Coated Fabric Market Size and Share
Coated Fabric Market Analysis by Mordor Intelligence
The Coated Fabric Market size is estimated at USD 24.67 billion in 2025, and is expected to reach USD 31.71 billion by 2030, at a CAGR of 5.15% during the forecast period (2025-2030). Growth is fueled by regulatory pressure for safer, lighter transportation materials, rising industrial-safety mandates, and the post-pandemic preference for hygienic, antimicrobial surfaces. Electric-vehicle platforms require lightweight, thermally efficient seat covers and air-bag fabrics, while hospitals and public spaces demand antiviral coatings that withstand repeated cleaning cycles. Supply shortages in specialty polymers and stricter per- and polyfluoroalkyl substances (PFAS) limits keep innovation in polyurethane (PU) and silicone systems brisk as producers seek compliant, high-performance alternatives. Meanwhile, Asia-Pacific’s manufacturing scale and smart-textile know-how reinforce its position as the leading production and consumption hub for premium coated substrates.
Key Report Takeaways
- By coating material, polymer-coated fabrics led with 80.67% of coated fabrics market share in 2024, and the polyurethane sub-segment is poised for a 6.93% CAGR to 2030.
- By fabric substrate, polyester accounted for 45.43% of the coated fabrics market share in 2024 and is set to grow fastest at a 7.24% CAGR through 2030.
- By application, automotive and transportation commanded 33.65% of the coated fabrics market size in 2024, while protective clothing is projected to expand at a 7.84% CAGR between 2025-2030.
- By geography, Asia-Pacific held 47.02% revenue in 2024; it is also the fastest-growing region with a 6.39% CAGR to 2030.
Global Coated Fabric Market Trends and Insights
Drivers Impact Analysis
Driver | (~) % Impact on CAGR Forecast | Geographic Relevance | Impact Timeline |
---|---|---|---|
Surge in automotive airbag and seat-cover volumes | +1.20% | Global, led by Asia-Pacific and North America | Medium term (2-4 years) |
Expansion of industrial protective-clothing mandates | +0.80% | Europe and North America, spreading to Asia-Pacific | Short term (≤ 2 years) |
Increasing demand for Antiviral and antimicrobial coatings for public-health resilience | +0.70% | Global, healthcare focus | Short term (≤ 2 years) |
Sensor-integrated e-textiles for smart interiors and wearables | +0.50% | North America & Europe early, Asia-Pacific production | Long term (≥ 4 years) |
Growing demand for coated fabrics from healthcare industry | +0.60% | Global, with developed markets leading adoption | Medium term (2-4 years) |
Source: Mordor Intelligence
Surge in Automotive Air-Bag and Seat-Cover Volumes
Automotive safety laws and electric-vehicle design targets are boosting demand for heat-stable, lightweight coated fabrics. Autoliv introduced an airbag fabric made from 100% recycled polyester in 2024, showing that stringent crash-safety requirements can coexist with circular-economy goals. Lear Corporation’s ComfortMax seat system, scheduled for 2025 launches, blends PU coatings with integrated heating to cut cabin-warm-up times and battery drain in electric cars. Covestro’s thermoplastic PU films enable flexible sunroof shades that house embedded electronics, illustrating the materials shift toward smart interiors[1]Covestro, “Flexible TPU Films for Smart Sunshades,” covestro.com . These breakthroughs push the coated fabrics market toward high-value, multifunctional constructions that tolerate abrasion, extreme temperatures, and complex forming.
Expansion of Industrial Protective-Clothing Mandates
Updated EU standards such as EN ISO 11612 require certified flame and heat protection, strengthening demand for advanced coatings over untreated fabrics. Sioen Industries extended its SYNQ multi-hazard workwear into the UK and Ireland in 2025 to address stricter employer liability rules. Silver-ion finishes can now achieve greater than 99% bacterial reduction after 50 laundering cycles, combining hygiene and safety in a single garment[2]MDPI, “Durability of Silver-Based Antimicrobial Finishes on Textiles,” mdpi.com . Manufacturers that secure multi-standard certifications convert regulation into durable revenue streams, particularly in chemicals, oil & gas, and utilities, where procurement cycles favor pre-approved vendors.
Increasing Demand for Antiviral and Antimicrobial Coatings for Public-Health Resilience
Hygiene concerns now extend coated textiles from hospitals to transit seating and hotel upholstery. Microban’s PFAS-free H₂O Shield range couples water repellency with broad-spectrum antimicrobial efficacy, answering consumer and regulatory calls for safer chemistries. Antimicrobial-coated fabrics also penetrate advanced wound-care dressings, where controlled release of silver ions delivers infection defence without compromising breathability. This public-health focus sustains premium pricing for coated fabrics that combine barrier performance, durability, and environmental compliance.
