Sheet Molding And Bulk Molding Compounds Market Size and Share
Sheet Molding And Bulk Molding Compounds Market Analysis by Mordor Intelligence
The Sheet Molding & Bulk Molding Compounds Market size is estimated at USD 4.03 billion in 2025, and is expected to reach USD 5.42 billion by 2030, at a CAGR of 6.09% during the forecast period (2025-2030). Sustained demand for lightweight structural parts in electric vehicles, low scrap rates from compression molding, and improved resin chemistries keep capital flowing into new capacity. Cost reductions per part, especially in complex geometries that previously relied on multi-stage stamping, accelerate the replacement of metal stampings with compression-molded composites across automotive and electrical applications. Original equipment manufacturers now specify advanced sheet molding materials with Class-A finishes, allowing direct exterior use and eliminating secondary paint steps that once limited adoption. Asia-Pacific retains cost-leadership in high-flow, low-density sheet molding compounds, while European regulations on styrene emissions fast-track epoxy-based alternatives.
Key Report Takeaways
- By resin type, polyester retained 55.19% of the sheet molding and bulk molding compounds market share in 2024; epoxy is projected to expand at a 6.92% CAGR through 2030.
- By fiber type, glass fiber led with 80.22% share of the sheet molding and bulk molding compounds market size in 2024; carbon fiber exhibits the fastest 7.06% CAGR to 2030.
- By manufacturing process, compression molding commanded 73.62% of 2024 revenue, while resin transfer molding is set to grow at 6.66% CAGR over 2025-2030.
- By end-user industry, automotive and transportation held 42.74% share of the sheet molding and bulk molding compounds market size in 2024 and is advancing at a 7.14% CAGR.
- By geography, Asia-Pacific captured 48.54% revenue in 2024 and is forecast to expand at a 6.45% CAGR to 2030.
Global Sheet Molding And Bulk Molding Compounds Market Trends and Insights
Drivers Impact Analysis
Driver | (~) % Impact on CAGR Forecast | Geographic Relevance | Impact Timeline |
---|---|---|---|
Light-weighting push from electric and hybrid vehicle OEMs | +1.8% | Global with APAC and North America leading | Medium term (2-4 years) |
Rapid capacity additions in electrical and electronics molding hubs | +1.2% | Primarily APAC with spill-over to North America | Short term (≤ 2 years) |
Cost-effective high-volume compression molding | +1.0% | Global | Long term (≥ 4 years) |
High-flow, low-density sheet molding components for Class-A panels | +0.9% | North America and EU, expanding to APAC | Medium term (2-4 years) |
Integration of in-mold electronics for smart panels | +0.7% | Global with early uptake in premium segments | Long term (≥ 4 years) |
Source: Mordor Intelligence
Light-weighting Push from Electric Vehicles and Hybrid Vehicle OEMs
Electric models move large battery packs, so every kilogram saved extends range. Automakers therefore redesign closures, body panels, and battery housings with advanced sheet molding compounds that cut part weight by up to 40% versus comparable aluminum designs while satisfying crash-load pathways and thermal shielding demands[1]Automotive Manufacturing Solutions, “Lightweight SMC Achieves Weight Savings in EV Battery Covers,” automotivemanufacturingsolutions.com. Tesla, General Motors, and leading Chinese brands have publicly outlined multi-part consolidation strategies that favor single-shot compression molding, reducing weld operations and line takt time. Sheet molding and bulk molding compounds market participants benefit as these programs scale from pilot to full volume production.
Rapid Capacity Additions in Electrical and Electronics Components Molding Hubs
APAC electronics clusters in China, Vietnam, and Malaysia continue installing high-tonnage compression presses equipped with automated material dosing and infrared curing control. Co-location of compounders, molders, and end-device assemblers shortens supply chains and helps manufacturers meet stringent dimensional tolerances required for connector housings and motor insulation systems. Government programs in China that target self-sufficiency in high-performance polymers reinforce this build-out, positioning the region to support global demand spikes.
