Heat Resistant Polymer Market Size and Share
Heat Resistant Polymer Market Analysis by Mordor Intelligence
The Heat Resistant Polymer Market size is estimated at USD 13.24 million in 2025, and is expected to reach USD 17.92 million by 2030, at a CAGR of 6.24% during the forecast period (2025-2030). Demand is propelled by electrified mobility, miniaturised electronics, and the aerospace shift toward lighter yet stronger structures, each application relying on materials that withstand heat, chemicals, and mechanical stress. Suppliers are rapidly commercialising PFAS-free chemistries to stay ahead of regulatory bans, while additive manufacturing opens new routes for complex spares and customised medical parts. Asia-Pacific retains volume leadership, North America drives technology adoption, and Europe shapes sustainability standards, together steering the Heat Resistant Polymer market toward steady, innovation-led growth. Competitive intensity remains moderate; portfolio divestments by large incumbents are reshaping participation even as niche specialists secure share in emerging applications.
Key Report Takeaways
- By type, fluoropolymers led with 35.18% of Heat Resistant Polymer market share in 2024, while Polyether-ether-ketone (PEEK) is projected to expand at a 7.82% CAGR through 2030.
- By end-user industry, the automotive segment commanded 42.67% of the Heat Resistant Polymer market size in 2024 and is expected to grow 7.91% annually to 2030.
- By geography, Asia-Pacific held 53.18% of the Heat Resistant Polymer market share in 2024 and is set to post a 7.56% CAGR between 2025-2030.
Global Heat Resistant Polymer Market Trends and Insights
Drivers Impact Analysis
Driver | (~) % Impact on CAGR Forecast | Geographic Relevance | Impact Timeline |
---|---|---|---|
High Demand in Aerospace & Automotive Components | +1.8% | North America & Asia-Pacific | Medium term (2-4 years) |
Superior Protection for Miniaturised Electrical Assemblies | +1.2% | Asia-Pacific core; spill-over to North America & EU | Short term (≤ 2 years) |
Surge in EV-fast-charger Power Electronics Adoption | +1.5% | China, EU, North America | Medium term (2-4 years) |
Additive-manufactured Spares for Next-gen Aircraft Engines | +0.9% | North America & EU, expanding to Asia-Pacific | Long term (≥ 4 years) |
Regulatory Tail-winds for Per- and polyfluoroalkyl Substances (PFAS)-free High-heat Polymers | +0.4% | Europe & North America, expanding globally | Long term (≥ 4 years) |
Source: Mordor Intelligence
High Demand in Aerospace & Automotive Components
Aircraft builders are accelerating the shift from metal to continuous-fiber thermoplastic composites, enabling faster assembly rates without compromising fatigue performance. Airbus and Boeing target monthly output exceeding 100 single-aisle jets, relying heavily on Polyether-ether-ketone (PEEK) and Polyphenylene Sulfide (PPS) structures for weight savings and production efficiency [1]Airbus, “Monthly Production Rate Guidance for A320 Family,” airbus.com. Electric-vehicle battery housings now integrate carbon-fiber-reinforced Polyether-ether-ketone (PEEK) that delivers 50% weight reduction and precise dimensional tolerance, helping Original Equipment Manufacturers (OEMs) extend driving range. Original Equipment Manufacturer (OEM) qualification pipelines also include bio-derived variants, signalling future supply diversification. Robust procurement pipelines across both sectors sustain baseline growth for the Heat Resistant Polymer market.
Superior Protection for Miniaturised Electrical Assemblies
Advanced polyimides combine thermal endurance above 400°C with copper-matched expansion, enabling fine-line circuitry in AI servers and 5G base stations. DuPont’s Circuposit SAP8000 plating chemistry and Microfill SFP-II-M copper fill pair with these films to prevent via voids under high current densities. Semiconductor fabs, meanwhile, pivot away from Per- and polyfluoroalkyl Substances (PFAS) processing aids; research groups report dielectric-constant cuts below 3.0 in fluorine-free polyimide layers, holding promise for faster chip interconnects. Flexible Organic Light Emitting Diode (OLED) displays also benefit from crack-resistant polyimide cover films that survive thousands of folding cycles. These attributes anchor continual material substitution within the Heat Resistant Polymer market.