Sensor-Integrated E-Textiles for Smart Interiors and Wearables
Coated substrates are evolving into electronic assemblies. Saarland University engineered elastomer films with on-board haptic feedback that flex repeatedly without delamination—a leap for VR gloves and upholstery that responds to touch. Conductive yarns spun from carbon-nanotube bundles can be over-coated to stabilize the nano-network while retaining drape. Auto makers test seat-occupancy sensors built into coated fabric layers, while hospitals evaluate patient-monitoring bedding systems, signaling a new demand cycle that fuses textile, electronics, and polymer-coating supply chains.
Restraints Impact Analysis
Restraint | (~) % Impact on CAGR Forecast | Geographic Relevance | Impact Timeline |
---|---|---|---|
PVC raw-material volatility & disposal scrutiny | -0.90% | Global, Europe regulatory lead | Short term (≤ 2 years) |
Specialty-polymer supply-chain disruptions | -0.60% | Global, Asia-Pacific sourcing | Medium term (2-4 years) |
Increasing demand for Bio-based, un-coated technical textiles | -0.40% | Europe and North America leading adoption | Long term (≥ 4 years) |
Source: Mordor Intelligence
PVC Raw-Material Volatility & Disposal Scrutiny
The EU’s proposal to restrict over 10,000 PFAS chemicals would directly affect vinyl-based coatings, as many formulations rely on fluorinated processing aids. Hanwha’s bio-attributed PVC, incorporating plant oils and waste cooking oil, cuts cradle-to-gate CO₂ by 58% yet carries higher feedstock costs that squeeze margins[3]Hanwha, “Bio-Attributed PVC Cuts 58% Carbon Emissions,” hanwha.com . Disposal fees and take-back schemes under the EU’s Extended Producer Responsibility (EPR) framework raise life-cycle costs for legacy PVC items, prompting OEMs to switch to PU and silicone systems despite upfront price premiums.
Specialty-Polymer Supply-Chain Disruptions
Tariffs on titanium dioxide, resins, and solvents from key trading partners inflate costs for technical-textile coaters in North America. Lead times for new polymer plants average 24 months, keeping short-term supply tight despite domestic expansion announcements. Coaters hedge risk through multi-regional sourcing and backward integration, but capital intensity and regulatory approvals prolong relief, particularly for novel recyclable or bio-based chemistries.
Segment Analysis
By Coating Material: Polymer Dominance Drives Innovation
Polymer coatings commanded 80.67% of the coated fabrics market share in 2024 as their versatility spans automotive, industrial, and consumer applications. Within this group, polyurethane grades are on track for a 6.93% CAGR to 2030, a pace that underscores OEM preference for flexible, solvent-free alternatives to vinyl. PVC retains scale benefits in tarpaulins and advertising banners, yet EPR fees and landfill bans shrink its addressable volume in Europe. Silicone systems win in high-temperature gaskets, while acrylic dispersion coatings anchor breathable outdoor gear. BASF’s 2024 launch of Haptex 4.0—a recyclable synthetic leather that co-recycles with PET—points to future formulations that streamline mechanical-recycling flows.
Continued R&D in bio-attributed polymers hints at fresh competition for incumbent chemistries. Rubber-coated fabrics meet niche demands for extreme abrasion yet face substitution by PU films that offer similar durability at lighter weights. Specialty nano-coatings that add conductivity or self-healing properties command premium margins, expanding the coated fabrics market into electronics and aerospace niches. Suppliers that master multi-layer co-casting and in-line curing stand to secure the highest returns as end-users seek turnkey solutions.
Note: Segment shares of all individual segments available upon report purchase
By Fabric Substrate: Polyester’s Dual Leadership
Polyester subtended 45.43% of the coated fabrics market share in 2024, and its 7.24% CAGR through 2030 illustrates unmatched versatility. The fibre’s strength-to-cost profile, dye receptivity, and compatibility with most polymer chemistries make it the default choice for airbags, luggage, and architectural membranes. Nylon remains indispensable for military tents and high-pressure hoses, but its higher price curtails share gains. Cotton enjoys a niche in breathable, fire-retardant workwear when paired with intumescent coatings, though synthetics are displacing blends in harsh environments.
