US Vibration Sensors Market Analysis by Mordor Intelligence
The United States vibration sensors market size reached USD 1.83 billion in 2025 and is forecast to reach USD 2.27 billion by 2030, reflecting a 4.33% CAGR. The United States vibration sensors market is moving from volume expansion toward technology-driven value creation as end users adopt edge AI, wireless connectivity, and Industry 4.0 practices. Uptake of predictive analytics, compliance pressures from OSHA and API standards, and the need to limit unplanned downtime underpin steady demand growth. Wireless nodes, energy-harvesting designs, and MEMS-based accelerometers broaden deployment options across aging industrial assets. Suppliers differentiate through integrated solutions that bundle hardware with cloud analytics while forming ecosystem partnerships to address cybersecurity and legacy-system integration challenges.
Key Report Takeaways
- By product type, accelerometers held 45.1% of the United States vibration sensors market share in 2024, while velocity sensors are projected to grow at a 7.81% CAGR to 2030.
- By sensor technology, wired digital systems accounted for 61.3% revenue share in 2024; wireless solutions are forecast to expand at a 9.23% CAGR through 2030.
- By sensing material, piezoelectric sensors commanded 49.4% of the United States vibration sensors market size in 2024, whereas MEMS devices are expected to advance at an 8.62% CAGR.
- By end-user industry, oil and gas led with 21.8% revenue share in 2024, while power generation is set to record the highest CAGR at 6.91% over 2025-2030.
US Vibration Sensors Market Trends and Insights
Drivers Impact Analysis
Driver | (~) % Impact on CAGR Forecast | Geographic Relevance | Impact Timeline |
---|---|---|---|
Rising demand for predictive-maintenance programs | +1.2% | Global, with concentration in US industrial corridors | Medium term (2-4 years) |
IIoT-enabled wireless vibration nodes gaining traction | +0.9% | US manufacturing belt, Texas energy corridor | Short term (≤ 2 years) |
Accelerating adoption of MEMS-based low-cost accelerometers | +0.7% | National, with early gains in automotive clusters | Medium term (2-4 years) |
OSHA and API compliance pressures in hazardous industries | +0.6% | Gulf Coast, Appalachian regions, California refineries | Long term (≥ 4 years) |
Edge-AI analytics unlocking new value pools | +0.5% | Silicon Valley, Boston tech corridor, Austin | Short term (≤ 2 years) |
Vehicle electrification driving high-frequency vibration sensing | +0.4% | Detroit, California, Southeast automotive regions | Long term (≥ 4 years) |
Source: Mordor Intelligence
Rising Demand for Predictive-Maintenance Programs
Unplanned downtime costs exceed USD 50 billion each year across U.S. manufacturing, prompting a shift from time-based to condition-based maintenance strategies. Many plants now deploy continuous vibration monitoring that detects bearing wear and misalignment early, extending asset life by as much as 30% while cutting spare-parts inventory. Machine learning applied to spectral data identifies anomalies that human analysts can miss, especially in facilities with interacting machines. Wind-farm operators using these tools have avoided lost production valued at EUR 4–5 million (USD 4.3–5.4 million) by predicting gearbox failures.[1]AspenTech, “Predictive Maintenance in Wind Turbines,” aspentech.com Early adoption success is accelerating broader rollouts across automotive, metals, and food-processing sites.[2]IBM, “Cost of Unplanned Downtime Study,” ibm.com
IIoT-Enabled Wireless Vibration Nodes Gaining Traction
Wireless monitoring eliminates cable routing and allows coverage of assets once considered unreachable. LoRaWAN networks transmit data more than 15 kilometers, proven in remote environmental sensing.[3]LoRa Alliance, “Long-Range IoT Networks,” iot.org Energy-harvesting devices powered by ambient vibration or heat remove battery-change labor, addressing previous cost barriers. Baker Hughes’ Ranger Pro sensor, approved for global hazardous areas, provides a template for oil and gas operators pursuing enterprise-wide condition monitoring. Short deployment times fit scheduled maintenance windows, supporting rapid ROI calculations.
Accelerating Adoption of MEMS-Based Low-Cost Accelerometers
MEMS accelerometers now cost under USD 10 per unit yet achieve noise performance once limited to piezoelectric devices priced five to ten times higher. Silicon micromachining improvements enable high-aspect-ratio structures that raise sensitivity while maintaining ruggedness. Electric-vehicle OEMs specify MEMS sensors to capture high-frequency vibration signatures critical for battery-pack integrity and motor control. TDK’s high-temperature closed-loop MEMS line extends viable operating range beyond 175 °C, opening gas-turbine and geothermal applications. As volumes scale, MEMS adoption spreads to medical, semiconductor, and building-automation contexts.
