Battery Systems For Electric Vehicle Market Analysis by Mordor Intelligence
The battery systems for electric vehicles market stands at USD 114.92 billion in 2025 and is forecast to climb to USD 203.25 billion by 2030, reflecting a 12.08% CAGR by 2030. Incentive-driven adoption targets in North America and Europe, rapid cost declines in lithium-ion chemistry, and vertically integrated gigafactory roll-outs across Asia, North America, and Europe underpin this expansion. The market also benefits from solid-state breakthroughs that promise higher energy density and safety, while multi-chemistry packs combining lithium-ion with sodium-ion or ultracapacitors widen design flexibility. Competitive intensity remains high as Chinese producers use lithium iron phosphate cost advantages to win share, even as regulatory frameworks in the United States and the European Union tighten local-content demands. Supply-chain bifurcation, thermal-runaway recalls, and critical-mineral volatility temper the outlook but do not derail the secular growth trajectory.
Key Report Takeaways
- By battery type, lithium-ion led with 94.12% of the battery systems for electric vehicles market share in 2024, while solid-state batteries are projected to grow at 39.92% CAGR through 2030.
- By battery chemistry, nickel manganese cobalt claimed 61.38% revenue share in 2024; sodium-ion is forecast to expand at a 44.16% CAGR to 2030.
- By vehicle type, passenger cars held 72.54% of the battery systems for the electric vehicles market size in 2024, whereas commercial vehicles post the fastest 19.47% CAGR.
- By propulsion technology, battery electric vehicles dominated with 71.46% share in 2024; plug-in hybrids are set to advance at 14.09% CAGR to 2030.
- By geography, Asia-Pacific captured 64.32% of the battery systems for electric vehicles market in 2024, while the Middle East and Africa region records the highest 15.74% CAGR.
Global Battery Systems For Electric Vehicle Market Trends and Insights
Drivers Impact Analysis
Driver | (~) % Impact on CAGR Forecast | Geographic Relevance | Impact Timeline |
---|---|---|---|
Government Incentives and Zero-Emission Mandates | +3.2% | Global, with strongest impact in North America & EU | Medium term (2-4 years) |
Declining Li-Ion Costs and Energy Density Gains | +2.8% | Global | Long term (≥ 4 years) |
OEM Giga-Factory Buildouts and Supply Pacts | +2.1% | North America, Europe, APAC core | Medium term (2-4 years) |
Fast-Charging Network Expansion | +1.9% | Global, with early gains in China, California, Europe | Short term (≤ 2 years) |
Vehicle-To-Grid Programs Monetizing Batteries | +1.1% | North America & EU, pilot programs in APAC | Long term (≥ 4 years) |
Insurance Discounts Linked to Battery Health | +0.7% | North America & EU | Short term (≤ 2 years) |
Source: Mordor Intelligence
Government Incentives and Zero-Emission Mandates
Regulatory frameworks accelerate demand by anchoring minimum sales volumes for electric drivetrains. The United States offers tax credits up to USD 7,500 per qualifying vehicle and escalates domestic-content thresholds each year. California’s Advanced Clean Cars II rule obliges automakers to reach 22% zero-emission sales in 2025 and 100% by 2035[1]“Advanced Clean Cars II Regulation,” California Air Resources Board, arb.ca.gov. The United Kingdom mandates 80% electric sales by 2030, while Canada targets 100% by 2035. Because non-compliance triggers sizable penalties, most vehicle makers lock in multi-year battery offtake contracts, providing cell manufacturers with volume security and cash-flow visibility.
Declining Li-ion Costs and Energy Density Gains
Learning-curve effects and materials substitution continue to drive cost trajectories downward. Several top-tier cell makers aim to push pack costs below USD 60 per kWh by 2026, versus USD 118 per kWh in 2024. Energy density climbs through silicon-rich anodes that raise specific capacity by 25-50%, while lithium iron phosphate improves volumetric density with refined cathode coatings. Rapid cost declines widen the total addressable market into entry-level passenger cars, two-wheelers, and cost-sensitive commercial fleets.
OEM Giga-factory Build-outs and Supply Pacts
Automakers invest billions of dollars in regional gigafactories to de-risk logistics, meet local-content rules, and capture upstream margins. New North American facilities collectively add over 500 GWh by 2030, enough capacity for ten million mid-sized vehicles annually. European joint ventures follow, with Spanish, German, and Nordic plants combining to exceed 400 GWh. Localization shrinks transit time, cuts tariffs, and allows platform-specific cell customization.