Circularity pushes recycled polyester into mainstream procurement lists. Autoliv’s adoption of 100% post-consumer polyester yarns in airbags proves that safety-critical gear can incorporate reclaimed feedstock while meeting crash-test thresholds. Meanwhile, bio-based polyester pilot lines advance, but output stays limited relative to virgin PTA/MEG capacity. Rayon and wool underpin luxury fashion accessories coated for stain resistance, serving brands that prize tactile aesthetics over cost efficiency.
By Application: Transportation Leads, Protection Accelerates
Transportation generated 33.65% of the coated fabrics market size in 2024, buoyed by requirements for seat upholstery, airbags, and convertible tops. The pivot to electric drivetrains multiplies demand for lightweight thermal barriers that protect battery enclosures. At the same time, protective clothing is expected to compound at 7.84% annually through 2030 as governments tighten industrial-safety codes. Sioen Industries’ push into multi-hazard gear illustrates how certification drives premium pricing.
Furniture upholstery remains resilient, boosted by consumer appetite for stain-repellent, PFAS-free coatings in residential and office décor. Technical-industrial uses—geomembranes, conveyor belts, and flexible storage tanks—absorb elastomer-coated fabrics that offer chemical resistance and dimensional stability. Smaller slices such as banner media ride advertising cycles yet benefit from digital-printing growth on PU-coated polyester.
Note: Segment shares of all individual segments available upon report purchase
Geography Analysis
Asia-Pacific retained 47.02% of global revenue in 2024 and is projected to expand at a 6.39% CAGR to 2030. China anchors regional heft with its end-to-end textile base and surging EV output, while India’s expansion in technical-textile parks attracts fresh capital from multinationals like Saint-Gobain, which targets a three-fold local revenue lift by 2035. Japan and South Korea supply cutting-edge coating lines that enable haptic, sensor-rich fabrics, closing the loop between R&D and scaled manufacturing.
North America is a mature buyer emphasizing high-value niches. The United States dominates aerospace, defense, and medical bedding lines that demand strict traceability. Canada leads U.S. PVC-coated-fabric imports, benefiting from duty-free access and proximity, while Mexico widens capacity in automotive seating against a backdrop of near-shoring. Regional policy favors PFAS-free chemistries, spurring investment in water-borne PU dispersions.
