Advanced Ceramics Market Size and Share
Advanced Ceramics Market Analysis by Mordor Intelligence
The advanced ceramics market is valued at USD 104.34 billion in 2025 and is forecast to expand to USD 144.44 billion by 2030, advancing at a 6.72% CAGR. Rising demand for materials that combine lightweight, high hardness, and thermal resilience is pushing aerospace, electronics, energy, and healthcare manufacturers to shift away from metals and high-performance polymers. Material innovation, particularly around titanate-based electroceramics and ceramic matrix composites, enlarges the addressable opportunity set for suppliers. Asia-Pacific retains its leadership position due to strong semiconductor capital expenditure, while medical applications record double-digit growth as bioceramics replace metal implants. Although elevated production costs and complex sintering pathways remain headwinds, automation, additive manufacturing, and closed-loop recycling initiatives steadily improve cost curves and environmental footprints.
Key Report Takeaways
- By material type, alumina commanded 41% of the advanced ceramics market share in 2024, while titanate ceramics are projected to grow at a 7.8% CAGR through 2030.
- By class type, monolithic ceramics led with 78% revenue share in 2024; ceramic matrix composites are forecast to expand at an 8.12% CAGR through 2030.
- By application, electroceramics accounted for 45% share of the advanced ceramics market size in 2024, and bioceramics are projected to advance at an 8.77% CAGR through 2030.
- By end-user industry, electronics held 44% of the advanced ceramics market share in 2024, while the medical sector is expanding at an 11.84% CAGR to 2030.
- By geography, Asia-Pacific dominated with a 54% share of the advanced ceramics market in 2024 and is expected to post a 7.06% CAGR through 2030.
Global Advanced Ceramics Market Trends and Insights
Driver Impact Analysis
Drivers | (~) % Impact on CAGR Forecast | Geographic Relevance | Impact Timeline |
---|---|---|---|
Metals and plastics substitution | +1.1% | North America, Europe | Medium term (2-4 years) |
Rapid uptake in medical devices | +2.3% | North America, Europe, developed Asia-Pacific | Long term (≥ 4 years) |
Eco-friendly and reliable performance profile | +0.8% | Europe, North America | Long term (≥ 4 years) |
Electronics and semiconductor demand | +1.5% | Asia-Pacific, North America | Medium term (2-4 years) |
Aerospace and Defense Sector demand | +1.8 | North America, Europe, and the Asia-Pacific defense markets | Medium term |
Source: Mordor Intelligence
Rise in Use as Alternative to Metals and Plastics
Advanced ceramics deliver hardness, wear resistance, and temperature stability that metals cannot match. Ceramic matrix composites in jet-engine hot sections cut component weight by 30% and improve fuel burn by 15% compared with nickel super-alloys. Automotive turbocharger rotors fabricated from silicon nitride withstand exhaust streams above 1,000 °C while maintaining dimensional accuracy. Industrial pump housings made from alumina and zirconia now last three to five times longer than stainless variants in abrasive slurries.
Growing Demand in the Medical Industry
Bioceramics such as alumina and zirconia exhibit proven biocompatibility and minimal ion release, which lengthens implant lifespans and decreases revision surgeries. Surgeons increasingly rely on 3D-printed silicon-nitride spinal cages tailored to patient anatomy, an advance made possible by low-temperature stereolithography. Orthopedic device makers also experiment with bioactive glass coatings that stimulate osteointegration and with drug-eluting porous ceramics for localized therapeutics.
Eco-friendliness and Reliability of Use
Ceramics are chemically inert and derived from plentiful minerals, which limits pollution during both use and disposal. Modern kilns equipped with recuperative burners cut CO₂ emissions by 30% relative to legacy tunnel kilns. Circular initiatives add further momentum. IKEA now incorporates up to 70% factory-generated ceramic scrap into new tableware lines, reducing landfill burden and raw-clay extraction.
