Intumescent Coatings Market Size and Share
Intumescent Coatings Market Analysis by Mordor Intelligence
The Intumescent Coatings Market size is estimated at USD 1.36 billion in 2025, and is expected to reach USD 1.67 billion by 2030, at a CAGR of 4.14% during the forecast period (2025-2030). Adoption is anchored in stricter global fire-safety standards, a decisive shift toward greener building materials and the desire to keep structural steel visible without compromising protection. Demand increases are incremental rather than explosive, a pattern that hints at resilience built on code compliance cycles instead of speculative construction booms. Water-based chemistries already generate 40% of revenue, and regulatory limits on volatile organic compounds suggest this share will keep rising as specifiers prefer low-odor solutions. The growing preference for proactive fire-risk mitigation in high-density cities, offshore energy hubs and modular factories points to broad use cases that value thin films which expand into an insulating char when exposed to heat. Parallel innovation around durability, faster cure and lower applied thickness is extending product life, so revenue growth increasingly reflects a higher lifetime value per square foot rather than pure volume gains in the Intumescent coatings market.
Key Report Takeaways
- By application, cellulosic coatings led with 53% of the Intumescent coatings market share in 2024 while hydrocarbon-rated products are forecast to expand at a 5.1% CAGR through 2030.
- By technology, water-based systems captured 40% of 2024 revenue and are set to grow at a 5.4% pace, outstripping solvent-borne alternatives.
- By resin type, epoxy platforms held 49% share of the Intumescent coatings market size in 2024; acrylic grades are set to close the gap with the fastest growth rate among traditional chemistries.
- By end-user industry, oil and gas operations accounted for 44.2% of the Intumescent coatings market size in 2024 and remain the primary revenue contributor.
- By geography, Asia Pacific generated 35% of global revenue in 2024 and is advancing at a market-leading 5.8% CAGR to 2030.
Global Intumescent Coatings Market Trends and Insights
Driver Impact Analysis
Driver | (~) % Impact on CAGR Forecast | Geographic Relevance | Impact Timeline |
---|---|---|---|
Accelerated high-rise fire codes | +1.2% | Asia Pacific, spillover Middle East | Medium term (2-4 years) |
Growth in oil and gas exploration | +0.9% | Global, focus North America & Middle East | Short term (≤ 2 years) |
EU low-VOC mandate | +1.3% | Europe, global manufacturing | Medium term (2-4 years) |
Modular off-site fabrication | +0.7% | North America, emerging Europe | Medium term (2-4 years) |
Shift toward environmentally friendly lines | +0.8% | Global, strongest in Europe & North America | Long term (≥ 4 years) |
Source: Mordor Intelligence
Accelerated High-Rise Fire Codes in Asia Pacific
New requirements for towers above 24 m make thin-film coatings nearly mandatory, giving developers products that deliver two-hour protection without adding structural weight. Certification regimes in China and India reward third-party testing, raising entry hurdles and giving early movers an edge. The Intumescent coatings market therefore enjoys a structural boost as skyline density grows and evacuation windows tighten. Suppliers that align product labels with local codes enter bid lists more easily, and approvals granted now often span multiple project phases, improving revenue visibility.
Growth in Oil and Gas Exploration Activities
Hydrocarbon-specialized products held 44.2% share in 2024 because offshore topsides, LNG plants and refineries must manage pool-fire temperatures above 1,100 °C. Shale-linked construction across North America keeps fabrication yards busy, sustaining a steady order flow of epoxy intumescent films. Contractors that bundle supply with installation achieve greater margin retention as operators value single-contract accountability. Once a coating wins protocol testing like UL 1709 it tends to remain on specification lists for years, supporting recurring income streams in the Intumescent coatings market.
EU Low-VOC Mandate Boosting Water-Borne Formulations
The European Union Paints Directive imposed tight VOC caps that accelerated R&D in acrylic and alkyd emulsions[1]Eur-Lex, “Directive 2004/42/EC on the limitation of VOCs,” eur-lex.europa.eu . Performance gaps versus solvent systems are narrowing and specifiers increasingly score embodied carbon alongside fire rating, shifting contract awards toward sustainability metrics. Smaller producers must either invest in water-based development or license technology, raising the competitive barrier and consolidating share among innovators.