OSHA and API Compliance Pressures in Hazardous Industries
Expanded OSHA instance-by-instance citations, plus API 670 mandates for rotating equipment, drive continuous monitoring of pumps, compressors, and turbines. Fines, remediation, and downtime can exceed USD 1 million per incident, making vibration sensors a risk-mitigation investment. Intrinsically safe designs rated for Class I Division 2 zones meet stringent energy-limitation rules while supporting through-glass programming that avoids enclosure opening. Compliance programs often bundle sensors with cloud dashboards that document audit trails for insurers and regulators.
Restraints Impact Analysis
Restraint | (~) % Impact on CAGR Forecast | Geographic Relevance | Impact Timeline |
---|---|---|---|
Integration issues with legacy machinery | -0.8% | Rust Belt manufacturing regions, aging refineries | Medium term (2-4 years) |
Shortage of intrinsically safe sensors for Class I/Div II zones | -0.6% | Gulf Coast petrochemical complexes, mining regions | Short term (≤ 2 years) |
Cyber-security risks from connected sensors | -0.4% | National critical infrastructure | Long term (≥ 4 years) |
Supply-chain volatility in piezo-ceramic materials | -0.3% | Global impact, concentrated in high-tech manufacturing | Medium term (2-4 years) |
Source: Mordor Intelligence
Integration Issues with Legacy Machinery
Many facilities rely on equipment built decades ago without standardized sensor mounts or communication ports. Retrofitting can cost three to five times more than installing sensors on new assets. Resonance effects in older frames complicate signal fidelity and demand custom fixtures that add labor hours. Multiple generations of proprietary protocols require gateways that increase capex and cybersecurity exposure. Analog Devices’ Voyager4 platform offers adaptive mounting and on-node AI to counter these hurdles, though price sensitivity slows adoption.
Shortage of Intrinsically Safe Sensors for Class I/Div II Zones
Certification cycles run 18–24 months, limiting availability of approved devices. Design requirements such as energy-limiting circuits raise unit prices by up to 400% versus general-purpose models, stretching project budgets. Petrochemical turnarounds have stalled when qualified sensors were back-ordered, forcing rescheduling of inspections. Portable intrinsically safe recorders for coal mines show innovation, but production volumes remain insufficient to alleviate supply risk. Operators consider dual sourcing and long-term contracts to secure supply continuity.
Segment Analysis
By Product Type: Accelerometers Lead Industrial Transformation
Accelerometers represented 45.1% of 2024 shipments, underlining their versatility across frequency ranges. Velocity sensors post the highest 7.81% CAGR as they capture low-frequency faults earlier in large rotating equipment. Multi-parameter devices combine acceleration, velocity, and temperature to simplify installation and reduce total cost of ownership. Analog Devices integrates edge AI in such packages, allowing on-node fault classification that trims network bandwidth. Growing use of velocity sensing in hydropower and pulp-and-paper plants supports revenue diversity within the United States vibration sensors market.
The second growth driver lies in expanding tire and gearbox testing where triaxial accelerometers track compound dynamic loads. Proximity probes, though niche, remain indispensable in non‐contact turbine applications. Tachometers retain value as reference instruments for order analysis in variable-speed drives. As plants digitize, asset-health platforms ingest data from all product types, creating service fees that augment hardware margins and strengthen supplier-customer ties within the United States vibration sensors market.
Note: Segment shares of all individual segments available upon report purchase
By Sensor Technology: Wireless Solutions Surge Despite Wired Dominance
Wired digital systems delivered 61.3% of 2024 revenue thanks to proven reliability and existing cable trays. However, wireless nodes grow 9.23% annually as battery life and radio resilience improve. LoRaWAN achieves kilometer-scale reach on single gateways, supporting distributed solar farms. Hybrid power-plus-wireless architectures appear in pharmaceutical cleanrooms where uptime and contamination control are paramount. Energy harvesting addresses maintenance pain points and expands use cases such as rotating kilns where slip rings add cost and complexity.
Data-diode features and AES-256 encryption mitigate cybersecurity concerns that once favored wired setups. Firmware-over-air updates let operators patch vulnerabilities without physical access. Standardization under ISA100 and IEC 62938 promotes interoperability across vendors, broadening the ecosystem for the United States vibration sensors market.
