Polyurea Market Size and Share
Polyurea Market Analysis by Mordor Intelligence
The polyurea market stands at USD 1.08 billion in 2025 and is on track to reach USD 1.41 billion by 2030, reflecting a steady 5.48% CAGR over the forecast period. Robust demand stems from infrastructure rehabilitation work, a policy-driven shift toward VOC-free protective coatings, and the technology’s expanding use in electric-vehicle battery safety systems. Continued government spending on bridges, pipelines, and water assets, combined with stricter emission limits, is pushing asset owners to replace slower-curing epoxy or polyurethane systems with fast-return polyurea alternatives. Rising corrosion-control budgets among oil and gas midstream operators, as well as new offshore wind installations, further widen commercial opportunities. Market participants respond through strategic M&A and targeted R&D that improve sustainability credentials, cost positions, and application know-how.
Key Report Takeaways
- By chemical structure, aromatic grades held 66.82% of polyurea market share in 2024; aliphatic grades are set to expand at a 6.04% CAGR through 2030.
- By type, hot polyurea led with 59.25% revenue share in 2024; cold polyurea are projected to grow at 6.55% CAGR to 2030.
- By product form, coatings accounted for 64.62% share of the polyurea market size in 2024, while sealants are advancing at a 7.05% CAGR.
- By end-user industry, construction commanded 40.25% of polyurea market share in 2024; energy and power exhibits the highest forecast CAGR at 7.01% through 2030.
- By geography, North America dominated with 40.82% revenue share in 2024, whereas Asia-Pacific is the fastest-growing region at 7.81% CAGR.
Global Polyurea Market Trends and Insights
Drivers Impact Analysis
Driver | (~) % Impact on CAGR Forecast | Geographic Relevance | Impact Timeline |
---|---|---|---|
Growing demand from infrastructure rehabilitation | +1.20% | North America, Europe | Medium term (2-4 years) |
Surge in corrosion‐control spending by oil & gas midstream operators | +0.80% | Middle East, North America, offshore regions | Short term (≤ 2 years) |
Rapid adoption in EV battery pack protection | +0.90% | Asia-Pacific core, spill-over to North America and Europe | Medium term (2-4 years) |
Mainstream shift from epoxy/polyurethane to faster‐return polyurea coatings | +1.10% | Global industrial markets | Short term (≤ 2 years) |
Regulatory push for VOC-free protective coatings | +0.70% | North America, Europe, widening into Asia-Pacific | Long term (≥ 4 years) |
Source: Mordor Intelligence
Growing Demand from Infrastructure Rehabilitation
Bridge decks, tunnels, and wastewater structures built decades ago are reaching end-of-design life, and owners now favor fast-curing systems that slash lane-closure penalties exceeding USD 25,000 per day in major cities. Polyurea bonds well to damp concrete, resists freeze-thaw cycling, and restores waterproofing without lengthy surface preparation, enabling agencies to reopen traffic within hours. Engineering studies show that polyurea overlays improve flexural toughness and seismic resilience of reinforced-concrete beams in regions such as California and Japan. The USD 1.2 trillion U.S. Infrastructure Investment and Jobs Act allocates significant funds for bridge replacement programs, channeling multi-year demand to qualified applicators. Sika’s 2024 acquisition of Kwik Bond Polymers added bridge-deck polymer expertise, positioning the firm to capture upcoming repair projects. Predictive maintenance models confirm that resealing concrete every 3 years can extend bridge service life by 1–2 years and cut lifecycle expenses by 6%.