Modular Off-Site Steel Fabrication in North America
Factory-built floor plates and wall panels are coated indoors, moved by crane and bolted on site, demanding a coating film that survives mechanical handling. High-build epoxy intumescent primers that cure quickly allow modules to be stacked within hours, shortening assembly schedules and elevating monthly consumption volumes. Faster cure cycles feed into faster plant throughput, creating a reinforcing loop that lifts demand in the Intumescent coatings market.
Restraint Impact Analysis
Restraint | (~) % Impact on CAGR Forecast | Geographic Relevance | Impact Timeline |
---|---|---|---|
Epoxy resin price volatility | −0.8% | Global, highest impact Asia Pacific | Short term (≤ 2 years) |
High cost of intumescent coatings | −1.1% | South America & parts of Asia | Medium term (2-4 years) |
Competition from alternative methods | −0.6% | Mature markets worldwide | Long term (≥ 4 years) |
Source: Mordor Intelligence
Epoxy Resin Price Volatility
Fluctuations in raw material costs squeeze margins, especially for Asian producers that buy spot cargoes. Multi-year supply contracts provide partial insulation yet cannot eliminate exposure when feedstock prices spike quickly. Budget overruns may delay project starts or trigger product substitution where standards allow, temporarily slowing growth in the Intumescent coatings market.
High Cost of Intumescent Coatings
Thin-film fire-proofing remains pricier than bulkier board systems. In value-sensitive regions such as parts of South America, the initial outlay discourages adoption, even when operating savings justify the premium over the life cycle. Projects with tight financing may revert to cheaper alternatives, putting a brake on penetration rates.
Segment Analysis
By Application: Divergence Between Cellulosic and Hydrocarbon Needs
Cellulosic coatings accounted for 53% of 2024 revenue equal to USD 667.8 million and continue to dominate because large volumes of commercial and residential steel require protection against slow-burn fires. Their relatively lower price broadens accessibility for mid-rise projects, so regulatory enforcement is not the sole driver. Architects see a clear cost-to-benefit ratio that supports repeat use, implying resilient baseline demand even if hydrocarbon volumes escalate faster. In contrast, hydrocarbon-rated lines generated USD 349 million yet are forecast to outpace the headline market with a 5.1% CAGR to 2030. These products must survive jet-fire and pool-fire testing, and once an EPC firm qualifies a brand it rarely changes mid-project. That stickiness locks in extended maintenance work, creating predictable after-sales income. The hydrocarbon subset therefore raises revenue per contract even if tonnage remains lower, reinforcing value concentration within the Intumescent coatings market.
The stronger growth rate in hydrocarbon films ties directly to new FPSO units, LNG export trains and refining upgrades in the Gulf Coast and Middle East. Offshore assets demand coatings that adhere under thermal shock, so epoxy systems remain the default platform. The Intumescent coatings market size for hydrocarbon applications is projected to climb as national energy strategies focus on downstream self-sufficiency. Cellulosic lines, meanwhile, keep pace with densifying cities where exposed steel delivers modern aesthetics. Together, the two fire scenarios carve distinct paths, but each strengthens overall penetration because they address separate safety imperatives rather than competing for the same square footage.
By Technology: Water-Based Systems Accelerate Environmental Transition
Water-borne solutions held 40% of 2024 revenue and are advancing at a 5.4% CAGR, leading the push toward low-VOC construction practices. Their absence of strong odor permits coating while tenants remain in place, a practical gain that simplifies refurbishment logistics. Building owners thus minimize downtime costs, an overlooked yet significant driver of repeat purchasing. Solvent-based and hybrid epoxy chemistries still account for the balance, favored where rapid cure at low temperature is mandatory, particularly offshore or in cold climates. Even so, suppliers tweak solvent blends to push VOC levels below future regulatory thresholds, signaling an evolutionary rather than abrupt phase-out.
As regulatory ceilings tighten, specifiers benchmark technologies not only on fire endurance but also on embodied carbon. Water-based films score well on both counts, encouraging project engineers to switch from older solvent types. The Intumescent coatings market size is expected to be increasingly influenced by lifecycle assessments that reward low emissions from manufacturing through application. Hybrid epoxies retain altitude by offering mechanical robustness plus improved environmental scores, illustrating a gradual convergence of performance and sustainability objectives.
