Cladding Market Size and Share
Cladding Market Analysis by Mordor Intelligence
The Cladding Market size is estimated at USD 121.5 billion in 2025, and is expected to reach USD 165.30 billion by 2030, at a CAGR of 6.35% during the forecast period (2025-2030). The upward trajectory is underpinned by stricter energy-efficiency rules, compulsory façade fire-performance testing, and municipal heat-island mitigation programs that collectively reshape material specifications and procurement practices. Demand is balanced between green-field activity and a fast-intensifying retrofit cycle in which aging facades need code-compliant fire resistance, lower operational carbon, and improved thermal performance. Supply-side resilience draws on vertical integration moves by large manufacturers and rising localization of metal and mineral panel production to shield projects from tariff-driven price swings. Ongoing digitalization—especially the use of twin-enabled asset monitoring—lowers lifecycle costs and influences bid decisions toward systems that can document performance in real time. External risks remain visible: aluminum price volatility can squeeze EPC margins, skilled-labor shortages lengthen installation schedules, and evolving fire codes can force unbudgeted façade replacements in dense urban cores[1]UK Government, “Combustible Cladding Ban Strengthened,” gov.uk.
Key Report Takeaways
- By material, metal panels led with 31% of cladding market share in 2024; wood products post the fastest CAGR at 6.60% through 2030.
- By construction type, new builds captured 62% of cladding market size in 2024, while renovation activity is projected to advance at a 6.92% CAGR to 2030.
- By application, commercial projects accounted for 51% of cladding market in 2024; the residential segment is growing at a 6.92% CAGR on the back of envelope-tightening codes.
- By geography, Asia-Pacific commanded 37% of the cladding market in 2024, whereas the Middle East & Africa region is forecast to expand at a 6.70% CAGR to 2030.
Global Cladding Market Trends and Insights
Drivers Impact Analysis
Driver | ( ~) % Impact on CAGR Forecast | Geographic Relevance | Impact Timeline |
---|---|---|---|
Tightening net-zero-ready energy codes | +1.2% | EU, California, early adopters globally | Medium term (2-4 years) |
Mandatory façade fire testing for high-rise retrofits | +0.8% | Major metros worldwide | Short term (≤ 2 years) |
Urban heat-island incentives favoring cool-roof cladding | +0.6% | North America, EU, select APAC cities | Medium term (2-4 years) |
Insurance rebates for hail-resistant metal panels | +0.4% | U.S. hail belt | Short term (≤ 2 years) |
Digital-twin predictive maintenance | +0.5% | Global institutional & commercial stock | Long term (≥ 4 years) |
Demand for low-carbon bio-based panels | +0.7% | North America, EU pilots in APAC | Long term (≥ 4 years) |
Source: Mordor Intelligence
Tightening Net-Zero-Ready Building Energy Codes
The 2024 International Energy Conservation Code introduces higher-performance envelope thresholds, while California’s 2025 standards require heat-pump-ready shells and advanced insulation detailing[2]California Energy Commission, “2025 Building Energy Efficiency Standards,” energy.ca.gov. State and municipal stretch codes that reference these benchmarks compel new projects to specify high-R, thermally broken cladding assemblies. Commercial landlords are prioritizing integrated façade systems to curb operational expenses and secure green-lease premiums. The building cladding market benefits as material choices shift from cost-driven to performance-driven selection.
Mandatory Façade Fire-Performance Testing in High-Rise Retrofits
Post-Grenfell reforms embed non-combustibility requirements into the 2024 International Building Code and parallel national standards[3]International Code Council, “2024 IBC Fire Provisions,” iccsafe.org. High-rise owners now commission NFPA 285 testing or equivalent assessments before recladding, accelerating the swap-out of combustible ACM systems for mineral fiber or solid aluminum solutions. Suppliers able to certify compliant assemblies see faster bid-cycle conversions, reinforcing the building cladding market’s tilt toward metal and stone wool cores.
Urban Heat-Island Mitigation Incentives Favouring Cool-Roof Cladding
Local Law 21 in New York City, Los Angeles Green Building Code metrics, and federal EPA guidance stimulate adoption of reflective coatings and light-colored panels that lower roof surface temperatures. Verified products listed by the Cool Roof Rating Council have become de-facto procurement shortlists, steering R&D spending toward high-solar-reflectance pigments.
