Brick Market Size and Share
Brick Market Analysis by Mordor Intelligence
The Brick Market size is estimated at USD 1.73 trillion in 2025, and is expected to reach USD 1.99 trillion by 2030, at a CAGR of 2.91% during the forecast period (2025-2030). Asia-Pacific remains the anchor, supplying both the largest sales volumes and the strongest growth momentum as urban populations rise and infrastructure programs scale up. Product innovation focuses on low-carbon fly-ash and calcium-silicate variants in response to tightening climate rules, while direct project-based procurement accelerates as contractors seek fewer intermediaries. Demand from non-residential construction—especially warehouses, data centers, and transport hubs—outpaces residential activity, reflecting the expanding digital economy and public-works spending. Meanwhile, European producers face cost pressures from the Carbon Border Adjustment Mechanism, prompting early movers to invest in decarbonized kilns and alternative fuels.
Key Report Takeaways
- By brick type, clay bricks led with 65% of the brick market share in 2024, while fly-ash bricks posted the fastest 3.22% CAGR to 2030.
- By application, building accounted for 60% share of the brick market size in 2024; path applications are set to expand at 3.14% CAGR between 2025 and 2030.
- By end-use industry, residential buildings held a 55% share in 2024, whereas the non-residential segment is growing faster at 3.34% CAGR through 2030.
- By distribution channel, dealer & retail networks captured 60% of 2024 revenue; direct project-based channels register the highest 3.70% CAGR for 2025-2030.
- By geography, Asia-Pacific held 48% revenue share of the brick market in 2024 and is advancing at a 3.44% CAGR through 2030.
Global Brick Market Trends and Insights
Drivers Impact Analysis
Driver | (~) % Impact on CAGR Forecast | Geographic Relevance | Impact Timeline |
---|---|---|---|
Post-COVID Re-urbanisation Boosting Mid-Rise Housing Demand in Asia | +0.80% | Asia-Pacific, spillover to Africa | Medium term (2-4 years) |
Green’ Building Codes Driving Fly-Ash and Calcium-Silicate Brick Uptake in Europe | +0.50% | Europe, North America | Long term (≥ 4 years) |
Modular Construction Increases Demand for High-Strength Hollow Bricks | +0.40% | Global, strongest in developed markets | Medium term (2-4 years) |
Government-Subsidised Low-Cost Housing in Sub-Saharan Africa | +0.70% | Sub-Saharan Africa, South Asia | Short term (≤ 2 years) |
Expansion of E-Commerce Warehousing in South America | +0.30% | South America, Asia-Pacific | Short term (≤ 2 years) |
Source: Mordor Intelligence
Post-COVID Re-urbanisation Boost
Rapid migration back to major Asian cities is refilling pipelines for mid-rise housing projects, sustaining steady brick market demand. UN ESCAP projects the region’s urban population will touch 3.2 billion by 2030, spawning 22 megacities[1]United Nations Economic and Social Commission for Asia and the Pacific, “United Nations report calls for urgent response to harness Asia-Pacific’s urban transformation,” unescap.org . Mid-rise formats rely on masonry for cost-effective load-bearing walls and local labor familiarity. Governments are increasing social-housing budgets to narrow deficits—India alone recorded an 18.7-million-unit gap in 2024, while Indonesia tallied 12.5 million units, each amplifying baseline need for bricks. Vendors position supply hubs close to Tier-1 growth corridors to minimize freight costs. Equipment upgrades that raise kiln capacity without higher fuel burn ensure contractors receive on-time deliveries during cyclical building surges.