Increasing Demand from Electronics and Semiconductors Industry
Aluminium nitride substrates with thermal conductivity above 170 W/m·K enable efficient heat extraction from high-power chips, safeguarding device reliability at smaller node sizes. Rapid expansion of foundry capacity in East Asia and the United States is therefore pulling additional demand for dielectric ceramics, packaging materials and lithography tool components.
Restraint Impact Analysis
Restraints | (~) % Impact on CAGR Forecast | Geographic Relevance | Impact Timeline |
---|---|---|---|
High production costs | -1.2% | Global | Short term (≤ 2 years) |
Complex manufacturing processes | -0.9% | Global | Medium term (2-4 years) |
End-of-life recycling constraints | -0.7% | Europe, North America | Long term (≥ 4 years) |
Source: Mordor Intelligence
Complex Manufacturing Process
Maintaining ±5 °C uniformity at 1,600 °C across large load sizes is challenging. Even minor temperature gradients create residual stresses that downgrade mechanical strength, forcing suppliers to perform additional inspection and culling. Precision grinding of fully sintered parts often records yields below 85% on complicated geometries. Additive manufacturing technologies such as binder jetting show promise by building near-net-shape parts that need minimal finishing, but throughput and surface finish still trail conventional routes
End-of-Life Recycling Challenges Limiting ESG Adoption
Unlike metals, advanced ceramics cannot be remelted without destroying phase integrity. Most industrial scrap ends up in landfills, which undermines corporate sustainability targets. Researchers explore the reuse of pulverized ceramic waste as filler for geotechnical grouts or as flux in glass making. Carbon Rivers has piloted a glass-to-glass reclamation process that converts ceramic-rich composites into clean fibers, pointing toward feasible downstream valorization.
Segment Analysis
By Material Type: Alumina Retains Scale While Titanate Gains Momentum
Alumina dominated the advanced ceramics market with a 41% share in 2024, supported by its balanced cost-performance profile and established supply chains. The material is entrenched in substrates, cutting tools, biomedical heads, and wear parts. Continuous process refinements now deliver sub-micron grain sizes that lift fracture toughness to 6 MPa·m½, enabling thinner components without performance trade-offs. On the demand side, electrification of transport and grid storage drives purchases of alumina-rich insulating hardware.
Titanate ceramics are the fastest-expanding material group at a 7.8% CAGR through 2030. Barium titanate multilayer capacitors remain the backbone of power-management circuits in smartphones and electric vehicles. Concurrently, lead-free potassium sodium niobate titanates gain traction in sonar transducers as a sustainable replacement for lead zirconate titanate. Recent research demonstrated ZnTiO₃-ZnO nanocomposite coatings that kill 97% of Staphylococcus aureus on contact, widening titanate potential in antimicrobial surfaces.
Note: Segment shares of all individual segments available upon report purchase
By Class Type: Monolithic Dominance Faces Composite Challenge
Monolithic ceramics held 78% of the advanced ceramics market size in 2024 because single-phase alumina, zirconia, and silicon nitride are well understood and cost-efficient at scale. Standardization around ISO 602 and ASTM C1327 test methods simplifies qualification for aerospace or medical entry, sustaining volume momentum. Producers continue to improve reliability through powder morphology control, resulting in Weibull moduli above 20 for structural grades, which reduces part-to-part variability.
Although smaller in dollar terms, Ceramic matrix composites exhibit an 8.12% CAGR owing to their transformational weight-to-strength trade-off. Exhaust systems and next-generation nozzle guide vanes now use silicon-carbide fiber–reinforced silicon-carbide matrices that tolerate 1,400 °C gas streams without active cooling. Airbus and GE are flight-testing oxide-oxide CMCs in fuselage stiffeners to curb maintenance costs. Electrochemical energy companies apply carbon-fiber-reinforced alumina in solid-oxide fuel-cell interconnects to extend stack life. The rapid conversion of laboratory concepts into commercial runs underscores the composite class as a major disruptive force within the advanced ceramics industry.
