Aerospace Fasteners Market Size and Share
Aerospace Fasteners Market Analysis by Mordor Intelligence
The aerospace fasteners market size is valued at USD 7.02 billion in 2025. It is forecast to reach USD 10.12 billion by 2030, advancing at a 7.59% CAGR as commercial and defense aircraft programs return to growth. Heightened production rates for single-aisle jets, demand for next-generation military aircraft, and the rise of electric vertical-takeoff-and-landing (eVTOL) fleets are the primary engines that will keep assembly lines active and lift aftermarket volumes. Aircraft OEMs are moving to higher-strength, lighter alloys and automated robotic fastening to meet record backlogs. At the same time, urban-air-mobility platforms expand the application base for small, high-cycle components. Titanium price volatility and supply-chain shocks such as the February 2025 Precision Castparts plant fire underscore the need for diversified sourcing and greater inventory buffers. At the same time, environmental rules phasing out cadmium plating accelerate the adoption of zinc-nickel and other compliant coatings in the aerospace fasteners market.
Key Report Takeaways
- By product type, bolts and screws led the aerospace fasteners market with a 35.71% share in 2024, whereas specialty panel fasteners are projected to advance at a 9.32% CAGR through 2030.
- By material, titanium-alloy fasteners captured 32.87% of the aerospace fasteners market share in 2024, while composite-compatible polymer fasteners are forecasted to post the fastest 10.65% CAGR to 2030.
- By application, commercial aviation accounted for a 60.12% revenue share of the aerospace fasteners market in 2024; unmanned aerial vehicles represent the quickest-expanding application, with a 9.81% CAGR through 2030.
- By end-user, the commercial segment held 65.82% of the aerospace fasteners market share in 2024, while the military segment records the highest expected 8.21% CAGR during 2025-2030.
- By geography, North America maintained a 35.76% share of the aerospace fasteners market in 2024; Asia-Pacific is set to grow the fastest at a 9.25% CAGR over the forecast period.
Global Aerospace Fasteners Market Trends and Insights
Drivers Impact Analysis
Driver | ( ~ ) % Impact on CAGR Forecast | Geographic Relevance | Impact Timeline |
---|---|---|---|
Accelerated growth in commercial aircraft production and deliveries | +1.8% | North America and Europe | Medium term (2-4 years) |
Fleet-modernisation and lightweighting push | +1.5% | Global | Long term (≥ 4 years) |
Increased procurement of next-generation military aircraft | +1.2% | North America, Europe, Asia-Pacific | Medium term (2-4 years) |
Expansion of global MRO infrastructure and aftermarket demand | +1.0% | Asia-Pacific and Middle East | Long term (≥ 4 years) |
Adoption of automated robotic fastening in complex assembly lines | +0.8% | North America and Europe | Medium term (2-4 years) |
Rising fastener demand from emerging urban air mobility (eVTOL) platforms | +0.6% | Global | Long term (≥ 4 years) |
Source: Mordor Intelligence
Accelerated growth in commercial aircraft production and deliveries
Record backlogs exceeding 8,600 aircraft at Airbus and 6,100 at Boeing translate directly into rising orders for certified bolts, screws, rivets, and specialty panel fasteners.[1]Cascadia Capital, “Commercial Aerospace Report,” cascadiacapital.com Single-aisle jets, which each require nearly 1 million fasteners, are the focal point of the ramp-up, stretching supplier capacity and allowing premium pricing for high-volume lines. LISI AEROSPACE reported EUR 838.9 million (USD 986.70 million) in 2024 revenue, a 17% jump linked to single-aisle build rates and 26.5% growth in European fastener operations.[2]LISI Group, “2024 Financial Results,” lisi-group.com Embraer’s outlook for 10,500 new sub-150-seat jets augments long-term demand beyond traditional narrowbody programs. Automated assembly cells built around laser-guided robots boost throughput and consistency across the aerospace fasteners market.
Fleet-modernisation and lightweighting push
Airlines targeting 15-20% fuel-burn cuts increasingly specify advanced alloys and integrated fastening solutions that reduce aircraft empty weight. Titanium grades such as Ti-6Al-2Sn-2Zr-2Mo-2Cr provide up to 30% weight savings over steel counterparts while meeting stringent fatigue limits. Composite-compatible polymer fasteners, which avoid galvanic corrosion when joining CFRP skins to metallic frames, post the fastest adoption and are forecast to rise 10.65% annually through 2030. The B787 and A350 airframes show that strategic fastener lightweighting can shave 2-3% of overall structural mass. The drive also extends to specialty panel devices that merge captive nuts, seals, and quick-release features, trimming part counts on high-volume doors and interior modules.
