Anti-Slip Coatings Market Size
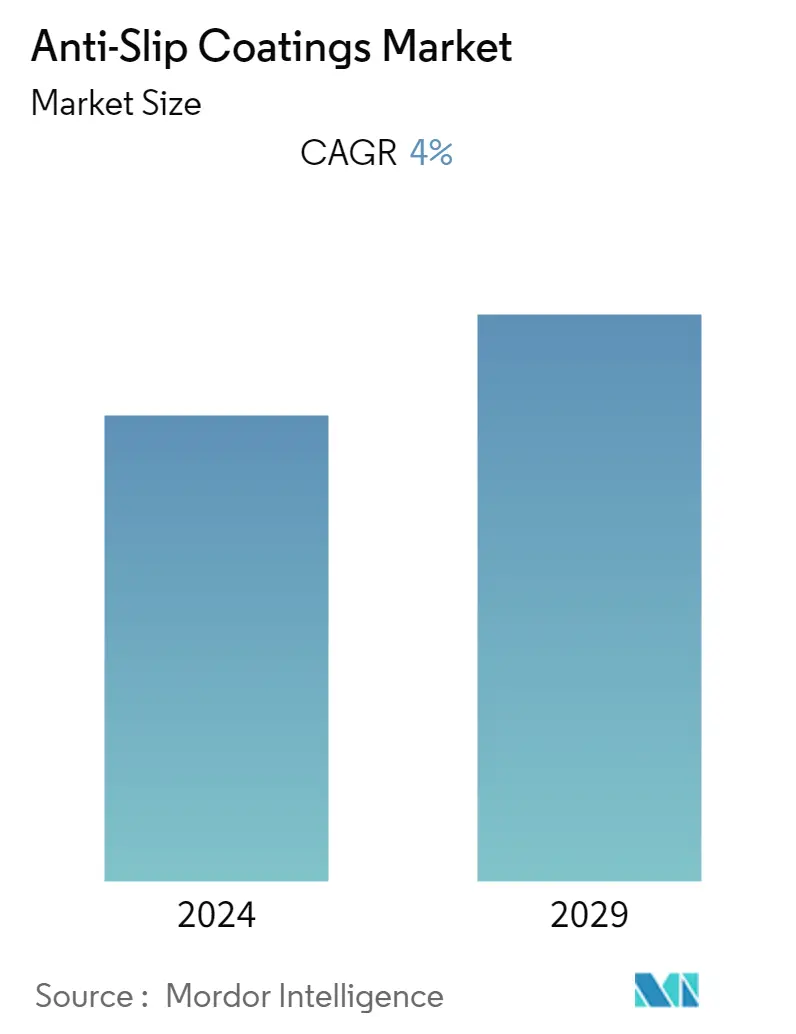
Study Period | 2019 - 2029 |
Base Year For Estimation | 2023 |
CAGR | 4.00 % |
Fastest Growing Market | Asia Pacific |
Largest Market | Asia Pacific |
Market Concentration | Low |
Major Players![]() *Disclaimer: Major Players sorted in no particular order |
Need a report that reflects how COVID-19 has impacted this market and its growth?
Anti-Slip Coatings Market Analysis
The market for anti-slip coatings is expected to grow at a CAGR of about 4% globally during the forecast period. Increasing application in the manufacturing sector and growing safety regulations from the government are driving market growth. On the flip side, stringent environmental regulations are expected to hinder the growth of the market studied.
- Anti-Slip Coatings market is expected to grow during the forecast period owing to the increasing application in the industrial sector.
- Asia-Pacific region dominated the market across the globe with the largest consumption from countries such as China, India, and Japan.
Anti-Slip Coatings Market Trends
This section covers the major market trends shaping the Anti-Slip Coatings Market according to our research experts:
Growing Application in Industrial Sector
- Anti-Slip Coatings are coatings used on floor, deck, railings, ramps and other areas for non-slippy nature. It is a coating formulated with a fine texture finish that is durable, easy to clean and chemically resistant. It is suitable for recreational, industrial environments and all other required areas.
- Anti-Slip Coatings adhere to concrete, metal, wood and other surfaces. It is fire retardant when dry and has excellent chemical resistance to oil, gasoline, acids, caustics, hydraulic fluids, and most solvents.
- Stringent regulations from government to maintain industrial safety are increasing the application of anti-slip coatings in industries
- About 296 Approved Cold Chain Projects in Food Processing have been approved in India as on May 2019 creating a major scope for the usage of anti-slip coatings in the industry.
