Aerospace Composites Market Analysis by Mordor Intelligence
The aerospace composites market is valued at USD 35.18 billion in 2025 and is projected to reach USD 57.77 billion by 2030, registering a 10.43% CAGR over the forecast period. Strong demand for lightweight structures that enhance fuel efficiency, expanding hypersonic programs, and the growing need for recyclable materials are the central forces shaping the aerospace composites market. Automated fiber placement (AFP) systems delivering 4–8 times higher throughput than legacy lay-up lines, the rapid uptake of thermoplastics in single-aisle backlogs, and fleet electrification requirements for high-temperature parts are among the most influential growth drivers. Major aircraft OEMs vertically integrate composite production to control quality and cost, intensifying supplier competition and accelerating qualification cycles for novel resins. Asia’s expanding manufacturing base and rising investments in electric propulsion are turning the region into the fastest-growing hub in the aerospace composites market.
Key Report Takeaways
- By fiber type, carbon fiber held 52.51% of the aerospace composites market share in 2024, while ceramic fiber is forecast to expand at a 10.92% CAGR through 2030.
- By resin type, thermosets led with 46.12% revenue share in 2024, but thermoplastics are advancing at a 13.51% CAGR to 2030.
- By manufacturing process, prepreg lay-up accounted for a 44.71% share in 2024; AFP registered the fastest growth at a 13.05% CAGR.
- By aircraft type, commercial narrow-body aircraft captured 38.50% of the aerospace composites market size in 2024, whereas spacecraft/launch vehicles are expected to grow at a 14.90% CAGR.
- By structural component, exterior and airframe parts represented a 50.51% share of the aerospace composites market in 2024; engine parts are growing the quickest at a 17.81% CAGR.
- By end-user, OEMs dominated with an 80.51% share in 2024, while the aftermarket/MRO segment is projected to rise at 9.00% CAGR.
- By region, North America held 30.05% of global revenue in 2025; the Asia-Pacific region is poised for a 10.10% CAGR through 2030.
Global Aerospace Composites Market Trends and Insights
Drivers Impact Analysis
Driver | (~) % Impact on CAGR Forecast | Geographic Relevance | Impact Timeline |
---|---|---|---|
Rapid adoption of thermoplastic composites to accelerte production rates of single-aisle programs (Europe-led) | +2.5% | Europe-led global | Medium term (2-4 years) |
Increasing penetration of carbon fiber in next-gen narrow-body wings in North America | +1.8% | North America, Europe | Medium term (2-4 years) |
Fleet eletrification and more-electric aircraft (MEA) driving high-temperature composite demand in Asia | +1.2% | Asia, global | Medium term (2-4 years) |
Space-launch commercialization boosing demand for lightweight composite structures | +2.0% | US, China, global | Short term (≤2 years) |
Military stealth programs propelling ceramic-matrix composite uptake in hypersonic applications | +1.5% | US, China, Russia | Medium term (2-4 years) |
OEM sustainability targets pushing recyclable composite solutions | +1.0% | Europe-led global | Long term (≥5 years) |
Source: Mordor Intelligence
Rapid Adoption of Thermoplastic Composites
Collins Aerospace demonstrates that thermoplastic aerostructures cut production cycles by 80%, eliminate autoclave curing, and are nearly 100% recyclable.[1]Collins Aerospace, “Thermoplastic Composites for High-Rate Aircraft Production,” collinsaerospace.comEuropean single-aisle programs have embraced the material to reduce delivery backlogs. At the same time, an Arkema-Hexcel partnership produced the first fully thermoplastic commercial aircraft structure, validating large-scale out-of-autoclave fabrication. High recyclability aligns with emerging sustainability mandates, positioning thermoplastics as a cornerstone of future aerospace composites market expansion.