Surge in EV-fast-charger Power Electronics Adoption
Ultra-fast roadside chargers expose plastic housings to surface temperatures above 115°C and continuous voltages near 1,000 V. Covestro’s Makrolon TC polycarbonate lowers hotspot temperature by 12°C in a 350 kW module, eliminating forced-air cooling. Celanese has commercialised Polyphenylene Sulfide (PPS) and High-Temperature Nylon (HTN) grades that combine V-0 flammability with comparative tracking indices above 600 V, ideal for power couplers. With regulators mandating network uptime standards of 98%, operators specify resins rated for 10,000-hour thermal ageing. These requirements reinforce double-digit volume growth of Heat Resistant Polymer in charging hardware through 2030.
Additive-manufactured Spares for Next-gen Aircraft Engines
NASA’s HiCAM initiative validates out-of-autoclave PEEK composites, targeting a six-fold build-rate boost for airframe ribs [2]NASA, “HiCAM: High-Rate Composite Aircraft Manufacturing,” nasa.gov. Victrex’s AM 200 filament addresses z-axis strength deficiencies, achieving 40% higher inter-layer toughness than standard PAEK feedstock. Oak Ridge National Laboratory demonstrates vacuum-assisted extrusion that cuts porosity below 2%, enabling 3D-printed polymer ducts for bleed-air systems. Airlines foresee digital inventories of certified spares, reducing lead-times from months to days. Such breakthroughs expand the accessible Heat Resistant Polymer market beyond conventional machining routes.
Restraints Impact Analysis
Restraint | (~) % Impact on CAGR Forecast | Geographic Relevance | Impact Timeline |
---|---|---|---|
Volatile raw-material & energy costs | -1.1% | EU & North America | Short term (≤ 2 years) |
Capital-intensive processing equipment requirement | -0.7% | Global, acute in emerging markets | Medium term (2-4 years) |
Looming Global Per- and polyfluoroalkyl Substances (PFAS) Restrictions on Fluoropolymers | -0.9% | EU and North America primarily, expanding globally | Long term (≥ 4 years) |
Source: Mordor Intelligence
Volatile Raw-material & Energy Costs
Supply disruptions have pushed benzene and caprolactam prices upward, leading BASF to add USD 0.15/lb to PA66 compound prices in June 2024. Concurrently, a 25% tariff on certain engineering resins sourced from Canada and Mexico threatens cost pass-through for United States (US) converters. Energy spikes in Europe escalate polymerisation overheads, narrowing margins for specialty compounds. Manufacturers deploy real-time analytics to hedge feedstock swings, yet project delays in downstream sectors occasionally curtail offtake. Such volatility caps near-term profitability across the Heat Resistant Polymer market.
Capital-intensive Processing Equipment Requirement
Extrusion of Polyether-ether-ketone (PEEK) demands barrel temperatures up to 450°C and corrosion-resistant alloys, lifting line costs above USD 2 million per 1,000 t/y capacity. Additive-manufacturing variants require heated build chambers held at 180°C, while quality control relies on multi-axis computed tomography scanners that can cost USD 800,000 each. New entrants in emerging economies often defer such investment, amplifying geographical concentration of supply. Large incumbents like BASF budget EUR 6.8 billion for growth projects through 2027, reinforcing scale advantages and slowing capacity dispersion. These hurdles temper the expansion pace of the Heat Resistant Polymer market, especially in price-sensitive applications.
Segment Analysis
By Type: PEEK Drives Innovation Despite Fluoropolymer Dominance
Fluoropolymers captured 35.18% of Heat Resistant Polymer market share in 2024 owing to unrivalled chemical inertness in semiconductor, aerospace, and chemical-processing environments. Regulatory headwinds targeting Per- and polyfluoroalkyl Substances (PFAS), however, spur Original Equipment Manufacturers (OEMs) to trial melt-processable alternatives such as PPS and polysulfones. Polyether-ether-ketone (PEEK), recording the fastest 7.82% CAGR, benefits from its biocompatibility in spinal cages and its printability in complex lattice implants. Victrex and Solvay have each launched medical-grade filaments certified under American Society for Testing and Materials (ASTM) F2026, accelerating hospital adoption. In additive manufacturing, Polyether-ether-ketone (PEEK) powder bed fusion volumes are projected to exceed 1,200 t by 2030, enlarging the Heat Resistant Polymer market size for the material. Polyphenylene Sulfide (PPS) is also rising; Syensqo’s Ryton PPS XE-5000 enables extrusion of pipe rated to 1,200 psi at 200°C, offering a drop-in upgrade for aggressive chemical service lines. Polybenzimidazole and specialty polyimides remain niche but indispensable in thermal shields and membrane separators above 300°C, preserving a premium pricing tier within the Heat Resistant Polymer market.