Fast-charging Network Expansion
Public-private funding programs accelerate charger density, targeting universal coverage along highways and dense urban corridors. The United States pursues 500,000 chargers by 2030, while the European Union links national targets to the registered electric vehicle base[2]“Global EV Outlook 2024,” iea.org. China already has 2.6 million public charging points. As dwell times shrink to 10 minutes for 400 km range additions, cell designs integrate advanced thermal plates and high-C-rate electrolytes to preserve cycle life.
Restraints Impact Analysis
Restraint | (~) % Impact on CAGR Forecast | Geographic Relevance | Impact Timeline |
---|---|---|---|
Mineral Supply and Price Volatility | -2.3% | Global, with highest impact in China dependent regions | Long term (≥ 4 years) |
Thermal-Runaway Recalls and Safety Perception | -1.8% | Global, with heightened sensitivity in developed markets | Medium term (2-4 years) |
Trade Barriers and Local-Content Rules | -1.4% | North America & EU primarily, spillover to allied nations | Medium term (2-4 years) |
Uncertain Recycling Economics for LFP / Na-Ion | -0.9% | Global, with early impact in markets with high recycling mandates | Long term (≥ 4 years) |
Source: Mordor Intelligence
Critical-Mineral Supply and Price Volatility
Concentration in upstream refining exposes manufacturers to geopolitical risk. China refines 80% of global lithium iron phosphate cathode material, while one country produces the majority of cobalt. Demand for lithium is expected to grow five-fold by 2030, yet mine approvals lag, forcing price swings that compress cell-maker margins. Diversification efforts require several years to materialize, extending dependence on dominant suppliers and undermining price visibility.
Thermal-Runaway Recalls and Safety Perception
High-profile battery fires prompt regulatory scrutiny and expensive recalls. Manufacturers bolster packs with ceramic separators, cell-to-pack firewalls, and advanced thermal management, yet consumer perception recovers slowly. Stricter retention standards demand that packs maintain 70% capacity for eight years, raising validation costs and prolonging development cycles.
Segment Analysis
By Battery Type: Lithium-ion Dominance Faces Emerging Challenges
Lithium-ion technology held 94.12% of the battery systems for electric vehicles market share in 2024 and remains the volume leader through 2030. Rapid pack-level innovation drives gravimetric densities toward 300 Wh/kg while trimming cost below USD 60 per kWh. The segment’s entrenched manufacturing ecosystem spans materials, cell formats, and recycling streams, reinforcing scale advantages and lowering entry barriers for new vehicle OEMs.
Solid-state cells record the highest 39.92% CAGR, propelled by ceramic separators that curb dendrite growth and cut capacity fade to 5% after 1,000 cycles. Their superior energy storage enables compact pack designs that free cabin space and trim curb weight, key factors in high-performance or extended-range models. Commercial readiness hinges on automated sintering and high-pressure lamination lines that slash production cost to parity with conventional lithium-ion by the late decade.
Note: Segment shares of all individual segments available upon report purchase
By Battery Chemistry: NMC Leadership Challenged by LFP Cost Advantages
Nickel manganese cobalt chemistry accounted for 61.38% of the battery systems for the electric vehicles market size in 2024, anchoring its position in premium passenger cars and light trucks that demand maximum range. Continuous cobalt-content reduction and manganese-rich formulations cut exposure to price spikes and ethical sourcing concerns.
Lithium iron phosphate rises sharply on the back of robust safety, abundant raw material supply, and lower cost, attracting budget segments and heavy-duty commercial vehicles. Sodium-ion cells, growing at 44.16% CAGR, unlock cold-temperature operation down to −40 °C and tolerate frequent fast-charge cycles. Their near-zero lithium content buffers price risk and allows domestic resource utilization in regions lacking lithium reserves. Hybrid packs combining sodium-ion and lithium-ion optimize cost while maintaining performance, creating an architecture bridge toward full sodium-ion transition once density reaches 200 Wh/kg.
By Vehicle Type: Commercial Vehicles Drive Fastest Growth
Passenger cars dominate revenue with a 72.54% share in 2024. Subsidies, expanding model line-ups, and falling battery prices make electric sedans and crossovers attainable to mass-market consumers. Charging infrastructure density in cities and along corridors removes range anxiety, cementing adoption trajectories.
Commercial vehicles register the fastest 19.47% CAGR as fleet operators exploit predictable duty cycles and total cost advantages. High daily utilization magnifies fuel savings, and dedicated depot charging eases infrastructure challenges. Electric last-mile vans, class-8 tractors with megawatt charging, and battery-swapping taxis find traction in markets where zero-emission zones and congestion fees penalize internal-combustion fleets. Purpose-built commercial packs favor long calendar life and robust thermal tolerance over headline range, spurring chemistry diversification into LFP and sodium-ion.
