Extruded Polypropylene (XPP) Foam Market Size and Share
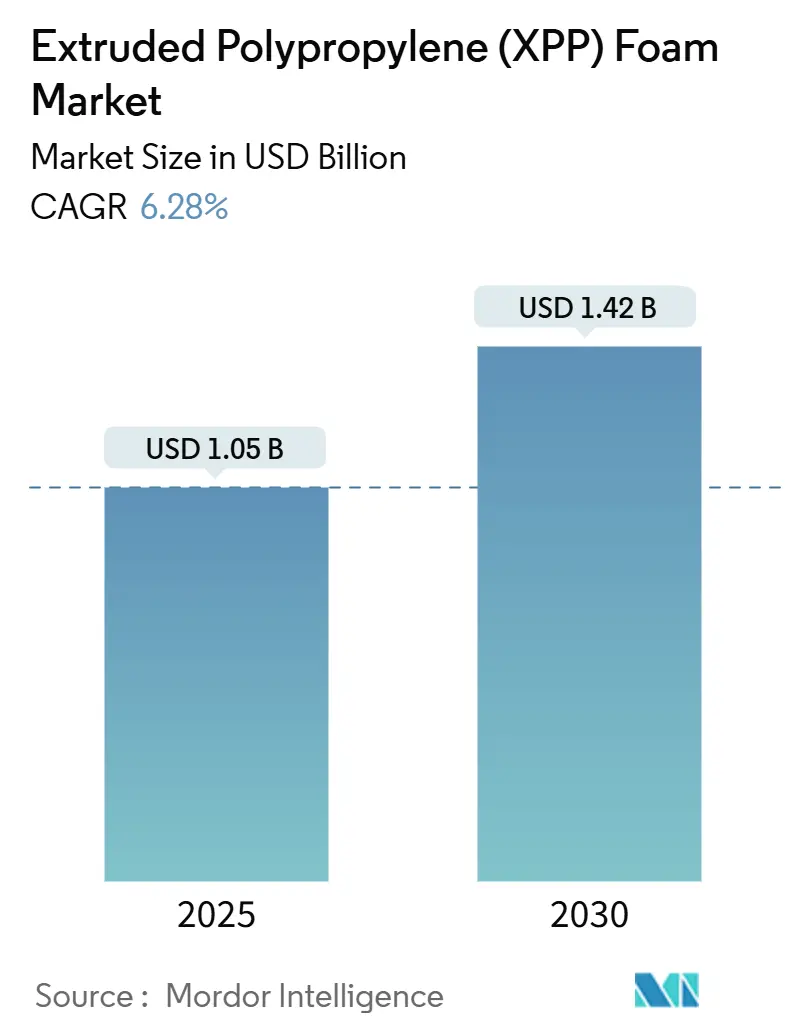
Extruded Polypropylene (XPP) Foam Market Analysis by Mordor Intelligence
The extruded polypropylene foam market is valued at USD 1.05 billion in 2025 and is forecast to reach USD 1.42 billion by 2030, advancing at a 6.28% CAGR. The steady climb mirrors rising material substitution in automotive, packaging, and construction, where low density, high impact strength, and heat resistance deliver measurable performance and sustainability benefits. Lightweighting mandates in vehicles, recyclable-content targets in packaging, and stricter building‐energy codes continue to expand the customer base. Supply-side momentum is reinforced by bio-circular polypropylene investments that lower carbon footprints and align with recycling rules, while recent breakthroughs in supercritical foaming add design flexibility. At the same time, volatile propylene costs and tight extrusion capacity constrain immediate scaling, giving established producers pricing power. Overall, the extruded polypropylene foam market is positioned for durable growth through the end of the decade.
Key Report Takeaways
- By type, low-density grades led with 51.19% of the extruded polypropylene foam market share in 2024, whereas high-density variants are set to grow at 7.98% CAGR to 2030.
- By end-user industry, automotive captured 52.95% revenue share of the extruded polypropylene foam market size in 2024 and is expanding at 7.26% CAGR to 2030.
- By geography, Asia-Pacific held 54.61% of 2024 revenues in the extruded polypropylene foam market, and is set to grow at the fastest CAGR of 7.45% through 2030.