By Resin Type: Epoxy Dominance Faces Multifaceted Challenges
Epoxy resins captured 49% share, equal to USD 617.4 million, by delivering superior mechanical strength and chemical resistance. Producers mitigate resin volatility through multi-year contracts, thereby smoothing cost swings that could otherwise erode margins. Acrylic systems occupy second position, thriving in mainstream building projects that prize a balance of price, dry-time and aesthetics. Polyurethane and alkyd lines serve niche roles such as façade panels where UV stability is critical. Emerging hybrids that graft acrylic modifiers onto epoxy backbones aim to merge durability with faster curing, showing that formulation boundaries are blurring to extend performance per gram.
Intumescent coatings market dynamics around resin choices increasingly weigh sustainability. Epoxy feedstocks rely on petrochemical inputs, prompting R&D into bio-based epoxies or partial biomass content. Acrylic pathways align well with water-borne dispersion, strengthening their medium-term growth prospects. Contractual hedging alone cannot suppress long-term volatility, so resin diversification becomes an operational hedge as well as a marketing narrative centered on green chemistry.
By End-User Industry: Oil and Gas Anchors Revenue Base
Oil and gas applications represented 44.2% of global demand worth USD 556.9 million in 2024. Offshore platforms and onshore terminals specify hydrocarbon-tested coatings conforming to UL 1709 or ISO 22899. These layers integrate into larger asset-integrity budgets where safety compliance overrides discretionary cuts, so short swings in crude prices have muted impact on procurement. Scheduled turnarounds bundle inspection, blast-clean and re-coat cycles, embedding a steady aftermarket that stabilizes year-to-year revenue in the Intumescent coatings market.