Increased procurement of next-generation military aircraft
Stealth coatings, distributed sensors, and electronic warfare payloads require fasteners that resist electromagnetic interference and high-frequency vibration. The expanding military drone sector, projected to triple in value by 2034, needs miniature titanium fasteners that hold tight tolerances yet remain suitable for cost-effective mass production. The US Department of Defense’s plans to field large unmanned fleets create a shift toward scalable, automated fastener manufacturing rather than the small-lot, bespoke approach historically used for fighters and bombers.
Expansion of global MRO infrastructure and aftermarket demand
The maintenance, repair, and overhaul market is on track to hit USD 119 billion in 2026, lifting recurring consumption of standard parts and driving digital inventory strategies that cut aircraft-on-ground time. India illustrates the trend: MRO spending is expected to quadruple by 2025 as carriers grow domestic fleets and major repair stations open under government incentives. Predictive analytics platforms that forecast fastener wear with more than 95% accuracy reduce surplus stock while ensuring on-time availability, pushing distributors toward wider catalogues and tighter delivery windows.
Restraints Impact Analysis
Restraint | ( ~ ) % Impact on CAGR Forecast | Geographic Relevance | Impact Timeline |
---|---|---|---|
Fluctuating raw material prices impacting cost stability | -1.2% | Global | Short term (≤ 2 years) |
Disruptions in OEM production lines affecting fastener demand cycles | -0.8% | Major manufacturing hubs | Short term (≤ 2 years) |
Increasing adoption of adhesives and integrated composite assemblies reducing fastener usage | -0.6% | North America and Europe, expanding to Asia-Pacific | Medium term (2-4 years) |
Environmental regulations limiting the use of cadmium-plated steel fasteners | -0.4% | Europe and North America, with spillover to global markets | Long term (≥ 4 years) |
Source: Mordor Intelligence
Fluctuating raw-material prices impacting cost stability
Aerospace-grade titanium moved 10.91% higher between early 2024 and late 2025, reaching USD 15-30 per pound, compared with USD 6-10 for commercial grades. The Russia-Ukraine conflict and tightening export controls spur OEMs to lock in volume through multiyear contracts or vertically integrate recycling streams. Aluminum and nickel costs rose on energy-related curbs at European smelters, raising pressure on fastener suppliers to hedge inputs or pass costs to customers.
Disruptions in OEM production lines affecting fastener demand cycles
The February 2025 fire that shut Precision Castparts’ 560,000-sq-ft Pennsylvania facility removed a substantial share of US rivet and hi-lock capacity for at least three months. Boeing’s USD 4.7 billion acquisition of Spirit AeroSystems underscores the imperative to bring critical structures and fastening sub-tiers under tighter OEM control. Certification hurdles under the incoming IA9100 standard complicate the rapid qualification of replacement suppliers, lengthening recovery timelines after single-point failures.
Segment Analysis
By Product Type: Specialty fasteners accelerate automation
Bolts and screws retained the largest 35.71% share in 2024 as primary structures and engines rely on their tensile strength. Specialty panel fasteners, though smaller in absolute volume, are the clear growth engine at 9.32% CAGR to 2030. This niche's aerospace fasteners market size is projected to expand as integrated, flush-mount designs reduce assembly steps on doors, fairings, and interiors. TriMas Aerospace won a global contract covering Airbus A320, A350, and A220 programs, centred on robot-friendly fastener geometries that lower takt time.[3]TriMas Corporation, “Long-Term Contract with Airbus,” trimas.com Adhesive-bonded studs from Click Bond illustrate how eliminating drilling can cut installation time by 60% while avoiding delamination on composite panels. Fast-advance riveting systems valued at USD 185.9 million by 2034 add to automation momentum.
In parallel, demand for nuts, collars, pins, and inserts remains steady as OEMs standardize self-locking and self-sealing variants that meet high-bypass engines' and rotorcraft's vibration and leakage limits. Blind rivets serve one-sided-access sections of wings and fuselages, benefiting from new alloys offering 10% higher shear strength at equal mass. Together, these trends sustain the aerospace fasteners market even as total part count per airframe falls.
