Factory Automation And Industrial Controls Market Analysis by Mordor Intelligence
The factory automation and industrial controls market size reached USD 311.90 billion in 2025 and is forecast to advance to USD 485.80 billion by 2030, translating into a 9.30% CAGR. Momentum builds as manufacturers confront talent shortages, stringent energy-efficiency rules, and the imperative to shorten supply chains. Rising labor costs encourage companies to install intelligent robotics and vision-enabled inspection cells, while energy-oriented directives in North America and the EU reward investments in high-efficiency drives and smart metering. Digital twins, edge analytics, and cloud-connected controllers form the core of next-generation factories, creating new revenue pools for service providers that overlay condition-based maintenance atop existing hardware stacks. Meanwhile, tariff-driven redesigns of semiconductor sourcing are accelerating regional production footprints, further lifting the factory automation and industrial controls market trajectory. Platform vendors that blend operational-technology expertise with secure software ecosystems continue to gain pricing power, supported by government funding such as the USD 53 billion CHIPS Act that underwrites capital outlays for domestic fabs.[1] Cybersecurity and Infrastructure Security Agency, “Primary Mitigations to Reduce Cyber Threats to OT and ICS,” cisa.gov
Key Report Takeaways
- By product, industrial control systems held 58% of the factory automation and industrial controls market share in 2024, whereas field devices are expanding at a 9.8% CAGR through 2030.
- By component, hardware accounted for 62.5% of the factory automation and industrial controls market size in 2024; services post the quickest rise at 11.2% CAGR.
- By end-user industry, automotive retained 27% revenue share in 2024, while pharmaceuticals grow fastest at 12.4% CAGR to 2030.
- By geography, Asia led with 39.4% revenue share in 2024; South America is projected to climb at a 10.1% CAGR during the outlook period.
Global Factory Automation And Industrial Controls Market Trends and Insights
Drivers Impact Analysis
Driver | (~) % Impact on CAGR Forecast | Geographic Relevance | Impact Timeline |
---|---|---|---|
Industry 4.0 adoption acceleration | +2.1% | Global with APAC leadership | Medium term (2-4 years) |
Energy-efficiency mandates and cost pressure | 1.80% | North America and EU, spreading to APAC | Long term (≥ 4 years) |
Rising labor shortages in manufacturing | +2.3% | Global, strongest in developed economies | Short term (≤ 2 years |
Low-code / no-code automation platforms | +0.9% | North America and EU first movers | Medium term (2-4 years) |
Source: Mordor Intelligence
Industry 4.0 Adoption Acceleration
Roughly 80% of global producers intend to embed Industry 4.0 solutions by 2025, yet only 10% have achieved end-to-end digitization. National programs—such as the UK’s Made Smarter grants and China’s network of 33 Manufacturing Innovation Centers—offer capital and technical guidance, pushing the factory automation and industrial controls market toward advanced analytics and autonomous optimisation. Singapore’s Smart Industry Readiness Index likewise helps mid-sized firms benchmark progress, ensuring that automated mobile robots and cloud scheduling tools deliver measurable cost relief. Convergence of AI, IoT sensors, and big-data engines yields real-time insights that cut scrap, tune energy loads, and shorten maintenance interventions. Vendors differentiate by wrapping cybersecurity and remote-support layers around these data flows, turning routine controller sales into multi-year service annuities.
Energy-Efficiency Mandates & Cost Pressure
Governments invested more than USD 1 trillion in efficiency programs and now expect industry to shoulder a sizeable share of the global CO₂-reduction target. Factories respond by installing variable-speed drives, smart compressors, and AI-enabled scheduling platforms that shift production to off-peak renewable availability. The United Nations Economic Commission for Europe promotes industrial energy-efficiency best practices, underscoring the link between digital controls and decarbonisation. In the factory automation and industrial controls market, vendors now pre-package carbon dashboards with programmable logic controllers, turning compliance into a value-added service. As utilities raise time-of-use tariffs, fast-payback projects such as intelligent lighting and heat-recovery systems climb the corporate capital list.
