Glass Fiber Reinforced Polymer Market Size and Share
Glass Fiber Reinforced Polymer Market Analysis by Mordor Intelligence
The Glass Fiber Reinforced Polymer Market size is estimated at USD 71.17 billion in 2025, and is expected to reach USD 90.45 billion by 2030, at a CAGR of 4.91% during the forecast period (2025-2030). Demand is rising as OEMs in transportation, renewable energy, aerospace, and construction replace heavier metals with corrosion-free composites to lower weight, boost durability, and meet stricter sustainability targets. Rapid urbanization, especially in Asia-Pacific, is stimulating infrastructure investments that specify glass fiber reinforced polymer solutions for rebar, bridge decks, and pipeline liners. Material innovation is widening the performance envelope: bio-based epoxy chemistries are entering series production, while quadaxial stitched reinforcements and hybrid carbon-glass fabrics are enabling new structural applications. Competition is intense but fragmented; multinationals are pruning low-margin lines and partnering with recyclers, whereas regional producers expand capacity close to customers to hedge logistics risk and currency volatility. End-of-life hurdles remain; nevertheless, breakthroughs in pyrolysis and silicon-carbide up-cycling are improving the circularity narrative and easing regulatory pressure in Europe and North America.
Key Report Takeaways
- By resin type, polyester commanded 62.15% share of the glass fiber reinforced polymer market size in 2024; epoxy is projected to grow fastest at 5.03% CAGR from 2025 to 2030.
- By manufacturing process, compression molding held 31.03% revenue share in 2024; injection molding is set to advance at the highest 4.94% CAGR during the forecast period.
- By fiber form, rovings accounted for 41.02% of the glass fiber reinforced polymer market size in 2024, while continuous filament mats will post the quickest 5.09% CAGR to 2030.
- By end-user industry, construction and infrastructure led with 36.82% of the glass fiber reinforced polymer market share in 2024, while wind energy is forecast to expand at a 5.18% CAGR through 2030.
- By geography, Asia-Pacific captured 48.91% of the glass fiber reinforced polymer market share in 2024 and will remain the fastest-growing region at 4.98% CAGR through 2030.
Global Glass Fiber Reinforced Polymer Market Trends and Insights
Drivers Impact Analysis
Driver | (~) % Impact on CAGR Forecast | Geographic Relevance | Impact Timeline |
---|---|---|---|
Growing Demand from the Automotive Sector | +1.20% | North America, Europe, Asia-Pacific | Medium term (2-4 years) |
Increasing Usage of Glass Fiber Reinforced Polymers in Wind Turbines | +1.30% | Europe, North America, emerging Asia-Pacific markets | Long term (≥4 years) |
Increasing Adoption of Glass Fiber Reinforced Polymers in the Aerospace Industry | +0.80% | North America, Europe, emerging Asia-Pacific | Medium term (2-4 years) |
Expandion of Construction and Infrastructure Sector | +1.40% | Global, highest in Asia-Pacific | Medium term (2-4 years) |
Growing Emphasis on Energy Efficent and Low-Weight Materials in Construction Industry | +0.90% | Global, with concentration in developed markets | Long term (≥4 years) |
Source: Mordor Intelligence
Growing Demand from the Automotive Sector
Electric-mobility programs are accelerating composite uptake because every kilogram saved extends driving range and shrinks battery size. Glass fiber reinforced thermoplastics now replace stamped steel in battery enclosures, trimming mass by 40% while improving fire resistance and thermal insulation[1]SGL Carbon, “Battery Cases for Electric Vehicles,” sglcarbon.com . OEMs deploy hybrid carbon-glass transmission housings that cut 30% weight yet keep stiffness for precise gear alignment. Glass fiber reinforced polymer market participants also exploit lower tooling costs to localize niche parts such as tension leaf springs that remove up to 50 kg from commercial vehicles, thereby permitting higher payloads.