Note: Segment shares of all individual segments available upon report purchase
By Material: Composite-compatible polymers gain traction
Titanium alloys led with a 32.87% share in 2024, a position they will likely maintain given superior weight-to-strength and corrosion resistance. Yet composite-compatible polymer fasteners register the highest 10.65% CAGR as carbon-fiber skins proliferate. Aluminum alloys remain vital for legacy aluminum fuselages, while high-temperature nickel super-alloys secure engine and exhaust placements.
The aerospace fasteners market share tied to titanium may widen as recycling technology matures; IperionX and Vegas Fastener are partnering to supply recycled titanium hardware for the US Army, signalling growing acceptance of circular-material flows. Meanwhile, EJOT’s FLOWpoint DELTA PT screws drive direct fastening into CFRP without pilot holes, avoiding conductive galvanic couples. Such innovations allow OEMs to eliminate metallic inserts and save weight on flight-critical joints.
By Application: UAVs emerge as growth driver
Commercial aviation generated 60.12% of 2024 revenue, reflecting the scale of airline backlogs and sizeable MRO demand. However, unmanned aerial vehicles (UAVs) pace the field at 9.81% CAGR thanks to expanding defense procurement and civilian drone services. Military aircraft preserve steady replacement demand as nations modernize their fleets.
UAV requirements differ: designers favour lightweight aluminum or composite fasteners that tolerate rapid thermal swings and meet tight cost caps. Additive manufacturing accelerates prototype-to-production cycles, with 3D-printed nylon-carbon filament fasteners already seeing qualification on low-risk drone subsystems. The eVTOL segment also demands compact, high-cycle locking systems certified for thousands of daily take-off and landing events, widening the aerospace fasteners market beyond conventional fixed-wing domains.
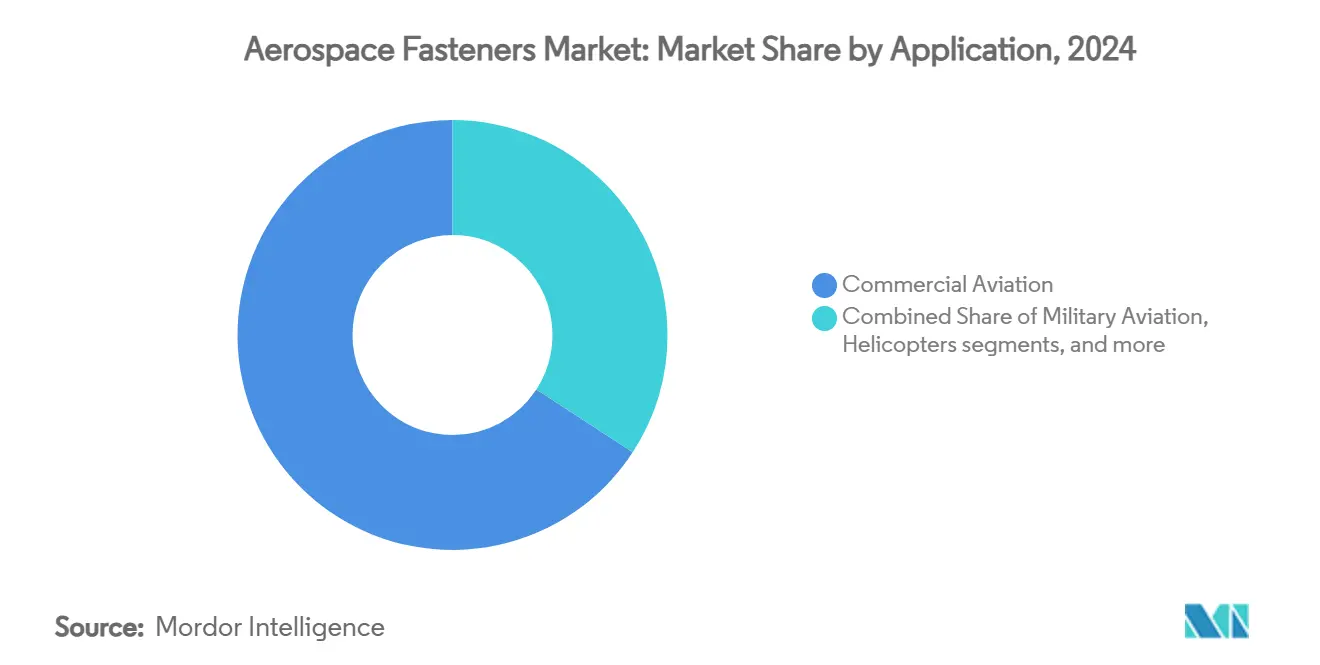
Note: Segment shares of all individual segments available upon report purchase
By End-User: Military segment accelerates
Commercial operators accounted for a 65.82% share in 2024, buoyed by extensive fleet sizes and recurring overhaul needs. The military segment, though smaller, rises at 8.21% CAGR on the strength of drone swarms, sixth-generation fighter programs, and space-based defense projects. NATO standardization pushes suppliers to offer catalogues that meet multiple national designations, consolidating volume despite bespoke mission profiles. Rapid-fielding doctrines also spur demand for designs manufacturable at forward bases via additive processes, a notable shift in procurement philosophy that supports agile supply.