‘Green’ Building Codes
Europe’s 90% emissions-cut target for 2040 is reshaping the brick market, accelerating the adoption of fly-ash and calcium-silicate bricks with smaller carbon footprints. Calcium-silicate units consume 241 kWh/t of primary energy versus higher values for traditional clay, appealing to designers seeking certification under the UK Net Zero Carbon Buildings Standard. Concrete bricks that bypass firing processes can save 2.4 tonnes of CO₂ per house and become net absorbers over their lifecycle. Public-sector projects now embed minimum recycled-material thresholds, pushing plants to integrate glass cullet and combusted solid waste into mixes. Manufacturers that verify cradle-to-site life-cycle data lock in specification advantage for renovation and public procurement tenders.
Modular Construction
Off-site prefabrication is scaling, compressing project timelines by 30-50% and cutting labor outlays by up to 80%. Modular builders require lightweight, high-strength hollow bricks that integrate with panelized frames. Porotherm clay units deliver superior thermal insulation in Australian pilots, matching structural codes while lowering embodied energy. Digital design tools such as BIM and real-time sensor feedback help optimize dimensions, enabling near-zero off-cuts on-site. Heidelberg Materials reports AI-guided batching systems that trim cement use by 20%, a benefit passed along to brick lines dedicated to modular packages.
Government-Subsidised Housing
Sub-Saharan initiatives are catalysts for the brick market as authorities aim to solve acute shelter shortages. Kenya targets 250,000 units annually to reduce its 2 million-home deficit. Zimbabwe has scheduled 220,000 dwellings by 2025, while Nigeria estimates a 28 million-home shortfall needing USD 46.7 billion investment. Builders favor locally sourced masonry that withstands hot climates and cuts import bills. 3D-printed schemes such as Mvule Gardens in Kenya demonstrate how fly-ash-based mortars can accelerate production; each two-bedroom shell is printed in 18 hours. Such proof points embed brick alternatives into subsidy frameworks, widening material uptake.
Restraints Impact Analysis
Restraint | (~) % Impact on CAGR Forecast | Geographic Relevance | Impact Timeline |
---|---|---|---|
Increasing Trends of Prefabricated Construction Components | -0.60% | North America, Europe, Australia | Medium term (2-4 years) |
Volatility in Clay Feedstock Prices in Asia | -0.30% | Asia-Pacific | Short term (≤ 2 years) |
Carbon-Tax Exposure for Energy-Intensive Kilns in Europe | -0.50% | Europe | Long term (≥ 4 years) |
Source: Mordor Intelligence
Prefabricated Construction Components
As labor shortages intensify, builders in North America and Europe pivot toward volumetric modules that sideline brick facades. Prefab solutions remove 30-50% of on-site time and lower labor costs by 50-80%. With the United States needing another 501,000 skilled workers in 2025, contractors view standard panels as risk hedges. Thin-brick slips and mechanically fixed veneers let masonry suppliers stay relevant, yet overall unit demand dips where full-bed bricks are displaced. Manufacturers invest in robotic laying lines to service hybrid wall panels but must amortize capital across a shrinking traditional volume base, squeezing margins.
Carbon-Tax Exposure
European makers confront escalating compliance costs as the EU Emissions Trading System expands and the Carbon Border Adjustment Mechanism phases in during 2026-2030. Producers shifting to biomethane or hydrogen reduce Scope 1 emissions but face high retrofit bills and uncertain fuel supply. Importers from low-carbon grids could gain footholds if domestic players lag, restructuring competitive hierarchies. Firms adopting regenerative burners and heat-recovery on dryers already claim 15% lower energy intensity, cushioning levy increases.
Segment Analysis
By Brick Type: Sustainability Drives Material Choice
Clay bricks dominated the brick market with 65% of revenue in 2024, yet fly-ash bricks record a 3.22% CAGR through 2030, widening their presence in regions tightening carbon rules. This shift is anchored in industrial-waste utilization, enabling plants to cut firing temperatures by 20% and align with circular-economy mandates. The brick market size for fly-ash variants is forecast to expand faster than any other type, helped by public procurement criteria that reward recycled content. Calcium-silicate units attract architects pursuing thermal-mass advantages in Europe’s cool climates, while concrete blocks that skip kiln firing appeal where electricity is available and fuel security is uncertain.