Increasing Penetration of Carbon Fiber in Next-Gen Narrow-Body Wings
Airbus’s eXtra Performance Wing testbed incorporates extensive CFRP skins to lower drag and cut CO₂, showcasing the build feasibility of 32 m-long carbon-fiber wingskins.[2]Airbus, “Extra Performance Wing and Bio-Fiber Panels Advance Sustainable Aviation,” airbus.com North American programs perform parallel studies, aiming to match or exceed European CFRP usage. Weight savings of up to 50% versus aluminum and AFP throughput gains directly address the aerospace composites market backlog challenge.
Fleet Electrification and More-Electric Aircraft
Electric propulsion subsystems require composite housings that endure 450°F operating environments; Hexcel’s high-temperature Flex-Core HRH-302 honeycomb meets this need. Asian manufacturers leverage electronics experience to integrate thermal management layers into composite skins, driving regional demand. The evolution of battery and fuel-cell architectures is expected to stimulate orders for hybrid polymer-ceramic laminates across the aerospace composites market.
Space Launch Commercialization
Reusable launchers depend on lightweight fairings; Chinese supplier Monks Aviation delivered composite fairings 30% lighter than metal designs for the Ceres-1 program. Parallel European initiatives are developing all-composite LH₂ tanks to TRL 5, underscoring strong market pull from private launch ventures. The spacecraft segment’s 14.90% CAGR positions it as the most dynamic pocket of the aerospace composites market.
Restraints Impact Analysis
Restraint | (~) % Impact on CAGR Forecast | Geographic Relevance | Impact Timeline |
---|---|---|---|
High preform and autoclave capital costs limiting adoption in tier-2 suppliers | -1.8% | Global, emerging markets | Short term (≤2 years) |
Supply-chain volatility for aerospace-grade precursors for PAN-based carbon fiber | -2.0% | Global | Short term (≤2 years) |
Qualification and certification delays for novel resin systems with FAA/EASA | -1.5% | Regulated markets | Medium term (2-4 years) |
Limited repairability expertise for advanced thermoplastics in MRO sector | -0.8% | Global | Long term (≥5 years) |
Source: Mordor Intelligence
High Preform and Autoclave Capital Costs
Aerospace-grade autoclaves cost USD 5–10 million and require extensive infrastructure, deterring Tier-2 entrants. Out-of-autoclave thermoplastic welding and resin infusion are emerging as lower-investment alternatives that can broaden supplier participation across the aerospace composites market.
Supply-Chain Volatility of Aerospace-Grade Precursors
Major OEMs formed the Aviation Supply Chain Integrity Coalition to harden vendor accreditation and part traceability after recurring precursor shortages disrupted deliveries. Efforts include stricter non-conformance audits and digital tracking, but raw-material lead times remain an ongoing risk within the aerospace composites market.
Segment Analysis
By Fiber Type: Ceramic Fibers Expand Heat-Resistant Envelope
Carbon fiber retained 52.51% of the aerospace composites market share in 2024, thanks to mature supply chains and superior stiffness-to-weight ratios. Ceramic fibers, however, are pacing the segment with a 10.92% CAGR, propelled by hypersonic and space vehicle demand for 1,500 °C capability.[3]Mitsubishi Chemical Group, “Ultra-High-Temperature Ceramic Matrix Composites for Space,” m-chemical.co.jp Hybrid laminates combining carbon and ceramic plies are gaining favor among engine OEMs aiming to cut cooling air draw by 25%. Graphene-enhanced rovings under evaluation show 20–30% modulus boosts while embedding strain-sensing pathways, a step toward self-monitoring wingskins.
The cost-effective positioning of glass fiber maintains relevance in radome and fairing skins, while aramid fibers sustain a share in ballistic-resistant helicopter floors. Continued material innovation supports diversification, yet carbon and ceramic remain the backbone of the aerospace composites market size throughout the forecast horizon.