Increasing Usage of Glass Fiber Reinforced Polymers in Wind Turbines
The wind sector is the fastest-growing end-user because taller towers and longer blades mandate lighter yet stronger materials. Turbine OEMs integrate carbon-glass hybrid spars and root inserts to keep tip deflection within limits, thereby enabling 15-MW platforms. Lithuanian researchers have validated pyrolysis routes that reclaim fibers and toxic styrene from end-of-life blades, reducing disposal impacts by up to 51% versus landfill. These advances improve the life-cycle credentials that national tenders increasingly require.
Increasing Adoption of Glass Fiber Reinforced Polymers in the Aerospace Industry
Aerospace engineers embed radio-frequency-transparent GFRP windows inside carbon fuselage skins, eliminating antenna fairings and lowering drag to save fuel burn on long-haul routes. Graphene-enhanced laminates provide lightning strike protection without copper meshes, removing further mass and easing repair logistics. Seats that mix bio-based resins with recyclable fibers deliver 20% lighter frames and help airlines satisfy emerging circularity mandates.
Expansion of Construction and Infrastructure Sector
Civil engineers specify GFRP rebar because it offers 1.5–2× the tensile strength of steel at one-quarter of the weight while never corroding, which extends bridge life in coastal or de-icing-salt environments. American Concrete Institute standards published in 2024 accelerated public-sector approvals, and Asia-Pacific megaprojects are now issuing tenders that require composite reinforcement. GFRP liners with 150-year service life rehabilitate undersized pipelines, boosting flow and lowering pumping energy. Energy-efficient building envelopes also adopt pultruded GFRP frames that minimize thermal bridging and cut operational emissions.
Restraints Impact Analysis
Restraint | (~) % Impact on CAGR Forecast | Geographic Relevance | Impact Timeline |
---|---|---|---|
High Manufacturing Cost | −0.8% | Global, severe in price-sensitive markets | Short term (≤2 years) |
Limited Recycling Capabilities | −0.6% | Europe, North America, emerging Asia-Pacific | Medium term (2-4 years) |
Availability of Alternative Materials | -0.50% | Global, severe in price-sensitive markets | Medium term (2-4 years) |
Source: Mordor Intelligence
High Manufacturing Cost
Specialized fiber sizing, tight process controls, and energy-intensive melting raise costs versus commodity metals. Price declines during 2024 squeezed margins; Owens Corning’s Composites sales fell 11% to USD 523 million in Q1 2024, prompting a strategic review of its glass reinforcements unit. Capital-intensive furnaces and limited economies of scale in emerging regions keep unit costs elevated, delaying adoption in cost-driven segments.
Limited Recycling Capabilities
Thermoset cross-linking prevents remelting, leading to landfill or incineration in many jurisdictions. Regulatory bans on composite waste in the European Union are tightening, exposing producers to higher disposal fees. Novel up-cycling converts ground GFRP into silicon carbide at operating costs below USD 0.05 per kg, offering a pathway to close the loop. Industrial scale-up, however, remains nascent, limiting immediate impact on glass fiber reinforced polymer market growth.
Segment Analysis
By Resin Type: Epoxy Accelerates While Polyester Retains Scale
Polyester resins dominated 2024 demand with a 62.15% share of the glass fiber reinforced polymer market size, thanks to low price and broad compatibility with compression and spray-up processes. Epoxy, though smaller, will register the highest 5.03% CAGR to 2030 because its superior adhesion, fatigue resistance, and low-void processing meet stringent aerospace, wind, and automotive specifications. Vinyl ester fills the mid-performance niche, combining better chemical resistance than polyester with lower cost than epoxy, and thus appeals to marine and chemical containment projects. Recent bio-based epoxies containing 23% renewable glycol cut manufacturing emissions by 21% without sacrificing mechanical strength, supporting ESG scorecards and procurement guidelines. Nanofiller-modified epoxies that double as solid polymer electrolytes open structural battery and supercapacitor use cases[2]Nitai Adak et al., “Epoxy-Based Multifunctional Solid Polymer Electrolytes,” Frontiers in Chemistry, frontiersin.org . The glass fiber reinforced polymer market expects continued cost pressure on conventional polyester as downstream customers seek lower embedded carbon alternatives.