Europe faces the world’s tightest textile regulations but leverages them to spearhead sustainable-coating technologies. The Extended Producer Responsibility framework launching in January 2025 obliges separate textile-collection systems, raising compliance hurdles for non-recyclable laminates. Germany and Italy concentrate on machinery exports that enable solvent-free, multi-pass lines; France and the Netherlands pilot chemical-recycling loops for coated off-cuts. The bloc’s looming PFAS curbs amplify demand for silicone and fluorine-free water barriers, giving EU producers a home-court edge in next-generation finishes.
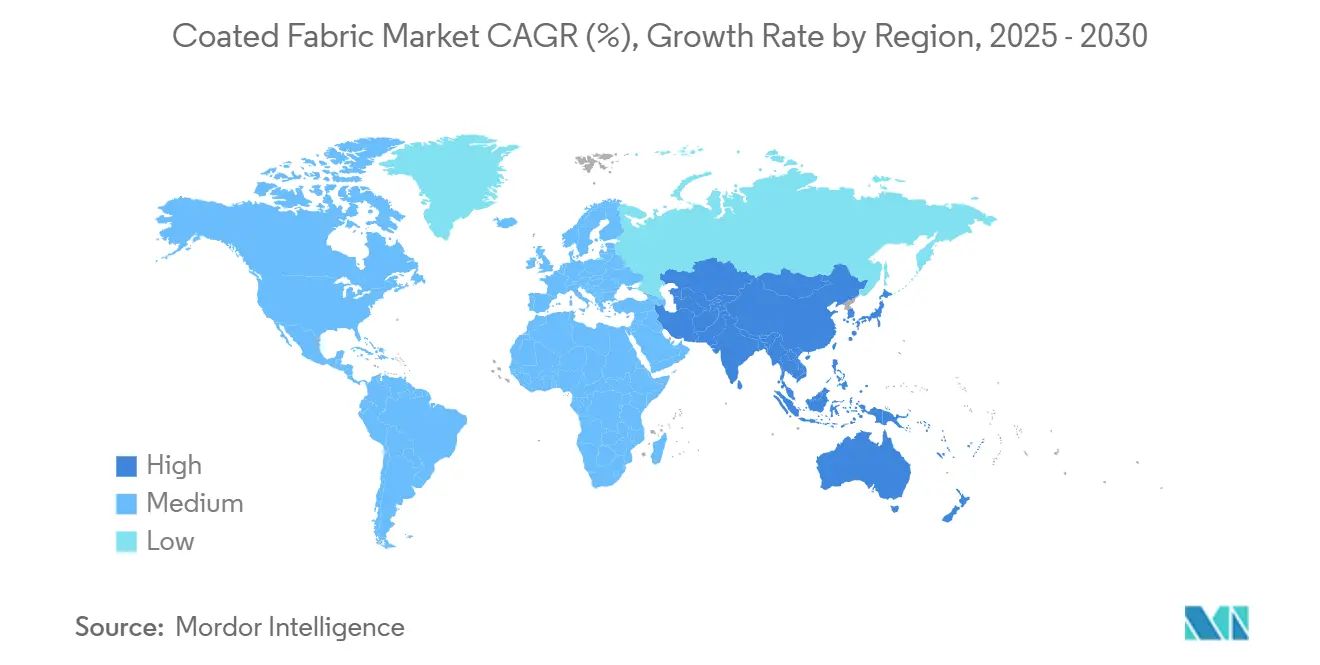
Competitive Landscape
The coated fabrics market is moderately fragmented: the top five suppliers controlled roughly 39% of 2024 revenue, reflecting vertical integration from polymer synthesis to finished rolls. Continental AG aligns its ContiTech division with vehicle electrification, offering low-emission silicone fabrics for battery enclosures. Freudenberg bolstered its reach by buying key Heytex assets for EUR 100 million in September 2024, adding three plants and deepening its presence in architectural membranes. Saint-Gobain’s Sekurit glass unit collaborates with its Performance Plastics arm to supply sunroof shade laminates compatible with panoramic roofs.
Specialty chemical players such as Covestro and BASF intensify competition by marketing PU systems tailored to circular-economy grades. Hanwha’s bio-attributed PVC marks an early mover advantage in low-carbon vinyl, though cost parity with conventional PVC remains elusive. Start-ups integrate printed circuits directly onto fabrics, offering OEMs turnkey sensor layers; incumbents respond via venture-capital arms to spot disruptive chemistries early. Success hinges on securing raw-material flexibility, certification portfolios, and R&D pipelines that keep pace with evolving eco-label thresholds.
Coated Fabric Industry Leaders
-
Continental AG
-
Graniteville
-
OMNOVA North America Inc.
-
Saint-Gobain
-
Trelleborg AB
- *Disclaimer: Major Players sorted in no particular order
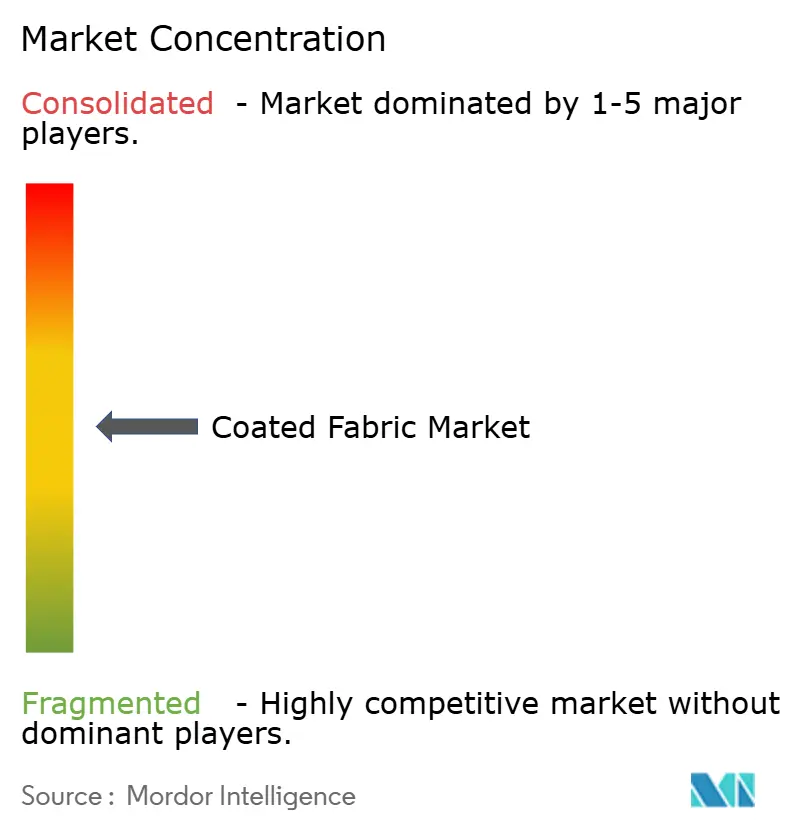
Recent Industry Developments
- December 2024: Trelleborg Engineered Coated Fabrics has partnered with Taiwan-based True Source to supply Dartex stretch TPU mattress covers for next-generation alternating-pressure medical beds. This collaboration strengthens Trelleborg's position in the premium healthcare coated fabrics market.