Surge in Corrosion-Control Spending by Oil & Gas Midstream Operators
Midstream firms face higher hydrogen-sulfide levels and acidic condensates, accelerating internal corrosion in pipelines and storage tanks. Polyurea’s elastomeric backbone and rapid cure enable thick-film linings that outperform epoxy at elevated temperatures and variable pH. Annual global corrosion damage tops USD 700 billion, and midstream assets account for a disproportionate share, bringing board-level focus to protective-coating performance. New solid-inhibitor packages embedded in gel epoxies further expand dual-system solutions that release corrosion inhibitors on demand. Marine operators consumed 27 million lb of polyurethane and polyurea topcoats in 2023, driven by vessel fuel-efficiency targets that require slick, color-stable hull finishes. Upcoming IMO carbon-intensity rules intensify the search for friction-reducing, low-VOC topcoats.
Mainstream Shift from Epoxy/Polyurethane to Faster-Return Polyurea Coatings
Factory and warehouse managers increasingly treat floor coating downtime as lost revenue. Polyurea solutions can reopen production lines the same day, unlike solvent-borne epoxy systems that may require 48 hours or more. Advanced polyaspartic formulations improve wear resistance and hardness while removing VOCs, complying with limits under the EPA National VOC Emission Standards[1]U.S. Environmental Protection Agency, “National VOC Emission Standards,” epa.gov . Self-healing nano-silica additives extend service intervals and boost return-on-investment for industrial facilities.
Regulatory Push for VOC-Free Protective Coatings
Broader adoption of solvent-free polyurea is driven by tightening rules such as NSF/ANSI/CAN 600 for drinking-water contact materials and the 2024 methylene chloride phase-out under TSCA[2]U.S. Environmental Protection Agency, “Final Rule: Methylene Chloride under TSCA,” usepa.gov . European REACH and upcoming Asian standards mirror these trends, forcing coaters to transition away from high-solvent blends. Bio-oil-based polyurethane technology demonstrates superior thermal stability and reduced corrosion rates, creating a viable route to blend renewable content into polyurea while staying compliant with low-emission targets. Suppliers that certify products to these global benchmarks gain a first-mover edge.
Restraints Impact Analysis
Restraint | (~) % Impact on CAGR Forecast | Geographic Relevance | Impact Timeline |
---|---|---|---|
Volatility in isocyanate & amine feedstock prices | −0.9% | Global, cost-sensitive sectors | Short term (≤ 2 years) |
Short pot-life increases applicator skill/ equipment cost | −0.6% | Higher impact in emerging markets | Medium term (2-4 years) |
Limited recyclability creating end-of-life disposal concerns | −0.4% | Europe, North America, expanding to Asia-Pacific | Long term (≥ 4 years) |
Source: Mordor Intelligence
Short Pot-Life Increases Applicator Skill & Equipment Cost
Spray-grade polyurea can gel in less than 10 seconds, demanding plural-component pumps capable of maintaining strict temperature and pressure windows. Entry-level rigs often cost more than USD 50,000, a hurdle for small contractors in Latin America, Africa, and parts of Southeast Asia. Skilled sprayers command premium wages and must complete certification programs that address proportioning, overlap technique, and troubleshooting. Cold-spray variants reduce upfront spend yet still entail specialized nozzles, moisture scavengers, and meticulous substrate preparation. Training initiatives led by associations such as the Polyurea Development Association help close gaps, but adoption lags in price-sensitive projects.
Limited Recyclability Creating End-of-Life Disposal Concerns
Cross-linked polyurea lacks melt-phase reprocessability, complicating circular-economy targets set by European OEMs and U.S. state procurement guidelines. Research at Aarhus University indicates polyurethane foam recycled through acidolysis can recover 82% of polymer mass, yet extending the method to polyurea remains technically complex[3]Phys.org, “Recycling Polyurethane Foam via Acidolysis,” phys.org . Microwave-assisted aminolysis trims CO₂ emissions by 38%, though industrial scale-up is still several years away. Non-isocyanate polyurethane (NIPU) chemistries promise greater recyclability but currently fall short on cure profile and impact resistance demanded by heavy-duty applications.