Note: Segment shares of all individual segments available upon report purchase
By Resin Type: Thermoplastics Challenge Thermoset Dominance
Thermoset epoxy and BMI systems commanded 46.12% of 2024 revenue because of an extensive qualification pedigree. Thermoplastic PEKK and PEI families are surging at a 13.51% CAGR, driven by 80% cycle-time reductions cited by Collins Aerospace. The aerospace composites market size for thermoplastics is projected to exceed USD 17 billion by 2030 as AFP lines pivot to in-situ consolidation. Bio-based resins pioneered by SHD Composites offer near-100% renewable content and withstand 200 °C service, aligning environmental targets with mechanical integrity.
Qualification momentum is accelerating: the FAA has already cleared welded thermoplastic control surfaces for business jets, signaling an imminent broadening of use cases across the aerospace composites industry.
By Manufacturing Process: AFP Transforms High-Rate Production
Prepreg lay-up delivered 44.71% of the 2024 value, yet AFP and automated tape laying are expanding at 13.05% CAGR as Electroimpact’s AFP 4.0 attains 99% quality compliance while quadrupling throughput on identical capital. The aerospace composites market size linked to AFP equipment installations is expected to outpace all other processes through 2030. RTM adoption is climbing for complex engine nacelles; additive composite printing remains nascent but offers topology-optimized brackets that cut buy-to-fly ratios by 80%. Under FAA assessment, the resin infusion for transport fuselages promises to shave operating costs in thin-walled shells, widening market accessibility.
By Aircraft Type: Spacecraft Lead Growth amid Commercial Recovery
As Airbus and Boeing cleared pandemic order backlogs, commercial narrow-bodies contributed the largest slice, 38.50% in 2024. The spacecraft and launch-vehicle category will grow at a 14.90% CAGR, reflecting private-launch proliferation and satellite constellation demand. Military fleets remain a resilient buffer, with stealth fighters integrating radar-absorbing CFRP skins. Business jets and rotorcraft incrementally raise composite content for range and payload gains. Emerging eVTOL craft call for high-rate thermoplastic fuselages, adding a fresh volume stream to the aerospace composites market.
By Structural Component: Engines Drive Advanced-Material Uptake
