Ceramic Textile Market Size and Share
Ceramic Textile Market Analysis by Mordor Intelligence
The ceramic textile market size is USD 183.56 million in 2025 and is forecast to reach USD 238.32 million in 2030, registering a 5.36% CAGR over the period. Steady gains stem from the growing need for high-temperature insulation in steel, petrochemical and battery manufacturing environments where conventional materials fail. Favourable energy-efficiency mandates, advances in bio-persistent fibre chemistry and rising electric-vehicle production also widen the ceramic textile market opportunity. Competitive pressure is mounting as leading producers scale capacity, while regulatory scrutiny on worker safety accelerates the shift toward low bio-persistent grades. Together these factors signal a maturing ceramic textile market that is moving from niche adoption to broader industrial mainstream acceptance.
Key Report Takeaways
- By fiber, refractory ceramic fiber led with 56.18% ceramic textile market share in 2024; low bio-persistent fibre is projected to advance at a 6.58% CAGR through 2030.
- By type, cloth contributed 37.95% of the ceramic textile market size in 2024, whereas sleeving and braided sleeves are expected to grow at a 7.08% CAGR to 2030.
- By end-user industry, industrial processing accounted for 46.42% of the ceramic textile market size in 2024, while electrical and electronics is the fastest mover with a 7.45% CAGR to 2030.
- By geography, Asia-Pacific dominated with a 42.19% ceramic textile market share in 2024 and is set to expand at a 6.17% CAGR through 2030.
Global Ceramic Textile Market Trends and Insights
Driver Impact Analysis
Driver | (~) % Impact on CAGR Forecast | Geographic Relevance | Impact Timeline |
---|---|---|---|
Growing demand for high-temperature industrial insulation | +1.2% | Global, with concentration in Asia-Pacific and North America | Medium term (2-4 years) |
Energy-efficiency regulations in process industries | +0.8% | North America & EU, expanding to Asia-Pacific | Long term (≥ 4 years) |
Superior weight-to-performance characteristics | +1.1% | Global, particularly aerospace and automotive sectors | Short term (≤ 2 years) |
Adoption in battery-gigafactory thermal management | +0.9% | Asia-Pacific core, spill-over to North America | Medium term (2-4 years) |
Fire-resistant materials requirements for urban air mobility | +0.6% | North America & EU, early adoption markets | Long term (≥ 4 years) |
Source: Mordor Intelligence
Growing Demand for High-Temperature Industrial Insulation
Continuous-run steel, glass and petrochemical kilns now reach operating temperatures above 1,200 °C, creating structural and energy losses that conventional mineral wool cannot handle. Ceramic textiles cut heat loss by as much as 30% compared with legacy refractory bricks, delivering measurable fuel savings while extending maintenance cycles. Higher throughput targets in Asian plants intensify this push, so the ceramic textile market is becoming a critical enabler of furnace upgrades worldwide.
Energy-Efficiency Regulations in Process Industries
Revised greenhouse-gas disclosure rules compel industrial sites to document thermal efficiency improvements, making ceramic fabrics an easy pathway to regulatory compliance without large process overhauls[1]U.S. Environmental Protection Agency, “Greenhouse Gas Reporting Rule: Addition of Ceramics Manufacturing,” epa.gov. North American refineries and European ceramics lines already rely on ceramic insulation modules to stay within reporting thresholds, and similar legislation is appearing in China and India. These trends reinforce long-run demand and give the ceramic textile market a policy tail-wind.
Superior Weight-to-Performance Characteristics
Aerospace turbine shrouds, automotive battery shields and next-generation exhaust systems all benefit from ceramic fibre strength above 2,000 MPa while remaining lighter than metallic alternatives. Weight savings translate into greater fuel economy or extended electric-vehicle range, so design engineers increasingly specify ceramic cloth, tape and rope for heat shields. This enhances the ceramic textile market narrative around performance rather than cost.
Adoption in Battery-Gigafactory Thermal Management
Rapid gigafactory construction across China, Japan and the United States boosts demand for insulation that tolerates thousands of heat cycles without micro-cracking. Panasonic Energy and other cell makers integrate ceramic blankets into oven walls and pack assemblies to meet tight safety margins[2]Panasonic Energy Co., Ltd., “Panasonic Expands North American Lithium-Ion Battery Production,” panasonic.com . As global electric-vehicle output climbs, battery plants represent one of the most reliable volume pipelines for the ceramic textile market.