Note: Segment shares of all individual segments available upon report purchase
By End-user Industry: Automotive Electrification Accelerates Demand
The automotive sector led with 42.67% of Heat Resistant Polymer market size in 2024, reflecting wide adoption in battery modules, e-motor housings, and power distribution components. Expected electrified-vehicle sales growth secures a 7.91% CAGR to 2030, supported by materials such as Celanese’s Zytel HTN FR53G50NH for battery end-plates that deliver dimensional stability at 150 °C continuous use. Aerospace and defence absorb the next-largest volume, with thermoplastic composite ribs and nacelles slashing assembly hours by up to 30%. Electrical and electronics applications grow on the back of 5G roll-outs and AI data-centre expansion, each demanding low-loss dielectric films and high-CTI connectors. Industrial machinery uses Polyphenylene Sulfide (PPS) and Polysulfone (PSU) grades to replace stainless steel in corrosive pumps, reducing maintenance downtime. Healthcare, although smaller in tonnage, commands high margins; Food and Drug Administration (FDA) clearance of Polyether-ether-ketone (PEEK)-based cranial implants has opened more than 350,000 potential procedures annually worldwide, anchoring a resilient revenue stream for medical-grade suppliers in the Heat Resistant Polymer market.

Note: Segment shares of all individual segments available upon report purchase
Geography Analysis
Asia-Pacific retained a commanding 53.18% Heat Resistant Polymer market share in 2024 and is forecast to grow 7.56% annually through 2030. China’s “Made in China 2025” semiconductor roadmap fuels polymer demand for advanced lithography equipment seals, while the country’s electric vehicle (EV) production captures 60% of global output, ensuring long-run consumption of thermal-management resins. Japan leads sustainable-materials research; Toray’s biomass-derived Acrylonitrile Butadiene Styrene (ABS) pilot, set for October 2025 start-up, demonstrates large-scale bio-feedstock integration. South Korea’s Toray Advanced Materials unit is adding 5,000 t/y PPS capacity at Gunsan, enhancing regional supply security. India’s ambition to assemble commercial aircraft locally encourages investment in domestic thermoplastic-composite facilities, further broadening the Heat Resistant Polymer market.
North America remains a technology incubator. The United States channels federal funding to aerospace innovation, with NASA backing Hi-Rate Composite Aircraft Manufacturing (HiCAM) composite research. Canada and Mexico integrate deeply into the continent’s supply chain but face tariff uncertainties that may re-allocate extrusion capacity southwards. Electric-pickup programmes by a trio of US OEMs are placing sizeable multi-year orders for flame-retardant PPS battery shields, anchoring steady polymer pull-through. Europe, accounting for roughly 21% of the Heat Resistant Polymer market, drives regulatory transformation. France banned PFAS in cosmetics and selected textiles in February 2025, and the European Chemicals Agency is drafting broader restrictions that could impact over 10,000 substances. This legislative momentum accelerates substitution efforts and underpins research and development spending on fluorine-free alternatives.
The remaining regions, such as South America, the Middle East, and Africa collectively represent under 8% of Heat Resistant Polymer market size today but offer long-term upside. Brazil’s hybrid-electric bus programmes and Chile’s copper-mining maintenance needs both specify high-temperature nylon parts. Saudi Arabia’s Vision 2030 petrochemicals expansion underpins resin feedstock integration, while South Africa’s renewable-energy build-out demands UV-stable polymeric housings. Capacity additions are slower due to capital costs; nevertheless, OEM localisation targets and import-substitution incentives foreshadow gradual share gains through 2030.