Construction contributes a smaller but faster-growing share at 4.91% CAGR. Urban skylines that showcase exposed steel drive aesthetical selection, while lightweight char layers avoid thick gypsum boards. Manufacturers respond with broader color ranges and clear coats that keep natural steel visible. Electrification trends in automotive and rail sectors create exploratory use cases for battery compartment safety. Although volumes are modest, the technical demands push suppliers to adapt existing formulations, planting seeds for adjacent growth inside the wider Intumescent coatings industry.
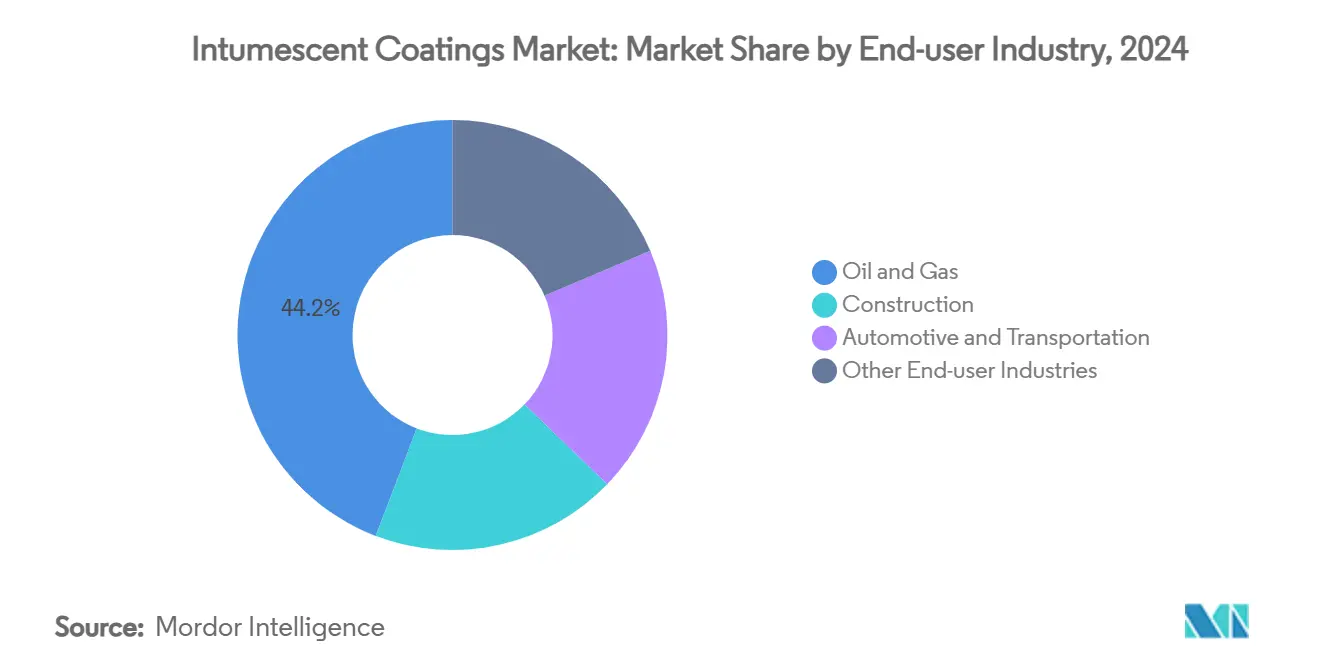
Note: Segment shares of all individual segments available upon report purchase
Geography Analysis
Asia Pacific generated USD 441 million or 35% of global revenue in 2024 and is forecast to climb at 5.8% CAGR through 2030. China enforces dual goals of high-rise safety and petrochemical self-reliance, underpinning steady volume in both cellulosic and hydrocarbon categories. India’s Smart Cities program embeds passive fire protection into municipal tender checklists, effectively making intumescent supply a prerequisite for state-funded towers. Producers that localize factories in the region mitigate exchange-rate risk and capture tax incentives that favor domestic manufacturing.
North America remains a core pillar of the Intumescent coatings market. The shale play drives fresh LNG and pipeline assets while an aging bridge stock invites intumescent retrofits referenced in FHWA guidelines. Supply chains hedged in USD reduce currency exposure, and broad field-service networks enable rapid inspection and remedial work that offset raw-material swings. Modular construction adds a new demand layer, since factory spraying compresses build schedules.
Europe demonstrates strong regulatory pull derived from the Paints Directive, which rewards water-borne innovations[2]European Commission, “Paints Directive VOC Limits,” ec.europa.eu . German and Scandinavian green-building labels amplify demand by linking procurement to embodied carbon scoring. Funding under the European Green Deal subsidizes pilot lines for lignin-based additives, encouraging suppliers to test bio-based routes inside regional labs. As a result, Europe often becomes the first adopter of low-carbon grades that later scale globally, further shaping the competitive direction of the Intumescent coatings market.