By Sensing Material/Principle: MEMS Technology Challenges Piezoelectric Dominance
Piezoelectric crystals retained 49.4% share in 2024 due to high-temperature tolerance and low noise floors that suit aerospace and energy applications. Lead-free ceramics are gaining traction to meet environmental directives, easing future regulatory risk. MEMS accelerometers grow 8.62% annually, leveraged by smartphone supply chains that push down cost while funding R&D for industrial robustness. Silicon-carbide MEMS devices now tolerate harsh chemical vapors and temperatures above 200 °C, broadening deployment in chemical reactors.
Magnetostrictive and fiber-optic sensors occupy niches where electromagnetic immunity matters, such as MRI facilities and high-voltage switchyards. Composite carbon-nanotube structures promise lighter housings for drone-based inspection kits, adding an emerging frontier for the United States vibration sensors market.
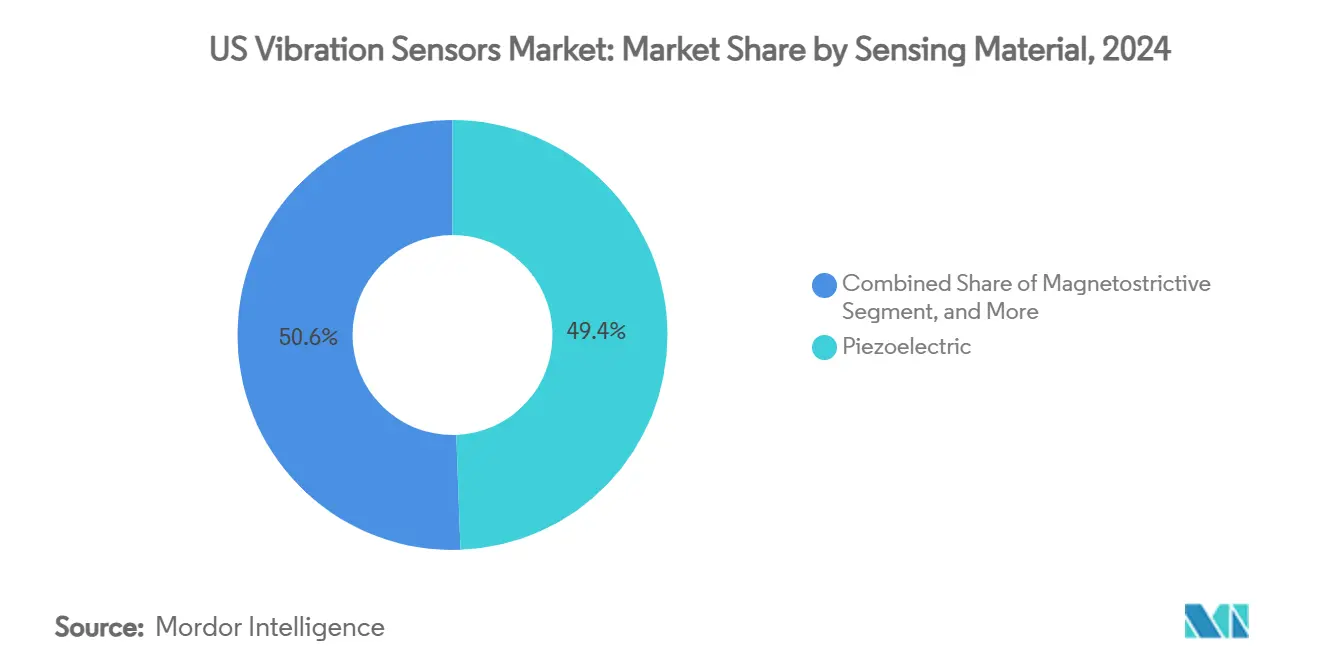
Note: Segment shares of all individual segments available upon report purchase
By End-User Industry: Power Generation Drives Growth Acceleration
Power-generation customers log a 6.91% CAGR, propelled by grid modernization, wind-farm expansions, and higher rotating-asset density in gas-peaking plants. Utilities embed sensors in turbine bearings, gearboxes, and generators to avoid forced outages that disrupt power-purchase agreements. Oil and gas remains the largest revenue contributor at 21.8% of 2024 spend due to extensive installed rotating fleets and stringent API guidelines. Aerospace and defense demand extreme reliability, influencing supplier quality systems and margin structures.