Restraint Impact Analysis
Restraint | (~) % Impact on CAGR Forecast | Geographic Relevance | Impact Timeline |
---|---|---|---|
Carcinogenic classification of refractory ceramic fiber | -0.7% | Global, with stricter enforcement in EU and North America | Short term (≤ 2 years) |
High production costs vs. conventional insulators | -0.4% | Global, particularly price-sensitive emerging markets | Medium term (2-4 years) |
Supply crunch of high-purity aluminosilicate feedstock | -0.3% | Global, with concentration in specialized mining regions | Long term (≥ 4 years) |
Source: Mordor Intelligence
Carcinogenic Classification of Refractory Ceramic Fibre
Occupational-exposure limits of 0.2 fibres/cm³ increase monitoring, personal-protective-equipment and disposal costs across plants that handle legacy refractory grades[3]Occupational Safety and Health Administration, “Permissible Exposure Limits for Refractory Ceramic Fiber,” osha.gov. Europe already mandates substitution assessments, accelerating the pivot to low bio-persistent fibres. This safety-driven switch trims short-term demand yet also stimulates innovation that ultimately widens the ceramic textile market.
High Production Costs versus Conventional Insulators
Sol-gel fibre drawing and sintering require tight temperature control and high-purity feedstocks, leading to prices that can be triple those of glass wool. Where thermal risks are lower than 800 °C, buyers often keep cheaper materials. Producers therefore invest in scale efficiencies and automated looms to narrow the cost gap, safeguarding future ceramic textile market competitiveness.
Segment Analysis
By Fiber: Bio-Persistent Alternatives Gain Momentum
Refractory ceramic fiber retained 56.18% of the ceramic textile market in 2024, valued near USD 103 million, yet its growth rate trails emerging low bio-persistent grades that post a 6.58% CAGR. Regulators and plant managers prefer fibres that dissolve in body fluids within 30 days, easing exposure compliance. The ceramic textile market size attributed to bio-persistent products could reach USD 62 million by 2030, confirming that health issues are no longer a niche concern.
Low-toxicity alumino-silicate fibers, polycrystalline mullite and engineered alkaline-earth silicate variants now match refractories on thermal shock resistance. Pilot lines in Japan and Germany already run fully on bio-persistent feedstock, while Chinese producers expand output for export. Strategic R&D partnerships with universities accelerate property improvements, ensuring the ceramic textile market remains technologically dynamic even as safer chemistries take hold.
Note: Segment shares of all individual segments available upon report purchase
By Type: Specialised Forms Drive Innovation
Cloth accounted for 37.95% of the ceramic textile market in 2024, translating to around USD 70 million. Demand here remains stable because cloth is versatile, easy to cut, and integrates well into furnace linings. Yet growth is shifting to sleeving, braided sleeves, tapes and ropes that together expand at 7.08% CAGR, raising their ceramic textile market share each year.
Automotive wire harnesses adopt braided sleeves for battery-fire containment, while turbine builders specify thick-wall sleeving for hot-gas duct protection. These tailored geometries open space for hybrid products that combine ceramic yarn with stainless-steel reinforcement, improving handling without sacrificing temperature limits. Advanced looms, precise braid angles and nanoparticle coatings create intellectual-property moats that protect margins inside the ceramic textile market.
By End-User Industry: Electronics Applications Accelerate
Industrial processing still represents 46.42% of the ceramic textile market size in 2024, driven by continuous kilns, reformers and glass forehearths. The segment enjoys predictable spending because any unscheduled shutdown quickly offsets material costs. However, electrical and electronics lines post a 7.45% CAGR thanks to denser semiconductor fabs, laser processing chambers and growing demand for chip packaging ovens.
As device geometries shrink, process windows tighten, so even minor thermal fluctuations can ruin yields. Ceramic tapes with low thermal mass stabilise temperature ramps, and woven gaskets resist plasma attack during wafer etching. This new volume eases reliance on cyclical steel output, cushioning the ceramic textile market whenever heavy industries slow.
Geography Analysis
Asia-Pacific held a 42.19% share of the ceramic textile market in 2024 and is on pace for a 6.17% regional CAGR. China leads kiln refurbishment projects, Japan focuses on fibre chemistry patents, and South Korea drives electronics-grade consumption. Access to aluminosilicate mines in Shandong and Guangxi further stabilises local supply chains, giving Asian producers a freight advantage into neighbouring refineries and battery plants.
North America remains strong in aerospace and is the fastest adopter of urban air mobility prototypes. Federal efficiency credit programmes reward facility upgrades, so US refineries replace old brick linings with folding ceramic modules despite higher upfront costs. Canadian nickel-cobalt projects, essential for EV supply chains, also deploy ceramic blankets in rotary calciners, broadening the ceramic textile market’s base in the region.