Cost-effective High-volume Compression Molding versus Metal Stamping
When annual volumes exceed 50,000 parts and geometries are complex, cost models show compression molding outperforms multi-stage stamping by eliminating secondary joining, spot welding, and corrosion-protection steps. Larger fiber volume fractions improve stiffness, allowing thinner wall sections without sacrificing mechanical strength. Tool upkeep for stamping dies is higher over life-of-program metrics than matched-metal compression molds, tipping total cost of ownership calculations toward composites.
High-flow, Low-density Sheet Molding Components Enabling Class-A Body Panels
Gel-coat-ready sheet molding formulations now deliver gloss and surface flatness comparable to painted steel. Incorporation of shrinkage-controlled additives and optimized fiber orientation permits intricate styling cues while preserving dimensional accuracy. Automotive exterior closures that once required paint shops now exit the press in final color, freeing OEMs from volatile organic compound emissions associated with solvent-based coatings.
Restraints Impact Analysis
Restraint | (~) % Impact on CAGR Forecast | Geographic Relevance | Impact Timeline |
---|---|---|---|
Styrene and fiberglass price volatility | -1.4% | Global, higher risk in cost-sensitive markets | Short term (≤ 2 years) |
Engineering thermoplastics replacing SMC in battery boxes | -0.8% | North America and EU, spreading worldwide | Medium term (2-4 years) |
End-of-life recycling hurdles for thermosets | -0.6% | EU and North America with regulatory expansion | Long term (≥ 4 years) |
Source: Mordor Intelligence
Styrene and Fiberglass Price Volatility
Styrene monomer trades in tight cycles, reacting to benzene feedstock swings and shipping constraints. Each USD 100 per ton change in styrene cascades into resin pricing, squeezing margins for small sheet molding compounders that lack long-term supply contracts. Simultaneous fiberglass surcharges further hinder price stability because glass fiber content approaches 65 wt % in many structural grades.
Engineering Thermoplastics Replacing SMC in Battery Boxes
Some battery developers turn to glass-fiber-reinforced polypropylene or PA6 systems delivered through injection molding. These thermoplastic enclosures meet flame-retardance and dielectric requirements while offering recyclability, aligning with circular-economy language now standard in supplier RFQs. For certain pack formats, cycle-time advantages in injection molding offset the higher resin cost, posing a competitive threat to traditional thermoset SMC.
Segment Analysis
By Resin Type: Polyester Dominance Faces Epoxy Challenge
Polyester resin accounted for 55.19% sheet molding and bulk molding compounds market share in 2024 thanks to low cost, broad supplier base, and cure kinetics tailored to legacy compression lines. The segment continues to profit from automotive demand for under-hood covers and structural interior brackets. At the same time epoxy grades post a 6.92% CAGR toward 2030, driven by reduced volatile organic compound content and elevated heat resistance that appeals to electric drivetrain designers. The Evonik-led program for glass-fiber-reinforced epoxy battery housings validated weight reductions approaching 10% while maintaining crush-force thresholds critical to vehicle homologation. As epoxy systems mature, hybrid lay-ups that blend polyester skins with epoxy cores may emerge to balance economics and strength.
By Fiber Type: Glass Fiber Supremacy with Carbon Fiber Innovation
Glass fiber kept 80.22% of 2024 revenue due to favorable cost-to-performance and excellent dielectric strength for electrical parts. Continuous furnace expansions at major glass fiber producers stabilize supply, supporting high-volume automotive launches in Asia-Pacific and North America[2]CompositesWorld, “Glass Fiber-Reinforced Epoxy SMC for Battery Housings,” compositesworld.com . Carbon fiber sheet molding compounds, posting a 7.06% CAGR, gain momentum in aerospace secondary structures and premium sports cars where curb-weight targets override raw-material premiums. Process simulation tools mapping fiber orientation now shorten development cycles, delivering predictable mechanical performance and cutting scrap rates. Hybridized fiber mats that alternate glass and carbon layers help designers hit mid-tier cost targets without compromising stiffness.
