Vibration Sensor Market Analysis by Mordor Intelligence
The vibration sensor market size is valued at USD 6.10 billion in 2025 and is forecast to reach USD 8.60 billion by 2030, reflecting a 7.10% CAGR during the period. Continued investment in predictive maintenance programs, miniaturized MEMS designs, and stricter machinery-health regulations accelerated adoption across factories, wind farms, and vehicle plants. Asia-Pacific manufacturers, wind turbine owners, and automotive assemblers directed much of this spending, aided by falling sensor prices and local semiconductor capacity expansions. Wireless connectivity reduced installation costs, and edge-AI firmware cut data traffic, making sensors viable for remote or hazardous sites. Meanwhile, supply-chain diversification gained urgency after China’s 2025 export controls on rare-earth inputs used in ceramic sensing elements.[1]MainRich Magnets, “China's 2025 Rare Earth Export Controls: A Comprehensive Guide for Importing Sintered NdFeB Magnets,” mainrichmagnets.com
Key Report Takeaways
- By product type, accelerometers held 54.4% of the vibration sensor market share in 2024, while wireless velocity sensors were projected to advance at a 9.1% CAGR through 2030.
- By technology, piezoelectric devices led with 46.3% share in 2024, but MEMS devices were the fastest growing at a 10.3% CAGR to 2030.
- By material, piezoelectric ceramics accounted for 58.4% share of the vibration sensor market size in 2024, whereas doped silicon substrates were expected to expand at a 7.9% CAGR.
- By end-use industry, industrial manufacturing commanded a 27.2% share in 2024, yet automotive applications were set to grow at an 8.9% CAGR through 2030.
- By geography, Asia-Pacific contributed 34.2% revenue in 2024 and was forecast to post an 8.3% CAGR, retaining regional leadership.
Global Vibration Sensor Market Trends and Insights
Drivers Impact Analysis
Driver | (~) % Impact on CAGR Forecast | Geographic Relevance | Impact Timeline |
---|---|---|---|
Proliferation of Predictive Maintenance Programs in Continuous Process Industries (Asia Pacific) | +1.8% | Asia-Pacific core, spill-over to MEA | Medium term (2-4 years) |
Rise of Wireless MEMS Sensors for Hazardous Oil and Gas Sites (Middle East) | +1.2% | Middle East and North America | Short term (≤ 2 years) |
Edge-AI Enabled Diagnostics in Automotive Assembly (Europe) | +1.5% | Europe and North America | Medium term (2-4 years) |
Mandatory ISO 20816 Compliance in EU and North America | +0.9% | EU and North America | Short term (≤ 2 years) |
Expansion of Wind Turbine Installations (Nordics and China) | +1.1% | Nordics, China, spill-over to Global | Long term (≥ 4 years) |
Miniaturization Demand from Wearables and Hearables | +0.8% | Global | Medium term (2-4 years) |
Source: Mordor Intelligence |
Proliferation of Predictive Maintenance Programs in Continuous Process Industries
Asia-Pacific plant operators used predictive maintenance to reduce unplanned downtime costs by up to 50%, relying on dense sensor grids that stream high-frequency data to analytics engines. Early projects such as the Nordic Sugar steam-dryer retrofit demonstrated 13-day fault-prediction windows, validating payback for large chemical and steel sites. Continuous monitoring displaced periodic walk-by inspections, and edge-computing chips embedded in nodes lowered latency to millisecond levels. Chinese stimulus for Industry 4.0 upgrades-maintained momentum, embedding thousands of devices per facility. Consequently, the vibration sensor market gained long-run recurring demand from maintenance budgets rather than capital expenditure cycles.
Rise of Wireless MEMS Sensors for Hazardous Oil and Gas Sites
Offshore platforms and refineries adopted certified wireless nodes that eliminated costly cable runs through ATEX zones. Battery lives exceeded three years, and piezoelectric energy harvesters further prolonged service intervals. Operators valued retrofit capability without shutting down throughput that could otherwise cost USD 50,000 per hour. Embedded FFT processing in each sensor produced actionable bearing-wear metrics, reducing the need for on-site vibration analysts. These benefits widened the addressable base and lifted the vibration sensor market in hydrocarbon economies that historically lagged digital-maintenance adoption.