Geography Analysis
North America led the aerospace fasteners market with 35.76% share in 2024, anchored by Boeing’s production centers, extensive defense budgets, and the world’s largest network of MRO facilities. Howmet Aerospace posted record Q1 2025 revenue and a 28.8% EBITDA margin, reflecting robust domestic demand. The Precision Castparts plant fire exposed supply-chain fragility, prompting policy moves to expand domestic titanium output and diversify regional fastener capacity. Government initiatives now support recycling and new mine feasibility studies to minimize import reliance.
Asia-Pacific is the clear growth engine at 9.25% CAGR to 2030. India exemplifies momentum: Boeing alone sources over USD 1.25 billion annually from local suppliers, while policy incentives under the Production-Linked scheme aim to lift aerospace value addition locally.[4]The STAT Trade Times, “Boeing’s India Sourcing,” stattimes.com China’s COMAC C919, carrying more than 1,000 orders, will lift regional fastener volumes as annual production climbs toward 200 jets by 2029. China’s 60% share of global titanium production provides material leverage, though aerospace-grade quality gaps still require imports for critical parts.
Europe maintains a mature yet pivotal position backed by Airbus ramps and strong aftermarket activity. The European Court of Justice annulled earlier chromium VI authorizations, accelerating the industry toward trivalent alternatives and placing compliance pressure on coating lines. LISI AEROSPACE recorded double-digit growth across eight straight quarters, highlighting recovery at key French and German plants. Brexit continues to reshape logistics, with several suppliers establishing dual inventory hubs to serve EU and UK customers without customs delays.
South America benefits from Embraer programs and the rise of regional MRO centers, though currency volatility moderates near-term investment. While smaller today, the Middle East and Africa see long-range fleets and local overhaul clusters emerging in the Gulf states, gradually expanding the aerospace fasteners market footprint.
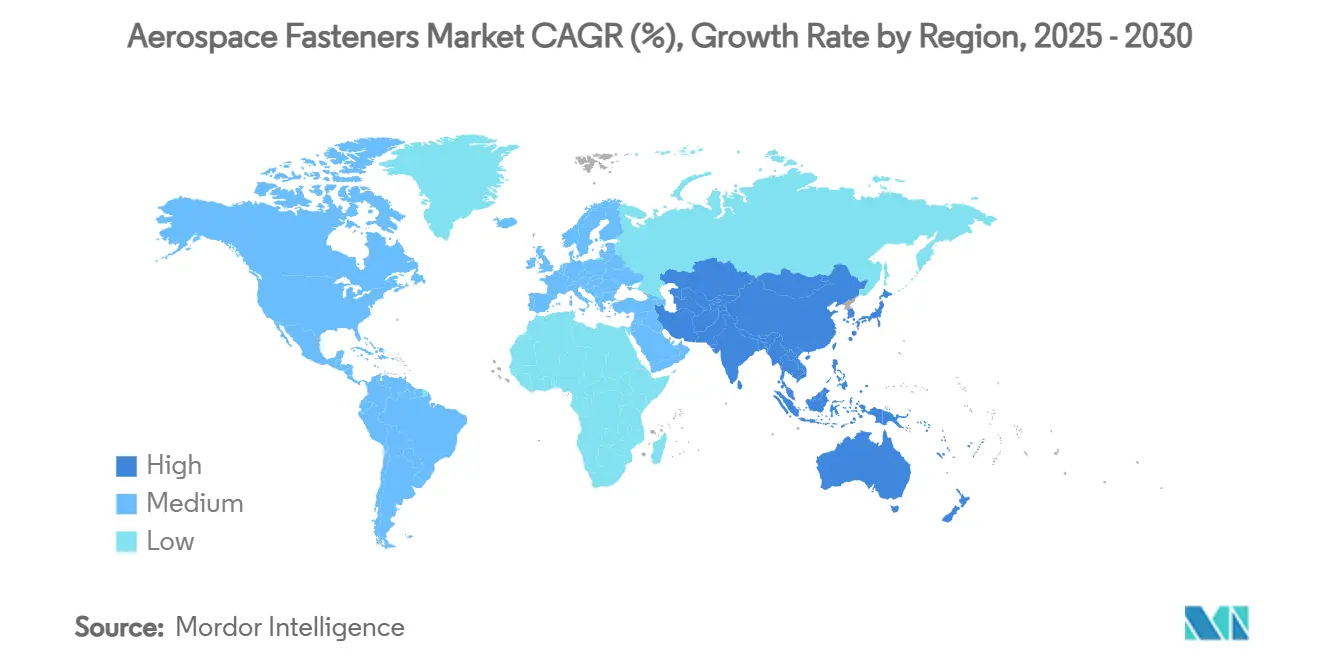
Competitive Landscape
The aerospace fasteners market remains moderately consolidated, characterized by high qualification barriers and sustained capital intensity. Leading producers leverage vertical integration, proprietary alloys, and automated lines to secure multiyear contracts at favorable terms. Howmet Aerospace exemplifies scale advantages, raising dividends on the back of 12% revenue growth and strong Fastening Systems margins.