Electric-vehicle factories deploy vibration nodes on battery conveyors and motor test stands to safeguard product quality. Hospitals use low-cost MEMS sensors to track vibrations during construction to protect MRI and CT imaging uptime. Mining firms rely on wireless sensor meshes to oversee crushers and conveyors in remote pits where cable deployment is prohibitive, underscoring diversified pull for the United States vibration sensors market.
Geography Analysis
The Gulf Coast hosts the most intensive deployments, powered by petrochemical plants and offshore rigs needing continuous monitoring for safety compliance. Texas blends conventional energy operations with expanding renewable projects such as wind-turbine farms and grid-scale batteries, lifting demand for wireless sensor backbones. Midwest industrial corridors, including Michigan and Ohio, retrofit aging stamping presses and machining centers with vibration nodes to extend asset life and uphold throughput targets. The United States vibration sensors market size tied to these Midwestern sectors is projected to climb steadily as predictive-maintenance culture spreads.
California supports high-performance sensor consumption in aerospace engine test cells and semiconductor fabs that insist on micro-g resolution. State-level sustainability incentives further promote condition-monitoring investment to curb energy waste. In the Northeast, a dense concentration of combined-cycle plants and chemicals facilities drives compliance-oriented spending, while regional universities partner with suppliers to pilot new sensing algorithms. Cross-border trade with Canada influences supply logistics but does not materially alter purchasing decisions inside the United States vibration sensors market.
Inter-regional competition for skilled maintenance technicians raises adoption of automation tools that fill workforce gaps. Federal infrastructure outlays and private-sector battery investments are expected to keep capital spending levels healthy, benefiting vendors positioned with scalable platforms. Regional economic development boards increasingly cite predictive maintenance projects as proof points in bids to attract manufacturing reshoring, providing another tailwind for vibration-sensor growth trajectories.
Competitive Landscape
The United States vibration sensors market remains moderately fragmented, with the top five players controlling roughly 35–40% of revenue. Global multinationals offer broad portfolios spanning sensors, gateways, and analytics software, while regional specialists focus on hazardous-area certifications or fiber-optic measurement. Honeywell’s partnership with Analog Devices integrates sensor outputs into building-management suites, allowing customers to consolidate HVAC, energy, and asset-health data streams. TDK emphasizes MEMS innovation, unveiling modules that blend AI coprocessing to reduce cloud traffic and latency.
Patent filings concentrate on wireless energy harvesting and anomaly-detection models, signalling a race to secure intellectual property in data-centric services. Suppliers bundle training and remote diagnostics into subscriptions, shifting revenue toward recurring streams. Some firms pursue OEM-installed sensor programs that lock in pull-through consumables and upgrade kits across equipment life cycles. Niche entrants carve space in intrinsically safe solutions, using certification expertise as a barrier to large-scale commoditization. As use cases expand to HVAC, elevators, and smart buildings, cross-domain alliances widen addressable markets without heavy capex for new product lines.
US Vibration Sensors Industry Leaders
-
National Instruments Corporation
-
Texas Instruments Incorporated
-
Emerson Electric Co.
-
Honeywell International Inc.
-
SKF USA Inc.
- *Disclaimer: Major Players sorted in no particular order
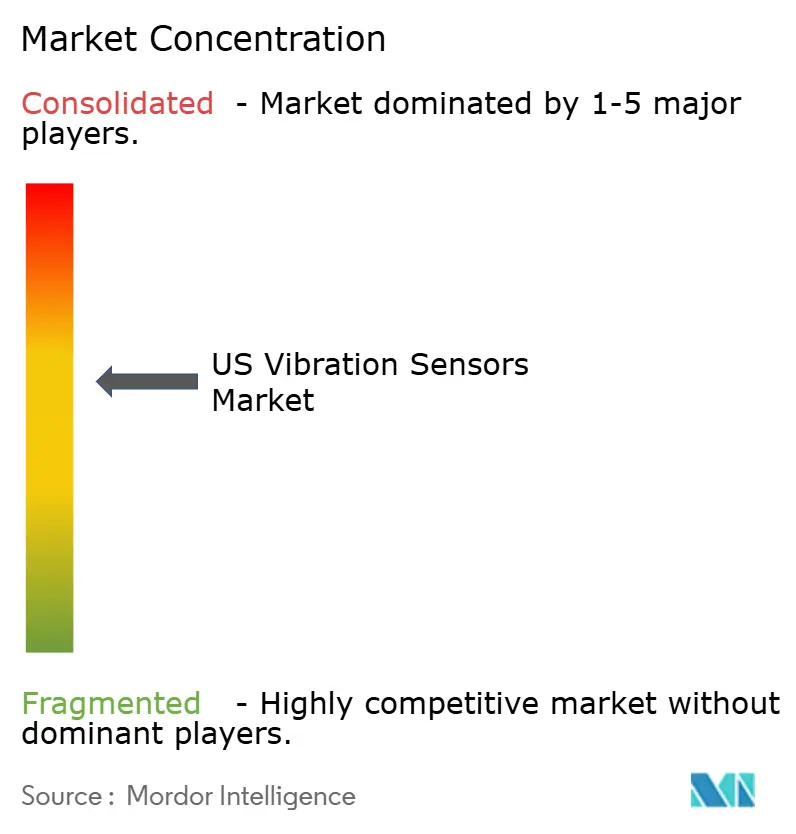
Recent Industry Developments
- June 2025: TDK introduced high-temperature closed-loop MEMS accelerometers for gas-turbine and geothermal assets. The move extends the firm’s reach into applications where cooling jackets were once mandatory, positioning TDK to capture share in high-value energy segments.