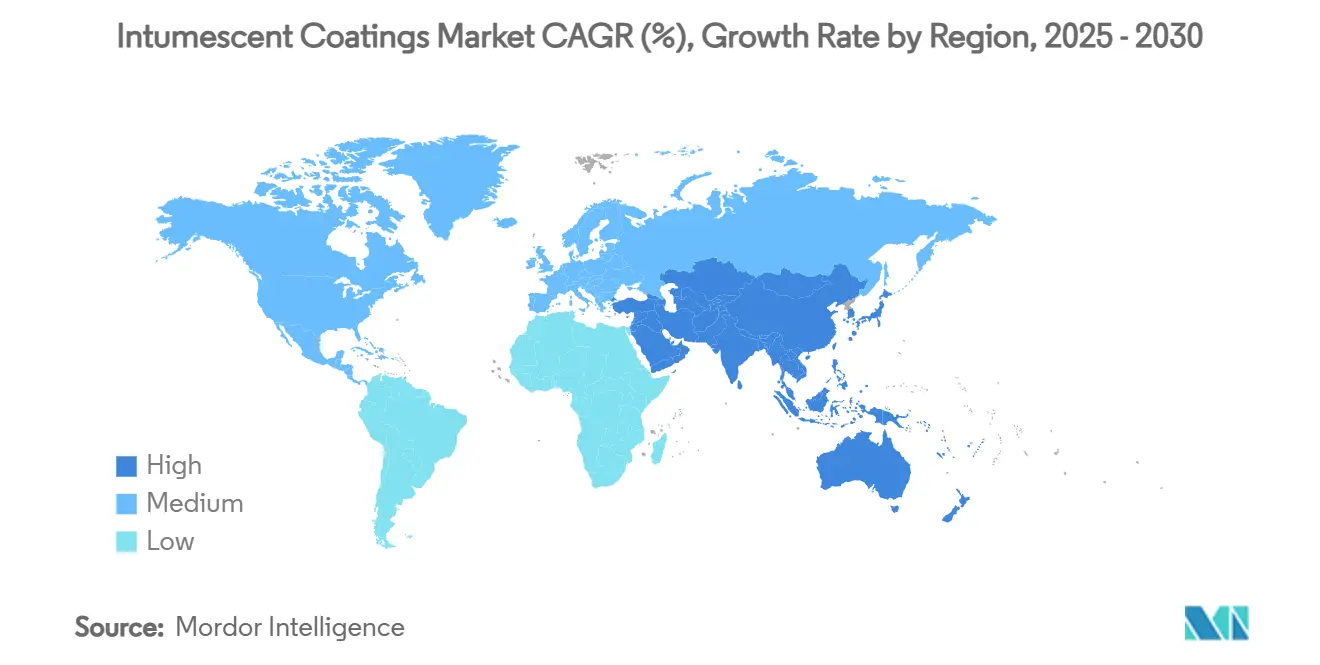
Competitive Landscape
The intumescent coating market is fragmented, with over 200 regional formulators competing for project-specific opportunities. Multinational companies leverage global technical-service teams and bundled agreements with EPC firms, creating barriers for smaller players. Patents on phosphorus-based catalysts and slow-release additives protect market positions, especially in critical infrastructure projects requiring proven chemistry and long warranties. Mid-tier and local producers differentiate through customized tinting, faster lead times, and local certification expertise. In Southeast Asia, logistics agility often outweighs global brand recognition, driving mergers focused on warehousing and distribution synergies. Competition is fierce in water-borne lines, where narrowing technology gaps and price sensitivity push suppliers to innovate with faster dry-times, extended pot life, and robotic spray compatibility. Strategic additive partnerships, involving pigment and flame-retardant specialists, are vital for optimizing thinner film expansion, strengthening vertical collaboration across the intumescent coatings market value chain.
Intumescent Coatings Industry Leaders
-
Jotun
-
The Sherwin-Williams Company
-
PPG Industries Inc.
-
Hempel A/S
-
Akzo Nobel N.V.
- *Disclaimer: Major Players sorted in no particular order
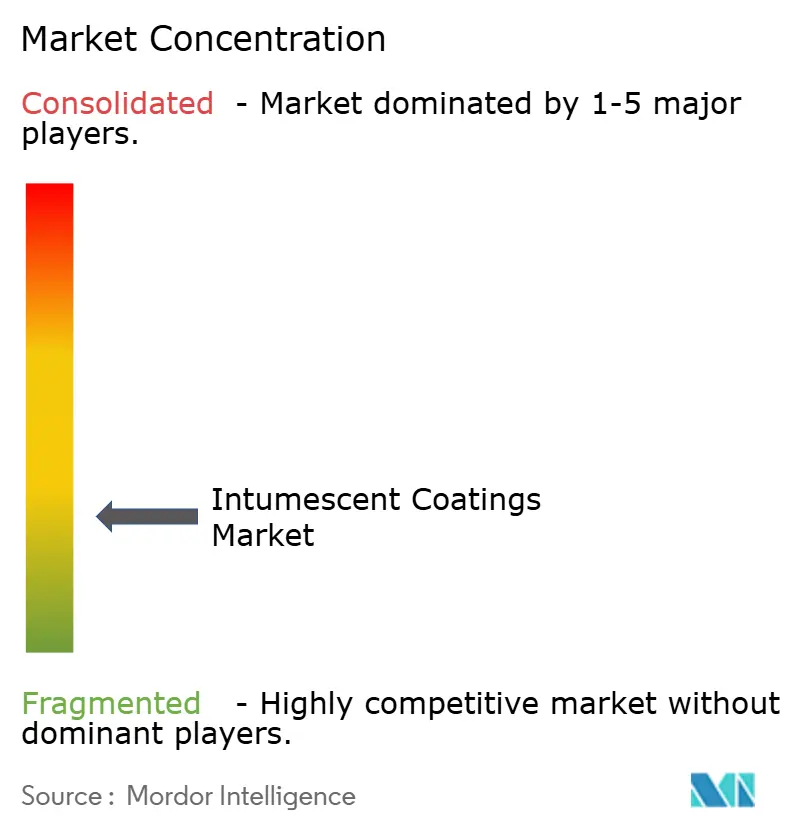
Recent Industry Developments
- July 2024: Hexion Inc. and Clariant partnered to develop advanced intumescent coatings, combining Hexion's VeoVa vinyl ester-based binders with Clariant's additives to enhance fire protection systems. These coatings form insulating foam during fires, preserving structural integrity and providing critical evacuation time.