Europe balances high labour costs with world-class materials research. Germany’s composites clusters refine ceramic matrix processes, France leverages its civil-aviation footprint, and Scandinavian steelmakers retrofit blast-furnace tapholes with ceramic rope seals to curb CO₂ intensity. Tighter worker-safety directives accelerate migration to bio-persistent fibres, so European demand tilts towards premium grades that lift the regional average selling price. Together these factors make the ceramic textile market outlook resilient across all three major economic blocs.
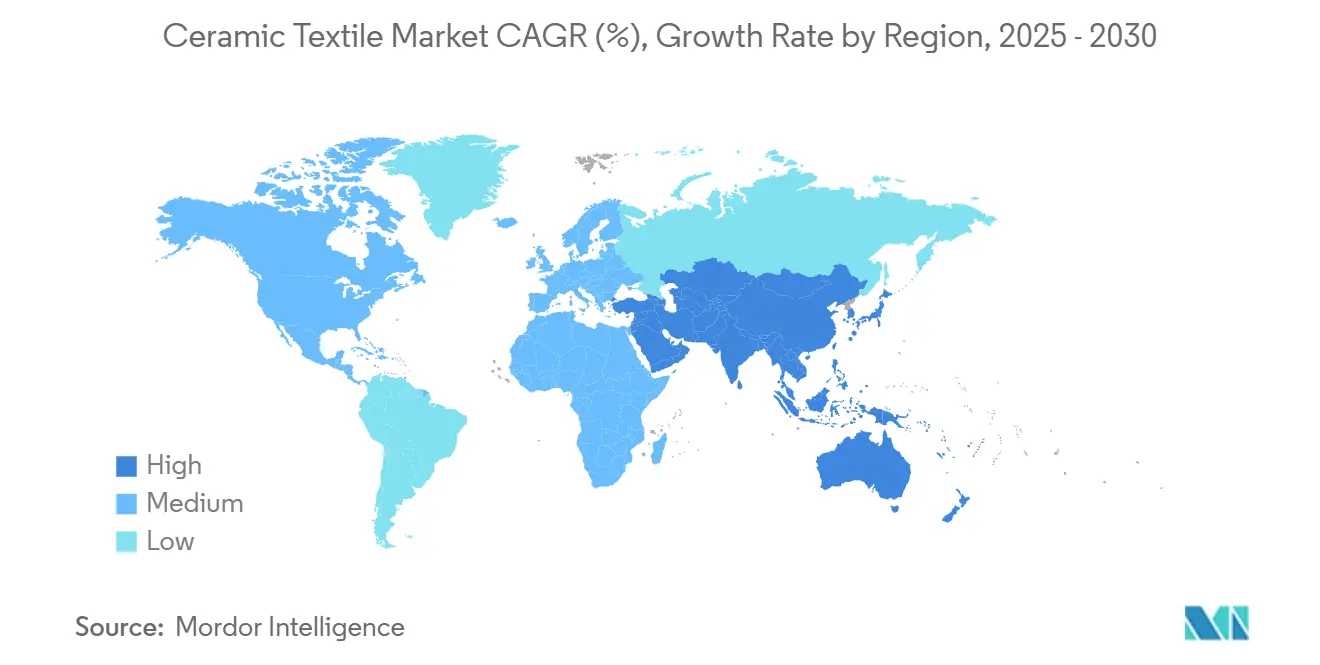
Competitive Landscape
The ceramic textile market is moderately fragmented, with global players competing alongside regional manufacturers. Companies like 3M leverage materials science expertise and distribution networks to maintain premium positions, while firms such as IBIDEN and Luyang Energy-saving Materials focus on niche applications or regional markets. Larger players are increasing investments in production capacity and R&D to address emerging applications like battery thermal management and urban air mobility. Vertical integration and application-specific product development are key strategies, as seen with Morgan Advanced Materials targeting high-value sectors like semiconductors and clean energy. Emerging opportunities in eVTOL aircraft thermal protection and next-generation battery systems favor companies with advanced technical capabilities. The market emphasizes advanced fiber chemistry, automated manufacturing, and tailored product development to meet sophisticated end-user demands.
Ceramic Textile Industry Leaders
-
3M
-
Mineral Seal Corporation
-
Alkegen
-
IBIDEN
-
Isolite Insulating Products Co., Ltd.