By Application: Electroceramics Lead as Bioceramics Accelerate
Electroceramics occupied 45% of the advanced ceramics market in 2024 and continue gaining relevance as chipmakers chase thermal management and miniaturization. Aluminium nitride substrates and beryllia alternatives dissipate heat swiftly in radio-frequency modules, while piezoelectric stacks convert electrical signals into mechanical displacement in precision motion platforms. The upcoming Electronic Materials and Applications 2025 forum will spotlight dielectric capacitors for hydrogen electrolysers and quantum computing packaging[1]American Ceramic Society, “Electronic Materials and Applications 2025,” ceramics.org.
Bioceramics, although representing a smaller monetary base, deliver the steepest growth trajectory, advancing at an 8.77% CAGR through 2030. Orthopedic surgeons prefer zirconia-toughened alumina hip heads because the composite’s flexural strength exceeds 1 200 MPa, mitigating in-vivo fracture risk. Dental implantologists use porous hydroxyapatite coatings that encourage osseointegration within 12 weeks. Research groups are coupling calcium-phosphate scaffolds with antibacterial copper ions to curb post-operative infections. As demographic ageing lifts implant volumes, healthcare procurement budgets increasingly allocate funds toward advanced ceramic solutions despite higher upfront prices.
By End-user Industry: Electronics Anchor Demand while Medical Gains Pace