Edge-AI Enabled Diagnostics in Automotive Assembly
European carmakers fitted edge-AI sensors to robotic arms and conveyor motors to detect micro-defects invisible to cameras or human inspectors. BMW’s Hams Hall plant avoided costly stoplines by flagging anomalies in under a millisecond. Analog Devices’ Voyager4 module filtered raw data on board, shrinking transmissions and extending battery life by 50%. Electric-vehicle lines introduced new high-speed motor harmonics, prompting frequent algorithm retraining but reinforcing the need for flexible firmware. As a result, the vibration sensor market captured a technology-driven upswing in European and North American vehicle factories.
Mandatory ISO 20816 Compliance in EU and North America
The ISO 20816-3:2022 standard codified vibration limits for industrial machines above 15 kW, obliging operators to install continuous monitoring on compressors, pumps, and turbines.[2]ISO, “ISO 20816-3:2022 Mechanical Vibration — Measurement and Evaluation of Machine Vibration — Part 3,” iso.org Evaluation zones tied vibration levels directly to maintenance triggers, steering buyers toward high-resolution sensors. Vendors such as Monnit offered devices tuned to the 10-200 Hz band aligned with compliance thresholds. Avoiding regulatory penalties and insurance surcharges kept purchase urgency high, bolstering short-term uptake in the vibration sensor market.
Restraints Impact Analysis
Restraint | (~) % Impact on CAGR Forecast | Geographic Relevance | Impact Timeline |
---|---|---|---|
Calibration Drift of Piezoelectric Sensors at Extreme Temperatures | -0.7% | Global, particularly harsh environments | Short term (≤ 2 years) |
Data-Security Concerns in Cloud-based Analytics (Defense) | -0.5% | North America and EU defense sectors | Medium term (2-4 years) |
Shortage of Specialty Piezo-ceramic Materials (China Export Quotas) | -0.9% | Global supply chain | Short term (≤ 2 years) |
Source: Mordor Intelligence |
Calibration Drift of Piezoelectric Sensors at Extreme Temperatures
Piezoelectric elements experienced output deviations above 110 °C, with errors hitting 1.06% at moderate heating rates. Frequent recalibration raised lifecycle costs in turbines and aerospace engines where thermal cycling was routine. High-temperature single-crystal alternatives operated reliably beyond 600 °C but commanded premium pricing. Developers explored compensation circuits and dual-sensor configurations, yet complex designs limited mass-market appeal. The resulting performance–price trade-off slowed deployments in harsh-duty niches of the vibration sensor market.
Data-Security Concerns in Cloud-based Analytics (Defense)
Defense and critical-infrastructure operators hesitated to stream vibration signatures into public clouds, fearing espionage or sabotage risks. Air-gapped or one-way data paths mitigated threats but curbed advanced pattern-recognition services. Edge processing offered a compromise, yet required on-site compute resources and secure firmware update channels. As a result, cybersecurity compliance slowed adoption in sensitive aerospace, naval, and pipeline assets, trimming growth potential for the vibration sensor market in those segments.
Segment Analysis
By Product Type: Accelerometers Drive Market While Velocity Sensors Accelerate
Accelerometers generated 54.4% revenue in 2024, underpinning the vibration sensor market size of USD 6.10 billion through their tri-axial versatility in vehicles, smartphones, and factory motors. Wireless velocity devices, though smaller in value, led growth at 9.1% CAGR to 2030 as refinery and pipeline engineers valued velocity’s direct correlation with bearing health.
The miniaturization push spurred next-generation accelerometers such as Bosch Sensortec’s BMA580, which reduced package volume by 76% while meeting sensitivity targets for hearables. Edge filtering in these chips cuts outbound data by transmitting only anomalies, conserving bandwidth in mesh networks. Parallel advances in energy harvesting prolonged node life, enabling five-year maintenance intervals on remote assets. Together, these enhancements allowed the vibration sensor market to broaden into wearables and condition-based lubrication systems previously constrained by power or size limits.
By Technology: MEMS Innovation Challenges Piezoelectric Dominance
Piezoelectric elements retained a 46.3% share in 2024 thanks to low-frequency sensitivity, but MEMS shipments expanded at a 10.3% CAGR as semiconductor fabs delivered wafer-level economies. The vibration sensor market benefited from single-die integration that collapsed discrete analog front-ends into compact system-on-chip packages.
Texas Instruments’ ultrasonic lens-cleaning demo highlighted MEMS versatility, using programmable vibrations to remove contaminants from automotive cameras. Foundry advances enabled multi-axis arrays measuring sub-g vibrations suitable for structural-health monitoring. Meanwhile, piezoresistive and capacitive designs served ultra-low-power wearables where duty cycles were sparse. This diversified portfolio allowed OEMs to choose architectures based on bandwidth, cost, and power, expanding overall penetration of the vibration sensor market.