Rising Labor Shortages in Manufacturing
Retirements and declining participation leave the global shop-floor workforce short by more than 2 million positions through 2030. Enterprises escalate automation rollouts, noting that 54% of investment plans target repetitive tasks, while 75% of executives highlight a growing need for data-centric roles to manage new technologies . In Japan, demographic headwinds spur autonomous vehicles and AI-guided construction equipment that later migrate to global manufacturing lines . Cost-benefit analyses show 20-30% labor-cost savings when robotics team with human operators, encouraging small plants to deploy collaborative arms and automated guided vehicles.
Low-Code / No-Code Automation Platforms
Low-code toolkits let process engineers configure dashboards and exception-handling logic without deep coding skills, compressing deployment lead-times and easing maintenance backlogs. Modern MES suites embed graphical workflow builders that sit on secure, standards-based data layers, limiting the risk of ungoverned shadow applications. Citizen-developer programs multiply subtle optimisation projects—ranging from automated changeover sequences to customised quality alerts—expanding the addressable base of the factory automation and industrial controls market.
Restraints Impact Analysis
Restraint | (~) % Impact on CAGR Forecast | Geographic Relevance | Impact Timeline |
---|---|---|---|
High upfront CAPEX of automation projects | -1.4% | Global, toughest for SMEs | Short term (≤ 2 years) |
Cyber-security vulnerabilities in OT networks | -1.1% | Global, critical infrastructure | Medium term (2-4 years) |
Source: Mordor Intelligence
High Upfront CAPEX of Automation Projects
Comprehensive automation programs often exceed traditional budgeting cycles, especially for small and mid-sized enterprises. Sector M&A multiples reached 18 times EBITDA in 2024, raising vendor pricing expectations and extending break-even horizons. Universal baseline import tariffs of 10%, plus a 50% duty on Chinese semiconductors, elevate component costs and complicate ROI math for capital programmes. While public grants under the CHIPS Act defray some expenses, managers still contend with training outlays and integration risks that may disrupt production during cut-overs.
Cyber-Security Vulnerabilities in OT Networks
Ransomware volumes rose 46% year-on-year, with industrial control systems a favourite entry point.[3] Critical infrastructure now sustains 13 attacks per second, a statistic that forces plant operators to review network topologies and segmentation policies. CISA urges disconnection of nonessential OT assets from public networks, credential hardening, and strict patch schedules. Guidance notwithstanding, legacy equipment and vendor heterogeneity slow remediation efforts, making managed-security-as-a-service a high-growth pocket within the factory automation and industrial controls market.
Segment Analysis
By Product: Control Systems Lead, Field Devices Accelerate
Industrial control systems secured 58% of the factory automation and industrial controls market in 2024, underscoring their role as the operational backbone for continuous and discrete manufacturing. Distributed control systems, SCADA, and modern PLCs integrate AI-powered diagnostics that pre-empt downtime events and synchronise with enterprise resource planning for just-in-time sequencing. Demand intensifies in semiconductor fabrication and battery cell assembly, areas that rely on microsecond-level loop execution to achieve defect-free throughput. At the same time, the factory automation and industrial controls market size attributed to field devices is on track to expand at 9.8% CAGR to 2030, propelled by advances in smart cameras and collaborative robotics that embed self-learning algorithms close to the production line.
Machine-vision platforms move beyond simple presence checks toward 3D measurement of complex contours, enabling in-line correction rather than post-process rework. Industrial robots, once fenced, now share workspace with humans, guided by safe-motion firmware and proximity sensors. These capabilities lower integration barriers and open fresh opportunities in industries with shorter product cycles. Sensor manufacturers push higher-resolution, lower-power designs that feed real-time vibration, acoustic, and thermal signatures back to the control layer, reinforcing predictive-maintenance models that stretch asset life and limit unplanned outages.
By Component: Hardware Dominance, Services Surge
Hardware generated 62.5% of the factory automation and industrial controls market size in 2024 as companies refreshed aging controllers and servo drives to handle faster cycle times and tighter tolerances. Nevertheless, service revenues are climbing 11.2% per year, reflecting management’s preference for outcome-based contracts that de-risk technology adoption. Multi-year agreements often bundle installation, integration, and analytics support into usage-based pricing frameworks that align vendor incentives with plant performance.