Vinyl ester producers are enhancing cure kinetics to suit high-speed resin transfer lines, while polyurethane chemistries gain adoption in impact-absorption panels where toughness outweighs stiffness. Niche thermoplastics such as PEEK remain essential in oil-and-gas downhole tools requiring 240 °C service temperatures. Oversupply concerns are limited because large polyester plants in China run captive furnace networks, allowing quick output throttling during demand swings. Epoxy suppliers hedge raw-material volatility through forward contracts on bisphenol-A and epichlorohydrin, stabilizing pricing to aerospace primes. Innovations in continuous processing, such as snap-cure epoxies that reach demold in 60 seconds, will compress cycle time and support volume ramp-ups in the glass fiber reinforced polymer market.
Note: Segment shares of all individual segments available upon report purchase
By Process: Injection Molding Poised for the Fastest Uptake
Compression molding, including Sheet Molding Compound and Glass Mat Thermoplastic, accounted for 31.03% of 2024 revenue due to high repeatability and favorable economics at medium volumes. Injection molding will post a 4.94% CAGR through 2030 as high-flow, long-fiber thermoplastic compounds allow thin-wall complex parts without secondary finishing. Vacuum-assisted resin transfer molding has evolved; adding pressure during cure boosts fiber volume to 62% and lifts tensile strength to 760 MPa while trimming thickness by 4%[3]Rulin Shen et al., “Enhanced Vacuum-Assisted Resin Transfer Molding,” MDPI Polymers, mdpi.com . Manual lay-up persists for architectural panels and yacht hulls where design freedom overrules takt time.
Continuous pultrusion lines now integrate inline sanding and priming, reducing downstream labor for window frames and power-grid crossarms. Hybrid production cells that switch between thermoset and thermoplastic matrices extend asset utilization and enable multimaterial modules in the glass fiber reinforced polymer market. Robotic handling lowers scrap, and closed-loop digital twins detect resin-rich zones in real time, preventing delamination hot spots. Cost parity with aluminum extrusion is within reach for high-volume automotive sill beams once cycle times fall below 55 seconds, a benchmark that major Tier-1 suppliers target by 2027. In emerging economies, localized compression presses fill regional demand, aided by concessional financing that supports technology transfer.
By Fiber Form: Rovings Dominate While Continuous Filament Mats Outpace Growth
Rovings offered 41.02% of 2024 demand because they suit nearly every automated placement technology, from filament winding to organo-sheet stamping. Continuous filament mats will register a 5.09% CAGR as designers specify multiaxial reinforcement for large wind blades and utility poles. Chopped strand mats remain popular in bathware and truck fairings where isotropic stiffness at low cost is adequate. Woven fabrics deliver high directional properties, though their slower lay-up speed limits use to aerospace spars and radomes. Quadaxial stitched glass incorporating Nomex threads yields superior conformability and fire resistance for complex molds, broadening adoption in rail interiors.
Suppliers are engineering surface treatments that enhance wet-out in low-styrene resins, an essential step as regulators tighten emissions thresholds. E-CR glass compositions with higher corrosion resistance are replacing traditional E-glass in chemical plant grating, extending service life in acidic environments. Optical fiber pullers co-locate with roving lines to exploit furnace economies of scale, enabling backward integration. The glass fiber reinforced polymer market benefits from hub-and-spoke logistics: bulk rovings feed regional fabric converters, cutting freight costs and lead times. Automation upgrades such as laser-guided spool changeover increase uptime and lower manufacturing cost per kilogram, easing one restraint to broader composite adoption.
By End User Industry: Construction Retains Lead, Wind Energy Gains Velocity
Construction held 36.82% of 2024 revenue, reflecting the widespread shift to corrosion-free rebar, bridge decks, and façade elements. The segment will expand steadily as governments channel stimulus toward climate-resilient infrastructure. Wind energy, though smaller today, will surge at 5.18% CAGR, supported by national offshore auctions and repowering of older fleets. Automotive original equipment manufacturers order high-volume structural brackets, roof panels, and crash beams to accelerate electrification targets. Marine builders specify vinyl-ester laminates for hulls, leveraging lighter displacement to improve fuel economy, while naval programs value radar transparency for signature management. Aerospace and defense secure premium materials, accepting higher costs for weight and performance gains, thus influencing high-margin niches in the glass fiber reinforced polymer market.