The electrical and electronics sector captured 44% of 2024 revenue because semiconductors, sensors, and power modules rely on consistent dielectric performance across varying temperatures. Foundry expansions under the United States CHIPS and Science Act, Japan’s supply-chain revitalization programs, and China’s self-reliance blueprint all converge on higher pull for ceramic etch rings, wafer chucks, and test sockets.
Medical devices display the swiftest rise, expanding at 11.84% CAGR. Bioceramic spinal cages reduce artefacts in magnetic-resonance imaging and permit surgeons to track fusion progress. Cardiovascular interventionists experiment with zirconia-reinforced lithium-silicate guidewire tips that navigate tortuous vessels without kinking. Hospital procurement pivots toward ceramic surgical tools that stay sharp longer and can withstand repeated autoclave cycles without corrosion, elevating total cost-of-ownership advantages.
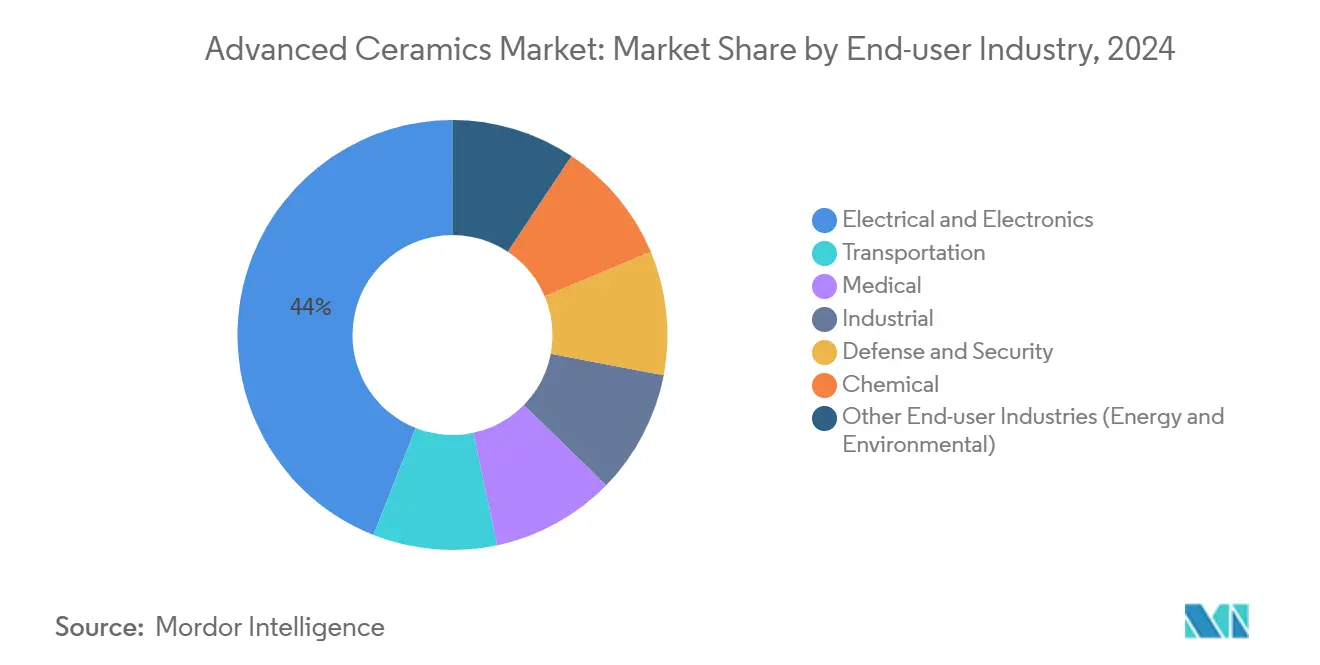
Note: Segment shares of all individual segments available upon report purchase
Geography Analysis
Asia-Pacific possessed 54% of the advanced ceramics market in 2024, underpinned by dense electronics clusters, established powder supply chains, and government incentives for high-value materials. China’s 14th Five-Year Plan classifies advanced ceramics as a strategic segment, unlocking tax credits and grant funding for pilot lines.
North America is witnessing a rise in consumption owing to robust aerospace, defense, and medical verticals. The United States Air Force Research Laboratory actively funds lightweight CMC combustor liners to extend jet-engine service intervals. Orthopedic device hubs in Indiana and Tennessee procure large volumes of zirconia-toughened alumina for hip components, driving concentrated regional demand.