By Propulsion Technology: BEV Dominance with PHEV Resurgence
Battery electric vehicles represented 71.46% of the battery systems for the electric vehicles market in 2024 and maintain lead status as regulations increasingly phase out internal-combustion engines. Dedicated BEV platforms optimize skateboard architectures, lowering the center of gravity and enabling advanced driver-assistance system integration.
Plug-in hybrids, growing at 14.09% CAGR, address infrastructure gaps and psychological range concerns in suburban and rural areas. A new generation of high-energy packs delivers up to 400 km electric-only range, reducing gasoline reliance while retaining long-distance flexibility. Fleet operators in Europe exploit taxation advantages linked to zero-emission mileage share, accelerating corporate PHEV uptake. Hybrid electric vehicles without plug-in capability gradually plateau as consumers transition toward plug-enabled models that maximize incentive eligibility.
Geography Analysis
Asia-Pacific maintained 64.32% share of the battery systems for electric vehicles market in 2024, anchored by an integrated supply chain that stretches from mineral processing through cell assembly to vehicle manufacturing. China alone supports a significant growth through 2030 as domestic demand remains strong and exports surge, particularly to Southeast Asia and Latin America. Japan advances solid-state research while Korea pivots toward high-manganese chemistries to regain competitiveness. Government incentive alignment and coordinated infrastructure spending continue to reinforce the regional ecosystem.
North America registers the second-largest market, the Inflation Reduction Act channels USD 369 billion in clean-energy funding and sets escalating critical-mineral thresholds, creating a robust pipeline of new gigafactories and mid-stream refining projects. Similarly, Europe advances at 9.40% CAGR on the back of its Green Deal policies and the European Battery Alliance. Strategic autonomy drives localized cathode production and cell assembly funded by public-private joint ventures. Germany leads research partnerships that push silicon-rich anodes, whereas Spain and France focus on mass-market lithium iron phosphate.
The Middle East & Africa region posts the highest regional growth at 15.74% CAGR. Saudi Arabia invests USD 6 billion in an integrated battery complex to diversify its economy and secure downstream automotive manufacturing. The United Arab Emirates targets 25% electric vehicle penetration by 2035, anchoring charging-corridor build-outs along inter-emirate highways. Early-stage projects in Ghana, Morocco, and Rwanda benefit from concessional finance and development-agency technical assistance, positioning the continent for localized two-wheeler and light-commercial electrification.
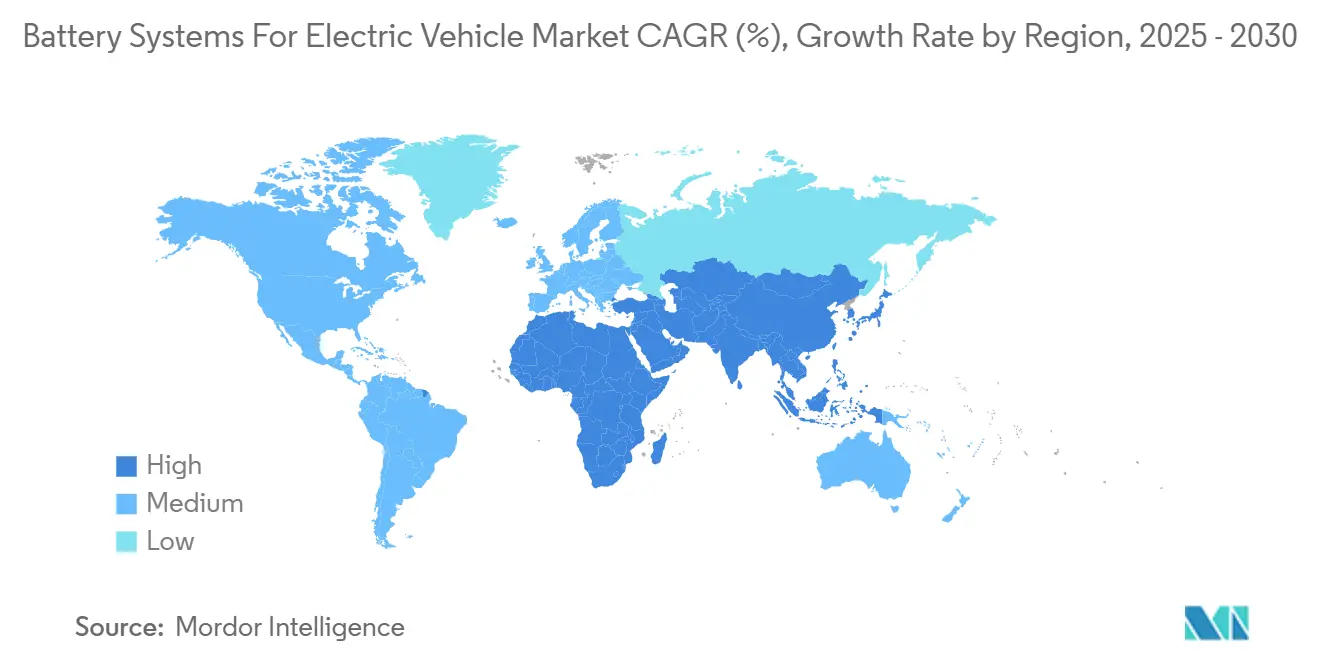
Competitive Landscape
High market concentration persists, with CATL leading the ground. Its scale advantage stems from vertical integration that covers mining partnerships, cell manufacturing, and battery-swapping networks. BYD leverages in-house vehicle production to optimize blade-battery formats, while Korean incumbents emphasize high-nickel chemistries and automotive-grade quality processes to defend premium niches. Japanese manufacturers focus on solid-state patents and ceramic separator expertise, lining up joint ventures with global OEMs to accelerate commercialization.