Global Extruded Polypropylene (XPP) Foam Market Trends and Insights
Driver Impact Analysis
Driver | (~) % Impact on CAGR Forecast | Geographic Relevance | Impact Timeline |
---|---|---|---|
Superior properties & high recyclability | +1.8% | Global | Long term (≥ 4 years) |
Automotive lightweighting mandates | +2.1% | North America & EU, APAC core | Medium term (2-4 years) |
Growing demand from packaging industry | +1.5% | Global, with early gains in Asia-Pacific | Short term (≤ 2 years) |
Increasing demand for recyclable and sustainable foams | +1.3% | EU & North America, spill-over to APAC | Long term (≥ 4 years) |
Drone & UAV protective packaging boom | +0.7% | North America & EU | Medium term (2-4 years) |
Source: Mordor Intelligence
Superior Properties & High Recyclability
XPP foam delivers a closed-cell matrix that absorbs energy, dampens noise, and insulates heat better than many incumbent polymers. It maintains dimensional integrity up to 130 °C, vital for vehicle under-hood and cabin components that experience temperature spikes. Because it is thermoplastic, the material can be shredded, re-pelletized, and extruded again without cross-linking degradation, satisfying circular-economy procurement policies. Its resistance to moisture, solvents, and ultraviolet radiation lengthens product life and lowers total cost. Global recycled-polypropylene usage continues to rise, giving converters a growing pool of feedstock that reinforces the extruded polypropylene foam market value proposition.
Automotive Lightweighting Mandates
Corporate Average Fuel Economy rules in the United States, the European Union’s CO₂ fleet targets, and China’s dual-credit system collectively pressure automakers to shed vehicle mass. Replacing heavy plastics or metal inserts with XPP foam in bumper cores, door panels, and battery enclosures cuts part weight by about 25% while keeping crash energy absorption intact. Chemical foaming enables thin-wall sections with fine cell morphology that meet strict dimensional tolerances. Automakers are now specifying recycled-content XPP grades, as demonstrated by interior-trim supplier Grupo Antolin’s 20% weight-reduction program using foamed recyclate[1]SAE International Staff, “Lightweighting Strategies for Electric Vehicles,” SAE International, sae.org.
Growing Demand from Packaging Industry
E-commerce growth and cold-chain logistics require protective packaging that resists compression set and insulates perishable goods. XPP foam meets these needs while complying with emerging bans on expanded polystyrene in food service. Bio-circular grades such as Braskem’s WENEW, derived from used cooking oil, match virgin performance and satisfy brand commitments to carbon neutrality. Adoption is spreading fastest in Asia-Pacific, where consumer-goods volumes are high and national plastic-waste regulations are tightening.
Increasing Demand for Recyclable and Sustainable Foams
The European Packaging and Packaging Waste Regulation mandates that all packaging be recyclable by 2030 and introduces graduated recycled-content quotas, accelerating interest in mono-material solutions. Brand owners in North America and Europe have raised post-consumer resin usage targets, lifting demand for mechanically recyclable foams. Producers with in-house reprocessing loops capture off-cuts and post-industrial scrap, increasing material yield and lowering carbon intensity.
Restraint Impact Analysis
Restraint | (~) % Impact on CAGR Forecast | Geographic Relevance | Impact Timeline |
---|---|---|---|
High price of extruded polypropylene | -0.70% | Global | Short term (≤ 2 years) |
Volatile propylene feedstock costs | -0.50% | Global, with acute impact in Asia-Pacific | Short term (≤ 2 years) |
Limited large-scale extrusion capacity in several regions | -0.80% | MEA, South America, parts of APAC | Medium term (2-4 years) |
Source: Mordor Intelligence
High Price of Extruded Polypropylene & Volatile Propylene Feedstock Costs
Spot propylene climbed to USD 825-835/mt FOB Korea in early 2025 after refinery outages tightened supply[2]Polymerupdate Editorial Team, “Asia Daily Petrochemical Report,” Polymerupdate, polymerupdate.com. North American polypropylene contracts followed, jumping 9% in Q1 2025 as producers declared force majeure. These price swings compress converter margins and delay capacity investments, especially for smaller firms that cannot hedge raw-material risk through long-term contracts. High resin costs ripple through the extruded polypropylene foam market, raising finished-product prices and prompting short-term customer substitution toward lower-priced foams when performance demands allow.