TriMas Aerospace’s global agreement with Airbus reflects OEMs’ push for fewer, dependable partners capable of supporting future robotized assembly cells. Nord-Lock’s Superbolt Load-Sensing Tensioner illustrates how smart-fastener technology differentiates offers by providing preload data with ±5% accuracy and remote monitoring, a capability prized for fleet-wide predictive maintenance.
Consolidation continues: Barnes acquired MB Aerospace to expand its reach in turbine-engine components, while Novaria folded in Anillo Industries to broaden its scope in specialty fasteners. Environmental regulation accelerates R&D on cadmium-free plates and hexavalent-chromium alternatives, creating a niche for early-mover suppliers skilled in eco-compliant coatings. White-space opportunities include eVTOL-specific fastening solutions and additive-ready designs for rapid battlefield repair.
Aerospace Fasteners Industry Leaders
-
Stanley Black & Decker, Inc.
-
TriMas Corporation
-
Howmet Aerospace Inc.
-
LISI Aerospace (LISI Group)
-
Precision Castparts Corp. (Berkshire Hathaway Inc.)
- *Disclaimer: Major Players sorted in no particular order
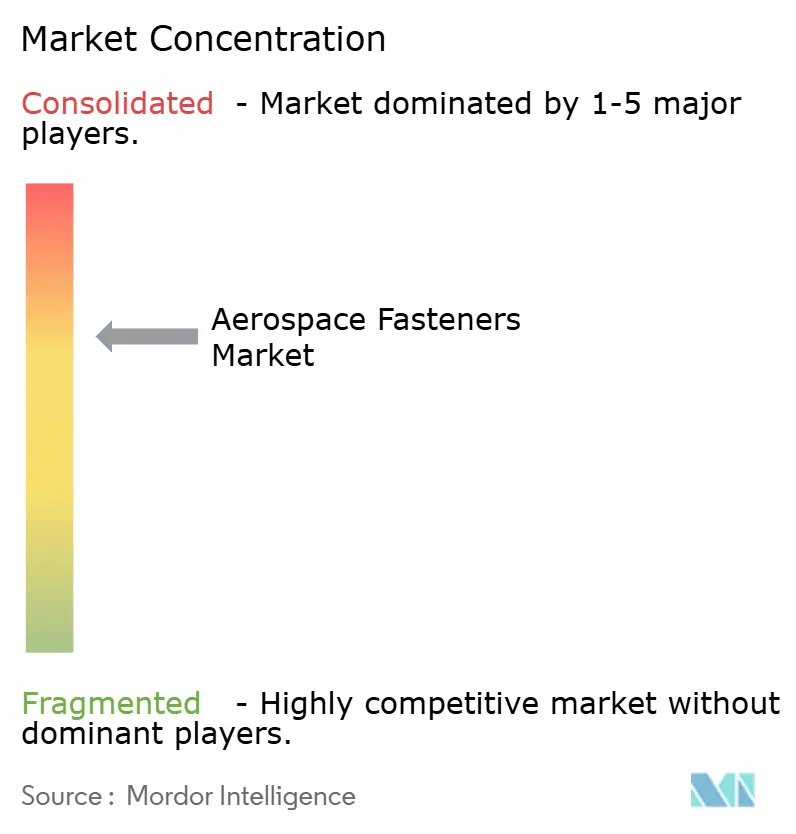
Recent Industry Developments
- June 2025: IperionX Limited secured a USD 99 million Small Business Innovation Research Phase III contract from the US Department of Defense to supply titanium components, including high-performance fasteners, supporting domestic titanium production for defense applications.