- Industrial sector leads in the utilization of anti-slip coatings with China, Germany, United States, India, Japan playing a major role in this market.
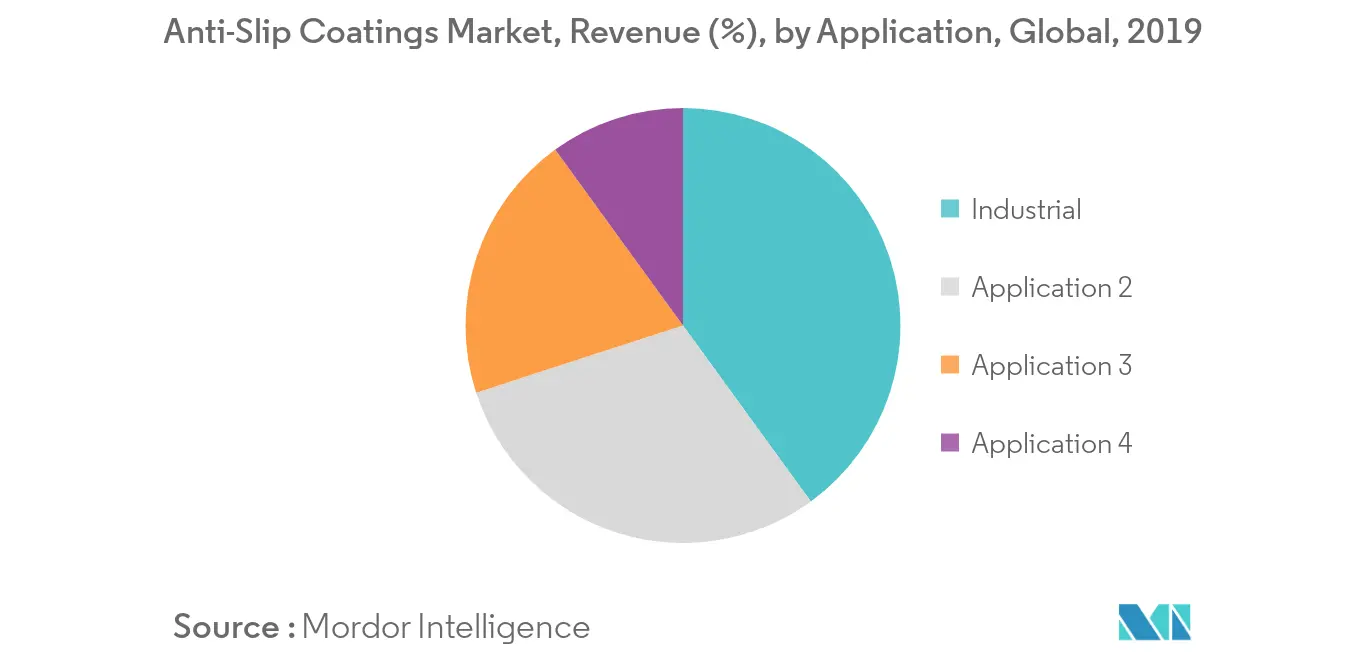
Asia-Pacific Region to Dominate the Market
- Asia-Pacific region is expected to dominate the market for anti-slip coatings during the forecast period. In countries like China, India, and Japan because of growing industrial safety, the demand for anti-slip coatings has been increasing in the region.
- The largest producers of anti-slip coatings are located in the Asia-Pacific region. Some of the leading companies in the production of anti-slip coatings are 3M, AkzoNobel N.V., Jotun, Sika AG, Henkel AG & Co. KGaA.
- According to the Ship Builders Association of Japan, the gross tonnage of ship size covered 14,354 by end of June 2019 which was 15,097 tonnage by the end of December 2018 creating growth in the market of anti-slip coatings.
- These anti-slip coatings can be used in wet areas, dry areas, clean room areas, and other workspaces as a safety measure in industries.
- The aforementioned factors coupled with government support are contributing to the increasing demand for anti-slip coatings market during the forecast period.