Segment Analysis
By Chemical Structure: Aromatic Dominance Faces Aliphatic Innovation
Aromatic materials led the polyurea market with 66.82% revenue share in 2024 on account of lower unit cost and broad supply availability. Major bridge-deck, tank-lining, and secondary-containment specifications still default to aromatic chemistry thanks to proven field durability and familiar processing parameters. However, aliphatic grades are projected to register a 6.04% CAGR as architects and vessel owners require superior color retention, UV stability, and aesthetics for exposed surfaces. Aliphatic producers are investing in bio-based diamine intermediates that trim carbon footprints without impairing cure kinetics. Research on polyaspartic ester inclusion of titania nanoparticles documented up to 28% tensile-strength gains while maintaining VOC-free profiles. Brands able to scale such innovations may erode the price gap against aromatics, shifting value capture toward solution providers rather than bulk monomer suppliers.
Aromatic suppliers are not standing idle. They optimize catalyst packages and introduce hybrid pigment stabilizers to moderate yellowing in outdoor settings. Some highway agencies now accept aromatic coats topped with aliphatic clear-sealers, blending economics and performance. Longer term, the pivot toward fully recyclable non-isocyanate routes could favor aliphatic backbones compatible with dynamic covalent chemistry. Vendors that master drop-in replacements for current hot-spray rigs will unlock accelerated adoption, particularly in regions where green-procurement clauses move from voluntary to mandatory status.
By Type: Hot Spray Systems Drive Volume While Cold Applications Gain Traction
Hot-spray equipment dominates the polyurea market because it enables high-build application rates exceeding 1,000 ft² per hour, a decisive advantage for 200-ft storage tanks or kilometer-scale aqueducts. A single shift can coat a 12,000-barrel frac tank, reducing rental charges for operators. The polyurea market share for hot-spray could slip modestly as smaller projects adopt cold-spray. OEMs continually redesign heated hoses with integrated sensors that self-correct pressure imbalances, lowering warranty claims.
Cold-spray technology is the fastest-growing niche at 6.55% CAGR, propelled by roof restoration, interior containment rooms, and medical-device tooling where overheating could damage substrates. Formulators leverage latent catalysts that activate in ambient humidity, extending open time to two minutes without sacrificing cure completeness. A biocide-resistant cold-spray line launched in 2025 for clean-room trays already booked multi-year contracts with Southeast Asian semiconductor fabs. Although unit pricing remains 8–12% higher than hot-spray, total installed cost becomes attractive once expensive heat-trace systems are removed.
By Product Form: Coatings Leadership Challenged by Sealant Innovation
Coatings represented 64.62% of total revenue in 2024 because they tackle broad substrate classes, from steel to geotextile liners. High-build, 100% solids coatings decrease water absorption in concrete decks by 96%, extending freeze-thaw cycles and limiting chloride ingress. Rapid-cure roof primers within this category let contractors complete full membrane builds in under two days compared with four using acrylic systems.
Sealants, however, chart the highest growth at 7.05% CAGR, leveraging polyurea’s tear strength and rebound to outperform silicones in expansion joints subject to seismic motion. New microencapsulated curing agents allow sealants to self-heal micro-cracks up to 150 µm, doubling average joint life in highway pavements. These features open doors in tunnel linings, stadium joints, and wind-tower flange seals. Lining products, which combine coating and sealing properties, continue making inroads in high-acid chemical sumps, though growth is slower as many petrochemical sites are in maintenance rather than build-out mode.
By End-User Industry: Construction Dominance Meets Energy Sector Acceleration
Construction retained 40.25% of 2024 revenue because governments channel infrastructure stimulus to shovel-ready bridge, rail, and water projects. Concrete repair specialists secure polyurea spot bids by demonstrating traffic-reopen times under three hours versus 24 hours for cementitious overlays, building a strong business case. The polyurea market size tied to construction is projected to advance, mirroring public-spend pipelines across the U.S., Japan, and the European Union. Integrators also package polyurea with fiber-reinforced polymers to retrofit aging parking garages susceptible to salt attack.