Electrical and electronics manufacturers adopt GFRP stator sealants that combine dielectric strength with tight dimensional tolerance, enabling compact, high-speed motors. Healthcare equipment producers select composite housings for MRI machines to avoid magnetic interference. Consumer goods brands explore translucent, color-integrated GFRP for sports equipment and luggage, tapping lifestyle aesthetics. Cross-industry interest benefits midstream suppliers who can pivot furnace output among rovings, chopped strands, and milled fibers to balance cyclical swings. End-market diversity therefore stabilizes furnace utilization and underpins long-range investment decisions across the glass fiber reinforced polymer market.
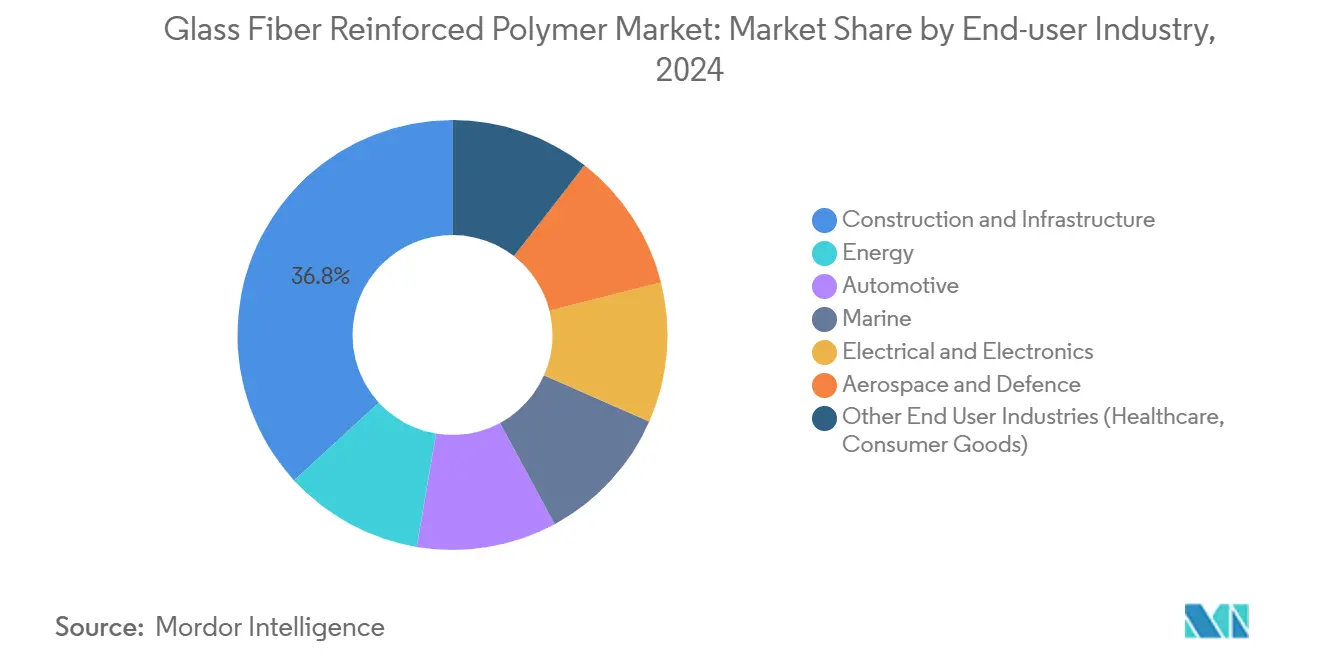
Note: Segment shares of all individual segments available upon report purchase
Geography Analysis
Asia-Pacific dominated with 48.91% revenue in 2024 and is projected to grow at a 4.98% CAGR through 2030. China accelerates capacity with mega-plants such as BASF’s USD 10.8 billion Zhanjiang Verbund, which will operate on 100% renewable electricity and supply automotive and electronics composites. India’s rail and road modernization campaigns stimulate local demand; BASF has announced additional polyamide and PBT expansions to serve downstream converters. ASEAN countries leverage near-shoring as supply-chain diversification pushes glass fiber reinforced polymer market participants to locate closer to end users.