Technological advances include char-based thin bricks exhibiting 4-7% water absorption, outperforming commercial peers and costing USD 25.83 per sq m, less than half the prevailing price for traditional options. Makers also promote hollow configurations that cut embodied CO₂ and lighten logistics loads. Collectively, these innovations reinforce the brick market goal of decarbonization without sacrificing structural reliability. Only a handful of early adopters own patents, hinting at near-term licensing revenue streams that could reshape profit pools within the brick industry.
Note: Segment shares of all individual segments available upon report purchase
By Application: Core Building Uses Retain Primacy
Building applications accounted for 60% of brick market share in 2024, reflecting masonry’s historic role in structural walls and facades. Code updates promoting airtight envelopes and fire resistance sustain this core demand. The brick market size for path and paving solutions, however, is expanding at a 3.14% CAGR as households invest in outdoor upgrades and municipalities retrofit sidewalks to endure heavier pedestrian flows.
Manufacturers exploit colorfast clays and high-friction textures to serve landscaping customers seeking design variety with low maintenance. Bricks configured with interlocking edges accelerate installation, lowering contractor costs and aligning with quick-turn renovation schedules. Parterre and decorative garden formats resurface in premium estates where aesthetic differentiation commands higher margins. Industrial customers favor acid-resistant bricks for furnace linings and chemical-processing pits, reinforcing a diverse end-use spread that shelters producers from single-sector downturns.
By End-Use Industry: Infrastructure Shapes Growth Profile
Residential buildings retained a 55% revenue position in 2024, yet the non-residential segment leads growth at 3.34% CAGR as governments fund transport corridors and e-commerce firms extend distribution hubs. The brick market supports massive warehouse floors that demand durable, thermally stable walls to moderate interior climates in tropical South America. Data centers classified as critical infrastructure in the United States also elevate orders for fire-rated brick envelopes.