The energy and power segment, led by offshore wind and energy-storage installations, achieves a 7.01% CAGR through 2030. Coating towers, transition pieces, and splash-zone structures with polyurea cuts maintenance intervals, a key consideration for turbines located 30 km offshore where access costs are high. Marine asset owners cite 10-year liner warranties offered by suppliers such as Advanced Polymer Coatings for chemical tankers operating in corrosive cargo trades. Industrial plant operators also extend polyurea usage to secondary containment areas mandated under EPA Spill Prevention Control and Countermeasure rules, safeguarding soil and groundwater.
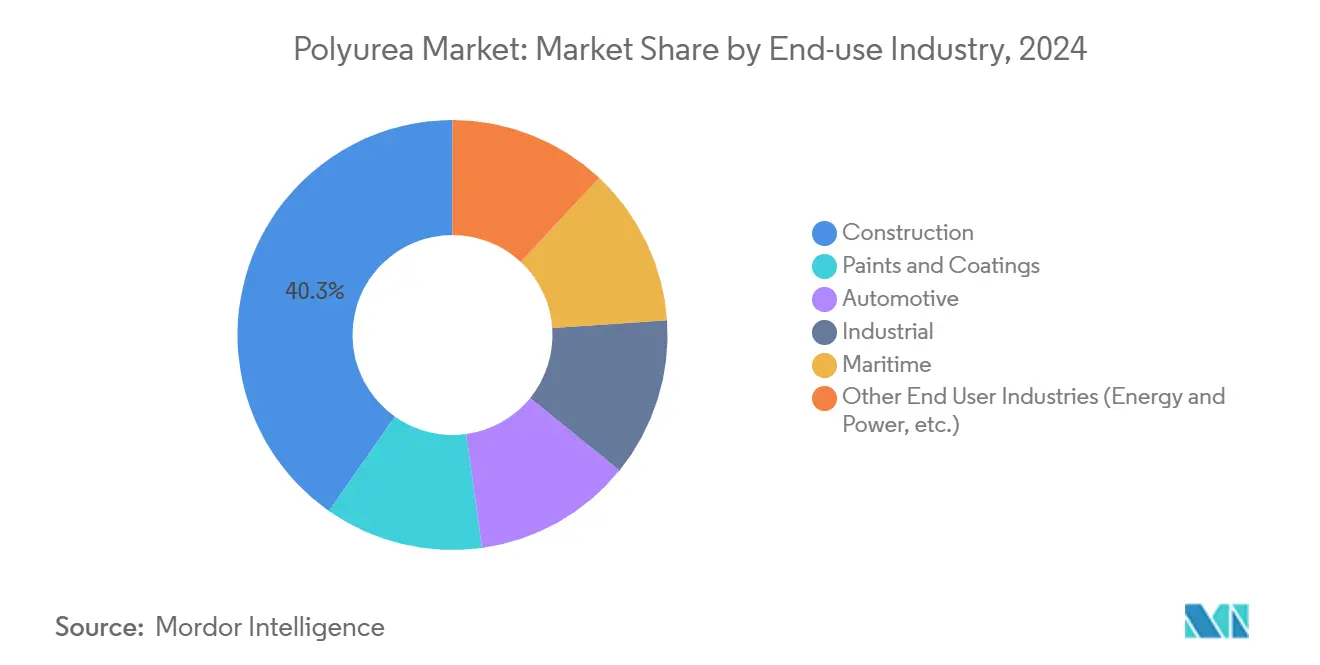
Note: Segment Share of all individual segments available upon report purchase
Geography Analysis
North America led the polyurea market with 40.82% revenue share in 2024 on the back of large rehabilitation budgets, stringent VOC rules, and an established network of trained applicators. Public-private partnerships fund multi-year water, bridge, and airport modernizations that favor rapid-cure solutions. Mexico’s production of polyurethane intermediates, buoyed by Tesla’s gigafactory in Nuevo León, improves regional feedstock security and shortens lead times for U.S. job sites. Canadian oil-sands operators adopt polyurea for tailings-pond liners, citing reduced liner-seam failure against cyclic freeze-thaw.