In North America, the United States leads turbine blade, aerospace, and infrastructure uptake. Jushi Group is finalizing a greenfield furnace in the country, promising regional supply security and import duty avoidance. Federal Buy-America clauses increasingly favor domestic sourcing, benefitting incumbent producers and new entrants. Canada focuses on lightweight buses and battery enclosures to meet zero-emission vehicle mandates.
Europe enforces circular-economy legislation that spurs investment in recyclable resins and blade-to-blade glass reclamation. Carbon Rivers’ multi-stage pyrolysis recovers fiber for reuse in insulation and sheet molding compounds, attracting grants and brand-owner partnerships. Germany supports hydrogen pipeline retrofits that require corrosion-resistant liners, while offshore wind build-out in the North Sea sustains high-modulus roving demand. South America and Middle East & Africa remain niche but are gaining momentum as Brazil upgrades ports and Saudi Arabia funds mega-projects in transport and renewable energy, opening new arenas for the glass fiber reinforced polymer market.
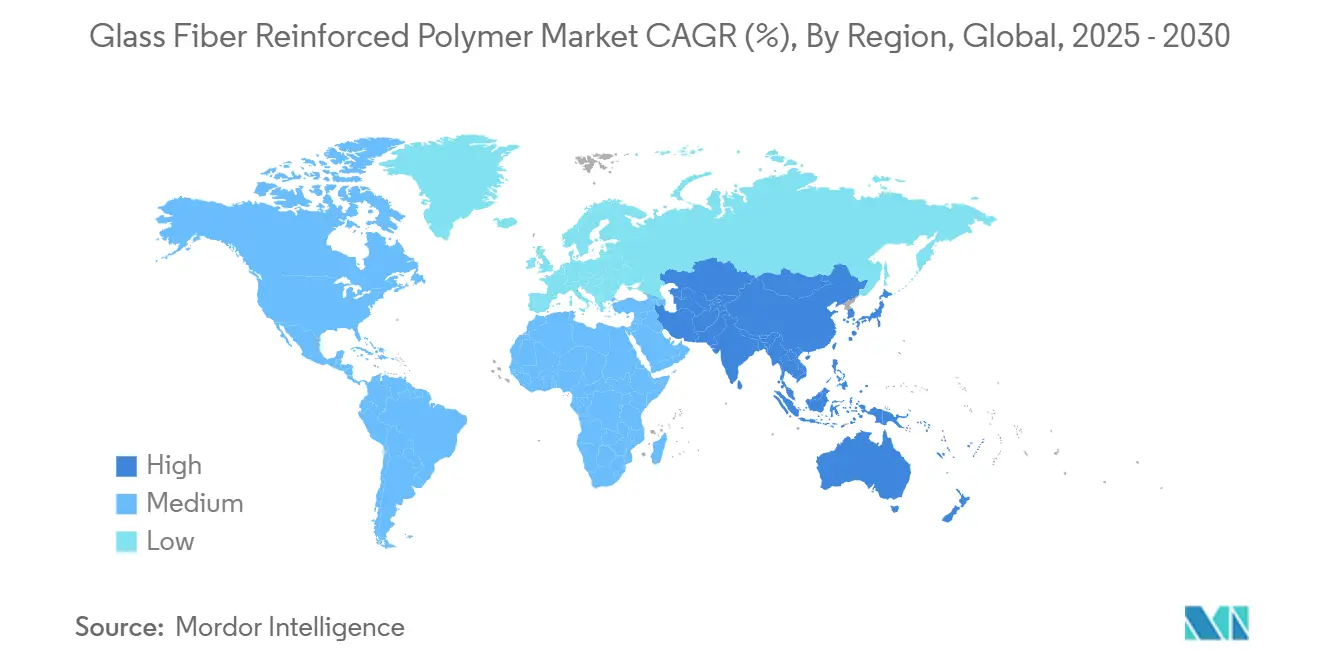
Competitive Landscape
The market is moderately fragmented; the top five suppliers account for roughly 30% of global volume, leaving ample space for regional challengers. Owens Corning is trimming underperforming assets and prioritizing higher-margin specialty rovings after its Composites EBIT margin slipped to 11% in Q3 2024. BASF is executing a EUR 10 billion Asia growth strategy centered on low-carbon production; loopamid PA6 recycled resin entered commercial output in 2025, reinforcing its sustainability positioning. Celanese is rolling out Zytel XMP70G50, a 50% glass-filled PA66 designed to replace metal in EV chassis, thereby capturing upstream integration synergies across its acetyl supply chain.