Europe maintains a prominent footprint through Germany’s advanced machinery and Italy’s sanitary ware expertise. The European Commission’s Advanced Materials for Industrial Leadership initiative emphasizes sustainability and recyclability, ensuring research budgets flow into low-carbon sintering and circular-economy pilots[2]European Commission, “Chemicals and Advanced Materials – Research and Innovation,” research-and-innovation.ec.europa.eu.
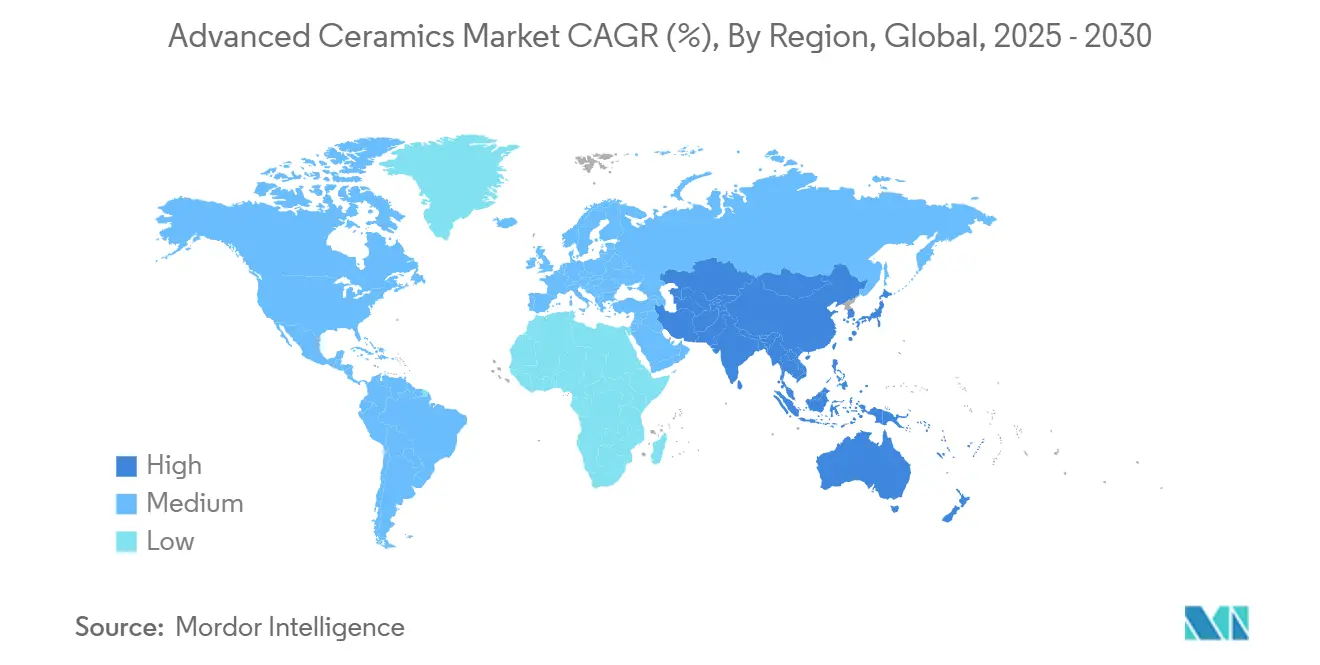
Competitive Landscape
The advanced ceramics market is highly fragmented. Strategic collaboration is intensifying. Semiconductor capital-equipment makers enter long-term agreements with ceramic suppliers to lock in purity and capacity, mitigating geopolitical supply disruptions. Aerospace primes coordinate qualification pathways for CMC turbine parts, ensuring parallel scale-up of fiber and matrix feedstocks. Overall, differentiation hinges on processing know-how, powder-to-part traceability, and the capability to co-design components with end users.
Advanced Ceramics Industry Leaders
-
KYOCERA Corporation
-
CoorsTek Inc.
-
CeramTec GmbH
-
Morgan Advanced Materials
-
3M
- *Disclaimer: Major Players sorted in no particular order
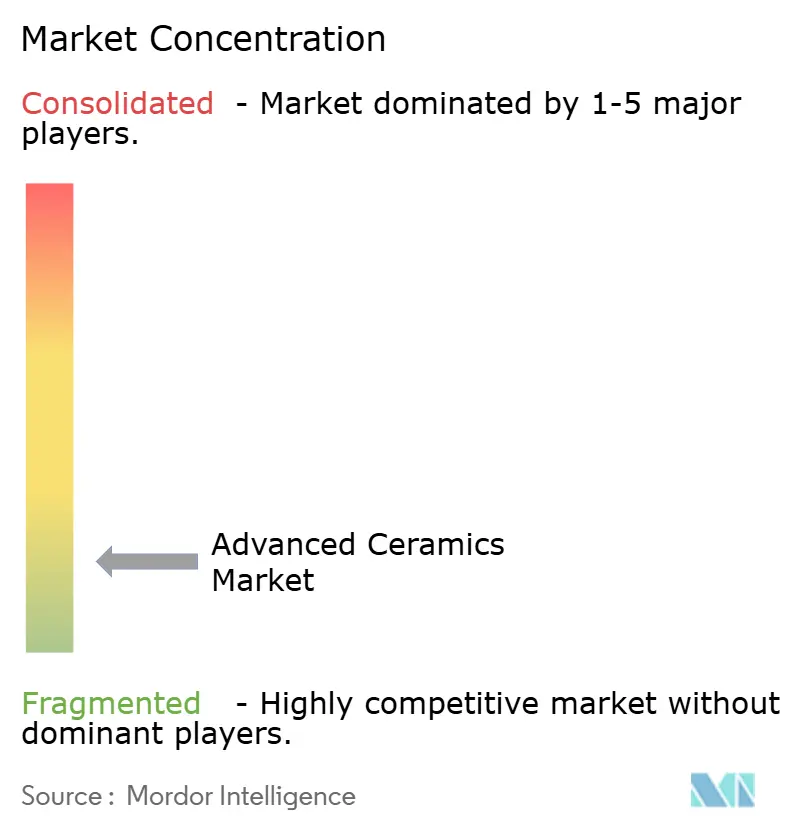
Recent Industry Developments
- August 2024: CoorsTek Inc. opened its third factory in Gumi, South Korea, positioning the site as a new-product-introduction center for advanced semiconductor equipment components.