Asia-Pacific is the fastest-growing region at 7.81% CAGR. China’s Belt and Road-linked investments require durable coatings for cross-border rail and pipeline corridors. India’s Smart Cities Mission allocates funds to multi-level parking decks and bus terminals that seek low-downtime flooring systems. Indonesia’s coatings market highlights eco-friendly formulations and polyurea standards discussed at the 2024 ASEAN Coating Innovation conference. South Korean shipyards specify aliphatic topsides for LNG carriers to comply with strict discoloration limits during Arctic passages.
Europe, the Middle East, and Africa display mixed trajectories. Western Europe pivots toward bio-based chemistries and recyclability, slowing total volume but increasing unit value. Middle Eastern refineries and new hydrogen cracker complexes drive protective-lining demand that withstands higher chloride content in crude. African markets embrace polyurea for potable-water tanks under donor-funded rural supply projects. South America grows steadily as Brazilian highway operators deploy joint sealants to extend pavement life in high-axle-load corridors, although macroeconomic swings create procurement volatility.
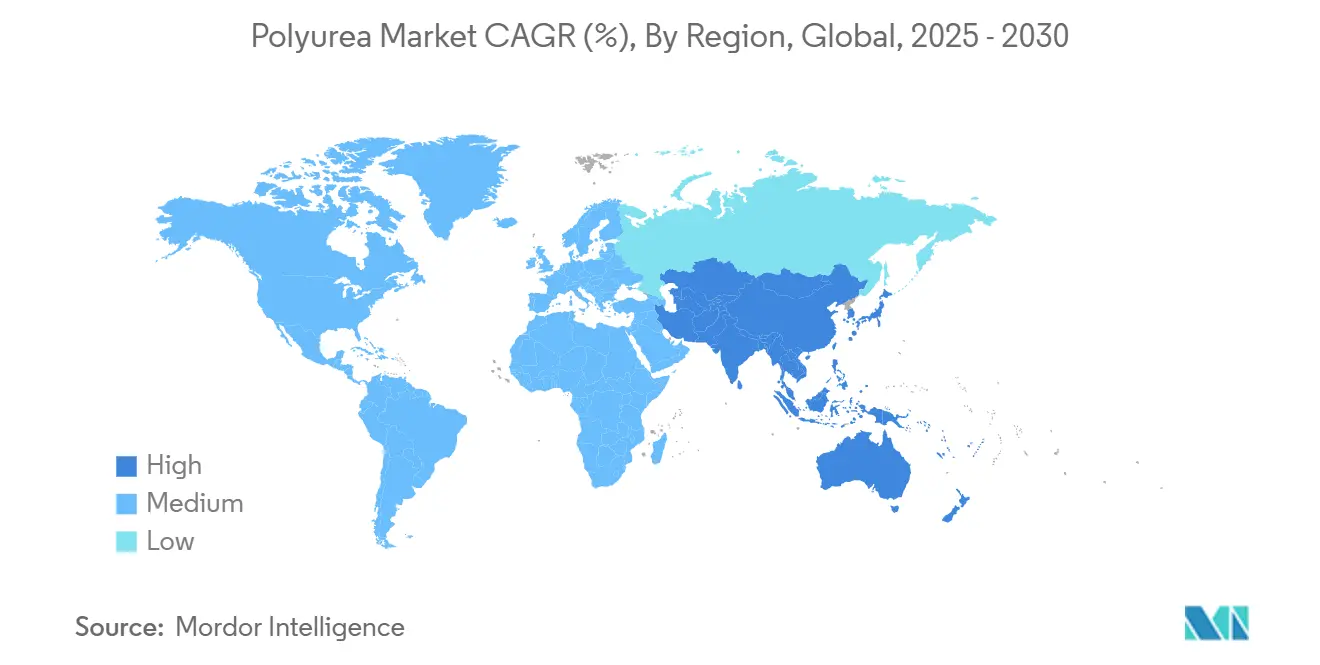
Competitive Landscape
The industry remains moderately fragmented. BASF, Huntsman, and Covestro maintain technology and upstream integration advantages, but mid-tier specialists thrive on application knowledge and quick product customization. LANXESS divested its Urethane Systems business to UBE Corporation for EUR 460 million in 2024 to streamline its portfolio and unlock synergies for the acquirer’s Asian growth strategy. BASF entrusted Univar Solutions with exclusive North American distribution rights for its Baxxodur amine curing agents, widening formulators’ access to blend components vital for high-performance polyurea.