By Material: Doped Silicon Gains Ground Against Ceramic Leadership
Piezoelectric ceramics delivered 58.4% of 2024 shipments, yet doped silicon grew at 7.9% CAGR as export quotas lifted prices for ceramic precursors. The vibration sensor market size for silicon solutions was forecast to widen as 200 mm MEMS lines amortized faster and integrated electronics reduced assembly cost.
Quartz filled high-precision niches, while flexible polymer films entered biomedical patches that required skin compliance. Hybrid stacks combining silicon MEMS and thin ceramic layers balanced cost and sensitivity, catering to midsized industrial users. These material shifts diversified sourcing footprints, partially insulating the vibration sensor market from geopolitical supply shocks.
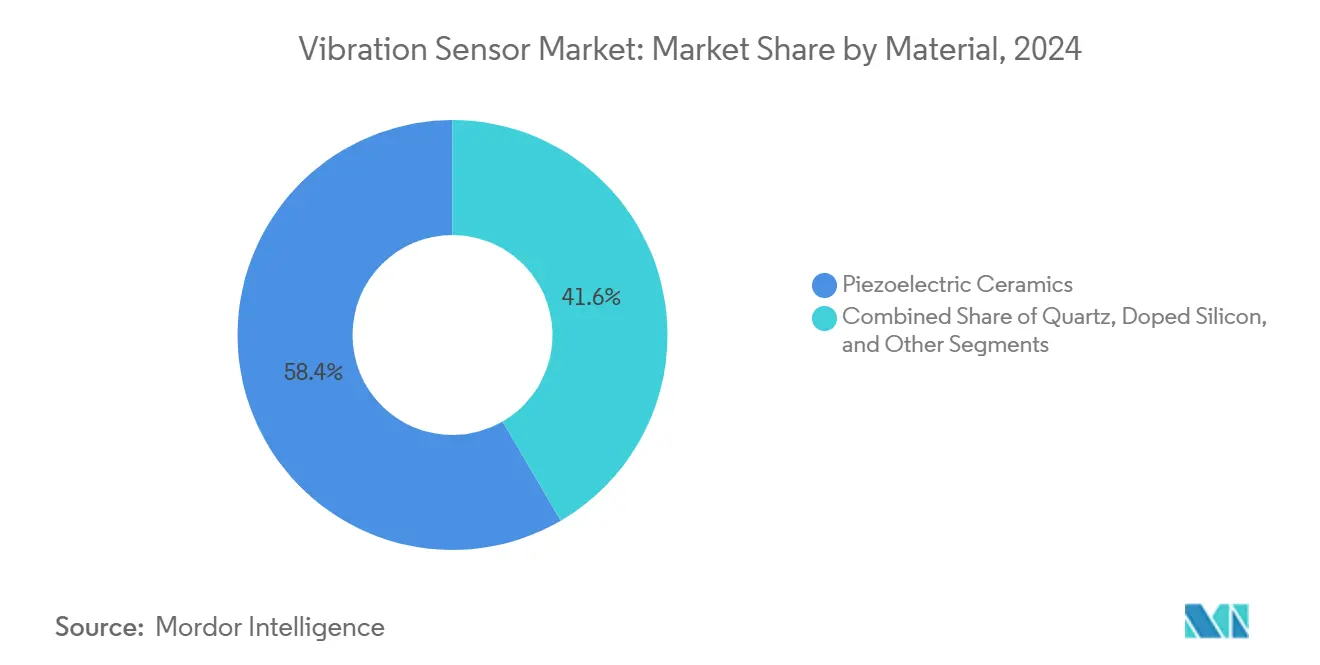
By End-Use Industry: Automotive Growth Outpaces Manufacturing Leadership
Industrial manufacturing generated 27.2% revenue in 2024, anchored by continuous-process plants that embedded thousands of nodes per site. Automotive lines, however, were projected to rise at 8.9% CAGR, adding USD 0.96 billion to the vibration sensor market size by 2030 as EV drivetrains introduced new monitoring points.
Edge-AI firmware allowed instant rejection of defective battery cells on conveyors, while in-vehicle sensors predicted motor-bearing wear before warranty lapses.[3]Automotive Manufacturing Solutions, “How AI Is Shaping the Future of Automotive Manufacturing,” automotivemanufacturingsolutions.com Oil and gas retained steady demand for explosion-proof wireless units, and power-generation operators equipped wind turbines to optimize blade pitch maintenance. Collectively, these verticals sustained a broad buyer base and underpinned recurring growth for the vibration sensor market.
