Market Size of Selective Laser Sintering Industry
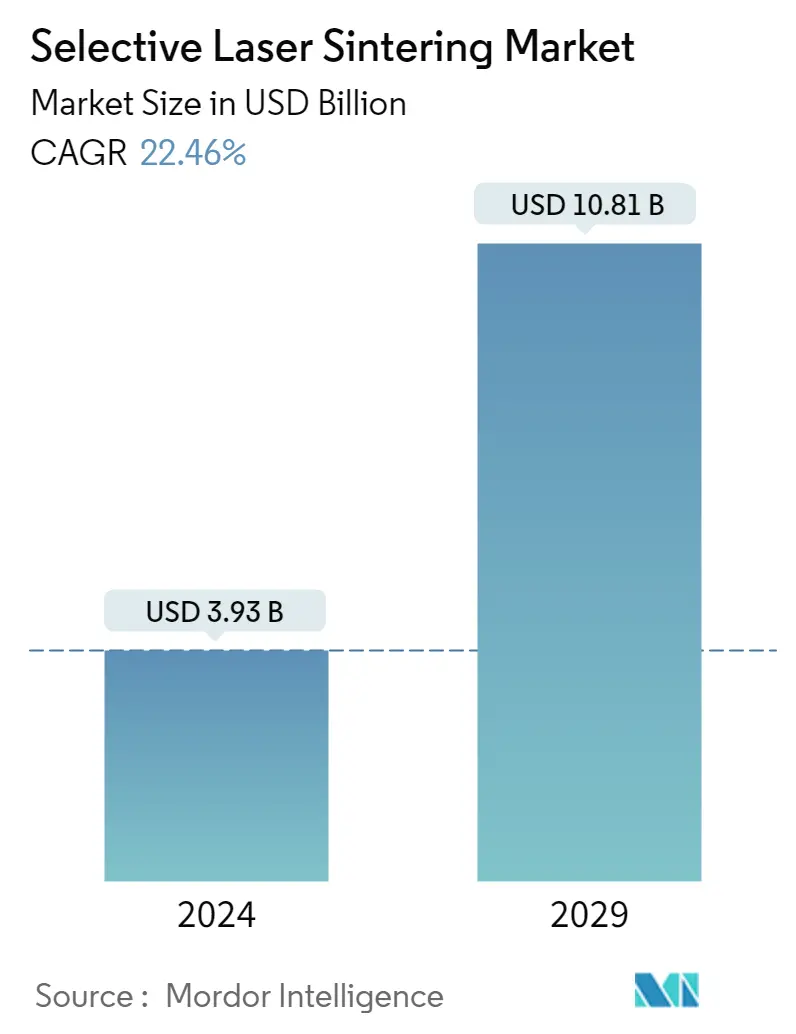
Study Period | 2019 - 2029 |
Market Size (2024) | USD 3.93 Billion |
Market Size (2029) | USD 10.81 Billion |
CAGR (2024 - 2029) | 22.46 % |
Fastest Growing Market | Asia Pacific |
Largest Market | North America |
Major Players![]() *Disclaimer: Major Players sorted in no particular order |
Need a report that reflects how COVID-19 has impacted this market and its growth?
Selective Laser Sintering (SLS) Market Analysis
The Selective Laser Sintering Market size is estimated at USD 3.93 billion in 2024, and is expected to reach USD 10.81 billion by 2029, growing at a CAGR of 22.46% during the forecast period (2024-2029).
Selective Laser Sintering (SLS), an additive manufacturing (AM) technique, is a process in which a high-powered laser beam is aimed into powdered material (typically nylon or polyamide) bed to sinter a layer of the desired object. Following the completion of that layer, the object is covered with a new layer of powder, and another layer is sintered.
- The market for SLS equipment is anticipated to be driven by the rising demand from developed countries, owing to the presence of research and development facilities in the countries. The adoption of laser sintering printers has increased due to the ease of availability of non-metal powders to create prototype models and parts. Also, laser sintering printers are the most precise when printing metal parts.
- Selective Laser Sintering (SLS) has been identified as one of the most-preferred technology and is expected to witness robust growth during the forecast period, owing to its various benefits over other technologies used for printing applications.
- SLS utilizes nylon powder as raw material as a substitute for the photosensitive resin used in Stereolithography. Companies and research organizations across the globe have been identified to take advantage of this material and technology to tackle concerns, such as the brittle nature of the resin when exposed to sunlight. In addition, SLS has also been proven to be cost and material friendly, as it does not require any dedicated support structure post-printing. In addition, SLS provides enhanced durability and can perform as well as either functional parts or prototypes.
- SLS further finds a wide array of applications across various verticals, such as aerospace, defense, and automotive, among others. With space exploration witnessing a paradigm shift, the demand for SLS printing is expected to mount, with an increasing number of countries gearing up to launch satellites.
- Various aerospace companies are adopting the technology to foster efficient production. For instance, in the space flight branch of aerospace, NASA and private companies are working to build rocket engines (and even entire rockets in the case of Relativity Space) with fewer parts, which is a crucial capability of 3D printing and a way to reduce production time and costs. Using selective laser sintering and the laying down and melting of metal powder (for example, Inconel copper super alloy power that can withstand high temperatures), parts are built up layer by layer. The SLS technique offers several benefits, like multiple parts can be printed as one unified part in just days; the rocket's weight can be reduced with fewer nuts, bolts, and welds. If the rocket proves faulty during a test, changes can be made to the 3D modeling software for a new rocket, and another test can be quickly set up.
- Further, in December 2021, Primaeam Solutions Pvt Ltd, an additive parts manufacturing company, inaugurated its new Additive Manufacturing Customer Experience Centre, Innovation & Incubation Centre for Healthcare, in Chennai, India. The 10,000 sq. ft. center would allow the company to develop its position as a prominent player in the additive manufacturing service bureau with technologies such as Electron Beam Melting (EBM), Selective Laser Sintering (SLM), Fused Deposition Modelling (FDM), Stereolithography (SLA), Multi Jet Fusion (MJF), and Continuous Filament Fabrication with Fiber reinforcement (CFF).
- The COVID-19 pandemic outbreak has created economic turmoil for small, medium, and large-scale industries worldwide. Adding to the woes, country-wise lockdown inflicted by the governments across the globe (to minimize the spread of the virus) has further resulted in industries taking a hit and disruption in supply chain and manufacturing operations across the world, as a large part of manufacturing includes work on the factory floor, where people are in close contact as they collaborate to boost the productivity.