Exterior skins and primary airframe members occupied 50.51% of 2024 revenue, yet engine components will climb fastest at 17.81% CAGR as CMC shrouds enable 200°F higher turbine entries. The aerospace composites market size attached to engines could nearly triple by 2030 as geared turbofan and open-rotor concepts seek mass and thermal advantages. Multifunctional laminates combining energy storage layers with load paths are under lab trials, pointing to future integration leaps.
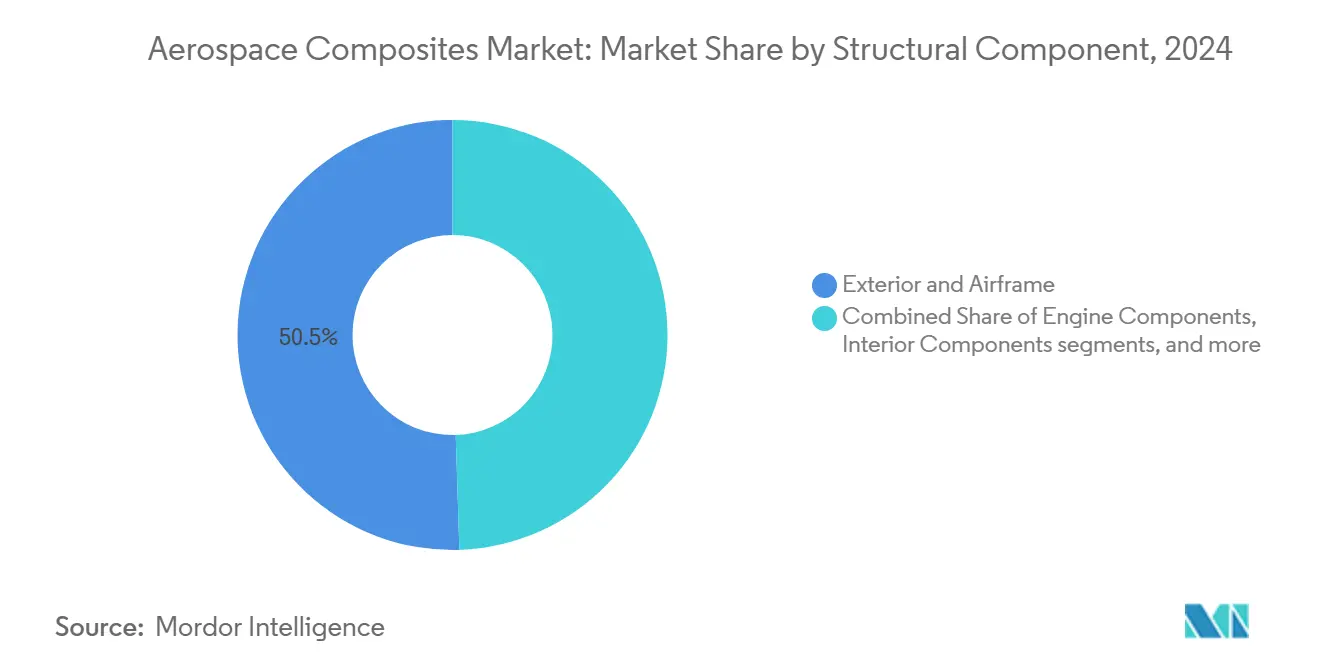
Note: Segment shares of all individual segments available upon report purchase
By End-User: MRO Opportunities Rise in Composite Fleet
OEMs controlled 80.51% of 2024 spend, but MRO is accelerating at 9% CAGR. Collins Aerospace operates eight global autoclave sites to service growing shop visits for composite airframes. GE Aerospace’s USD 1 billion injection into its repair network targets engine composite fan-case throughput to contain airline downtime.[4]GE Aerospace, “2025 Standalone Annual Report,” ge.com As the installed base ages, demand for bonded-patch and scarf-repair expertise will enlarge the aerospace composites market.
Geography Analysis
North America remains the largest regional contributor with a market share of 30.05%, anchored by The Boeing Company, GE Aerospace, and Lockheed Martin Corporation. The region accounts for roughly 75% of North American sales, with Canada’s Montréal cluster supplying high-end nacelles. NASA’s HiCAM program underpins thermoplastic welding certification, reinforcing domestic supply chains.
Europe follows, propelled by Airbus and a robust tier network in Germany, France, and the United Kingdom. Aggressive sustainability mandates, such as the EU’s Fit for 55 package, are catalyzing the adoption of bio-based composites. Thermoplastic wineskins under production in Wales exemplify Europe’s commitment to high-rate, low-carbon manufacturing.
Asia-Pacific is the fastest-growing territory with a CAGR of 10.10%, driven by China’s COMAC fleet ramp-up and electric-propulsion R&D hubs in Japan and South Korea. HRC’s new Chinese plant supplies AFP stringers for aerospace and high-speed rail, underscoring manufacturing scale advantages.[5]CompositesWorld Staff, “Out-of-Autoclave Processing Gains Ground,” compositesworld.com India is nurturing a composites corridor around Bengaluru, supplying ISRO launch vehicles and HAL fighters, further enlarging regional aerospace composites market activity.
Latin America, led by Brazil’s Embraer, integrates composites in E2 jet families, while Mexico’s Querétaro cluster fabricates nacelle doors for North American primes. In the Middle East and Africa, the United Arab Emirates’ Strata composites facility and South Africa’s Denel Aerostructures are emerging contributors, aided by offset agreements and skills transfer.