Geography Analysis
Asia-Pacific led with a 34.2% share in 2024 as China’s wind-turbine roll-outs and India’s semiconductor design centers lifted local demand. The region’s 8.3% CAGR also out-paced global averages, preserving its leadership through 2030. Japanese precision-machinery firms ordered high-resolution sensors for robotics, further enlarging the vibration sensor market in the bloc.
North America followed, driven by ISO compliance in chemical plants and aerospace programs requiring radiation-tolerant devices. US defense retrofits favored edge-processed units that remained air-gapped, mitigating cybersecurity exposure. Canadian miners installed ruggedized wireless mesh networks across remote pits where wired runs were impractical, adding niche demand to the vibration sensor market.
Europe exhibited advanced maturity, exemplified by BMW’s sensor-equipped robo-dogs patrolling engine plants. Nordic offshore wind farms fitted high-channel-count systems on 15 MW turbines to monitor yaw and blade harmonics. Strict worker-safety directives assured steady upgrades, keeping the vibration sensor market resilient despite macroeconomic headwinds.
South America and the Middle East/Africa remained emerging but dynamic. Brazilian miners and agribusiness processors began installing condition-monitoring kits, aided by falling MEMS costs. Gulf-region NOCs embraced ATEX-rated wireless sensors for flare stacks and compressors, quickly expanding the vibration sensor market footprint in hazardous-area deployments.
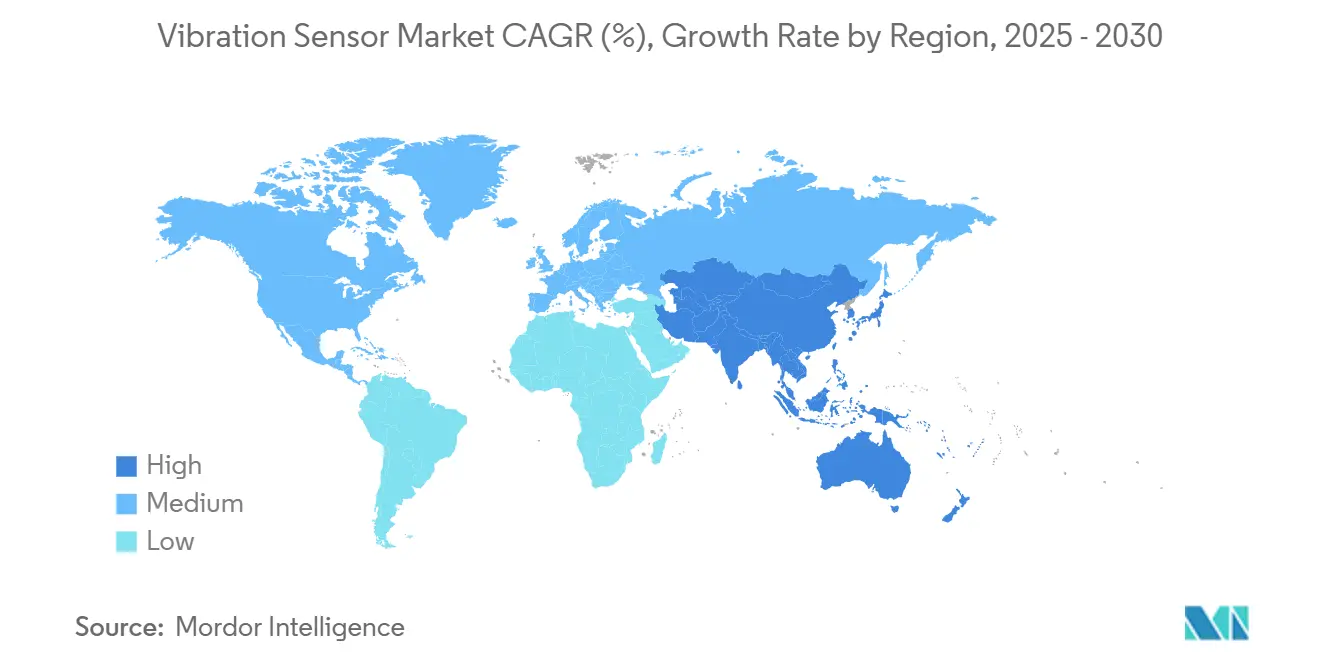
Competitive Landscape
The market was moderately fragmented in 2025. Emerson expanded analytics depth by completing its USD 8.2 billion acquisition of National Instruments, combining sensors with LabVIEW-grade software. SKF augmented service revenues by acquiring John Sample Group’s lubrication management unit, linking vibration thresholds with automated grease systems. Honeywell collaborated with Qualcomm to embed 5G chipsets in low-power sensor gateways, adding bandwidth for higher-sample-rate data.[4]Honeywell, “Honeywell and Qualcomm Work to Revolutionize Energy Sector With 5G, Low Power Wireless and AI-enabled Solutions,” honeywell.com
Start-ups focused on piezoelectric micromachined ultrasonic transducers and conformable array patents, pursuing flexible peel-and-stick sensors that conformed to complex machinery shapes. Component giants such as Texas Instruments released integrated hot-swap eFuses and radar SoCs that complemented sensor nodes with power and perception ICs. Amid talent shortages, many incumbents forged software alliances to embed machine-learning libraries into firmware rather than building from scratch, sharpening differentiation in the vibration sensor market.