In housing, rising mortgage rates in 2024 curtailed starts, but planned cuts from 2025 reinvigorate single-family construction, particularly in North America. Regulatory pushes for net-zero dwellings incentivize wall systems that retain heat and lower operational energy. Brick veneers matched with external-insulation finishing systems satisfy these performance metrics while preserving traditional curb appeal. Public-sector rental programs in Europe and Asia formalize quotas for low-carbon bricks, cushioning residential volume dips elsewhere.
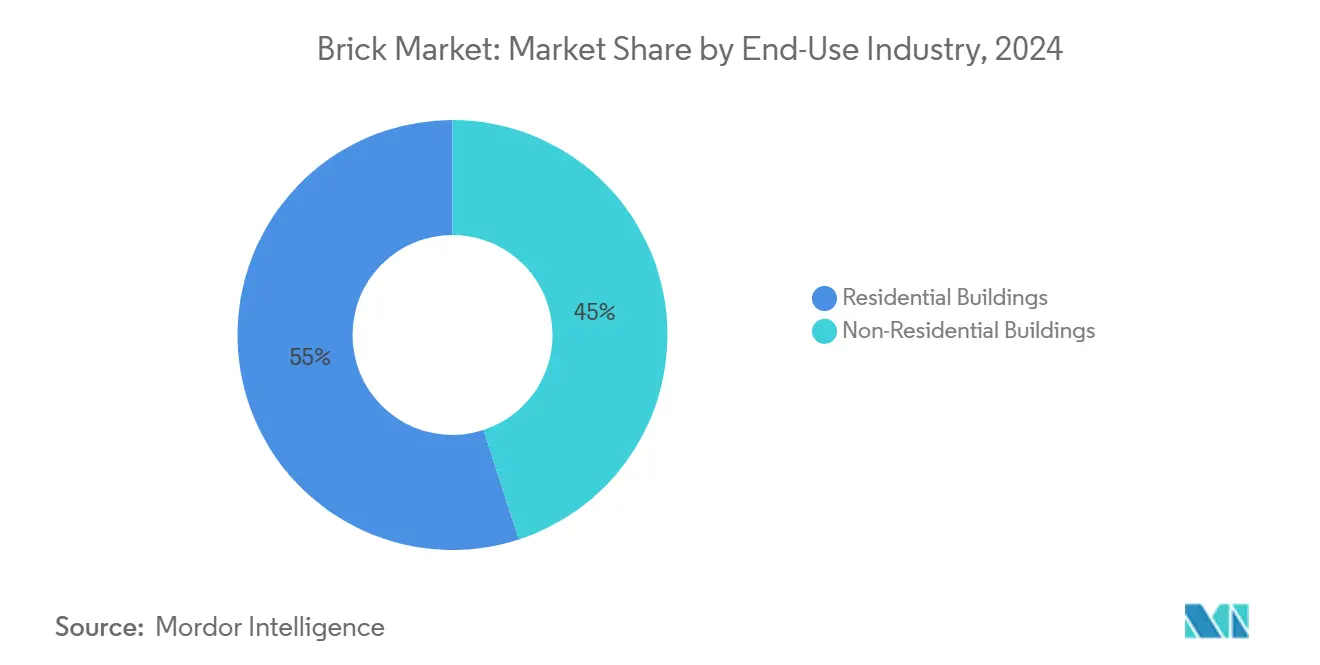
By Distribution Channel: Direct Project Path Gains Traction
Dealer and retail outlets captured 60% of brick market revenue in 2024 thanks to entrenched suburban dealer networks and DIY refurbishment demand. Yet direct project-based distribution is the fastest lane, expanding 3.70% annually as contractors integrate procurement with scheduling software. Major U.S. roofing distributor SRS was acquired by The Home Depot for USD 18.25 billion, underscoring consolidation that favors high-volume direct buys.
Digital portals such as Beacon PRO+ let site managers place repeat orders and track deliveries, improving inventory accuracy and cash-flow planning. Artificial-intelligence tools route trucks to mitigate driver shortages and cut fuel burn, further reducing landed costs. Dealers respond by specializing in colored or antique-finish bricks with value-added design services, protecting margins even as high-rise contractors bypass intermediaries. Market participants expect hybrid models where manufacturers run direct key-account teams while maintaining dealer partners for patchwork residential demand.
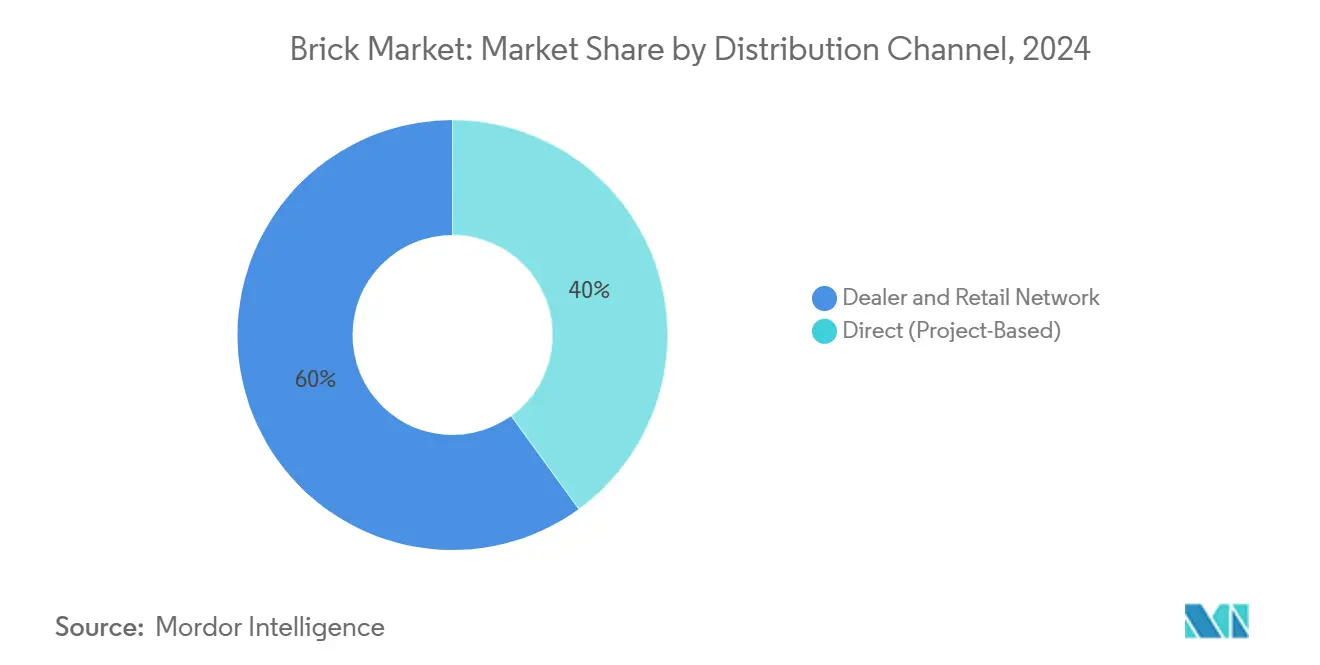
Geography Analysis