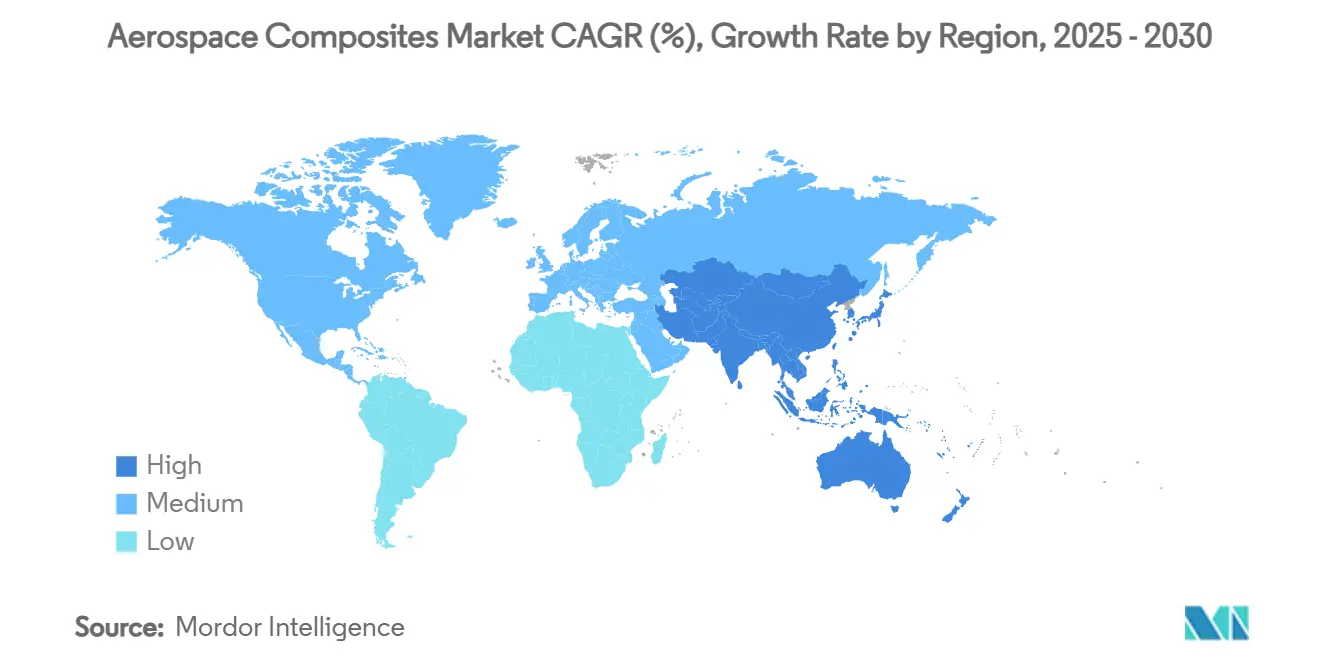
Competitive Landscape
The aerospace composites market shows moderate concentration. Toray dominates intermediate-modulus carbon fiber supply, while Hexcel and Solvay leverage integrated prepreg and honeycomb offerings. Hexcel’s 2024 sales of USD 1.903 billion marked an 11.8% rise in commercial aerospace revenue.
OEM vertical integration is intensifying. Airbus is co-developing thermoplastic ribs with Stelia, and Boeing’s Charleston out-of-autoclave center fabricates B787 skin panels in-house. To maintain share, material firms are forming alliances—Arkema-Hexcel for PEKK tapes and Solvay-Safran for resin transfer-molded fan blades.
Strategic mergers and acquisitions are accelerating. Kineco’s full acquisition of Kineco Kaman Composites India boosts its defense footprint, while Daikin’s stake in Advanced Composite Corporation enhances resin chemistries for thermoplastic fuselages. Investment in AFP, CMC capacity, and recycling plants remains a priority as companies target differentiated positions within the aerospace composites industry.
Aerospace Composites Industry Leaders
-
Hexcel Corporation
-
Solvay
-
SGL Carbon
-
Mitsubishi Chemical Carbon Fiber and Composites, Inc. (Mitsubishi Chemical Group Corporation)
-
Toray Industries, Inc.