White-space opportunities persisted in energy harvesting, cybersecurity-hardened protocols, and API standards that allowed multi-vendor data fusion. Vendors able to bundle hardware, software, and long-term service contracts stood to command premium margins. However, price pressure on commodity accelerometers encouraged scale manufacturers in Taiwan and Mainland China to chase volume, intensifying rivalry across low-end tiers of the vibration sensor market.
Vibration Sensor Industry Leaders
-
SKF GmbH
-
Bosch Sensortec GmbH (Robert Bosch GmbH)
-
Honeywell International Inc.
-
Emerson Electric Corporation
-
Texas Instruments Incorporated
- *Disclaimer: Major Players sorted in no particular order
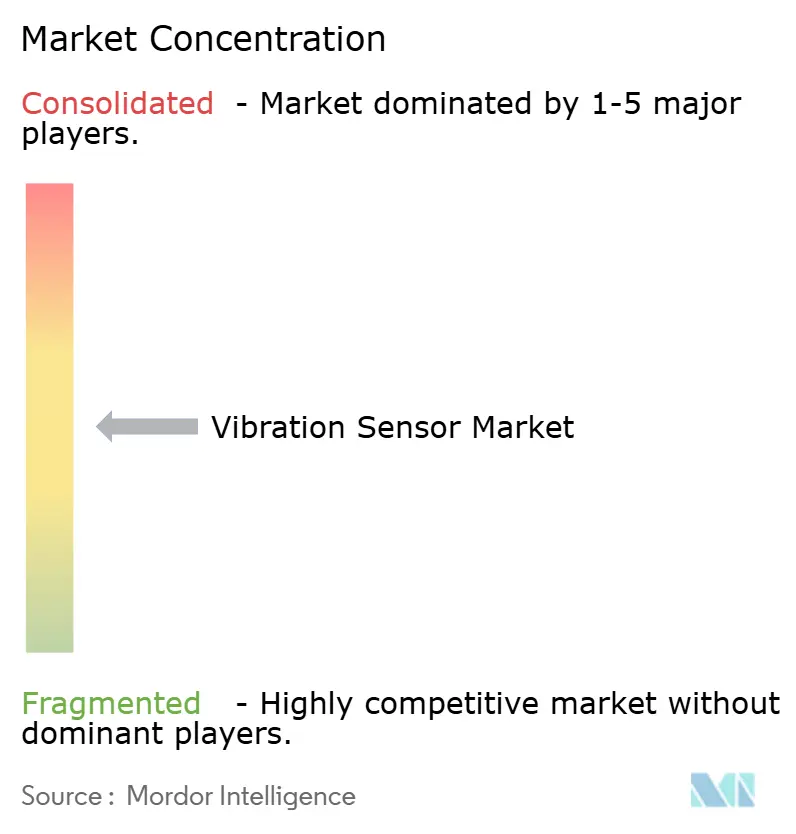
Recent Industry Developments
- May 2025: Vestas secured a 495 MW offshore wind order featuring 33 V236-15 MW turbines in Taiwan, underscoring demand for advanced vibration monitoring in large-class turbines.
- March 2025: Texas Instruments launched the TPS1685 48 V hot-swap eFuse capable of protecting 6 kW server loads, supporting AI workloads that require refined thermal and vibration oversight.
- January 2025: Texas Instruments unveiled the AWRL6844 60 GHz radar sensor for in-cabin monitoring, integrating four transmitters and receivers to lower system cost by USD 20 per vehicle.