Limited Large-Scale Extrusion Capacity in Several Regions
Few plants operate the tandem-extrusion lines needed for stable high-throughput XPP production outside East Asia, Europe, and the United States. Importing foam billets raises freight costs and carbon footprints, countering corporate sustainability goals. Capital expenditure for a modern 15 ktpa line exceeds USD 35 million, a deterrent in demand-emerging regions like Southeast Asia and the Middle East. Equipment, process know-how, and maintenance support remain concentrated among a handful of suppliers, extending lead times for new entrants[3]American Foam Products Staff, “Dramatic Rise of Material Costs for Foam Fabricators,” American Foam Products, americanfoamproducts.com.
Segment Analysis
By Type: High-Density Variants Drive Innovation
High-density grades represent the fastest-advancing slice of the extruded polypropylene foam market, posting a 7.98% CAGR through 2030 as designers pursue higher compressive strength and dimensional rigidity. In 2024, Low-density foam remained the leader, holding 48.19% of the extruded polypropylene foam market share, thanks to packaging and interior auto uses where weight savings trump structural loads.
Process engineers now tailor density within a single sheet by modulating nucleating agents across the melt profile, achieving multi-zone parts that blend cushioning and stiffness. Supercritical CO₂ foaming narrows cell-size distribution and lifts mechanical integrity, a breakthrough for panels subject to concentrated loads. Nanofiller research, including graphene platelet additions, demonstrates up to 30% modulus uplift at filler loadings below 1 wt% %, broadening the suitability of XPP in construction thermal-break assemblies. Architects specify high-density XPP over mineral wool as building-envelope codes tighten due to comparable R-values at half the mass.
Low-density foam still powers in-line returnable packaging, foldable dunnage, and HVAC ducts. New clarifier masterbatches raise heat-distortion temperatures by 8 °C, extending service life in under-hood airflow components where continuous temperatures reach 110 °C. Market leaders are combining post-industrial scrap with virgin resin for low-density sheets, keeping physical properties unchanged while lowering resin costs and greenhouse-gas intensity.
Materials technologists expect the extruded polypropylene foam market to shift toward hybrid density solutions that exploit the best attributes of each grade. High-density cores paired with low-density skins inside one co-extruded laminate enable lightweight yet robust transport container walls. The new configurations are likely to capture share from solid polypropylene boards and aluminum honeycomb, especially in last-mile logistics enclosures seeking weight and cost reductions.
Note: Segment Share of all individual segments available upon report purchase
By End-User Industry: Automotive Sector Maintains Dual Leadership
Automotive designers anchor more than half of all sales, with the extruded polypropylene foam market size for automotive applications projected to grow at a 7.26% CAGR. Battery-electric vehicle programs drive the fastest gains, as every kilogram trimmed can extend range by 0.6 km on the WLTP cycle, a metric regulators and consumers value. XPP foam shields battery housings from road debris while acting as a thermal barrier that slows thermal runaway propagation. Interior trends toward minimalist cabins emphasize lightweight, soft-touch panels, where foamed polypropylene handily displaces talc-filled homopolymer sheets.
Construction absorbs the second-largest share, benefiting from XPP’s moisture resistance and ability to meet stringent fire-tester E84 Class A flame-spread scores with halogen-free additives. Improved compressive strength supports sandwich roof-panel designs in modular homes, slashing assembly time and on-site waste. Packaging’s contribution is scaling with online grocery volumes, and brand owners leverage foam’s closed-cell insulation to maintain chilled temperatures during 24-hour delivery windows.
Automotive contracts increasingly stipulate a minimum of 25% recycled content, encouraging foam producers to install degassing extruders that refine post-consumer polypropylene. This aligns with United States Inflation Reduction Act incentives that reward lower life-cycle emissions in vehicle supply chains. At the same time, in-vehicle acoustic performance is rising in priority as electric drivetrains remove engine noise, and XPP’s tunable cell geometry enables tailored sound-transmission loss curves. These cross-currents confirm that the extruded polypropylene foam industry will remain integral to next-generation mobility solutions while deepening its foothold in construction and logistics.