- *Disclaimer: Major Players sorted in no particular order
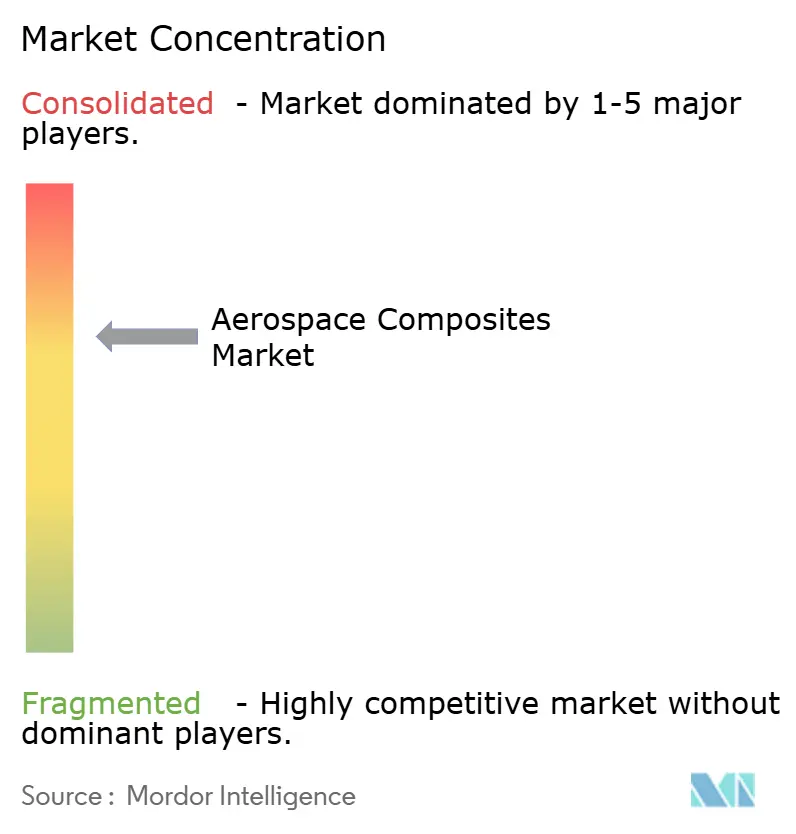
Recent Industry Developments
- June 2024: Airbus flight-tested a bio-fiber nose panel on the H145 PioneerLab, confirming performance parity with conventional carbon fiber.
- April 2024: MIT researchers unveiled “nanostitching” using carbon nanotubes to boost interlaminar toughness by 62%.
- March 2024: Arkema-Hexcel produced the first fully thermoplastic aircraft structure consolidated out-of-autoclave.
- February 2024: Mitsubishi Chemical Group introduced a 1,500 °C-capable ceramic matrix composite for space launch customers.
Global Aerospace Composites Market Report Scope
Aerospace composites are chosen for their ability to provide a combination of lightweight, high strength, corrosion resistance, and fatigue resistance. These characteristics make composites particularly suitable for applications where traditional materials like metals might be less efficient due to their weight or susceptibility to corrosion.
The aerospace composites market includes all applications of composites in military aircraft, commercial aircraft, general aviation aircraft, and spacecraft. Fiber type, application, and geography segment the aerospace composites market. By fiber type, the market is segmented into glass fiber, carbon fiber, ceramic fiber, and other fiber types. By application, the market is segmented into commercial aviation, military aviation, general aviation, and space. The report also covers the market sizes and forecasts for the aerospace composites market in major countries across different regions. For each segment, the market size is provided in terms of value (USD).