- September 2024: Freudenberg Performance Materials has strengthened its coated technical textiles segment by acquiring key assets of the Heytex Group for approximately EUR 100 million. The acquisition includes three production facilities in Germany and China.
Global Coated Fabric Market Report Scope
A coated fabric is a fabric that has been coated to make it more durable, stronger, and weather resistant. These fabrics are treated with a chemical that makes the surface more resistant to damage. The coated fabrics are widely utilized in a variety of applications, including transportation, protective apparel, industrial, furniture and seating, and others. The coated fabric market is segmented by product, application, and geography. By product, the market is segmented into polymer-coated, fabric-backed wall coverings, and rubber-coated products. By application, the market is segmented into automotive and transportation, protective clothing, furniture, industrial, and other applications. The report also covers the coated fabric market size and forecasts in 15 countries across major regions. For each segment, market sizing and forecasts have been done on the basis of revenue (USD million).
By Coating Material | Polymer Coated | PVC Coated | |
PU Coated | |||
PE Coated | |||
Other Polymer Coated Mterials (Acrylic Coated, Silicone Coated, etc.) | |||
Rubber Coated | |||
Fabric-Backed Wall Coverings | |||
By Fabric Substrate | Polyester | ||
Nylon | |||
Cotton and Blends | |||
Other (Wool, Rayon, etc.) | |||
By Application | Automotive and Transportation | ||
Protective Clothing | |||
Furniture | |||
Industrial | |||
Other Applications (Banners, Packaging, etc.) | |||
By Geography | Asia-Pacific | China | |
India | |||
Japan | |||
South Korea | |||
Rest of Asia-Pacific | |||
North America | United States | ||
Canada | |||
Mexico | |||
Europe | Germany | ||
United Kingdom | |||
Italy | |||
France | |||
Rest of Europe | |||
South America | Brazil | ||
Argentina | |||
Rest of South America | |||
Middle East and Africa | Saudi Arabia | ||
South Africa | |||
Rest of Middle East and Africa |
Polymer Coated | PVC Coated |
PU Coated | |
PE Coated | |
Other Polymer Coated Mterials (Acrylic Coated, Silicone Coated, etc.) | |
Rubber Coated | |
Fabric-Backed Wall Coverings |
Polyester |
Nylon |
Cotton and Blends |
Other (Wool, Rayon, etc.) |
Automotive and Transportation |
Protective Clothing |
Furniture |
Industrial |
Other Applications (Banners, Packaging, etc.) |
Asia-Pacific | China |
India | |
Japan | |
South Korea | |
Rest of Asia-Pacific | |
North America | United States |
Canada | |
Mexico | |
Europe | Germany |
United Kingdom | |
Italy | |
France | |
Rest of Europe | |
South America | Brazil |
Argentina | |
Rest of South America | |
Middle East and Africa | Saudi Arabia |
South Africa | |
Rest of Middle East and Africa |
Key Questions Answered in the Report
What is the current size of the coated fabrics market?
The coated fabrics market generated USD 24.67 billion in revenue in 2025 and is projected to reach USD 31.71 billion by 2030.
Which region leads coated fabrics consumption?
Asia-Pacific held 47.02% of global revenue in 2024 and is also the fastest-growing region, advancing at a 6.39% CAGR through 2030.
Which coating material segment is expanding most rapidly?
Polyurethane-coated fabrics are expected to grow at a 6.93% CAGR between 2025-2030 due to flexibility and PFAS-free formulation advantages.
Why are protective-clothing applications gaining momentum?
Stricter industrial-safety regulations and demand for antimicrobial performance push protective-clothing fabrics toward a 7.84% CAGR through 2030.
How are PFAS regulations influencing product innovation?
Impending PFAS bans are accelerating the shift toward silicone and PU chemistries, as suppliers redesign coatings to meet new sustainability and compliance standards.
Page last updated on: July 8, 2025