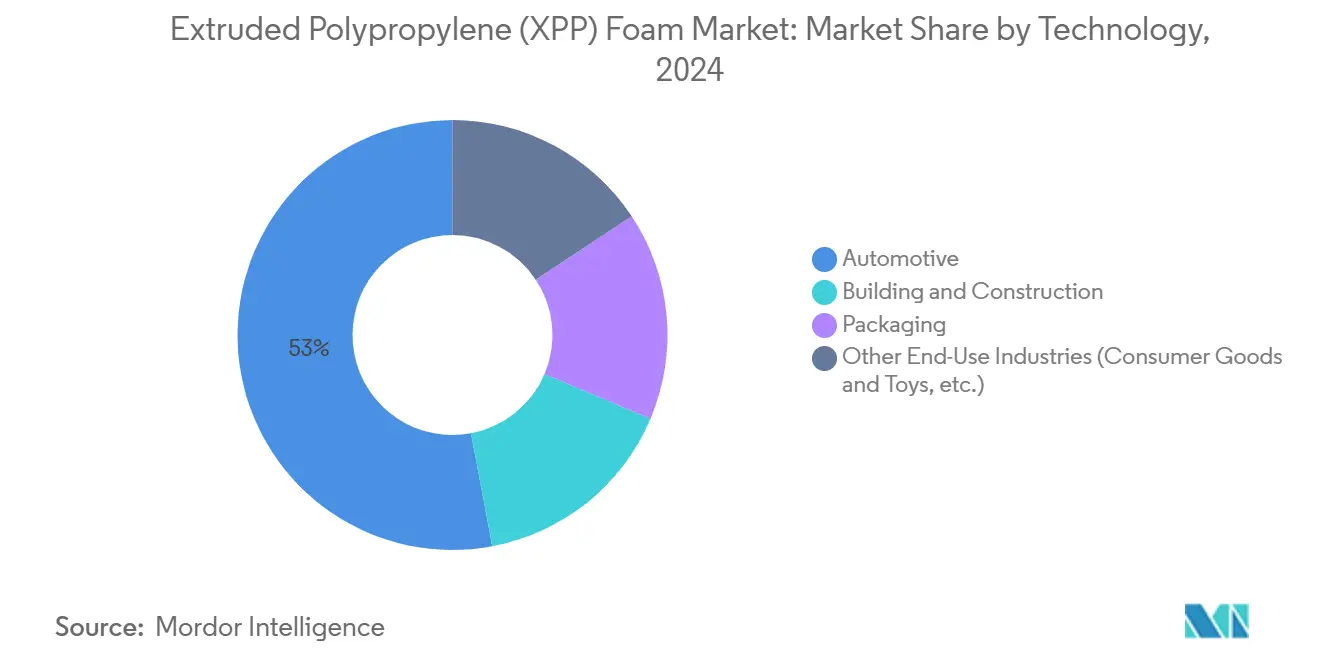
Note: Segment Share of all individual segments available upon report purchase
Geography Analysis
Asia-Pacific anchors the extruded polypropylene foam market with 54.61% of 2024 revenues, driven by China’s automotive exports, India’s surge in quick-service food delivery, and Japan’s early adoption of circular packaging. Regional consumption is projected to climb 7.45% CAGR through 2030 as OEMs localize electric-vehicle component production and e-commerce penetration spreads beyond tier-one cities. Government rebate programs for lightweight vehicles and restrictions on single-use plastics reinforce demand for recyclable foams. Producers enjoy shorter supply chains to regional propylene crackers, keeping cost inflation below global averages and supporting competitive pricing.
North America holds the second-largest slice, propelled by pickup and SUV platforms that require large energy-absorbing components. The United States Department of Energy’s Lightweight Materials Consortium continues to fund research into foamed polyolefin battery shields, keeping the region at the forefront of application engineering. Installations of bio-propane-to-propylene units in Texas bolster feedstock security and unlock low-carbon foam grades. However, the region still contends with propylene price volatility, which can slow downstream investment during supply disruptions.
Europe fosters high-value niches tied to stringent recyclability and carbon-footprint targets. Automakers in Germany and France deploy XPP in crash-pad structures that must pass pedestrian-safety tests while remaining fully recyclable. The region’s extruded polypropylene foam market share could rise three percentage points by 2030 if PPWR compliance accelerates conversion away from expanded polystyrene in retail food trays. European converters benefit from harmonized waste-collection schemes that secure clean post-consumer streams for closed-loop programs, but higher energy prices continue to pressure operating margins relative to Asia.