By Fiber Type | Glass Fiber | |||
Carbon Fiber | ||||
Ceramic Fiber | ||||
Aramid Fiber | ||||
Other Fiber Types | ||||
By Resin Type | Thermoset Composites | |||
Thermoplastic Composites | ||||
By Manufacturing Process | Lay-Up (Hand and Automated) | |||
Resin Transfer Molding (RTM) | ||||
Filament Winding | ||||
Injection/Compression Molding | ||||
Automated Fiber Placement and Tape Laying | ||||
Additive Manufacturing of Composites | ||||
By Aircraft Type | Commercial Aircraft | Narrow-Body | ||
Wide-Body | ||||
Regional Jets | ||||
Freighters | ||||
Business Jets | ||||
Military Aircraft | Fighter Jets | |||
Transport and Tanker | ||||
Rotorcraft | ||||
Helicopters | ||||
Spacecraft and Launch Vehicles | ||||
By Structural Component | Interior Components | |||
Exterior and Airframe | ||||
Engine Components | ||||
Auxiliary Structures | ||||
By End-User | OEM | |||
Aftermarket/MRO | ||||
By Geography | North America | United States | ||
Canada | ||||
Mexico | ||||
Europe | United Kingdom | |||
Germany | ||||
France | ||||
Rest of Europe | ||||
Asia-Pacific | China | |||
Japan | ||||
India | ||||
South Korea | ||||
Rest of Asia-Pacific | ||||
South America | Brazil | |||
Rest of South America | ||||
Middle East and Africa | Middle East | Saudi Arabia | ||
United Arab Emirates | ||||
Rest of Middle East | ||||
Africa | South Africa | |||
Rest of Africa |
Glass Fiber |
Carbon Fiber |
Ceramic Fiber |
Aramid Fiber |
Other Fiber Types |
Thermoset Composites |
Thermoplastic Composites |
Lay-Up (Hand and Automated) |
Resin Transfer Molding (RTM) |
Filament Winding |
Injection/Compression Molding |
Automated Fiber Placement and Tape Laying |
Additive Manufacturing of Composites |
Commercial Aircraft | Narrow-Body |
Wide-Body | |
Regional Jets | |
Freighters | |
Business Jets | |
Military Aircraft | Fighter Jets |
Transport and Tanker | |
Rotorcraft | |
Helicopters | |
Spacecraft and Launch Vehicles |
Interior Components |
Exterior and Airframe |
Engine Components |
Auxiliary Structures |
OEM |
Aftermarket/MRO |
North America | United States | ||
Canada | |||
Mexico | |||
Europe | United Kingdom | ||
Germany | |||
France | |||
Rest of Europe | |||
Asia-Pacific | China | ||
Japan | |||
India | |||
South Korea | |||
Rest of Asia-Pacific | |||
South America | Brazil | ||
Rest of South America | |||
Middle East and Africa | Middle East | Saudi Arabia | |
United Arab Emirates | |||
Rest of Middle East | |||
Africa | South Africa | ||
Rest of Africa |
Key Questions Answered in the Report
What is the projected size of the aerospace composites market by 2030?
The aerospace composites market is forecast to reach USD 57.77 billion by 2030, growing at a 10.43% CAGR.
Which composite material is growing the fastest in aerospace applications?
Thermoplastic composites are expanding at a 13.51% CAGR due to 80% cycle-time reductions and near-100% recyclability.
Why are ceramic matrix composites important for future engines?
CMCs withstand temperatures above 1,200°C, enabling hotter, more efficient turbines that cut fuel burn and emissions.
Which aircraft segment offers the highest growth for composites?
Spacecraft and launch vehicles lead with a 14.90% CAGR as reusable rockets and satellite constellations drive lightweight-structure demand.
How are OEM sustainability goals influencing material choices?
Targets to reduce life-cycle emissions are accelerating adoption of bio-derived fibers, recyclable thermoplastics and closed-loop carbon-fiber recycling.
What role does AFP technology play in meeting production backlogs?
Automated fiber placement boosts throughput by up to 8-times and reduces labor, enabling OEMs to clear single-aisle order backlogs efficiently.
Page last updated on: June 27, 2025