- February 2024: Murata Manufacturing’s Izumo subsidiary broke ground on a multilayer ceramic capacitor facility in Shimane, Japan, expanding capacity to satisfy medium- and long-term demand.
Global Advanced Ceramics Market Report Scope
The advanced ceramics market is segmented by material type, class type, end-user industry, and geography. By material type, the market is segmented into alumina, titanate, zirconia, silicon carbide, aluminum nitride, silicon nitride, magnesium silicate, pyrolytic boron nitride, and other material types. By class type, the market is segmented into monolithic ceramics, ceramic matrix composites, and ceramic coatings. By end-user industry, the market is segmented into electrical and electronics, transportation, medical, industrial, defense and security chemical, and other end-user industries. The report also covers the market size and forecasts in 15 countries across major regions. The market sizing and forecasts for each segment have been calculated based on revenue (USD million).
By Material Type | Alumina | ||
Zirconia | |||
Titanate | |||
Silicon Carbide | |||
Silicon Nitride | |||
Aluminum Nitride | |||
Magnesium Silicate | |||
Pyrolytic Boron Nitride | |||
Others | |||
By Class Type | Monolithic Ceramics | ||
Ceramic Matrix Composites | |||
Ceramic Coatings | |||
By Application | Structural Ceramics | ||
Bioceramics | |||
Electroceramics | |||
Wear and Corrosion Components | |||
Thermal Barrier and UHTC Components | |||
Catalyst Supports and Filters | |||
Others (Environmental and Energy Systems) | |||
By End-user Industry | Electrical and Electronics | ||
Transportation | |||
Medical | |||
Industrial | |||
Defense and Security | |||
Chemical | |||
Other End-user Industries (Energy and Environmental) | |||
By Geography | Asia-Pacific | China | |
India | |||
Japan | |||
South Korea | |||
Rest of Asia-Pacific | |||
North America | United States | ||
Canada | |||
Mexico | |||
Europe | Germany | ||
United Kingdom | |||
France | |||
Italy | |||
Rest of Europe | |||
South America | Brazil | ||
Argentina | |||
Rest of South America | |||
Middle-East and Africa | Saudi Arabia | ||
South Africa | |||
Rest of Middle-East and Africa |
Alumina |
Zirconia |
Titanate |
Silicon Carbide |
Silicon Nitride |
Aluminum Nitride |
Magnesium Silicate |
Pyrolytic Boron Nitride |
Others |
Monolithic Ceramics |
Ceramic Matrix Composites |
Ceramic Coatings |
Structural Ceramics |
Bioceramics |
Electroceramics |
Wear and Corrosion Components |
Thermal Barrier and UHTC Components |
Catalyst Supports and Filters |
Others (Environmental and Energy Systems) |
Electrical and Electronics |
Transportation |
Medical |
Industrial |
Defense and Security |
Chemical |
Other End-user Industries (Energy and Environmental) |
Asia-Pacific | China |
India | |
Japan | |
South Korea | |
Rest of Asia-Pacific | |
North America | United States |
Canada | |
Mexico | |
Europe | Germany |
United Kingdom | |
France | |
Italy | |
Rest of Europe | |
South America | Brazil |
Argentina | |
Rest of South America | |
Middle-East and Africa | Saudi Arabia |
South Africa | |
Rest of Middle-East and Africa |
Key Questions Answered in the Report
What is the projected Advanced Ceramics market size by 2030?
The market is forecast to reach USD 144.44 billion by 2030.
Which region holds the largest Advanced Ceramics market share today?
Asia-Pacific leads, accounting for roughly 54% of global revenue in 2024.
Why are advanced ceramics preferred in medical implants?
They offer high biocompatibility, wear resistance, and long service life, which reduce revision surgeries.
Which ceramic class is growing fastest?
Ceramic matrix composites are expanding most rapidly due to aerospace and energy turbine adoption.
Page last updated on: June 23, 2025