Regional players in China, India, and the Middle East commission furnaces with nameplate capacities of 80,000 tpa, often benefiting from subsidized energy and land. These entrants target commodity rovings for infrastructure and wind sectors, heightening price competition. Strategic alliances bridge technology gaps: Kineco Exel has partnered with Vestas to supply pultruded carbon-glass planks, integrating into global blade value chains. Upstream petroleum companies explore vertical moves into epoxy and vinyl ester precursors, seeking captive demand for by-products. Innovation clusters in Europe collaborate on graphene functionalization and bio-based matrix chemistries, feeding a relentless pipeline of differentiating features that help firms defend margins as standard grades commoditize within the glass fiber reinforced polymer market.
Glass Fiber Reinforced Polymer Industry Leaders
-
China Jushi Co. Ltd
-
Johns Manville
-
Owens Corning
-
PPG Industries Inc.
-
Advanced Composites Inc.
- *Disclaimer: Major Players sorted in no particular order
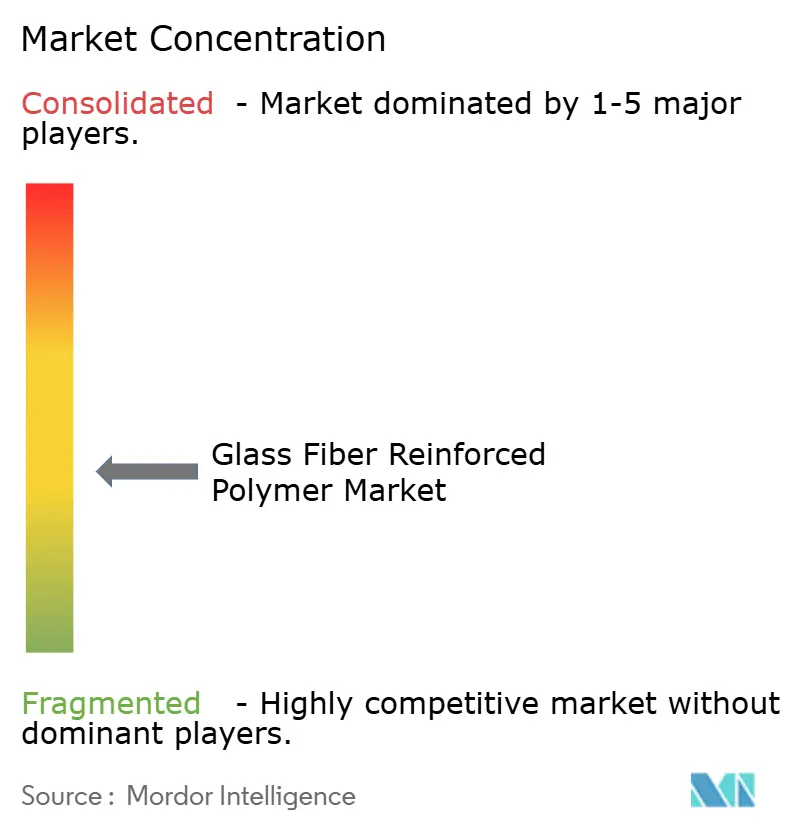
Recent Industry Developments
- November 2024: Owens Corning plans to invest in a new fiberglass insulation line in Kansas, scheduled to commence operations in 2027, while evaluating strategic alternatives for its global glass reinforcements business. This move is expected to influence the glass fiber-reinforced polymer market by driving innovation and expanding product offerings.