By Manufacturing Process: Compression Molding Efficiency Drives Adoption
Compression molding produced 73.62% of 2024 parts by value, attributable to steady press improvements, rapid charge placement robotics, and tighter mold-temperature control. Integrated data logging permits real-time cure-profile optimization, driving overall equipment effectiveness beyond 85%. Resin transfer molding grows at 6.66% CAGR, propelled by interest in thicker structural sections such as truck roofs that benefit from adjustable resin injection fronts and embedded structural foams. The sheet molding and bulk molding compounds market size attached to resin transfer molding thus rises as manufacturers seek higher fiber volumes and premium surfacing.
By End-user Industry: Automotive Leadership Drives Market Evolution
Automotive and transportation held 42.74% share in 2024 and leads growth at 7.14% CAGR, reflecting accelerated electric-vehicle platform refresh cycles. Single-mold lift-gates, pickup boxes, and battery covers reduce weld points and improve corrosion resistance versus steel, attracting both legacy automakers and start-ups. Electrical and electronics follow, supported by miniaturization trends requiring thin-wall flame-retardant housings. Building and construction leverage SMC for corrosion-proof bridge decking and utility enclosures, while aerospace uses carbon-fiber grades for fairings and interior monuments where fire-smoke-toxicity compliance is mandatory.
Note: Segment shares of all individual segments available upon report purchase
Geography Analysis
Asia-Pacific retains the cost advantage that underpins its 48.54% share in 2024. Intensifying domestic EV production, rising middle-class appliance consumption, and government incentives for composite part localization keep presses running near capacity. With estimated demand growth translating to a 6.45% regional CAGR, the sheet molding and bulk molding compounds market continues to shift toward Asian value chains.
North America sits second in regional revenue. Early electric-pickup launches require large structural covers, and aerospace programs consume high-modulus carbon sheet molding compounds for secondary structures. Federal policy that funds onshore battery factories encourages new composite battery-box lines, lifting local compound consumption.