- February 2023: PPG Industries, Inc. launched PPG STEELGUARD 951, an epoxy intumescent fire protection coating offering up to three hours of fire resistance, corrosion protection in ISO 12944 C5 environments, and rapid curing. It combines durability, edge retention, and compliance with global fire and corrosion standards for modern architectural steel applications.
Global Intumescent Coatings Market Report Scope
The intumescent coating layer expands and produces a 'char,' which insulates the material inside from flames by cutting off the oxygen necessary for combustion. Due to these properties, intumescent is used as a coating material to protect substances from heat and fire damage. The intumescent coatings market is segmented by application, end-user industry, and geography. By application, the market is segmented into cellulosic and hydrocarbon. The market is segmented by the end-user industry into construction, automotive and other transportation, oil and gas, and other end-user industries. The report also covers the market size and forecast for the intumescent coatings market in 16 countries across major regions. For each segment, the market sizing and forecast have been done based on volume (tons).
By Application | Cellulosic | ||
Hydrocarbon | |||
By Technology | Solvent-Based | ||
Water-Based | |||
Epoxy Based | |||
By Resin Type | Epoxy | ||
Acrylic | |||
Polyurethane | |||
Alkyd | |||
Other Resins | |||
By End-user Industry | Construction | ||
Oil and Gas | |||
Automotive and Transportation | |||
Other End-user Industries | |||
By Geography | Asia-Pacific | China | |
India | |||
Japan | |||
South Korea | |||
Rest of Asia-Pacific | |||
North America | United States | ||
Canada | |||
Mexico | |||
Europe | Germany | ||
United Kingdom | |||
France | |||
Italy | |||
Russia | |||
Rest of Europe | |||
South America | Brazil | ||
Argentina | |||
Rest of South America | |||
Middle East and Africa | Saudi Arabia | ||
South Africa | |||
Rest of Middle East and Africa |
Cellulosic |
Hydrocarbon |
Solvent-Based |
Water-Based |
Epoxy Based |
Epoxy |
Acrylic |
Polyurethane |
Alkyd |
Other Resins |
Construction |
Oil and Gas |
Automotive and Transportation |
Other End-user Industries |
Asia-Pacific | China |
India | |
Japan | |
South Korea | |
Rest of Asia-Pacific | |
North America | United States |
Canada | |
Mexico | |
Europe | Germany |
United Kingdom | |
France | |
Italy | |
Russia | |
Rest of Europe | |
South America | Brazil |
Argentina | |
Rest of South America | |
Middle East and Africa | Saudi Arabia |
South Africa | |
Rest of Middle East and Africa |
Key Questions Answered in the Report
What is the projected Intumescent coatings market size by 2030?
The market is forecast to reach USD 1.67 billion by 2030 under a 4.14% CAGR trajectory.
Which region is expected to post the fastest growth in the Intumescent coatings market?
Asia Pacific shows the strongest expansion with a 5.8% CAGR through 2030, driven by stricter high-rise fire codes and continued industrial investment.
Why are water-based intumescent coatings gaining popularity?
They meet low-VOC regulations, emit minimal odor during application and increasingly match solvent-based performance on durability and fire rating.
How do hydrocarbon and cellulosic coatings differ?
Hydrocarbon variants withstand rapid temperature escalation typical of petrochemical fires, whereas cellulosic coatings target slower-burning structural fires common in buildings.
Page last updated on: July 7, 2025