Sustainability-driven white spaces encourage collaboration between chemical majors and carbon-utilization start-ups. HB Fuller partnered with Aether Industries to commercialize polyols containing up to 40% CO₂, improving cradle-to-gate emission profiles without modifying existing spray rigs. Research institutes progress on self-healing top-coats that micro-encapsulate isocyanate monomers, enabling autonomous repair after hail strikes or mechanical abrasion. Market entrants differentiate through niche verticals such as EV battery shielding, where established coating suppliers lack focused test-data sets. Long-term winners will combine chemistry innovation with field-service support, supplying certified applicator-training modules and predictive-analytics dashboards that document coating performance.
Polyurea Industry Leaders
-
BASF SE
-
Huntsman International LLC
-
PPG Industries Inc.
-
Covestro AG
-
The Sherwin-Williams Company
- *Disclaimer: Major Players sorted in no particular order
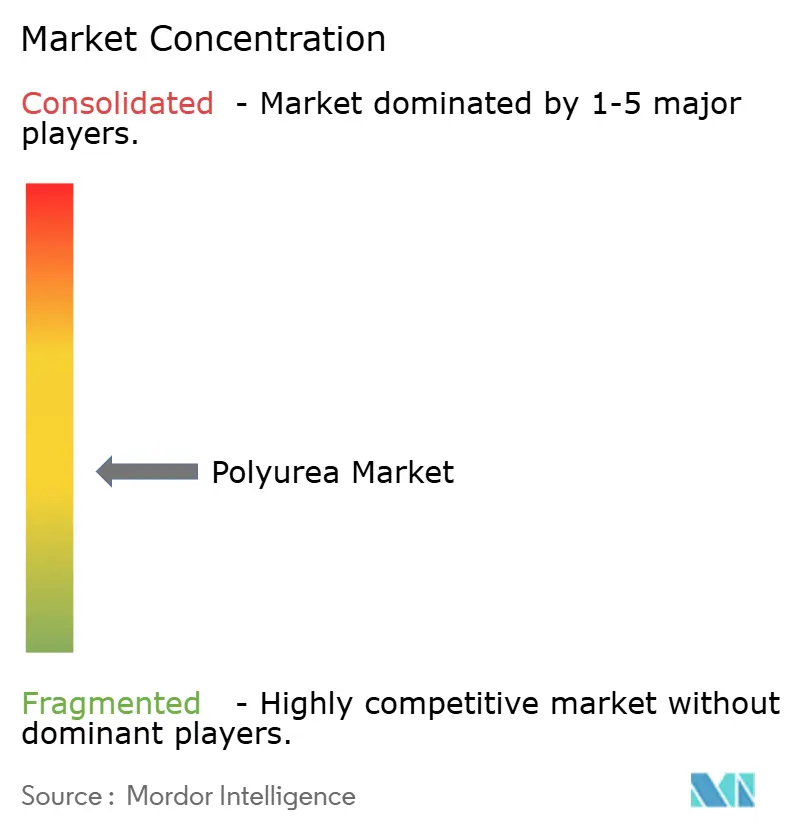
Recent Industry Developments
- September 2024: Univar Solutions, LLC has expanded its partnership with BASF to distribute the full range of Baxxodur amine-based curing agents in the U.S. and Canada. This provides North American customers access to BASF's complete portfolio of curing and accelerating agents, essential for enhancing polyurea systems and more.