- March 2024: At CHINAPLAS 2024, BASF and Jiangsu Worldlight New Material Co., Ltd unveiled a new polyurethane photovoltaic module frame. This innovative frame, crafted from glass fiber-reinforced polyurethanes, boasts an impressive 85% reduction in carbon footprint when compared to traditional aluminum frames.
Global Glass Fiber Reinforced Polymer Market Report Scope
The glass fiber reinforced polymer market report includes:
By Resin Type | Polyester | ||
Vinyl Ester | |||
Epoxy | |||
Polyurethane | |||
Other Resin Types (PEEK Resin, Phenolic Resin, etc.) | |||
By Process | Manual Process | ||
Compression Molding | Sheet Molding Compound Process | ||
Glass Mat Thermoplastic Process | |||
Continuous Process | |||
Injection Molding | |||
By Fiber Form | Rovings | ||
Chopped Strands Mats | |||
Continuous Filament Mats | |||
Woven Rovings/Fabrics | |||
By End User Industry | Energy | ||
Automotive | |||
Marine | |||
Construction and Infrastructure | |||
Electrical and Electronics | |||
Aerospace and Defence | |||
Other End User Industries (Healthcare, Consumer Goods) | |||
By Geography | Asia-Pacific | China | |
India | |||
Japan | |||
South Korea | |||
Rest of Asia-Pacific | |||
North America | United States | ||
Canada | |||
Mexico | |||
Europe | Germany | ||
United Kingdom | |||
France | |||
Italy | |||
Rest of Europe | |||
South America | Brazil | ||
Argentina | |||
Rest of South America | |||
Middle East and Africa | Saudi Arabia | ||
South Africa | |||
Rest of Middle-East and Africa |
Polyester |
Vinyl Ester |
Epoxy |
Polyurethane |
Other Resin Types (PEEK Resin, Phenolic Resin, etc.) |
Manual Process | |
Compression Molding | Sheet Molding Compound Process |
Glass Mat Thermoplastic Process | |
Continuous Process | |
Injection Molding |
Rovings |
Chopped Strands Mats |
Continuous Filament Mats |
Woven Rovings/Fabrics |
Energy |
Automotive |
Marine |
Construction and Infrastructure |
Electrical and Electronics |
Aerospace and Defence |
Other End User Industries (Healthcare, Consumer Goods) |
Asia-Pacific | China |
India | |
Japan | |
South Korea | |
Rest of Asia-Pacific | |
North America | United States |
Canada | |
Mexico | |
Europe | Germany |
United Kingdom | |
France | |
Italy | |
Rest of Europe | |
South America | Brazil |
Argentina | |
Rest of South America | |
Middle East and Africa | Saudi Arabia |
South Africa | |
Rest of Middle-East and Africa |
Key Questions Answered in the Report
How big is the Glass Fiber Reinforced Polymer market in 2024 and what is the expected size by 2030?
The market is valued at USD 71.17 billion in 2024 and is projected to reach USD 90.45 billion by 2030.
Which region holds the largest Glass Fiber Reinforced Polymer market share?
Asia-Pacific leads with 48.91% share, driven by rapid industrialization and local capacity expansions.
What end-use sector dominates demand for Glass Fiber Reinforced Polymer industry products?
Construction and infrastructure account for the largest share because GFRP rebar and profiles combat corrosion and lower lifecycle costs.
Why is GFRP preferred in electric vehicles?
It offers high strength at low weight, improving vehicle range while meeting crash requirements, and it can integrate thermal management functions in battery enclosures.
What is the main obstacle to wider GFRP adoption?
High manufacturing costs relative to metals and limited recycling options are key constraints, though process automation and novel recycling methods are gradually easing these issues.
How fast is the wind-energy segment of the Glass Fiber Reinforced Polymer market growing?
It is forecast to grow at 5.18 % CAGR through 2030 as turbine blades become larger and demand higher-performance composites.
Page last updated on: July 1, 2025