Asia-Pacific generated 48% of 2024 global sales and is projected to grow 3.44% annually to 2030, buoyed by record urban migration and transport megaprojects. China and India spearhead masonry consumption as public-sector housing pushes converge with subway, airport, and industrial-park builds. Producers deploy tunnel kilns with waste-heat recovery to meet provincial emission caps and reduce coal dependence, safeguarding supply resiliency during demand spikes.
North America is experiencing growth in market value, driven by pending interest-rate cuts that are unlocking stalled projects. The AIA Consensus Construction Forecast sees non-residential spending rising 2.2% in 2025 and 2.6% in 2026 after a strong 2023-2024 run[2]AIA Economics & Market Research, “January 2025 AIA Consensus Construction Forecast,” aia.org. Fly-ash bricks gain traction among designers chasing LEED points, while thin-brick panels speed up urban multifamily builds. Canada’s colder climate sustains demand for high-thermal-mass clay units in residential retrofits to cut heating loads.
Europe trails in growth but leads innovation as the CBAM exposes carbon-intensive imports and rewards local low-carbon pioneers. The continent imported over 500 million bricks in 2022, generating 288,190 tonnes of CO₂, prompting calls for onshoring greener capacity. Scandinavia’s public-procurement policies stipulate embodied-carbon ceilings, channeling orders toward calcium-silicate or unfired concrete bricks. Eastern Europe builds capacity to serve domestic and German markets facing material tightness.
South America’s brick market pivots on warehouse and logistics developments catalyzed by e-commerce. Brazil accelerates industrial parks along new highways, increasing demand for large-format blocks that reduce lay-rate time. Material suppliers invest in local plants to sidestep currency volatility and import duties. Middle East and Africa, although smaller today, hold the loftiest upside as 70% of buildings required by 2040 are yet to be built. Kenya, Nigeria and Egypt roll out public-private partnerships to deliver affordable homes, embedding brick procurement targets into tender documents to stimulate domestic manufacturing.
