubber |
Reclaimed Rubber |
Extrusion |
Molding and Casting |
Calendaring |
3-D Printing / Additive Manufacturing |
Conveyor Belts |
Transmission Belts |
Pressure Hoses |
Other Application (Roofing, Tubes, Rolls, etc.) |
Automotive and Transportation |
Construction and Infrastructure |
Mining and Metals |
Industrial Machinery and Equipment |
Chemical and Petrochemical |
Aerospace and Defence |
Electrical and Electronics |
Others |
Asia-Pacific | China |
India | |
Japan | |
South Korea | |
Thailand | |
Indonesia | |
Vietnam | |
Malaysia | |
Philippines | |
Rest of Asia-Pacific | |
North America | United States |
Canada | |
Mexico | |
Europe | Germany |
United Kingdom | |
France | |
Italy | |
Spain | |
Russia | |
NORDIC Countries | |
Turkey | |
Rest of Europe | |
South America | Brazil |
Argentina | |
Colombia | |
Rest of South America | |
Middle East and Africa | Saudi Arabia |
United Arab Emirates | |
Qatar | |
South Africa | |
Nigeria | |
Egypt | |
Rest of Middle East and Africa |
Key Questions Answered in the Report
What is the current size of the industrial rubber market?
The market is valued at USD 16.33 billion in 2025 and is projected to reach USD 19.69 billion by 2030 at a 3.81% CAGR.
Which segment holds the largest industrial rubber market share?
Synthetic rubber leads with 71.09% share, benefiting from processing consistency and broad application across automotive, construction and machinery uses.
Why are conveyor belts so important to the industrial rubber market?
Conveyor belts account for 38.65% of 2024 revenue and grow the fastest at 4.87% CAGR because mining, logistics and manufacturing sectors increasingly automate bulk-material handling.
How are electric vehicles influencing industrial rubber demand?
EVs require specialized low-rolling-resistance tires, high-performance gaskets and lightweight NVH components, driving rubber innovation even as overall vehicle mass decreases.