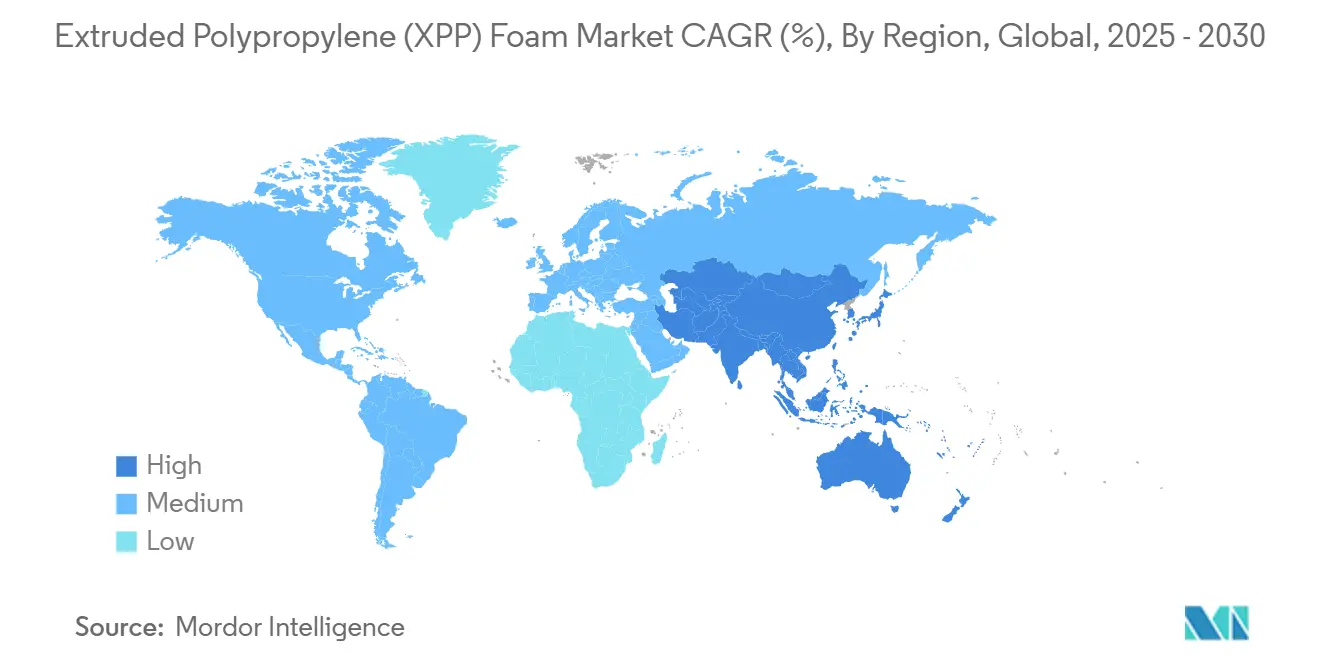
Competitive Landscape
The extruded polypropylene (XPP) foam market is moderately consolidated, with key players such as Borealis, Braskem, Pregis LLC, etc. focusing on technological advancements and capacity expansions. Borealis utilizes Borcell technology and captive propylene to produce foams with cell sizes under 100 µm, critical for automotive interior panels. Producers are also advancing graphene-enhanced foams for EV battery packs and low-VOC formulations to meet China’s GB/T 27630 air-quality standards, leveraging data analytics to optimize foam density for crash simulations and strengthen OEM collaborations.
Extruded Polypropylene (XPP) Foam Industry Leaders
-
Pregis LLC
-
BOREALIS GMBH
-
TORAY INDUSTRIES, INC.