Predictive-maintenance subscriptions aggregate vibration and temperature trends, benchmarking equipment fleets against anonymised peer datasets to spotlight outliers well before catastrophic failure. System-integration houses monetise protocol converters and edge gateways that join legacy Modbus devices to cloud dashboards running on secure OPC UA links. As the installed base of intelligent sensors swells, training and change-management engagements rise in parallel, completing the shift from one-time capital transactions to annuity-style service flows within the factory automation and industrial controls market.
By End-User Industry: Automotive Leads, Pharmaceutical Accelerates
Automotive lines represented 27% of factory automation and industrial controls market share in 2024, anchored by the electrification cycle that demands high-precision laser welding, battery cell stacking, and automated end-of-line testing. Flexible manufacturing cells accommodate frequent model launches and retrieval of historical energy-consumption data needed for scope-3 emissions reporting. Pharmaceutical operations, meanwhile, register the fastest growth at 12.4% CAGR through 2030 as regulators push for real-time release testing and smaller batch runs tailored to personalised therapies. Projects such as Merck’s USD 300 million FLEx Center showcase modular pods controlled by cloud-based MES that shorten validation timelines and support rapid molecule changeovers.
Food and beverage producers tighten traceability from raw-material intake to palletising, deploying vision-guided robotics and automated labelling to satisfy shelf-life accuracy rules. Chemical complexes automate compressor islands and safety-instrumented systems to comply with emissions caps, while electronics manufacturers rely on sub-micron motion control for wafer etching and camera optical-alignment stations.
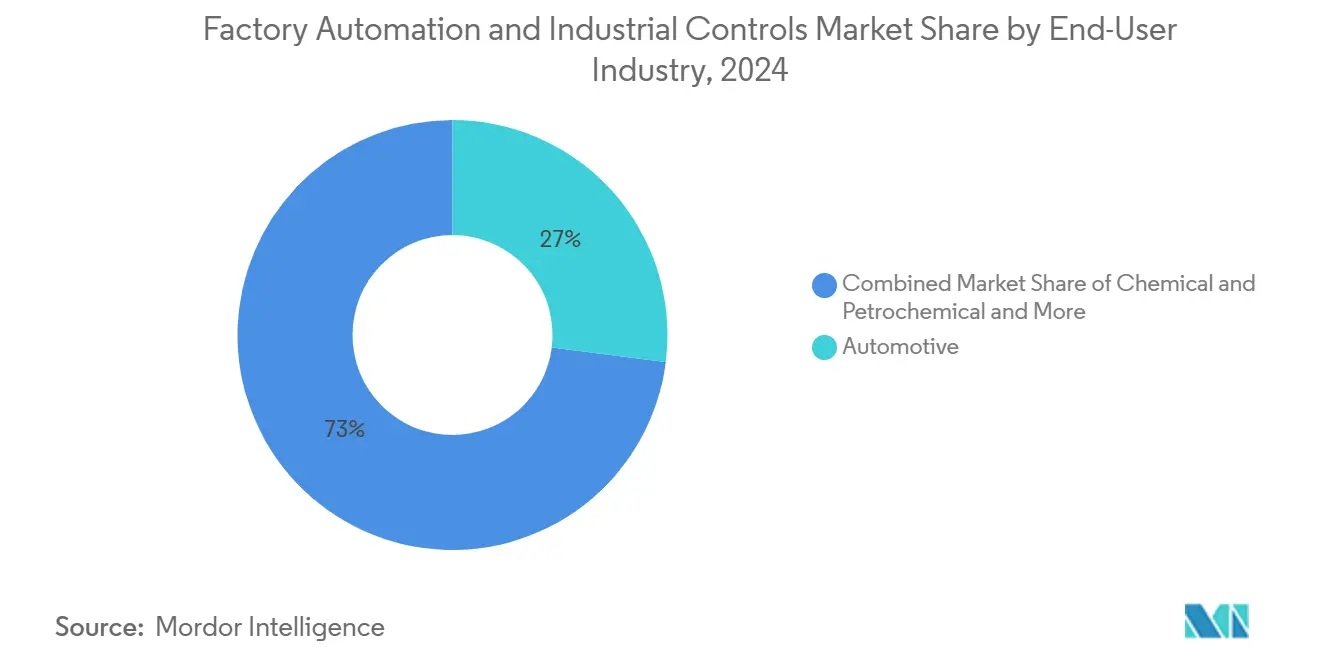
Note: Segment shares of all individual segments available upon report purchase
By Control System Architecture: Proprietary Systems Dominate, Open Standards Gain
Proprietary architectures still account for 71% of installations as of 2024 because single-vendor stacks deliver end-to-end performance guarantees and simplified support. Yet open architectures are expanding at 13% CAGR, encouraged by vendor-neutral OPC UA and Time-Sensitive Networking profiles that promise deterministic, cyber-secure traffic over standard Ethernet. Hybrid deployments permit brownfield sites to bolt interoperable gateways onto existing assets, giving managers a phased path toward full openness. Market interest in open solutions rises when multi-site enterprises negotiate groupwide service contracts and seek to avoid price escalation tied to vendor lock-in.