- *Disclaimer: Major Players sorted in no particular order
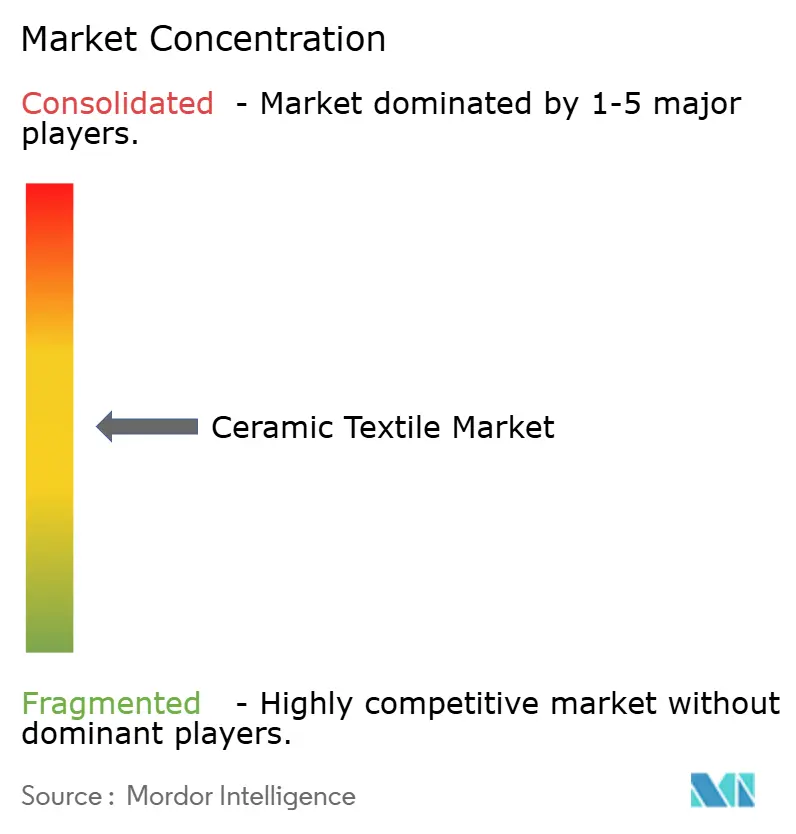
Recent Industry Developments
- November 2024: NUTEC Group expanded its headquarters in Huntersville, North Carolina, by doubling its floorspace to enhance the production capacity of ceramic-fiber modules and blankets.
- April 2024: The US Environmental Protection Agency, effective January 2025, incorporated ceramics manufacturing into its Greenhouse-Gas Reporting Rule, increasing compliance obligations for producers across the ceramic textile value chain.
Global Ceramic Textile Market Report Scope
The Ceramic Textile Market report include:
By Fiber | Refractory Ceramic | ||
Low Bio-Persistent | |||
Other Fibers (Polycrystalline Mullite Fiber, etc.) | |||
By Type | Cloth | ||
Tape | |||
Rope | |||
Yarn | |||
Other Types (Sleeving / Braided Sleeve, etc.) | |||
By End-User Industry | Industrial | ||
Transportation | |||
Other End-User Industries (Electrical and Electronics, etc.) | |||
By Geography | Asia-Pacific | China | |
India | |||
Japan | |||
South Korea | |||
Rest of Asia-Pacific | |||
North America | United States | ||
Canada | |||
Mexico | |||
Europe | Germany | ||
United Kingdom | |||
Italy | |||
France | |||
Rest of Europe | |||
South America | Brazil | ||
Argentina | |||
Rest of South America | |||
Middle East and Africa | Saudi Arabia | ||
South Africa | |||
Rest of Middle East and Africa |
Refractory Ceramic |
Low Bio-Persistent |
Other Fibers (Polycrystalline Mullite Fiber, etc.) |
Cloth |
Tape |
Rope |
Yarn |
Other Types (Sleeving / Braided Sleeve, etc.) |
Industrial |
Transportation |
Other End-User Industries (Electrical and Electronics, etc.) |
Asia-Pacific | China |
India | |
Japan | |
South Korea | |
Rest of Asia-Pacific | |
North America | United States |
Canada | |
Mexico | |
Europe | Germany |
United Kingdom | |
Italy | |
France | |
Rest of Europe | |
South America | Brazil |
Argentina | |
Rest of South America | |
Middle East and Africa | Saudi Arabia |
South Africa | |
Rest of Middle East and Africa |
Key Questions Answered in the Report
What is the current Ceramic Textile Market size?
The ceramic textile market is valued at USD 183.56 million in 2025 and is forecast to reach USD 238.32 million by 2030, reflecting a 5.36% CAGR.
Which region holds the largest share and is expanding the quickest?
Asia-Pacific commands 42.19% of global revenue in 2024 and is advancing at a 6.17% CAGR, the fastest among all regions.
How do ceramic textiles help improve industrial energy efficiency?
Ceramic fiber linings can cut furnace heat loss by up to 30%, allowing plants to meet energy-efficiency mandates without major process redesign.
What key restraints limit wider ceramic textile adoption?
Carcinogenic classification of some fibers, elevated production costs versus mineral wool, and occasional feedstock shortages all temper market expansion.
Page last updated on: June 30, 2025