Market Size of Global Spark Plasma Sintering Industry
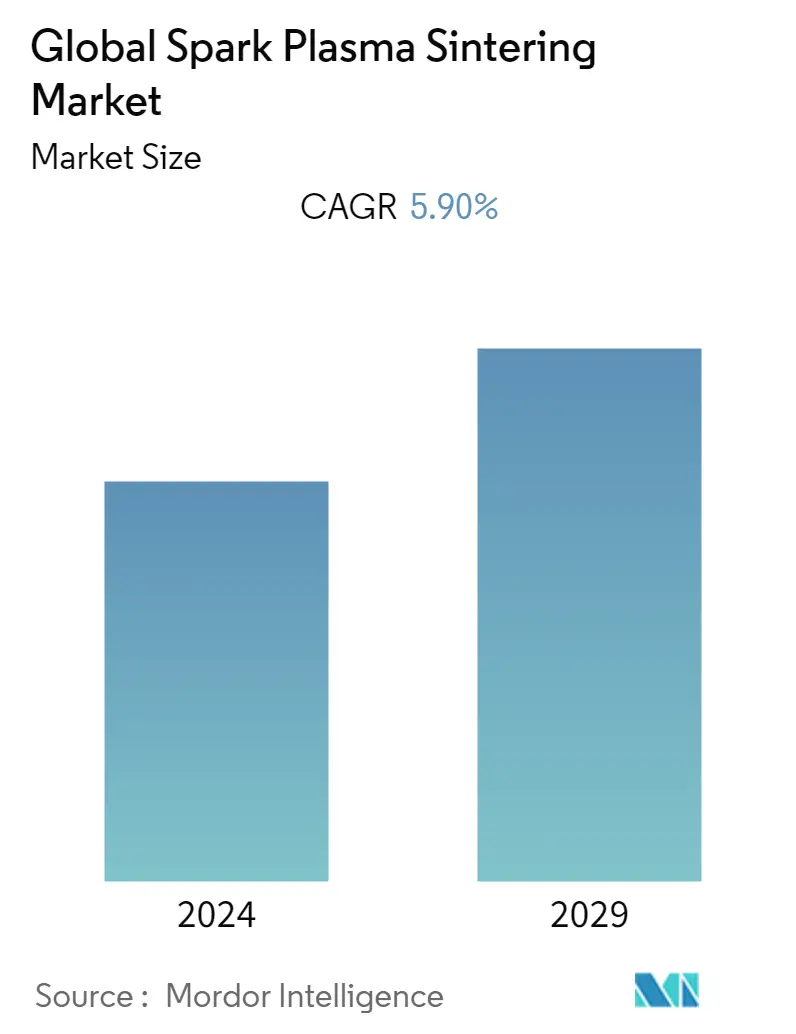
Study Period | 2019 - 2029 |
Base Year For Estimation | 2023 |
CAGR | 5.90 % |
Fastest Growing Market | North America |
Largest Market | North America |
Market Concentration | High |
Major Players![]() *Disclaimer: Major Players sorted in no particular order |
Need a report that reflects how COVID-19 has impacted this market and its growth?
Spark Plasma Sintering Market Analysis
The Spark Plasma Sintering Market is projected to register a CAGR of over 5.9% during the forecast period. The rising adoption of the electric current-assisted sintering method as a tool for the consolidation of various metallic/non-metallic powders and the increasing adoption of the field-assisted sintering technique (FAST) for designing nanomaterials are some of the significant growth drivers for the studied market.
- In the last couple of decades, elaboration techniques based on high current intensities have attracted substantial interest from industrial sectors. Among these techniques, spark plasma sintering has emerged as the most adopted method in the last few years. The SPS technique has recently made significant advancements in materials science and materials processing due to the capability of fast and efficient densification of various materials and the suitability of the equipment for conducting solid-state syntheses and syntheses.
- SPS, also known as FAST, is a high-speed powder consolidation technology that develops quality-centered products from nanomaterials. The technology has gained significant attention for its ability to retain nanocrystalline microstructures and create materials with interesting functional properties. SPS systems have surpassed conventional methods, like hot press (HP) sintering, hot isostatic pressing (HIP), or atmospheric furnaces. Micro-spark/plasma is the most common technique among various proposed physical mechanisms for the SPS process.
- In recent years, SPS has emerged as the preferred option for producing high-strength, ultra-fine crystalline materials; dispersion strengthened materials, thermoelectric or metal-diamond (or generally metal-carbon) composite materials, and sputter targets. Besides, the process facilitates the adjustment of temperature gradients within the sintering body during compaction. It enables the production of gradient and layered materials with widely differing properties (e.g., ZrO2/stainless steel, Al2O3/titanium).
- The increasing adoption of the SPS method as a tool for consolidating powders is also demonstrated by a large number of papers published in recent years. Although SPS is still an emerging technology, slow developments, research, and applications have been increasingly witnessed in recent years, attracting great attention from the research and industrial sectors. For instance, one of the most common applications of SPS is the sintering of high melting point materials, such as titanium nitride. They have been extensively used in the aerospace industry for compressor, turbine, and pressure piping in an engine, owing to their high corrosion resistance, high strength, and relatively lightweight. These factors are fuelling their deployment in the automotive and defense sector.
- Some of the industrial applications of SPS include fuel cell materials, high strength and wear-resistant tooling, sputter targets, diamond compaction for abrasives, and the development of pure or mixed metallics, ceramics, or cermets, where maintaining nanometric and fine microstructure is required. The increasing adoption of innovative metals, composite materials in industrial and consumer products, and ceramics is anticipated to grow during the forecast period, owing to their increasing availability and decreasing manufacturing costs.
- Moreover, during the COVID-19 lockdown, many types of research were carried out in the SPS, which had a positive influence on the studied market growth. For instance, in April 2021, IDAHO researchers will help the industry make high-performance parts inexpensive and durable. Idaho National Laboratory developed advanced capabilities to help the industry design efficient SPS manufacturing processes. The lab's latest addition, one of the largest machines of its kind worldwide, makes it possible to manufacture new materials at industrially relevant scales. INL designed and built four custom SPS machines that range from supporting small experiments on the bench scale to industrial-scale, large-format, and high-throughput systems.
- However, SPS requires a significant up-front investment in time and expense. The operational variables include but are not limited to heat ramp rates, material properties, die design and material, hold temperatures and times, force strategies, vacuum, atmospheric conditions, power settings, and cooling conditions. This can act as a restraining factor to the growth of the market.