- May 2025: Baker Hughes launched the Ranger Pro wireless sensor with global hazardous-area approvals and seamless integration into System 1 software. The release strengthens the company’s full-stack condition-monitoring portfolio and supports its services-led growth strategy.
- April 2025: Nanoprecise Sci Corp augmented its wireless sensors with edge AI that classifies over 70 mechanical faults in real time. This advancement underpins the firm’s differentiation on early warning accuracy and reduces customer dependence on central analytics capacity.
- February 2025: Analog Devices published Voyager4 documentation featuring battery-life optimization for IIoT deployments. Providing open design details encourages ecosystem adoption and aligns with the company’s strategy of driving demand for its mixed-signal chipsets.
US Vibration Sensors Market Report Scope
The United States Vibration Sensors Market is segmented on the basis of Type (Accelerometers, Electrodynamic Velocity Transducer, Non-Contact Displacement Transducer), By Material (Doped Silicon Sensors, Piezoelectric Ceramics, Quartz), By Technology (Hand Probes, Piezoelectric, Piezoresistive Sensors, Strain Gauge Sensor, Tri-Axial Sensor, Variable Capacitance Sensors) By Application (Aerospace, Automobile, Coal Mining and Quarry, Consumer Electronics, Food, Machine Monitoring, Medicine, Oil and Gas and Others).
By Product Type | Accelerometers |
Proximity Probes | |
Tachometers | |
Velocity Sensors | |
Others | |
By Sensor Technology | Wired (Analog/Digital) |
Wireless (BLE, LoRa, Wi-Fi) | |
By Sensing Material / Principle | Piezoelectric |
MEMS (Capacitive/Piezoresistive) | |
Magnetostrictive | |
Fiber-Optic | |
By End-user Industry | Automotive |
Aerospace and Defense | |
Oil and Gas | |
Metals and Mining | |
Power Generation | |
Healthcare | |
Consumer Electronics | |
Other End-user Industries |
Accelerometers |
Proximity Probes |
Tachometers |
Velocity Sensors |
Others |
Wired (Analog/Digital) |
Wireless (BLE, LoRa, Wi-Fi) |
Piezoelectric |
MEMS (Capacitive/Piezoresistive) |
Magnetostrictive |
Fiber-Optic |
Automotive |
Aerospace and Defense |
Oil and Gas |
Metals and Mining |
Power Generation |
Healthcare |
Consumer Electronics |
Other End-user Industries |
Key Questions Answered in the Report
What is the current value of the United States vibration sensors market?
The market is valued at USD 1.83 billion in 2025.
How fast is the United States vibration sensors market expected to grow?
It is projected to expand at a 4.33% CAGR, reaching USD 2.27 billion by 2030.
Which product category holds the largest share?
Accelerometers lead with 45.1% revenue share as of 2024.
Why are wireless vibration sensors gaining popularity?
They cut installation costs, reach remote assets, and now leverage energy harvesting for long life.
Which end-user segment is forecast to grow the fastest?
Power generation shows the highest CAGR at 6.91% due to grid modernization and renewable integration.
What are the key regulatory drivers for sensor adoption?
OSHA enforcement and API 670 standards mandate continuous monitoring of critical rotating equipment.
Page last updated on: July 11, 2025