- September 2024: At Simac Tanning Tech, BASF introduced advanced concepts and recycling methods for polyurethanes. Under the theme ‘Make the Move,’ BASF showcased materials and technologies designed to manufacture shoes that are lighter, more comfortable, and highly durable.
Global Polyurea Market Report Scope
Polyurea is a synthetic polymer derived from the reaction of a diamine with a diisocyanate. Polyurea offers rapid curing time and high strength, which makes it useful in a wide range of industrial and commercial applications, such as construction waterproofing, industrial flooring, coatings for truck beds, tank linings, etc. Further, polyurea is also used as a sealant and insulation material.
The polyurea market is segmented by chemical structure, type, product, end-user, and geography. By chemical structure, the market is segmented into aromatic and aliphatic. By type, the market is segmented into hot polyurea and cold polyurea. By product, the market is segmented into lining, coating, and sealant. By end-user industry, the market is segmented into construction, paints and coating, automotive, industrial, marine, and others (transportation, etc.). The report also covers the market size and forecasts for the market in 15 countries across the globe.
For each segment, the market sizing and forecasts have been done on the basis of value (USD).
By Chemical Structure | Aromatic | ||
Aliphatic | |||
By Type | Hot Polyurea | ||
Cold Polyurea | |||
By Product Form | Coatings | ||
Linings | |||
Sealants | |||
By End-use Industry | Construction | ||
Paints and Coatings | |||
Automotive | |||
Industrial | |||
Maritime | |||
Other End User Industries (Energy and Power, etc.) | |||
By Geography | Asia-Pacific | China | |
Japan | |||
India | |||
South Korea | |||
Rest of Asia-Pacific | |||
North America | United States | ||
Canada | |||
Mexico | |||
Europe | Germany | ||
United Kingdom | |||
France | |||
Italy | |||
Rest of Europe | |||
South America | Brazil | ||
Argentina | |||
Rest of South America | |||
Middle East and Africa | Saudi Arabia | ||
South Africa | |||
Rest of Middle East and Africa |
Aromatic |
Aliphatic |
Hot Polyurea |
Cold Polyurea |
Coatings |
Linings |
Sealants |
Construction |
Paints and Coatings |
Automotive |
Industrial |
Maritime |
Other End User Industries (Energy and Power, etc.) |
Asia-Pacific | China |
Japan | |
India | |
South Korea | |
Rest of Asia-Pacific | |
North America | United States |
Canada | |
Mexico | |
Europe | Germany |
United Kingdom | |
France | |
Italy | |
Rest of Europe | |
South America | Brazil |
Argentina | |
Rest of South America | |
Middle East and Africa | Saudi Arabia |
South Africa | |
Rest of Middle East and Africa |
Key Questions Answered in the Report
What is the current size of the polyurea market?
The polyurea market stands at USD 1.08 billion in 2025 and is projected to reach USD 1.41 billion by 2030.
Which region leads the polyurea market in revenue?
North America holds the largest share at 40.82% thanks to strong infrastructure spending and strict environmental rules.
What segment is growing fastest within the polyurea market?
Sealants are the fastest-growing product form segment, advancing at a 7.05% CAGR through 2030.
Why is polyurea preferred for infrastructure rehabilitation?
Its rapid cure, superior adhesion, and long-term durability enable bridge or tunnel reopening within hours, cutting downtime costs dramatically.
How are regulations influencing polyurea demand?
Global VOC-reduction policies and drinking-water safety standards favor solvent-free polyurea formulations that comply without sacrificing performance.
What are the primary challenges facing polyurea adoption?
Feedstock price volatility, the need for skilled applicators with specialized equipment, and limited recyclability remain key hurdles.
Page last updated on: June 25, 2025