- October 2024: Honeywell partnered with Qualcomm to integrate low-power AI processors with industrial sensors for enhanced energy-sector monitoring.
Global Vibration Sensor Market Report Scope
A vibration sensor is a device that detects and measures the amount and frequency of vibration in a system, machine, or piece of equipment. These measurements can detect asset imbalances or other problems and predict future breakdowns. Vibration monitoring and analysis are essential quality measurement phenomena in modern industrial infrastructure.
The report tracks the revenue genrated from sale of vibration sensors across the all the regions which inlcude North America, Europe, Asia Pacific, Latin America and Middle East & Africa.
The studied market is segmented by Product Types such as Accelerometers, Velocity Sensors, and Non-contact Displacement Transducers among various Ends User Industries such as Automotive, Healthcare, Aerospace, Defense, Consumer Electronics, Oil and Gas, and multiple geographies. The impact of Covid-19 on the market is also covered under the scope of the study.
By Product Type | Accelerometers | ||
Velocity Sensors | |||
Displacement Sensors | |||
Gyroscopes (Vibration-Grade) | |||
By Technology | Piezoelectric | ||
Piezoresistive | |||
Capacitive | |||
Strain-Gauge | |||
MEMS | |||
By Material | Quartz | ||
Piezoelectric Ceramics | |||
Doped Silicon | |||
Others | |||
By End-Use Industry | Automotive | ||
Aerospace and Defense | |||
Oil and Gas | |||
Industrial Manufacturing | |||
Power Generation (incl. Wind) | |||
Healthcare | |||
Consumer Electronics and Wearables | |||
Others | |||
By Geography | North America | United States | |
Canada | |||
Europe | Germany | ||
United Kingdom | |||
France | |||
Italy | |||
Spain | |||
Rest of Europe | |||
Asia-Pacific | China | ||
Taiwan | |||
Japan | |||
South Korea | |||
India | |||
ASEAN | |||
Rest of Asia-Pacific | |||
South America | Mexico | ||
Brazil | |||
Argentina | |||
Rest of South America | |||
Middle East and Africa | Middle East | Saudi Arabia | |
United Arab Emirates | |||
Turkey | |||
Rest of Middle East | |||
Africa | South Africa | ||
Rest of Africa |
Accelerometers |
Velocity Sensors |
Displacement Sensors |
Gyroscopes (Vibration-Grade) |
Piezoelectric |
Piezoresistive |
Capacitive |
Strain-Gauge |
MEMS |
Quartz |
Piezoelectric Ceramics |
Doped Silicon |
Others |
Automotive |
Aerospace and Defense |
Oil and Gas |
Industrial Manufacturing |
Power Generation (incl. Wind) |
Healthcare |
Consumer Electronics and Wearables |
Others |
North America | United States | |
Canada | ||
Europe | Germany | |
United Kingdom | ||
France | ||
Italy | ||
Spain | ||
Rest of Europe | ||
Asia-Pacific | China | |
Taiwan | ||
Japan | ||
South Korea | ||
India | ||
ASEAN | ||
Rest of Asia-Pacific | ||
South America | Mexico | |
Brazil | ||
Argentina | ||
Rest of South America | ||
Middle East and Africa | Middle East | Saudi Arabia |
United Arab Emirates | ||
Turkey | ||
Rest of Middle East | ||
Africa | South Africa | |
Rest of Africa |
Key Questions Answered in the Report
What is the current size of the vibration sensor market?
The vibration sensor market stood at USD 6.10 billion in 2025 and is forecast to grow to USD 8.60 billion by 2030 at a 7.10% CAGR.
Which product type dominates the vibration sensor market?
Accelerometers led with 54.4% vibration sensor market share in 2024, reflecting their broad applicability across industrial and consumer devices.
Why are MEMS technologies growing faster than piezoelectric sensors?
MEMS devices benefit from semiconductor economies of scale, on-chip integration, and suitability for wireless, edge-AI applications, giving them a 10.3% CAGR through 2030.
Which region represents the largest opportunity for suppliers?
Asia-Pacific contributed 34.2% revenue in 2024 and is projected to grow at 8.3% CAGR, driven by manufacturing automation and wind turbine installations.
What are the main restraints facing adoption?
High-temperature calibration drift in piezoelectric sensors and cybersecurity concerns over cloud analytics limit uptake in aerospace and defense settings.
How are leading companies differentiating their offerings?
Market leaders integrate AI analytics, secure wireless protocols, and energy-harvesting options to shift from hardware sales toward subscription-based condition-monitoring services.
Page last updated on: