Market Size of Surface Mountable Laser Direct Structuring Antenna (LDS) Industry
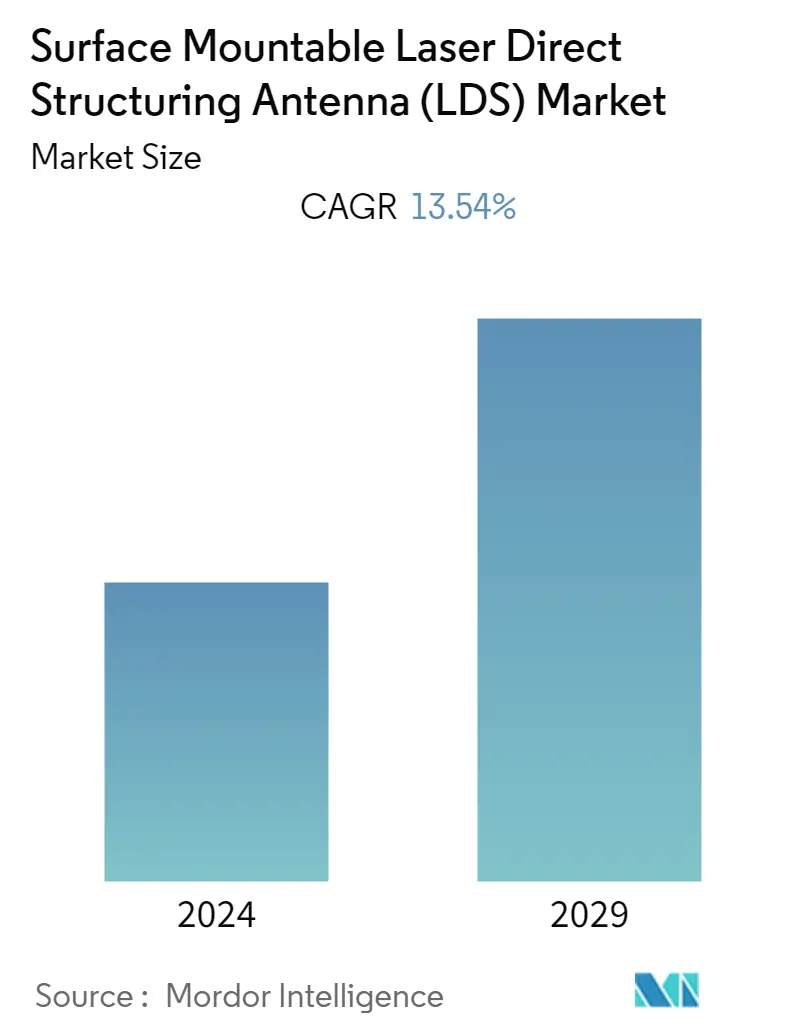
Study Period | 2019 - 2029 |
Base Year For Estimation | 2023 |
CAGR | 13.54 % |
Fastest Growing Market | Asia Pacific |
Largest Market | Asia Pacific |
Market Concentration | High |
Major Players![]() *Disclaimer: Major Players sorted in no particular order |
Need a report that reflects how COVID-19 has impacted this market and its growth?
Surface Mountable Laser Direct Structuring Antenna Market Analysis
The Surface Mountable Laser Direct Structuring Antenna (LDS) market is expected to register a CAGR of 13.54% over the forecast period from 2021 to 2026. Antenna design with Laser Direct Structuring (LDS) technology offers the designers huge flexibility. LDS technology is one of the most advanced and robust 3D antenna manufacturing technology available. According to Multiple Dimensions AG, over one billion LDS antennas have been produced in the past decade. With LDS technology, antenna designers can create compelling antenna designs with new degrees of freedom in three dimensions. Multi-band, Bluetooth, Wi-Fi, CDMA, GSM, Cellular 3G, 4G LTE, and emerging 5G frequencies are served. LDS antennas cover the full spectrum of today's and tomorrow's mobile RF devices. Antennas manufactured using LDS are completely Surface Mount Technology (SMT) capable. Components on flat surfaces and the same level can be mounted using automatic assembly.
- LDS technology gives flexibility for geometric 3D design providing freedom in making antenna products beyond the previously often used flex circuit based antenna technologies. LDS is a better alternative to metal stamped or flexible adhesive antenna designs where the antenna's shape is too complicated or when the space allowed for placement is limited. Another one of the benefits of LDS is that the design frieze can be done much later. The users could till able to adjust the circuit artwork later on in the process, even if the parts are already molded or in the process of being molded. This flexibility and freedom enables to decide later on what type of structure one wants to put on. This is why cell phone antenna manufacturers prefer LDS so much as it allows them to fine-tune their antenna to get the best performance out of it before deciding on a design frieze.
- For the production of antennas in even the smallest electronic components, the 5G generation requirements can be a significant challenge. The aim is to achieve higher frequencies and higher data throughput. The Laser Direct Structuring (LDS) process key to this. It generates antennas for these high requirements quickly and easily on three-dimensional plastic components of any shape. There is no requirement for cost-intensive and loss prone connectors. The higher the frequency of an antenna, the finer its structures. Laser systems operate with high precision and can produce minimal structures with only 25 µm conductor path and insulation channel width. With antennas manufactured using the LDS method, the frequencies of 77 GHz required for 5G could be achieved.
- Modern automotive requires a wide array of sensors and assistive electronics, which increase the comfort and safety of the passengers in the vehicle. At the same time, the goal is to reduce the number of components used and significantly reduce manufacturing costs. Mechatronic Integrated Devices (MIDs), combined with the appropriate connection and assembly technology, is ideal for achieving these goals. It allows typical electromechanical functions such as buttons, plugs, and other connecting elements to be integrated into a single module, which serves as a molded interconnect device. Using the LDS process increases the available design options, accelerates modifications in electronic modules, and allows model variants to be produced cost-effectively, ultimately resulting in more profitable development and manufacturing.
- With the outbreak of COVID-19, various companies have been developing stamp-sized devices, comprising a suite of sensors, including ones that record body temperature and blood oxygen levels. This advance can be used to catch early signs and symptoms of COVID-19, and help monitor patients as the illness progresses. Small diagnosis and monitoring devices help to improve the lives of millions of patients. Combined with comprehensive wireless communication technology, this allows visits to the doctor to be reduced to a minimum. This development requires a more advanced manner of intelligently compressing more functions into a smaller space. With its precision and high reliability, the laser-based LDS process fulfills precisely these requirements.