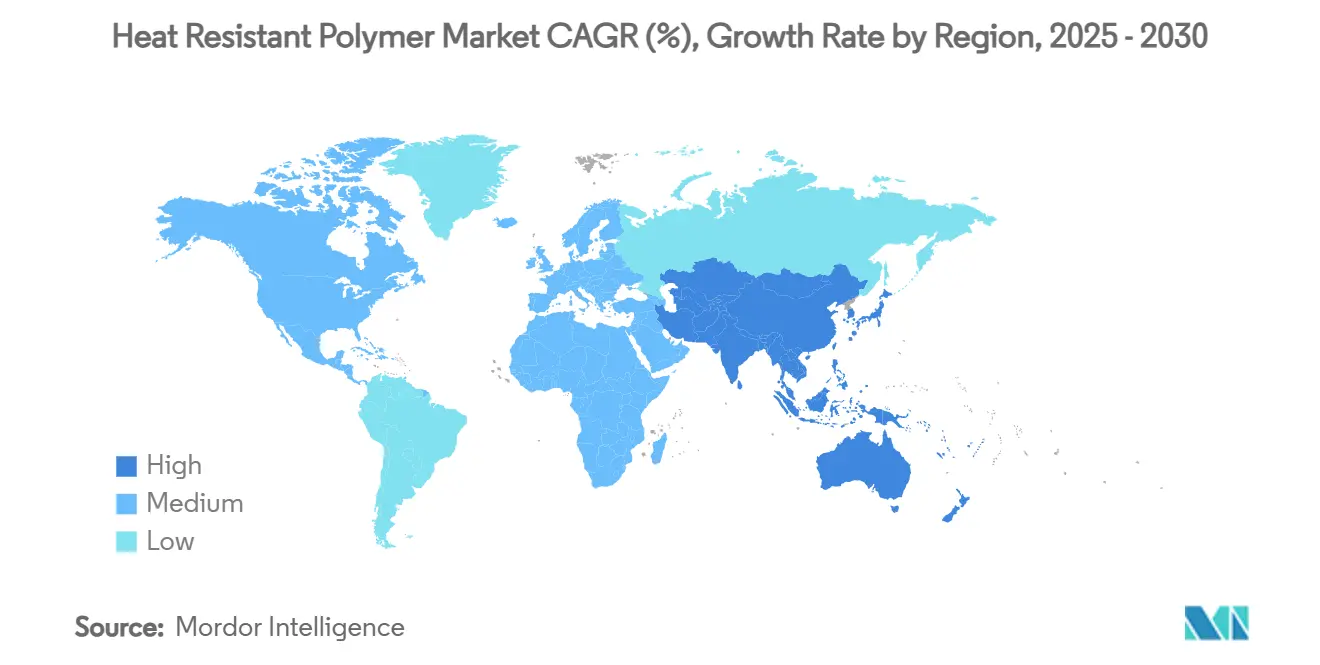
Competitive Landscape
The Heat Resistant Polymer market features a balance of global majors and focused specialists. BASF, Daikin Industries, DuPont, Solvay, and Victrex collectively hold the majority revenue share, supported by integrated feedstocks and multi-region plants. Victrex, a prominent player in the pure-play Polyether-ether-ketone (PEEK) industry, sustains double-digit EBITDA margins through IP-backed medical and aerospace grades. Patent filings for bio-advantaged polyaryletherketones and solvent-free fluoropolymer coatings are surging, reflecting the industry’s pivot toward circularity. Suppliers are also investing in closed-loop recycling; Solvay introduced a pilot line in Italy producing 30% recycled Polyphenylene Sulfide (PPS) pellet grades that meet aerospace specifications.
Heat Resistant Polymer Industry Leaders
-
DuPont
-
Daikin Industries
-
Solvay
-
BASF
-
Victex Plc.
- *Disclaimer: Major Players sorted in no particular order
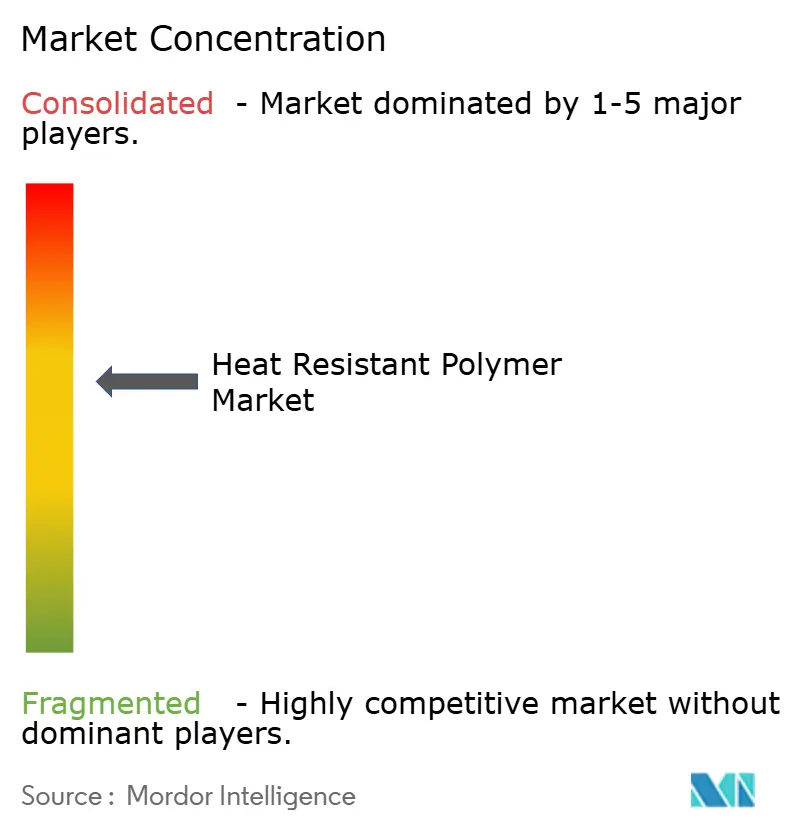
Recent Industry Developments
- July 2025: Arkema announced plans to invest USD 20 million to establish a new Rilsan Clear transparent polyamide unit, a high-performance heat-resistant polymer, at its Singapore facility. Operations are expected to begin in Q1 2026.