Accelerated Insurance Premium Rebates for Hail-Resistant Metal Panels
In Texas, Class 4-rated metal systems qualify homeowners for up to 35% policy discounts, creating a measurable payback case that outweighs higher upfront panel costs. Insurers elsewhere in the U.S. hail belt are replicating rebate structures, lifting demand for standing-seam and impact-tested claddings.
Restraints Impact Analysis
Restraint | ( ~) % Impact on CAGR Forecast | Geographic Relevance | Impact Timeline |
---|---|---|---|
Volatile aluminum prices squeezing EPC margins | -0.9% | North America & EU | Short term (≤ 2 years) |
Fragmented local fire codes delaying approvals | -0.6% | Federal systems in US, Canada, Australia | Medium term (2-4 years) |
Skilled-labor shortages lengthening schedules | -1.1% | North America & EU | Medium term (2-4 years) |
Insurance exclusions for combustible façades | -0.7% | Post-Grenfell metros worldwide | Short term (≤ 2 years) |
Source: Mordor Intelligence
Volatile Aluminum Prices Squeezing EPC Margins
Pending 2025 U.S. tariffs pushed Midwest aluminum premiums sharply higher, complicating bid pricing for curtain-wall and rainscreen packages. Contractors attempt hedging or escalation clauses, yet competitive tender rules often cap pass-through, eroding margins and delaying project starts.
Skilled-Labour Shortages Lengthening Installation Schedules
ABC projects the U.S. industry will need 439,000 additional workers in 2025, rising to 499,000 in 2026, with façade installers among the scarcest trades. Schedule slippage raises holding costs for developers and can prompt substitution toward lighter, easier-to-install systems, influencing material mix within the building cladding market.
Segment Analysis
By Material: Metal Dominance Faces Bio-Based Disruption
Metal panels generated the single-largest revenue block, equal to 31% building cladding market share in 2024, as regulators demanded non-combustible exteriors on high rises. Wood cladding, buoyed by carbon-credit schemes and improved fire-retardant treatments, is registering a 6.60% CAGR through 2030 and is already specified on several net-zero schools and civic projects. Ceramic rainscreens continue to anchor premium commercial façades due to colorfastness and freeze-thaw resilience. Brick and stone veneer sales rise in renovation programs aiming to preserve architectural vernacular while boosting envelope R-values.
Demand in the “others” basket—stucco, glass, fiber-cement, and vinyl—follows region-specific code rhythms. Fiber-cement boards, supported by a USD 150 million domestic capacity expansion that aligns with federal “Build America” rules, secure listings on infrastructure projects and large multifamily builds. Smart glass façades gain traction where dynamic shading helps projects comply with cooling-load budgets. As codes prioritize performance attributes over material cost, suppliers that can certify low-carbon footprints and integrated fire-plus-thermal resistances position best for share capture within the building cladding market.
By Construction Type: Renovation Acceleration Outpaces New Build
New construction commanded 62% of 2024 revenue owing to large pipeline projects in data centers, healthcare, and mixed-use towers. Yet retrofit activity is predicted to advance at a 6.92% CAGR because city ordinances now compel older stock to replace combustible panels and upgrade U-values. Public notices banning high-risk cladding products, such as the Victorian Building Authority’s 2021 ruling, underscore legal liability and speed replacement cycles.
New-build sites freely integrate sub-girt thermally broken brackets and sensor conduits at design stage, keeping unit install costs lower than on occupied buildings. Retrofit scopes face logistical constraints—access, phasing, tenant coordination—which increase labor hours; nonetheless, rebate programs and insurance compliance mitigate payback periods. As deadlines for energy-performance disclosures converge with fire-safety retrofits, renovation is becoming a structural—not cyclical—growth lever for the building cladding market.
By Application: Commercial Leadership Challenged by Residential Innovation
Commercial buildings retained 51% of sales during 2024, driven by stringent façade performance clauses in office, hospital, and higher-education procurements. Developers favor curtain-wall-plus-rain-screen hybrids that accommodate digital-twin sensors for warranty-backed energy budgets. Infrastructure—airports, rail hubs, stadiums—adds steady demand for blast-rated and heavy-duty laminates.