Technology differentiation shapes strategic positioning. Chinese suppliers expand lithium iron phosphate capacity to undercut price points in entry segments, whereas Western ventures prioritize cobalt-free high-manganese cathodes to meet regulatory sourcing thresholds. Intellectual property around solid-state electrolytes remains concentrated among a handful of players, limiting fast followers. Meanwhile, battery-as-a-service business models that decouple cell ownership from vehicles attract mobility-platform investment, setting the stage for recurring-revenue ecosystems.
Geopolitical headwinds now influence procurement strategy. Foreign-entity-of-concern rules in the United States restrict incentive eligibility for cells containing Chinese materials. European import tariffs and carbon-border adjustments may follow. Consequently, joint ventures, minority equity stakes, and long-term supply contracts diversify sourcing and hedge compliance risk.
Battery Systems For Electric Vehicle Industry Leaders
-
Panasonic Corporation
-
Samsung SDI Co Ltd
-
Contemporary Amperex Technology Co., Limited. (CATL)
-
BYD Co. Ltd.
-
LG Energy Solution Ltd.
- *Disclaimer: Major Players sorted in no particular order
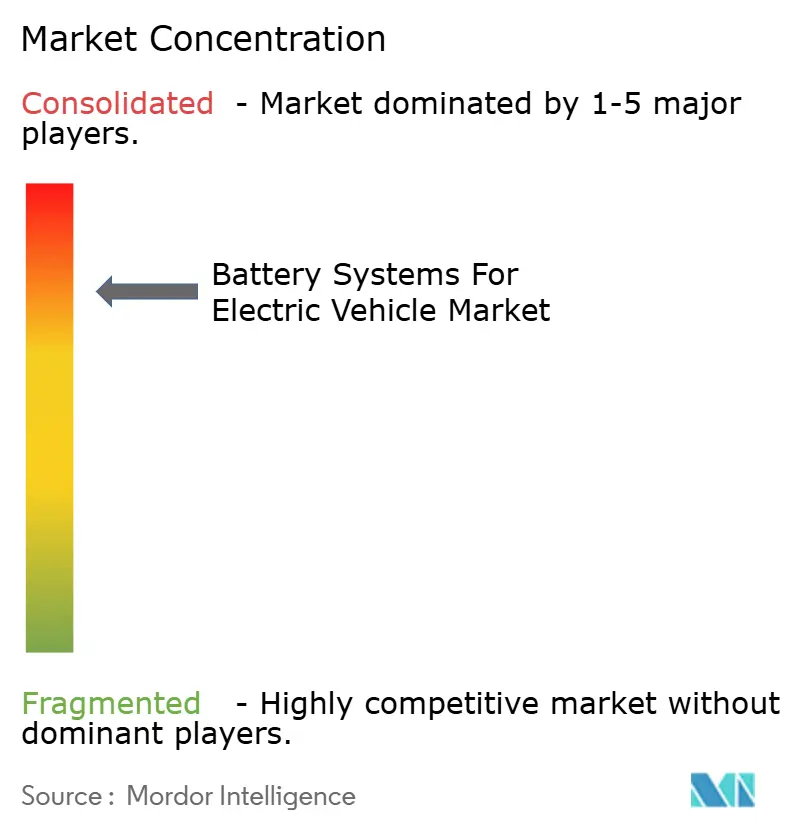
Recent Industry Developments
- April 2025: CATL launched its Naxtra sodium-ion battery featuring 175 Wh/kg density, 90% power retention at −40 °C, and mass-production readiness.