Standardisation bodies across Europe advocate semantic models and unified ontologies so that machines can publish contextualised data without bespoke middleware. The long-term prize is a resilient supply network where software updates propagate seamlessly and cyber patches apply across diverse equipment, lowering total cost of ownership for the factory automation and industrial controls market.
Geography Analysis
Asia captured 39.4% of 2024 revenue thanks to dense manufacturing ecosystems, skilled labour pools, and assertive digital-policy frameworks. China’s 2025-era initiatives finance demonstration lines that combine AI scheduling with 5G-enabled motion control, while Japanese conglomerates deploy autonomous haulage and precision welding robots to offset chronic labour gaps.[2] Mitsui & Co. Global Strategic Studies Institute, “Targeting a Paradigm Shift Through New Technologies,” mitsui.com South Korea’s chip fabrication complexes and India’s smart-meter roll-outs further extend hardware demand, reinforcing Asia’s central role in the factory automation and industrial controls market.
North American manufacturers accelerate investments as supply-chain sovereignty climbs the federal agenda. The CHIPS Act’s USD 53 billion allotment stimulates local sensor and controller production, creating knock-on demand for secure edge-computing appliances. Universal tariffs introduced in April 2025 reinforce near-shoring, encouraging automation in small and mid-tier plants that previously relied on offshore component sourcing.
Europe focuses on sustainability and cyber-resilience. While the EUR 150 billion allocation for digital transition under the Recovery and Resilience Facility (USD 163 billion) aims to modernise industrial bases, execution gaps prompt many firms to leverage private-sector integrators to meet reporting deadlines eca. Compliance pressures with energy codes and supply-chain traceability hold particular sway in food, chemicals, and consumer goods plants.
South America, though starting from a smaller installed base, is projected to expand at a 10.1% CAGR through 2030. Brazil’s “New Industry Brazil” program earmarks R$ 300 billion (USD 61 billion) for R&D incentives, equipment credits, and tax benefits, making automation upgrades financially attractive. Argentina’s digital-factory roadmap encourages IoT pilots in agricultural machinery and food processing despite skills shortages. As cross-border technology transfer grows, regional system integrators partner with global OEMs to deliver turnkey lines suited to smaller batch volumes and variable-quality power supplies common in the region.
The Middle East and Africa join the factory automation and industrial controls market as policy makers diversify away from resource-heavy sectors. Green-field industrial zones embed predictive-maintenance platforms from inception, allowing them to leapfrog legacy architectures and focus on data-driven operations keyed to export-market compliance.
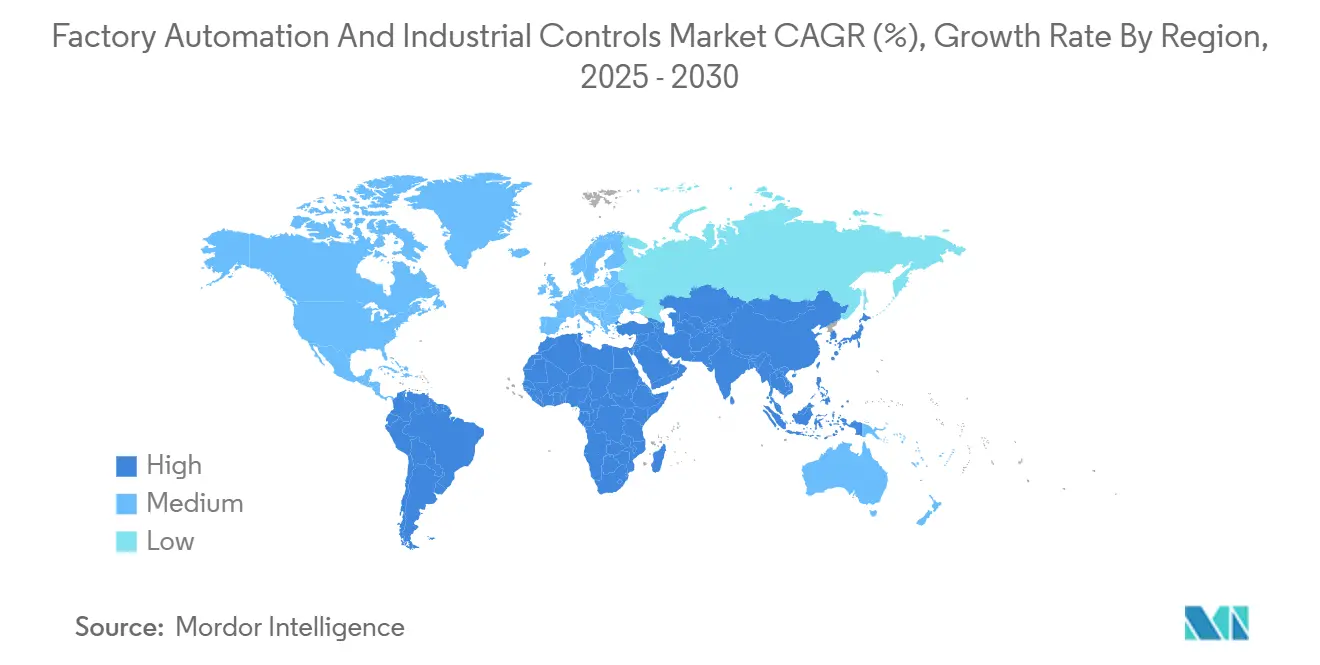
Competitive Landscape
The market shows moderate concentration, with large incumbents restructuring to sharpen strategic focus. Honeywell will split into three independent entities by 2026, enabling targeted investment in high-growth verticals such as digital industrial automation. Siemens enhanced its simulation and high-performance computing capabilities by acquiring Altair Engineering for USD 10.6 billion, a move that deepens its end-to-end digital-thread proposition. Emerson fully absorbed Aspen Technology, integrating advanced process-optimisation software into its hardware-rich portfolio to sell performance-guaranteed solutions.
Cyber-security is now a core buying criterion. Nozomi Networks, buoyed by USD 100 million Series E funding from OEM investors, positions its threat-intelligence platform as an OEM-agnostic overlay for heterogeneous plants nozomi. ABB answered with GMD Copilot, an AI assistant that mines real-time control-loop data to propose productivity tweaks. Private-equity inflows, reaching USD 14.87 billion in 2024, fuel consolidation of niche sensor and software firms, chasing scale synergies and cross-selling to installed bases.
Pricing power tilts toward vendors that deliver integrated offerings combining hardware, analytics, and managed security. Yet open-architecture momentum eases market entry for specialists that solve specific pain points, such as time-sensitive networking switches or low-code MES plug-ins. As interoperability progresses, switching costs decline—pressuring incumbents to innovate faster and move up the value chain via services.
Factory Automation And Industrial Controls Industry Leaders
-
ABB Limited
-
Schneider Electric SE
-
Rockwell Automation, Inc.
-
Mitsubishi Electric Corp.
-
Siemens AG
- *Disclaimer: Major Players sorted in no particular order
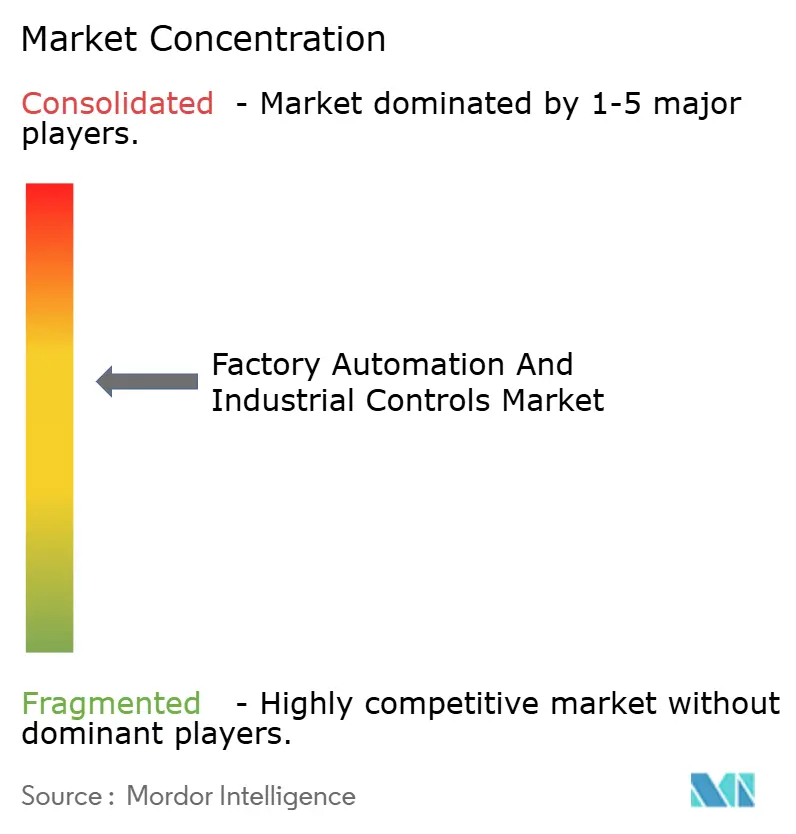
Recent Industry Developments
- January 2025: Merck commenced construction of a USD 300 million modular pharmaceutical facility in Rahway, New Jersey, embedding cloud-driven MES and flexible clean-room pods to accelerate personalised-medicine production
- January 2025: Delta Electronics enabled Phoenix Silicon International to operate the world’s first fully automated 8-inch wafer fab by integrating a DIAMES manufacturing-execution system, boosting annual capacity to 630,000 wafers
- November 2024: Rockwell Automation posted USD 8.26 billion in fiscal-year sales, a 9% decline, yet retained a USD 3.09 billion backlog that underpins service revenue visibility
- October 2024: Siemens completed the USD 10.6 billion acquisition of Altair Engineering, fortifying its digital-simulation and high-performance computing stack for industrial client
Global Factory Automation And Industrial Controls Market Report Scope
Factory automation and industrial control is a rising trend in the manufacturing industry, which provides smart manufacturing infrastructure. Industrial control and factory automation facilitate cost efficiency, quality of production and standardize manufacturing, reliability, and flexibility in the process of manufacturing. Industrial control and factory automation offer a perfect mix of mechanical components and devices for the information technology market.
The factory automation and industrial controls market is segmented by product (industrial control systems(distributed control system (DCS), programmable logic controller (PLC), supervisory control and data acquisition (SCADA), product lifecycle management (PLM), human machine interface (HMI), manufacturing execution system (MES), enterprise resource planning (ERP), other industrial control systems), field devices (machine vision system, robotics (industrial), sensors and transmitters, motors and drivers, other field devices)), end user industry (automotive, chemical and petrochemical, utility, pharmaceutical, food and beverage, oil and gas, other end-user industries) and geography (North America(United States, Canada), Europe (United Kingdom, Germany, France, Rest of Europe), Asia-Pacific (China, India, Japan, Rest of Asia-Pacific), Latin America, Middle East & Africa). The report offers market forecasts and size in value (USD) for all the above segments.
By Product | Industrial Control Systems | Distributed Control System (DCS) | |
Programmable Logic Controller (PLC) | |||
Supervisory Control & Data Acquisition (SCADA) | |||
Product Lifecycle Management (PLM) | |||
Human-Machine Interface (HMI) | |||
Manufacturing Execution System (MES) | |||
Enterprise Resource Planning (ERP) | |||
Other Industrial Control Systems | |||
Field Devices | Machine Vision Systems | ||
Industrial Robotics | |||
Sensors and Transmitters | |||
Motors and Drives | |||
Other Field Devices | |||
By Component | Hardware | ||
Software | |||
Services | |||
By End-User Industry | Automotive | ||
Chemical and Petrochemical | |||
Utility | |||
Pharmaceutical | |||
Food and Beverage | |||
Oil and Gas | |||
Electronics and Semiconductor | |||
Aerospace and Defense | |||
Other Industries | |||
By Control System Architecture | Proprietary / Vendor-Specific | ||
Open / Interoperable | |||
Hybrid Architecture | |||
By Geography | North America | United States | |
Canada | |||
Mexico | |||
South America | Brazil | ||
Argentina | |||
Rest of South America | |||
Europe | United Kingdom | ||
Germany | |||
France | |||
Italy | |||
Russia | |||
Rest of Europe | |||
APAC | China | ||
India | |||
Japan | |||
South Korea | |||
Australia and New Zealand | |||
Rest of APAC | |||
Middle East | UAE | ||
Saudi Arabia | |||
Turkey | |||
Rest of Middle East | |||
Africa | South Africa | ||
Nigeria | |||
Egypt | |||
Rest of Africa |
Industrial Control Systems | Distributed Control System (DCS) |
Programmable Logic Controller (PLC) | |
Supervisory Control & Data Acquisition (SCADA) | |
Product Lifecycle Management (PLM) | |
Human-Machine Interface (HMI) | |
Manufacturing Execution System (MES) | |
Enterprise Resource Planning (ERP) | |
Other Industrial Control Systems | |
Field Devices | Machine Vision Systems |
Industrial Robotics | |
Sensors and Transmitters | |
Motors and Drives | |
Other Field Devices |
Hardware |
Software |
Services |
Automotive |
Chemical and Petrochemical |
Utility |
Pharmaceutical |
Food and Beverage |
Oil and Gas |
Electronics and Semiconductor |
Aerospace and Defense |
Other Industries |
Proprietary / Vendor-Specific |
Open / Interoperable |
Hybrid Architecture |
North America | United States |
Canada | |
Mexico | |
South America | Brazil |
Argentina | |
Rest of South America | |
Europe | United Kingdom |
Germany | |
France | |
Italy | |
Russia | |
Rest of Europe | |
APAC | China |
India | |
Japan | |
South Korea | |
Australia and New Zealand | |
Rest of APAC | |
Middle East | UAE |
Saudi Arabia | |
Turkey | |
Rest of Middle East | |
Africa | South Africa |
Nigeria | |
Egypt | |
Rest of Africa |
Key Questions Answered in the Report
What is the current size of the factory automation and industrial controls market?
The market stands at USD 311.9 billion in 2025 and is projected to reach USD 485.8 billion by 2030.
Which region leads the factory automation and industrial controls market?
Asia accounts for 39.4% of 2024 revenue, reflecting its dense manufacturing base and government-backed digitisation programs.
Which segment is growing fastest within the factory automation and industrial controls market?
Services expand at an 11.2% CAGR through 2030, driven by demand for predictive-maintenance, integration, and managed-security contracts.
How are labor shortages influencing automation investment?
Anticipated workforce gaps of over 2 million roles by 2030 push manufacturers to automate repetitive tasks and introduce collaborative robots, resulting in 20-30% labor-cost savings.
Page last updated on: June 20, 2025