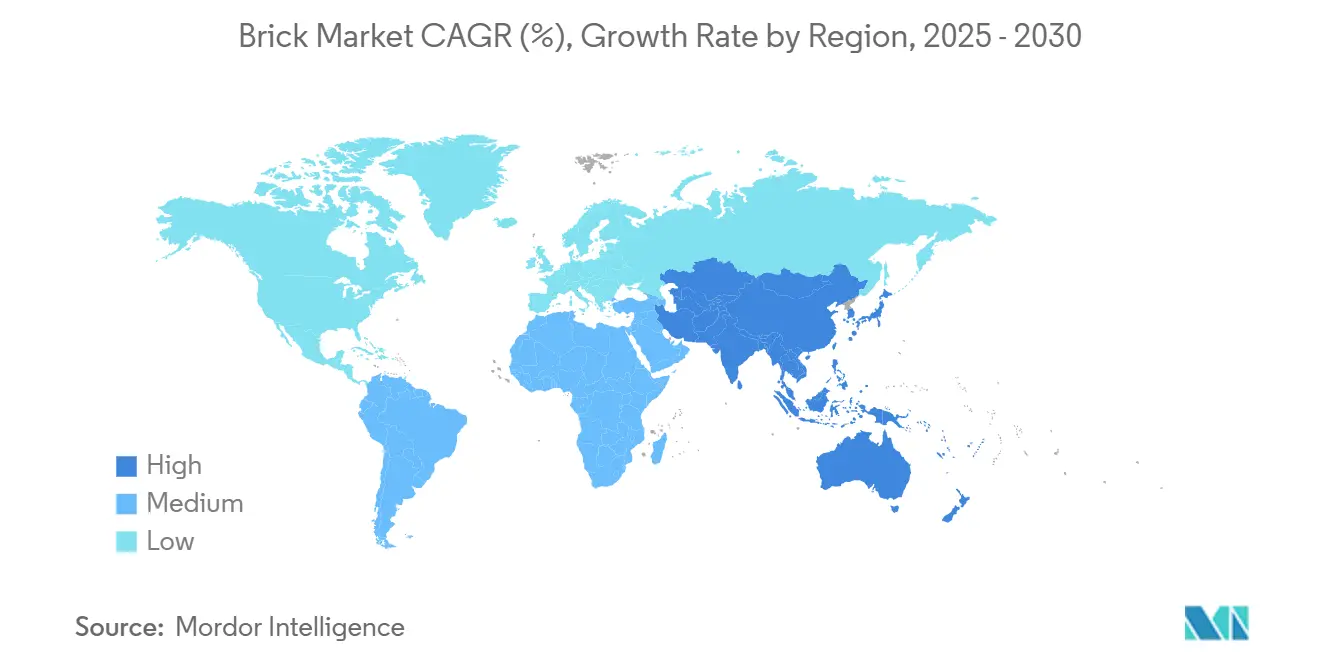
Competitive Landscape
The brick market exhibits highly fragmented concentration at the global level. Wienerberger AG, Acme Brick Company, and Brickworks Ltd headline large-scale rivals, collectively leveraging broad portfolios and high-throughput kilns. Wienerberger posted EUR 2,213 million in H1 2024 revenue, up year on year, and broadened its roofing platform via the Terreal acquisition[3]Heimo Scheuch, “Wienerberger with Solid Half-Year Performance Well-Placed for Market Recovery,” Wienerberger, wienerberger.com .
Strategic moves center on decarbonization, automation, and portfolio balance. Heidelberg Materials applies AI to real-time kiln monitoring, claiming 20% cement-use reductions extendable to masonry units. Oldcastle APG bought Master Block in January 2025 to shore up supply in high-growth Arizona. Forterra’s completion of Europe’s largest brick plant at Desford raises UK capacity and embeds advanced slip-extrusion lines for panelization compatibility.
Niche disruptors spotlight recycled textile or bio-based feedstocks that lower embodied emissions while matching compressive strength standards. Intellectual-property ownership in char-based thin bricks and 3D-printable fly-ash mortar positions start-ups for licensing or joint ventures with incumbents needing rapid ESG upgrades. Consolidators pursue bolt-on buys of regional paver or block makers to secure channel access and reduce last-mile costs, signaling an era of value-chain integration ahead.