-
Zotefoams plc
-
DS Smith
- *Disclaimer: Major Players sorted in no particular order
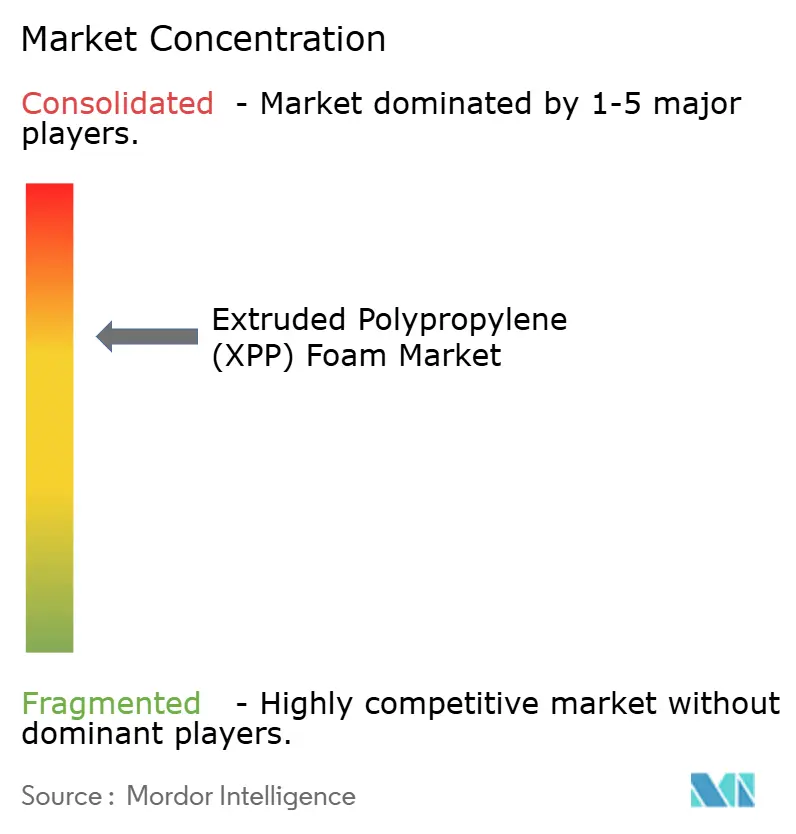
Recent Industry Developments
- March 2024: Polypropylene prices increased significantly across North America, with 4-5 cents per pound increases in early 2025 following production disruptions and tight supply conditions. These price movements reflect structural supply constraints affecting the entire XPP foam value chain.
- June 2023: The transportation industry is transitioning to extruded polypropylene (XPP) foam core, valued for its lightweight, high-performance, and recyclable properties in truck trailers and RVs. As a result, Czech-based Spur announced Hardex XPP closed-cell foam core to meet this demand. Targeting sandwich structures with fiber-reinforced composite skins, Hardex XPP addresses a market often overlooked by larger plastics firms.
Global Extruded Polypropylene (XPP) Foam Market Report Scope
The Extruded Polypropylene Foam market report include:
Type | Low-Density XPP Foam | ||
High-Density XPP Foam | |||
By End-User Industry | Automotive | ||
Building and Construction | |||
Packaging | |||
Other End-User Industries (Consumer Goods and Toys, etc.) | |||
By Geography | Asia-Pacific | China | |
Japan | |||
India | |||
South Korea | |||
ASEAN Countries | |||
Rest of Asia-Pacific | |||
North America | United States | ||
Canada | |||
Mexico | |||
Europe | Germany | ||
United Kingdom | |||
Italy | |||
France | |||
Rest of Europe | |||
South America | Brazil | ||
Argentina | |||
Rest of South America | |||
Middle East and Africa | Saudi Arabia | ||
South Africa | |||
Rest of Middle East and Africa |
Low-Density XPP Foam |
High-Density XPP Foam |
Automotive |
Building and Construction |
Packaging |
Other End-User Industries (Consumer Goods and Toys, etc.) |
Asia-Pacific | China |
Japan | |
India | |
South Korea | |
ASEAN Countries | |
Rest of Asia-Pacific | |
North America | United States |
Canada | |
Mexico | |
Europe | Germany |
United Kingdom | |
Italy | |
France | |
Rest of Europe | |
South America | Brazil |
Argentina | |
Rest of South America | |
Middle East and Africa | Saudi Arabia |
South Africa | |
Rest of Middle East and Africa |
Key Questions Answered in the Report
What is the current Extruded Polypropylene (XPP) Foam Market size?
The extruded polypropylene foam market is valued at USD 1.05 billion in 2025.
Which end-user sector contributes the most to sales?
Automotive applications command 52.95% of 2024 revenue and are growing at a 7.26% CAGR through 2030.
Which region leads the market and why?
Asia-Pacific holds 54.61% share in 2024 and advances at 7.45% CAGR thanks to strong vehicle output and rising packaged-goods demand.
Why are high-density XPP foams expanding faster than low-density grades?
High-density variants deliver greater compressive strength for structural parts and are projected to grow at a 7.98% CAGR to 2030.