Residential demand, however, is the fastest-rising application at 6.92% CAGR. California’s 2025 energy code intensifies wall R-value and air-tightness targets, pushing single-family builders toward factory-finished insulated panels. ICC approval of hemp-crete walls introduces a carbon-negative path for low-rise housing, supported by local rebate schemes. Multifamily developers adopt metal-and-panel composites to minimize maintenance while satisfying Green Lease criteria. The shift blurs historical price hierarchies: performance parity is leading to convergence in material types across commercial and residential parcels inside the building cladding market.
Geography Analysis
Asia-Pacific accounted for 37% of global revenue in 2024. China’s urban-renewal funding packages keep façade replacement programs active even as residential starts cool, while local governments in second-tier cities incentivize reflective roof membranes to cut summer power peaks. India’s national infrastructure corridors spur demand for fire-rated metal panels in warehousing and logistics parks, with material cost inflation offset by improved construction finance availability. Japan’s moderated cost environment unlocks small-footprint hospitality projects that deploy thin-gauge ceramic rainscreens to withstand seismic drift. Regional sustainability charters, including Indonesia’s Nusantara capital plan, embed low-carbon façade targets at master-plan level, reinforcing long-run engagement for the building cladding market.
The Middle East & Africa region posts the fastest growth at a projected 6.70% CAGR through 2030. Saudi Arabia’s Vision 2030 pipeline, surpassing USD 1.1 trillion in announced construction value, specifies non-combustible façade systems able to perform under extreme thermal cycling. UAE data-center builds, growing at 36% annually, demand highly insulated sandwich panels to manage HVAC loads, and developers increasingly source these panels locally to meet Emiratization thresholds. Contractors cite procurement visibility, sustainability passporting, and digital-twin readiness as top award criteria, a trend mirrored by 58% of firms surveyed in the region.
North America remains a volume engine despite slower 2% year-on-year construction spending growth. Seattle alone expects USD 17.4 billion in new contracts in 2025, underpinned by laboratory and life-science expansions that specify unitized glass-and-panel façades capable of 0.30 W/m²-K assembly performance. Federal infrastructure funds cascade into state university retrofits where aged precast is replaced by ventilated fiber-cement cladding. Europe’s demand stabilizes on retrofit projects that must meet post-Grenfell combustibility bans; French renovation tax credits sustain volumes even as green-field permits soften. South American growth concentrates in Brazil’s northeastern urban nodes, where social-housing façades increasingly use fiber-cement to resist humid tropical conditions. Together, these dynamics illustrate why the building cladding market is simultaneously global and intensely local.
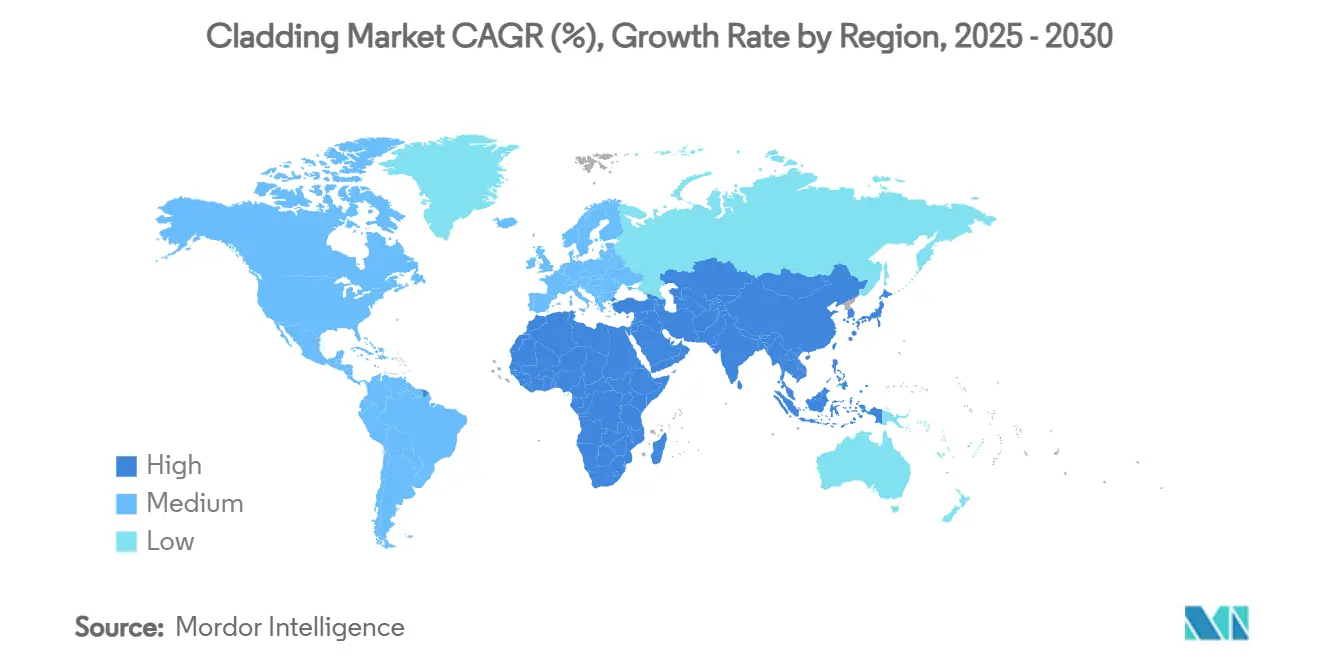
Note: Segments share of all individual segments available upon report purchase
Competitive Landscape
The supplier ecosystem shows moderate fragmentation. Top multilayer-panel producers, insulation majors, and façade-system specialists pursue acquisition-led scale and vertical integration. Kingspan posted 6% 2024 revenue growth and cut emissions 27%, supported by EUR 714 million in plant upgrades and bolt-ons. Saint-Gobain executed twin deals—CSR Limited in Australia and The Bailey Group of Companies in Canada—to deepen regional access to metal-building products.
White-space opportunities emerge in bio-based façades and SaaS-enabled performance guarantees. James Hardie’s planned acquisition of AZEK marries fiber-cement expertise with polymer decking know-how, creating a platform to cross-sell exterior envelope solutions in high-wind zones. Nichiha’s domestic manufacturing investment secures Build America compliance for public-works bids and reduces logistics carbon for large-format fiber-cement systems.
Digitalization differentiates incumbents: suppliers embed RFID tags and sensor suites into panels, feeding asset-management dashboards that insurers consider when pricing premiums. Collaboration with robotics firms to automate panel installation is emerging as a hedge against labor scarcity. Competitive intensity thus pivots on three axes—sustainability credentials, supply-chain proximity, and data-enabled service wrap—each redefining value capture within the building cladding market.
Cladding Industry Leaders
-
Tata Steel Ltd.
-
Etex Group
-
Compagnie de Saint Gobain SA.
-
Kingspan Group
-
Arconic Corporation
- *Disclaimer: Major Players sorted in no particular order
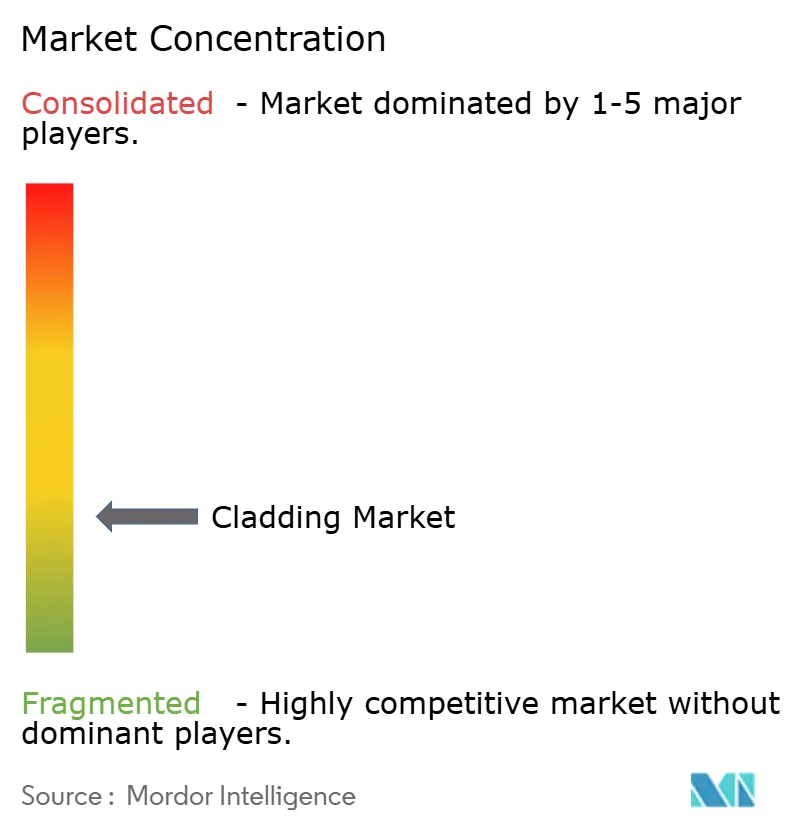
Recent Industry Developments
- April 2025: James Hardie announced the acquisition of AZEK, broadening its exterior building products portfolio.
- March 2025: California Building Officials published amendments effective July 2025 that tighten single-family and multifamily envelope standards.
- February 2025: Kingspan reported FY 2024 results showing 6% revenue growth and EUR 714 million (USD 787.9 million) in acquisitions and capex.
- January 2025: Nichiha USA confirmed Build America, Buy America compliance following a USD 150 million plant expansion.
Global Cladding Market Report Scope
The exterior of a structure is covered with panels made of a different material during the cladding process. Buildings are constructed using cladding systems. The cladding market report provides an overview of the market with an exhaustive analysis of current advancements in the market. The report also focuses on the trends in production and consumption data for the product, policies and plans, cost structures, and manufacturing processes. Moreover, the company profiles of the key manufacturers, along with a thorough analysis, are also provided.
The Metal Cladding Market Is Segmented By Material (Metal, Terracotta, Fiber Cement, Concrete, Ceramics, Wood, Vinyl, And Other Materials), By Component Type (Wall, Roofs, Windows, And Doors), By Application (Residential, Non-Residential), And By Geography (North America, Europe, Asia-Pacific, South America, And The Middle East And Africa). The Market Size And Forecasts Are Provided In Terms Of Value (USD) For All The Above Segments.
By Material | Ceramic | ||
Wood | |||
Brick and Stone | |||
Metal | |||
Others (Stucco, Glass, Fibre Cement, Vinyl) | |||
By Construction Type | New Construction | ||
Renovation | |||
By Application | Commerical | ||
Residential | |||
Infrastructure | |||
By Region | North America | United States | |
Canada | |||
Mexico | |||
South America | Brazil | ||
Argentina | |||
Chile | |||
Rest of South America | |||
Europe | Germany | ||
United Kingdom | |||
France | |||
Italy | |||
Spain | |||
Rest of Europe | |||
Asia-Pacific | China | ||
India | |||
Japan | |||
South Korea | |||
Australia | |||
Rest of Asia-Pacific | |||
Middle East & Africa | United Arab Emirates | ||
Saudi Arabia | |||
South Africa | |||
Nigeria | |||
Rest of Middle East & Africa |
Ceramic |
Wood |
Brick and Stone |
Metal |
Others (Stucco, Glass, Fibre Cement, Vinyl) |
New Construction |
Renovation |
Commerical |
Residential |
Infrastructure |
North America | United States |
Canada | |
Mexico | |
South America | Brazil |
Argentina | |
Chile | |
Rest of South America | |
Europe | Germany |
United Kingdom | |
France | |
Italy | |
Spain | |
Rest of Europe | |
Asia-Pacific | China |
India | |
Japan | |
South Korea | |
Australia | |
Rest of Asia-Pacific | |
Middle East & Africa | United Arab Emirates |
Saudi Arabia | |
South Africa | |
Nigeria | |
Rest of Middle East & Africa |
Key Questions Answered in the Report
What is the current value of the building cladding market?
The market is valued at USD 121.5 billion in 2025.
How fast is the building cladding market expected to grow?
It is forecast to expand at a 6.35% CAGR, reaching USD 165.3 billion by 2030.
Which material holds the largest building cladding market share?
Metal panels lead with 31% of 2024 revenue.
Why is renovation activity rising faster than new construction?
Mandatory fire-safety upgrades and energy-code compliance deadlines accelerate retrofit demand at a 6.92% CAGR.
Which region is the fastest-growing market for cladding?
The Middle East & Africa region is projected to grow at 6.70% CAGR through 2030.
How are digital twins impacting the building cladding industry?
Real-time façade monitoring cuts maintenance costs and supports performance-guaranteed service models that are reshaping buyer preferences.