Europe upholds strict environmental rules that spur adoption of low-styrene sheet molding systems and epoxy innovations. Automaker roadmaps that phase out internal combustion between 2030 and 2035 expand demand for lightweight composites. Meanwhile, robust chemical-industry infrastructure supports specialized resin additives that raise mechanical performance and prolong mold life.
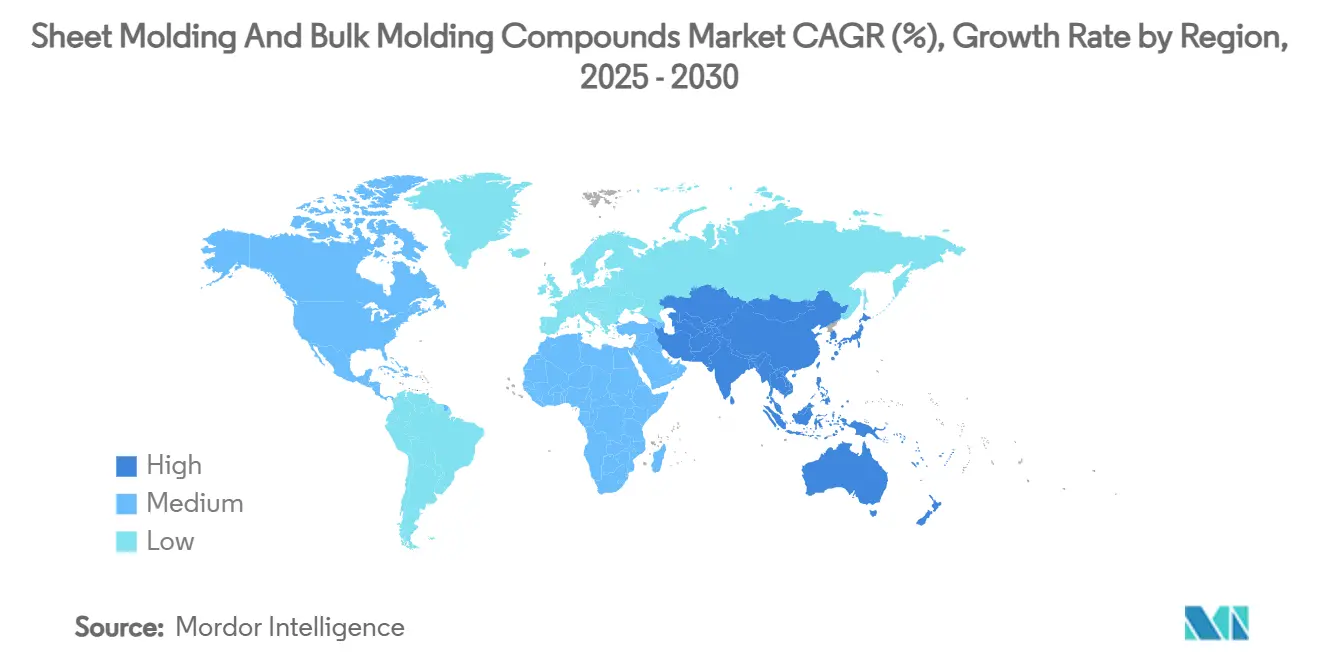
Competitive Landscape
The sheet molding and bulk molding compounds market remains moderately fragmented. AOC, POLYNT SPA, and Core Molding Technologies leverage global production footprints and long-term Tier-1 contracts to anchor share. Regional challengers in China and India differentiate on price and logistics, serving localized demand with shorter lead times. Technology leadership, not capacity, defines competitive edge: AOC introduced low-styrene resin grades that meet EU worker-exposure limits, while Core Molding Technologies integrates sensor foils during molding to monitor in-service strain.
Epoxy-based sheet molding compounds represent the fastest arena for differentiation. Patents surrounding toughening chemistries, cure-cycle reduction, and filler-matrix coupling dominate recent filings, signaling a pivot from cost-driven to performance-driven competition. Suppliers also collaborate with press builders to integrate closed-loop temperature control, cutting scrap and raising throughput.
White-space exists in sustainable resin systems. Start-ups look to bio-based unsaturated polyester precursors and recyclable thermoset architectures to meet 2030 circular-economy targets. Strategic alliances between resin specialists, fiber producers, and Tier-1 molders will likely consolidate knowledge and hasten commercialization.
Sheet Molding And Bulk Molding Compounds Industry Leaders
-
Continental Structural Plastics (Teijin)
-
Polynt-Reichhold
-
IDI Composites International
-
Menzolit
-
Polytec Group
- *Disclaimer: Major Players sorted in no particular order
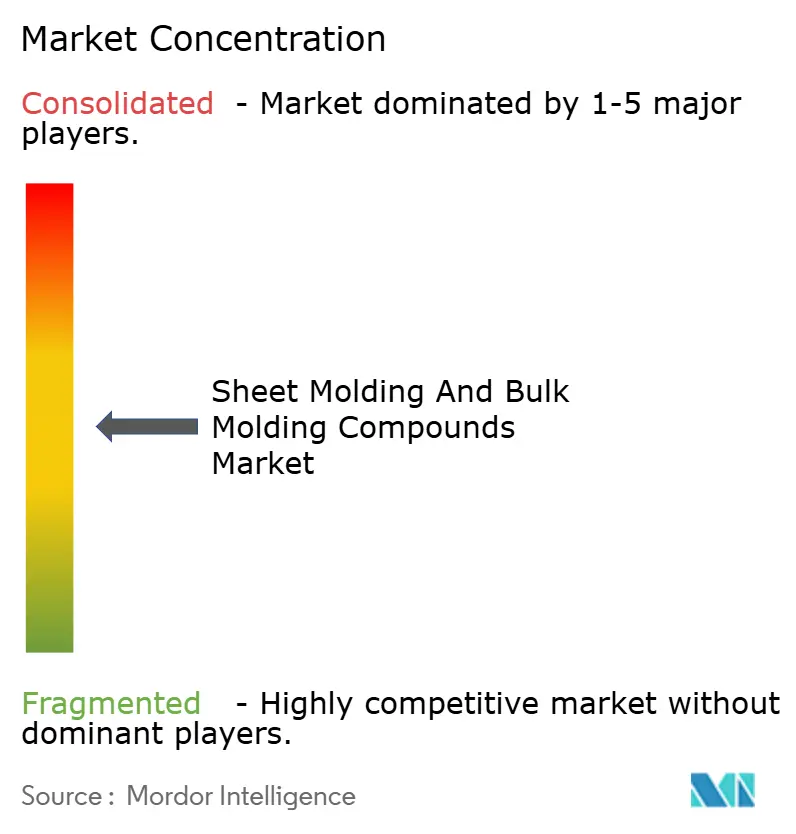
Recent Industry Developments
- November 2024: IDI Composites International has unveiled its new global headquarters and state-of-the-art manufacturing facility in Noblesville, Indiana. Spanning 120,000 square feet, the facility is home to IDI's corporate offices, as well as manufacturing units for sheet molding compound (SMC) and bulk molding compound (BMC).