- April 2025: Murata Manufacturing and QuantumScape began collaborating on ceramic film scale-up for solid-state separators.
- March 2025: A leading automaker signed a high-volume battery supply agreement exceeding 100 GWh for United States-based production from 2028.
- February 2025: Volkswagen and CATL expanded their cooperation in China to codify next-generation lithium-ion pack architecture.
Global Battery Systems For Electric Vehicle Market Report Scope
Battery system means a complete energy storage system, including the battery cell, battery module, battery management system, cell balance circuit, monitoring and sensing, thermal management system, safety management system, and physical integration and algorithms and source code related thereto.
The battery systems for electric vehicles market is segmented by type, vehicle type, and geography. By type, the market is segmented as lithium-ion, nickel-metal hydride batteries, lead-acid batteries, ultra-capacitors, and others. By vehicle type, the market is segmented as passenger cars and commercial vehicles. By geography, the market is segmented as North America, Europe, Asia-Pacific, South America, and Middle East, and Africa.
The report offers market size and forecasts for all the above segments in value (USD).
By Battery Type | Lithium-ion | ||
Nickel-metal-hydride | |||
Lead-acid | |||
Ultracapacitors | |||
Solid-state and others | |||
By Battery Chemistry | NMC | ||
NCA | |||
LFP | |||
LMO | |||
Sodium-ion and emerging | |||
By Vehicle Type | Passenger Cars | ||
Commercial Vehicles | |||
By Propulsion Technology | Battery Electric Vehicle (BEV) | ||
Plug-in Hybrid Electric Vehicle (PHEV) | |||
Hybrid Electric Vehicle (HEV) | |||
By Geography | North America | United States | |
Canada | |||
Rest of North America | |||
South America | Brazil | ||
Argentina | |||
Rest of South America | |||
Europe | Germany | ||
United Kingdom | |||
France | |||
Italy | |||
Spain | |||
Netherlands | |||
Russia | |||
Rest of Europe | |||
Asia-Pacific | China | ||
Japan | |||
South Korea | |||
India | |||
Australia | |||
Thailand | |||
Middle East and Africa | Saudi Arabia | ||
United Arab Emirates | |||
Turkey | |||
South Africa | |||
Egypt | |||
Rest of Middle East and Africa |
Lithium-ion |
Nickel-metal-hydride |
Lead-acid |
Ultracapacitors |
Solid-state and others |
NMC |
NCA |
LFP |
LMO |
Sodium-ion and emerging |
Passenger Cars |
Commercial Vehicles |
Battery Electric Vehicle (BEV) |
Plug-in Hybrid Electric Vehicle (PHEV) |
Hybrid Electric Vehicle (HEV) |
North America | United States |
Canada | |
Rest of North America | |
South America | Brazil |
Argentina | |
Rest of South America | |
Europe | Germany |
United Kingdom | |
France | |
Italy | |
Spain | |
Netherlands | |
Russia | |
Rest of Europe | |
Asia-Pacific | China |
Japan | |
South Korea | |
India | |
Australia | |
Thailand | |
Middle East and Africa | Saudi Arabia |
United Arab Emirates | |
Turkey | |
South Africa | |
Egypt | |
Rest of Middle East and Africa |
Key Questions Answered in the Report
Why is Asia-Pacific the largest regional contributor to the battery systems for electric vehicles market?
An integrated supply chain from mineral processing to vehicle assembly, coupled with aggressive purchase subsidies and infrastructure outlays, allows the region to command 64.32% of global revenue.
Which chemistry is gaining the fastest momentum after lithium-ion?
Sodium-ion exhibits the highest 44.16% CAGR thanks to low-cost raw materials and robust cold-temperature performance.
How will solid-state batteries influence market growth by 2030?
Solid-state cells grow at 39.92% CAGR, boosting energy density and safety; they are expected to capture material share once manufacturing cost approaches parity with lithium-ion packs.
What restrains the battery systems for electric vehicles industry despite strong demand?
Critical-mineral concentration, thermal-runaway recalls, and evolving trade barriers collectively impacts the forecast CAGR.
Which vehicle segment offers the most attractive growth opportunity?
Commercial vehicles lead with 19.47% CAGR because fleet operators derive rapid total-cost-of-ownership benefits and comply with zero-emission zone mandates.
Page last updated on: July 2, 2025