Brick Industry Leaders
-
Acme Brick Company
-
Wienerberger AG
-
Brickworks
-
Ibstock Plc.
-
Triangle Brick Co.
- *Disclaimer: Major Players sorted in no particular order

Recent Industry Developments
- August 2024: Oldcastle APG, a subsidiary of CRH, has acquired Master Block, Inc., a concrete block manufacturer located in El Mirage, Arizona, United States. This acquisition strengthens Oldcastle's masonry and fence block production capabilities in the greater Phoenix area.
- December 2024: As of December 2024, Forterra has completed its strategic capital investment program, which included the establishment of Europe's largest brick factory in Desford, the comprehensive redevelopment of the Wilnecote factory, and the implementation of an advanced brick slip extrusion line at the Accrington facility.
Global Brick Market Report Scope
Brick is a type of block used for building walls, pavements and other elements in masonry and building construction. The brick market is segmented by brick type, Application, and geography. By Brick Type, the market is segmented into Clay, Sand Lime, Fly-ash Clay, and Other Brick Types. , The market is segmented by Applications: Buildings, paths, Parterre, and Other Applications. The report also covers the market size and forecasts for the brick market in 15 countries across major regions. For each segment, the market sizing and forecasts have been done on revenue (USD million).
By Brick Type | Clay | ||
Sand Lime | |||
Fly-Ash Clay | |||
Other Brick Types | |||
By Application | Building | ||
Path | |||
Parterre | |||
Other Applications | |||
By End-Use Industry | Residential Buildings | ||
Non-Residential Buildings | |||
By Distribution Channel | Direct (Project-Based) | ||
Dealer and Retail Network | |||
By Geography | Asia-Pacific | China | |
India | |||
Japan | |||
South Korea | |||
Rest of Asia-Pacific | |||
North America | United States | ||
Canada | |||
Mexico | |||
Europe | Germany | ||
United Kingdom | |||
France | |||
Italy | |||
Rest of Europe | |||
South America | Brazil | ||
Argentina | |||
Rest of South America | |||
Middle East and Africa | Saudi Arabia | ||
South Africa | |||
Rest of Middle East and Africa |
Clay |
Sand Lime |
Fly-Ash Clay |
Other Brick Types |
Building |
Path |
Parterre |
Other Applications |
Residential Buildings |
Non-Residential Buildings |
Direct (Project-Based) |
Dealer and Retail Network |
Asia-Pacific | China |
India | |
Japan | |
South Korea | |
Rest of Asia-Pacific | |
North America | United States |
Canada | |
Mexico | |
Europe | Germany |
United Kingdom | |
France | |
Italy | |
Rest of Europe | |
South America | Brazil |
Argentina | |
Rest of South America | |
Middle East and Africa | Saudi Arabia |
South Africa | |
Rest of Middle East and Africa |
Key Questions Answered in the Report
What is the current value of the brick market?
The brick market is valued at USD 1.73 trillion in 2025 and is forecast to reach USD 1.99 trillion by 2030.
Which region contributes the most to brick sales?
Asia-Pacific leads with 48% of global revenue in 2024 and records the fastest 3.44% CAGR through 2030.
Why are fly-ash bricks gaining popularity?
Fly-ash bricks utilize industrial waste and cut firing energy, aligning with green-building codes and helping meet aggressive emissions-reduction targets.
How is modular construction affecting brick demand?
Modular construction favors lightweight hollow bricks designed for prefabricated panels, supporting new demand even as it reduces traditional site-laid volumes.
What is the biggest restraint for European brick producers?
Carbon-tax exposure from the EU ETS and the Carbon Border Adjustment Mechanism raises production costs, pushing firms to adopt low-carbon fuels and efficient kilns.
Which distribution channel is growing fastest for bricks?
Direct project-based procurement is rising at 3.70% CAGR as contractors consolidate orders and rely on digital supply-chain platforms for timely deliveries.
Page last updated on: July 1, 2025