- December 2023: In a bid to cater to the surging demand in the transportation and electrical and electronics sectors, National Manufacturing Group has forged a strategic alliance with Laval, a worldwide frontrunner in composite materials. This collaboration is set to bolster the production and distribution of both sheet molding and bulk molding compounds.
Global Sheet Molding And Bulk Molding Compounds Market Report Scope
The global sheet molding & bulk molding compounds market report includes:
By Resin Type | Polyester | ||
Epoxy | |||
By Fiber Type | Glass Fiber | ||
Carbon Fiber | |||
By Manufacturing Process | Compression Molding | ||
Injection / Transfer Molding | |||
Resin Transfer Molding (RTM) | |||
Pultrusion | |||
By End-user Industry | Automotive and Transportation | ||
Electrical and Electronics | |||
Building and Construction | |||
Aerospace | |||
Domestic Appliances | |||
Other End-user Industries (Energy, etc.) | |||
By Geography | Asia-Pacific | China | |
Japan | |||
India | |||
South Korea | |||
ASEAN Countries | |||
Rest of Asia-Pacific | |||
North America | United States | ||
Canada | |||
Mexico | |||
Europe | Germany | ||
United Kingdom | |||
France | |||
Italy | |||
Spain | |||
Russia | |||
NORDIC Countries | |||
Rest of Europe | |||
South America | Brazil | ||
Argentina | |||
Rest of South America | |||
Middle-East and Africa | Saudi Arabia | ||
South Africa | |||
Rest of Middle-East and Africa |
Polyester |
Epoxy |
Glass Fiber |
Carbon Fiber |
Compression Molding |
Injection / Transfer Molding |
Resin Transfer Molding (RTM) |
Pultrusion |
Automotive and Transportation |
Electrical and Electronics |
Building and Construction |
Aerospace |
Domestic Appliances |
Other End-user Industries (Energy, etc.) |
Asia-Pacific | China |
Japan | |
India | |
South Korea | |
ASEAN Countries | |
Rest of Asia-Pacific | |
North America | United States |
Canada | |
Mexico | |
Europe | Germany |
United Kingdom | |
France | |
Italy | |
Spain | |
Russia | |
NORDIC Countries | |
Rest of Europe | |
South America | Brazil |
Argentina | |
Rest of South America | |
Middle-East and Africa | Saudi Arabia |
South Africa | |
Rest of Middle-East and Africa |
Key Questions Answered in the Report
What is the current Sheet Molding & Bulk Molding Compounds Market size?
The sheet molding and bulk molding compounds market size is USD 4.03 billion in 2025.
Which segment is growing fastest?
Epoxy-based sheet molding compounds record the highest 6.92% CAGR through 2030 on rising demand for low-emission, high-strength materials.
Why is Asia-Pacific the leading region?
Concentrated automotive and electronics manufacturing hubs, robust supply chains, and government support for composite technology give Asia-Pacific 48.54% market share.
How are electric vehicles influencing material choice?
Electric vehicle OEMs seek weight reduction and part consolidation, prompting wider adoption of lightweight sheet molding compounds for battery enclosures and exterior closures.
What limits broader use of thermoset SMC in battery packs?
Regulatory preference for recyclable materials and the rising competitiveness of injection-molded thermoplastic composites restrain thermoset uptake in certain battery enclosure applications.
Page last updated on: July 15, 2025