- July 2024: Alfa Chemistry broadened its product lineup by introducing a diverse selection of high-performance fluoropolymer materials, including PTFE (Polytetrafluoroethylene), PCTFE (Polychlorotrifluoroethylene), ETFE (Ethylene Tetrafluoroethylene), alongside a variety of other fluoropolymer coatings. These fluoropolymer materials are heat resistant in nature.
Global Heat Resistant Polymer Market Report Scope
The global heat resistant polymer market report includes:
By Type | Fluoropolymers | ||
Polyamides | |||
Polyphenylene Sulfide (PPS) | |||
Polybenzimidazole (PBI) | |||
Polyether-ether-ketone (PEEK) | |||
Other Types (Polyimides, Polysulfones, etc.) | |||
By End-user Industry | Automotive | ||
Aerospace & Defence | |||
Electrical & Electronics | |||
Industrial Equipment | |||
Marine | |||
Other End-user Industries (Healthcare, etc.) | |||
By Geography | Asia-Pacific | China | |
Japan | |||
India | |||
South Korea | |||
ASEAN Countries | |||
Rest of Asia-Pacific | |||
North America | United States | ||
Canada | |||
Mexico | |||
Europe | Germany | ||
United Kingdom | |||
France | |||
Italy | |||
Spain | |||
Russia | |||
NORDIC Countries | |||
Rest of Europe | |||
South America | Brazil | ||
Argentina | |||
Rest of South America | |||
Middle East and Africa | Saudi Arabia | ||
South Africa | |||
Rest of Middle East and Africa |
Fluoropolymers |
Polyamides |
Polyphenylene Sulfide (PPS) |
Polybenzimidazole (PBI) |
Polyether-ether-ketone (PEEK) |
Other Types (Polyimides, Polysulfones, etc.) |
Automotive |
Aerospace & Defence |
Electrical & Electronics |
Industrial Equipment |
Marine |
Other End-user Industries (Healthcare, etc.) |
Asia-Pacific | China |
Japan | |
India | |
South Korea | |
ASEAN Countries | |
Rest of Asia-Pacific | |
North America | United States |
Canada | |
Mexico | |
Europe | Germany |
United Kingdom | |
France | |
Italy | |
Spain | |
Russia | |
NORDIC Countries | |
Rest of Europe | |
South America | Brazil |
Argentina | |
Rest of South America | |
Middle East and Africa | Saudi Arabia |
South Africa | |
Rest of Middle East and Africa |
Key Questions Answered in the Report
What is the current size of the Heat Resistant Polymer market?
The Heat Resistant Polymer Market stands at USD 13.24 Million in 2025 and is projected to reach USD 17.92 Million by 2030.
Which segment is growing the fastest?
Polyether-ether-ketone (PEEK) is the fastest-expanding polymer type, expected to post a 7.82% CAGR through 2030.
How dominant is the automotive sector?
Automotive applications account for 42.67% of the market in 2024 and are forecast to grow at 7.91% annually over the next five years.
Why is Asia-Pacific so important?
Asia-Pacific holds 53.18% market share owing to its large electric vehicle (EV), electronics, and aerospace industries, and it is set to grow 7.56% a year through 2030.
What impact will Per- and polyfluoroalkyl Substances (PFAS) regulations have?
Imminent bans in Europe and parts of North America are accelerating the transition toward fluorine-free alternatives, opening new opportunities for Polyphenylene Sulfide (PPS), Polyether-ether-ketone (PEEK), and novel bio-based chemistries.
Page last updated on: April 24, 2025