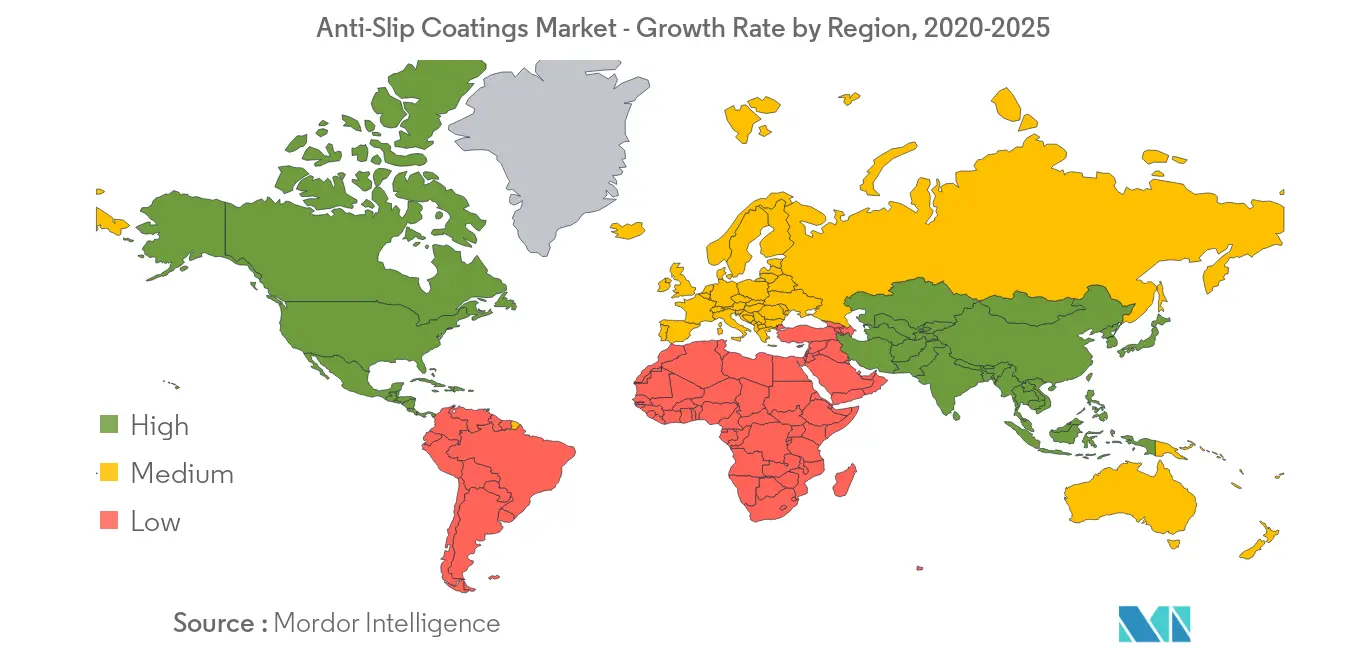
Anti-Slip Coatings Industry Overview
The global anti-slip coatings market is fragmented with players accounting for a marginal share of the market. Few companies include are AkzoNobel N.V., PPG Industries, Axalta Coating Systems, The Sherwin-Williams Company, Jotun.
Anti-Slip Coatings Market Leaders
Jotun
PPG Industries, Inc.
Akzo Nobel N.V.
Axalta Coating Systems
The Sherwin-Williams Company
*Disclaimer: Major Players sorted in no particular order
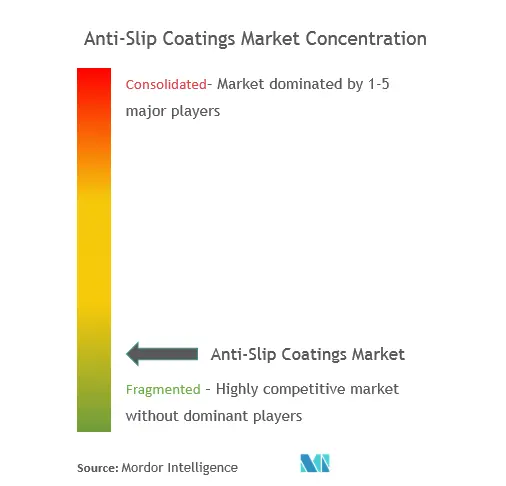
Anti-Slip Coatings Market Report - Table of Contents
-
1. INTRODUCTION
-
1.1 Study Assumptions
-
1.2 Scope of the Study
-
-
2. RESEARCH METHODOLOGY
-
3. EXECUTIVE SUMMARY
-
4. MARKET DYNAMICS
-
4.1 Drivers
-
4.1.1 Increasing Application in Manufacturing Sector
-
4.1.2 Growing Safety Regulations from Government
-
-
4.2 Restraints
-
4.2.1 Stringent Environmental Regulations
-
4.2.2 Other Restraints
-
-
4.3 Industry Value Chain Analysis
-
4.4 Porter's Five Forces Analysis
-
4.4.1 Threat of New Entrants
-
4.4.2 Bargaining Power of Buyers
-
4.4.3 Bargaining Power of Suppliers
-
4.4.4 Threat of Substitute Products
-
4.4.5 Degree of Competition
-
-
-
5. MARKET SEGMENTATION
-
5.1 Resin Type
-
5.1.1 Epoxy
-
5.1.2 Acrylic
-
5.1.3 Polyurethane
-
5.1.4 Others
-
-
5.2 Technology
-
5.2.1 Water Based
-
5.2.2 Solvent Based
-
-
5.3 Application
-
5.3.1 Residential
-
5.3.2 Commercial
-
5.3.3 Industrial (Includes Marine)
-
5.3.4 Others
-
-
5.4 Geography
-
5.4.1 Asia-Pacific
-
5.4.1.1 China
-
5.4.1.2 India
-
5.4.1.3 Japan
-
5.4.1.4 South Korea
-
5.4.1.5 Rest of Asia-Pacific
-
-
5.4.2 North America
-
5.4.2.1 United States
-
5.4.2.2 Canada
-
5.4.2.3 Mexico
-
-
5.4.3 Europe
-
5.4.3.1 Germany
-
5.4.3.2 United Kingdom
-
5.4.3.3 France
-
5.4.3.4 Italy
-
5.4.3.5 Rest of Europe
-
-
5.4.4 South America
-
5.4.4.1 Brazil
-
5.4.4.2 Argentina
-
5.4.4.3 Rest of South America
-
-
5.4.5 Middle-East and Africa
-
5.4.5.1 Saudi Arabia
-
5.4.5.2 South Africa
-
5.4.5.3 Rest of Middle-East and Africa
-
-
-
-
6. COMPETITIVE LANDSCAPE
-
6.1 Mergers and Acquisitions, Joint Ventures, Collaborations, and Agreements
-
6.2 Market Share/Ranking Analysis**