- February 2025: TriMas Corporation secured a multi-year global contract with Airbus covering A320, A350, and A220 programs, focused on robotic-assembly-ready fasteners.
Global Aerospace Fasteners Market Report Scope
The aerospace fasteners include rivets, screws, nuts, bolts, clamps, and aircraft fittings in the various parts of an aircraft. The report study excludes the use of fasteners in space applications.
The aerospace fasteners market is segmented by application, material, and geography (North America, Europe, Asia-Pacific, Latin America, and the Middle East and Africa). By application, the market is segmented into commercial aircraft, military aircraft, and general aviation aircraft. By material, the market is segmented into aluminum, steel, superalloys, and titanium. The report also covers the market sizes and forecasts for the aerospace fasteners market in major countries across different regions.
For each segment, the market size is provided in terms of value (USD).
By Product Type | Bolts and Screws | |||
Nuts and Collars | ||||
Rivets and Blind Fasteners | ||||
Pins and Inserts | ||||
Specialty/Panel Fasteners | ||||
By Material | Aluminum Alloy | |||
Titanium Alloy | ||||
Stainless and Alloy Steel | ||||
Super-Alloys | ||||
Composite-compatible Polymer Fasteners | ||||
By Application | Commercial Aviation | |||
Military Aviation | ||||
General and Business Aviation | ||||
Helicopters | ||||
Spacecraft and Launch Vehicles | ||||
Unmanned Aerial Vehicles (UAVs) | ||||
By End-User | Commercial | |||
Military | ||||
By Geography | North America | United States | ||
Canada | ||||
Mexico | ||||
Europe | Germany | |||
United Kingdom | ||||
France | ||||
Italy | ||||
Spain | ||||
Rest of Europe | ||||
Asia-Pacific | China | |||
India | ||||
Japan | ||||
South Korea | ||||
Rest of Asia-Pacific | ||||
South America | Brazil | |||
Rest of South America | ||||
Middle East and Africa | Middle East | Saudi Arabia | ||
United Arab Emirates | ||||
Rest of Middle East | ||||
Africa | South Africa | |||
Rest of Africa |
Bolts and Screws |
Nuts and Collars |
Rivets and Blind Fasteners |
Pins and Inserts |
Specialty/Panel Fasteners |
Aluminum Alloy |
Titanium Alloy |
Stainless and Alloy Steel |
Super-Alloys |
Composite-compatible Polymer Fasteners |
Commercial Aviation |
Military Aviation |
General and Business Aviation |
Helicopters |
Spacecraft and Launch Vehicles |
Unmanned Aerial Vehicles (UAVs) |
Commercial |
Military |
North America | United States | ||
Canada | |||
Mexico | |||
Europe | Germany | ||
United Kingdom | |||
France | |||
Italy | |||
Spain | |||
Rest of Europe | |||
Asia-Pacific | China | ||
India | |||
Japan | |||
South Korea | |||
Rest of Asia-Pacific | |||
South America | Brazil | ||
Rest of South America | |||
Middle East and Africa | Middle East | Saudi Arabia | |
United Arab Emirates | |||
Rest of Middle East | |||
Africa | South Africa | ||
Rest of Africa |
Key Questions Answered in the Report
What is the current value of the aerospace fasteners market?
The market is worth USD 7.02 billion in 2025 and is projected to rise to USD 10.12 billion by 2030, advancing at a 7.59% CAGR.
Which region leads the aerospace fasteners market?
North America holds the largest 35.76% share, backed by Boeing’s production lines and extensive MRO infrastructure.
Which segment is growing fastest within the aerospace fasteners market?
Unmanned aerial vehicles (UAVs) show the highest 9.81% CAGR through 2030 as defense and commercial drone fleets expand.
Why are titanium fasteners so important in aerospace?
Titanium offers a superior strength-to-weight ratio and corrosion resistance, enabling up to 30% weight savings versus steel in critical joints.
How is automation changing aerospace fastener production?
OEMs are adopting robotic assembly lines and smart fasteners that provide real-time preload data, improving consistency and lowering takt time.
What impact do environmental regulations have on fastener coatings?
The phase-out of cadmium and chromium VI coatings is accelerating the shift to zinc-nickel and trivalent-chromium alternatives that meet toxicity and outgassing limits.
Page last updated on: July 3, 2025