-
6.3 Strategies Adopted by Leading Players
-
6.4 Company Profiles
-
6.4.1 3M
-
6.4.2 Axalta Coating Systems
-
6.4.3 Akzo Nobel N.V.
-
6.4.4 Hempel A/S
-
6.4.5 Henkel AG & Co. KGaA
-
6.4.6 Jotun
-
6.4.7 PPG Industries, Inc.
-
6.4.8 Randolph Products Co.
-
6.4.9 Sika AG
-
6.4.10 The Sherwin-Williams Company
-
- *List Not Exhaustive
-
-
7. MARKET OPPORTUNITIES AND FUTURE TRENDS
-
7.1 Development of High Efficient Anti-Slip Coatings
-
7.2 Other Opportunities
-
Anti-Slip Coatings Industry Segmentation
The Anti-Slip Coatings Market report include:
Resin Type | |
Epoxy | |
Acrylic | |
Polyurethane | |
Others |
Technology | |
Water Based | |
Solvent Based |
Application | |
Residential | |
Commercial | |
Industrial (Includes Marine) | |
Others |
Geography | |||||||
| |||||||
| |||||||
| |||||||
| |||||||
|
Anti-Slip Coatings Market Research FAQs
What is the current Anti-Slip Coatings Market size?
The Anti-Slip Coatings Market is projected to register a CAGR of 4% during the forecast period (2024-2029)
Who are the key players in Anti-Slip Coatings Market?
Jotun, PPG Industries, Inc., Akzo Nobel N.V., Axalta Coating Systems and The Sherwin-Williams Company are the major companies operating in the Anti-Slip Coatings Market.
Which is the fastest growing region in Anti-Slip Coatings Market?
Asia Pacific is estimated to grow at the highest CAGR over the forecast period (2024-2029).
Which region has the biggest share in Anti-Slip Coatings Market?
In 2024, the Asia Pacific accounts for the largest market share in Anti-Slip Coatings Market.
What years does this Anti-Slip Coatings Market cover?
The report covers the Anti-Slip Coatings Market historical market size for years: 2019, 2020, 2021, 2022 and 2023. The report also forecasts the Anti-Slip Coatings Market size for years: 2024, 2025, 2026, 2027, 2028 and 2029.
Anti-Slip Coatings Industry Report
Statistics for the 2024 Anti-Slip Coatings market share, size and revenue growth rate, created by Mordor Intelligence™ Industry Reports. Anti-Slip Coatings analysis includes a market forecast outlook to 2029 and historical overview. Get a sample of this industry analysis as a free report PDF download.